- Home
- >
- UV Cure Adhesive
Welcome to our comprehensive guide on UV Cure Adhesives, your gateway to understanding the fascinating world of light-activated bonding solutions. UV cure adhesives have revolutionized industries with their quick and efficient curing process, offering unmatched versatility in various applications. This page is your go-to resource for everything related to UV cure adhesive, providing insights, recommendations, and answers to your burning questions.
Table of Contents
ToggleHow does UV-cure adhesive work?
UV-cure adhesives, also known as ultraviolet (UV) curing adhesives, harden or cure rapidly when exposed to ultraviolet light. These adhesives are commonly used in various industries for bonding, coating, and encapsulating applications. The basic principle behind UV-cure adhesives involves a photochemical reaction initiated by exposure to ultraviolet light. Here’s a general overview of how UV-cure adhesives work:
Composition:
- UV-cure adhesives typically consist of three main components: a monomer, an oligomer, and a photoinitiator.
- Monomer:This is the basic building block of the adhesive. It’s a low molecular weight compound that can undergo polymerization.
- Oligomer:Oligomers are higher molecular weight compounds that contribute to the final properties of the cured adhesive.
- Photoinitiator:This chemical compound absorbs UV light and initiates polymerization.
Exposure to UV Light:
- When the UV-cure adhesive is applied to the bonding surfaces, it remains liquid or gel-like.
- The assembly is exposed to UV light with a specific wavelength (usually 200 to 400 nanometers). Commonly, UV lamps or LEDs are used as light sources.
Photoinitiation:
- The photoinitiator absorbs the UV light and undergoes a chemical reaction, generating free radicals or other reactive species.
- These reactive species then interact with the monomers and oligomers in the adhesive, initiating polymerization.
Polymerization:
- Polymerization is the process where the monomers and oligomers react with each other to form long chains (polymers).
- As polymerization progresses, the adhesive transforms from a liquid or gel into a solid, bonding strongly between the surfaces.
Curing Time:
- UV-cure adhesives offer rapid curing times, often within seconds to minutes, depending on factors such as the intensity of the UV light, the adhesive composition, and the thickness of the adhesive layer.
Advantages:
- One of the critical advantages of UV-cure adhesives is their fast curing time, which can improve manufacturing efficiency.
- They also offer precise control over curing since the adhesive only cures when exposed to UV light.
UV-cure adhesives find applications in industries such as electronics, medical devices, optics, and automotive, where rapid and controlled bonding is crucial. The ability to achieve strong bonds quickly without heat makes them suitable for bonding heat-sensitive materials.
What are the key advantages of UV-cure adhesives?
UV-cure adhesives offer several key advantages, making them popular in various industries. Here are some of the main benefits:
Rapid Cure Time:
- UV-cure adhesives cure quickly when exposed to ultraviolet (UV) light. This rapid curing allows for faster production processes, reducing assembly time and increasing overall efficiency.
Precise Control:
- The curing process of UV adhesives can be easily controlled. Manufacturers can control the intensity and duration of UV light exposure, ensuring accurate and consistent results. This is crucial for applications that require high levels of accuracy and repeatability.
Reduced Energy Consumption:
- UV-cure adhesives typically require less energy compared to other curing methods. Curing occurs at room temperature, minimizing the need for elevated temperatures or ovens. This can result in energy savings and a more environmentally friendly manufacturing process.
Low Volatile Organic Compounds (VOCs):
- UV-cure adhesives often have low or zero VOC content, contributing to a healthier and safer working environment. This characteristic is essential for meeting regulatory standards and promoting sustainability in manufacturing processes.
Bond Strength and Durability:
- UV-cured adhesives can provide strong and durable bonds. The cured adhesive often exhibits excellent adhesion to various substrates, including plastics, glass, and metals, resulting in robust and reliable assemblies.
Minimal Heat Generation:
- UV curing generates minimal heat during the process. This is advantageous for heat-sensitive substrates or components, as it helps prevent damage or distortion during bonding.
Versatility:
- UV adhesives can be formulated to suit various applications and requirements. Whether bonding rigid or flexible materials, UV-cure adhesives offer versatility in meeting different manufacturing needs.
Solvent-Free Formulations:
- Many UV-cure adhesives are solvent-free, reducing the risk of environmental pollution and health hazards associated with solvent-based adhesives. This aligns with the increasing demand for eco-friendly and sustainable manufacturing practices.
Improved Quality Control:
- The instant cure feature of UV adhesives enables real-time quality control. Manufacturers can quickly assess the bond strength and product quality immediately after the curing process, allowing for rapid identification and correction of any issues.
Reduced Wastage:
- UV-cure adhesives typically have a longer shelf life than some other adhesive types. Curing on demand reduces wastage since the adhesive only cures when exposed to UV light, allowing for better adhesive application control.
Despite these advantages, it’s important to note that UV-cure adhesives may not be suitable for all applications, and factors such as substrate compatibility, cure depth, and equipment costs should be considered when choosing an adhesive for a specific application.
In which industries are UV cure adhesives commonly used?
UV-cure adhesives are versatile and find applications in various industries due to their fast curing time and strong bond formation when exposed to ultraviolet (UV) light. Some of the sectors where UV-cure adhesives are commonly used include:
- Electronics:UV-cure adhesives are widely used in the electronics industry for bonding and encapsulating components on circuit boards. They offer fast processing times and enable precise bonding without heat damage.
- Medical Devices:UV adhesives are used to assemble medical devices because of their rapid curing capabilities and biocompatibility. They are employed in applications such as bonding medical sensors and attaching components.
- Optics:In the optics industry, UV-cure adhesives are used for lens assembly, bonding glass elements, and connecting optical components. The quick curing time is especially advantageous in visual manufacturing processes.
- Automotive:UV adhesives are used in automotive manufacturing for bonding various components, such as glass, trim, and interior elements. The quick curing time helps streamline production processes.
- Aerospace:In the aerospace industry, UV-cure adhesives are used for bonding and sealing applications where fast curing is essential. They are employed in the assembly of aircraft components and structures.
- Printing:UV-cure adhesives are commonly used in the printing industry for binding and laminating processes. UV-curable inks, coatings, and adhesives are applied and cured rapidly using UV light in printing applications.
- Woodworking and Furniture:UV adhesives are used for bonding wood components, furniture assembly, and laminating surfaces. They provide a strong bond and reduce the need for clamping during the curing process.
- Packaging:UV-cure adhesives are employed in the packaging industry for bonding and sealing cartons and other packaging materials. The quick curing time allows for faster production speeds.
- Construction:UV adhesives are used for bonding glass, plastic, and metal components. They find applications in assembling architectural elements like glass facades and panels.
- Telecommunications:UV-cure adhesives manufacture telecommunications equipment for bonding and encapsulating electronic components.
These are just a few examples, and the use of UV-cure adhesives continues to expand as new formulations are developed, and industries seek efficient and environmentally friendly bonding solutions.
Can UV-cure adhesives bond different materials?
UV-cure adhesives are versatile and can be used to bond a variety of materials. These adhesives are typically formulated to work well with different substrates, including metals, plastics, glass, and some types of rubber. However, the effectiveness of the bond can depend on several factors:
- Substrate Compatibility:UV-cure adhesives may have limitations regarding certain materials. It’s essential to check the manufacturer’s recommendations to ensure compatibility with the specific materials you are working with.
- Surface Preparation:The surfaces to be bonded should be clean and free of contaminants, as any impurities can affect the bond strength. To improve adhesion, some materials may require additional surface treatment, such as primers.
- UV Transparency:UV-cure adhesives rely on exposure to ultraviolet (UV) light to initiate curing. Therefore, materials that block UV light may bond less effectively. Transparent or translucent materials are generally more suitable for UV adhesives.
- Gap Size:UV-cure adhesives are well-suited for bonding applications with minimal gaps between the substrates. Other types of adhesives with higher gap-filling capabilities might be more appropriate if there are significant gaps.
- Curing Time:UV adhesives cure rapidly when exposed to UV light. This can be an advantage for production processes where fast bonding is required. However, ensuring the adhesive has sufficient time to flow and fill gaps before curing is essential.
Before using a UV-cure adhesive for a specific application, conducting compatibility and adhesion tests is advisable. Manufacturers often provide technical data sheets about the recommended substrates, surface preparation, curing times, and other essential details.
Remember that UV-cure adhesives offer advantages such as rapid curing and strong bonds, but they may only be suitable for some applications. It’s always a good idea to consult the adhesive manufacturer or seek professional advice for specific bonding requirements.
What factors influence the curing time of UV adhesives?
The curing time of UV (ultraviolet) and various factors influence adhesives. UV adhesives are typically cured using ultraviolet light, which triggers a photochemical reaction that transforms the liquid adhesive into a solid state. The curing time can be affected by the following factors:
*UV Light Intensity:The intensity of the UV light source is a critical factor. Higher-intensity light sources can lead to faster curing times. However, it’s essential to ensure the adhesive is compatible with the specific wavelength of UV light.
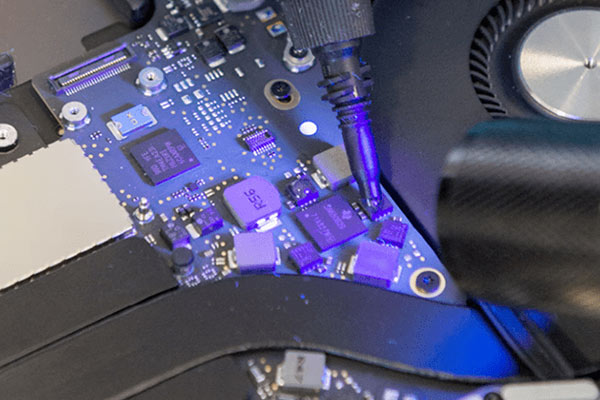
*Wavelength of UV Light:UV adhesives are formulated to cure under particular wavelengths of UV light. Using the correct wavelength is essential for efficient curing. Different formulations of UV adhesives may require various UV light sources.
*Adhesive Thickness:The thickness of the adhesive layer can impact curing time. Thicker coatings may require more time for the UV light to penetrate and cure the adhesive completely.
*Adhesive Composition:The formulation of the UV adhesive itself plays a significant role. Different formulations have varying sensitivities to UV light; some may require more energy or time for complete curing.
*Photoinitiators:UV adhesives often contain photoinitiators, compounds that absorb UV light and initiate the curing process. The type and concentration of photoinitiators can affect the speed and efficiency of curing.
*Temperature:The ambient temperature can influence the curing time. Generally, higher temperatures can accelerate the curing process. However, staying within the recommended temperature range for the specific adhesive is essential to avoid undesirable effects.
*Substrate Material:The nature of the substrate or materials being bonded can impact curing time. Certain materials may absorb or reflect UV light, affecting the efficiency of the curing process.
*Oxygen Inhibition:Some UV adhesives may exhibit oxygen inhibition, where the presence of oxygen interferes with the curing process. Inerting the environment or using specially formulated adhesives can help mitigate this issue.
*Humidity:High humidity levels can sometimes affect the curing process of certain UV adhesives. It’s essential to consider the manufacturer’s recommendations regarding environmental conditions.
*Light Exposure Time:The duration of exposure to UV light is crucial. Insufficient exposure time may result in incomplete curing, while excessive exposure may not provide additional benefits and could lead to overcuring.
Following the manufacturer’s recommendations and guidelines for the specific UV adhesive used is essential, as these factors can vary based on the adhesive formulation and intended application.
Are UV-cure adhesives environmentally friendly?
UV-cure adhesives are relatively environmentally friendly compared to traditional adhesive options. However, like any material, their environmental impact depends on various factors, including the specific formulation of the adhesive, its application, and disposal.
Here are some potential environmental considerations for UV-cure adhesives:
- Volatile Organic Compounds (VOCs):UV-cure adhesives typically have lower or no volatile organic compound emissions than solvent-based adhesives. This can contribute to improved air quality and reduced environmental impact.
- Energy Consumption:The curing process of UV-cure adhesives requires ultraviolet light, which may come from mercury vapor lamps or light-emitting diodes (LEDs). While the energy consumption during the curing process is generally lower than the heat required for some traditional adhesives, the production and disposal of UV lamps or LEDs can still have environmental implications.
- Chemical Composition:Some UV-cure adhesives may contain chemicals that could have environmental implications. It’s essential to consider the specific formulation of the adhesive, and some products may be designed to be more environmentally friendly than others.
- Waste Generation:The waste generated during the production, application, and disposal of UV-cure adhesives should be considered. Proper disposal methods should be followed to minimize the environmental impact.
- Life Cycle Analysis:A comprehensive life cycle analysis (LCA) is needed to assess the environmental impact of UV-cure truly adhesives. This analysis considers all product life stages, from raw material extraction to manufacturing, distribution, use, and disposal.
It’s important to note that technological advancements and a growing emphasis on sustainability have led to the development of UV-cure adhesives with improved environmental profiles. When choosing adhesives, it’s recommended to consider products labeled as environmentally friendly, low-VOC, or designed for reduced environmental impact.
Before selecting an adhesive, it’s advisable to review product documentation safety data sheets and consult with manufacturers to better understand the specific environmental characteristics of the UV-cure adhesive in question.
What safety precautions should be taken when working with UV adhesives?
Working with UV (ultraviolet) adhesives requires careful handling to ensure safety. UV adhesives cure rapidly when exposed to ultraviolet light, and they are commonly used in various industries for bonding and assembly purposes. Here are some safety precautions to consider when working with UV adhesives:
Personal Protective Equipment (PPE):
- Wear appropriate PPE, including safety glasses with UV protection to shield your eyes from harmful UV radiation.
- Use gloves to protect your skin from direct contact with the adhesive.
Ventilation:
- Work in a well-ventilated area to minimize exposure to fumes that may be released during curing.
UV Light Exposure:
- Avoid direct exposure to UV light. UV light sources used for curing can cause eye and skin damage.
- Use barriers, such as UV-blocking shields or curtains, to prevent accidental exposure to UV light.
Skin Contact:
- Avoid direct skin contact with uncured UV adhesives. In case of contact, wash the affected area immediately with soap and water.
Eye Protection:
- Protect your eyes from UV light by wearing safety glasses with appropriate UV filters.
Training:
- Ensure that personnel working with UV adhesives are trained on safe handling procedures, including using PPE and UV light sources properly.
Material Compatibility:
- Be aware of the compatibility of the adhesive with different materials. Some materials may be sensitive to UV exposure and could be damaged.
Emergency Procedures:
- Have emergency procedures in place in case of accidental exposure or spills. This may include access to eye wash stations and emergency showers.
Storage:
- Store UV adhesives in a cool, dry place according to the manufacturer’s recommendations. Follow any specific storage guidelines provided.
Read the Safety Data Sheet (SDS):
- Familiarize yourself with the Safety Data Sheet for your particular UV adhesive. The SDS includes essential information on the hazards, safe handling, and emergency procedures.
Equipment Maintenance:
- Regularly inspect and maintain UV curing equipment to ensure it functions properly and safely.
Dispose of Waste Properly:
- Follow proper disposal procedures for waste materials, including used containers and cured adhesives.
Following these safety precautions can minimize the risks of working with UV adhesives and create a safer work environment. Always refer to the manufacturer’s instructions and safety guidelines for your specific UV adhesive.
Are there variations in UV cure adhesives for specific applications?
UV cure adhesives come in various formulations to suit specific applications and performance requirements. These adhesives are commonly used in electronics, medical devices, optics, and automotive industries, among others. Here are some variations and considerations for UV cure adhesives in specific applications:
Optical Applications:
- Some UV cure adhesives are designed for optical clarity and low yellowing to meet the stringent requirements of applications like bonding lenses, optical filters, and display screens.
Medical Applications:
- UV cure adhesives used in medical devices must be biocompatible and meet regulatory standards. They are often formulated to be resistant to bodily fluids and sterilization processes.
Electronics:
- Electronics applications may require UV-cure adhesives with good thermal conductivity and electrical insulation properties. These adhesives are used for bonding circuit board components and encapsulating electronic assemblies.
Flexible Substrates:
- For applications involving flexible substrates like films or printed circuitry, UV cure adhesives with flexibility and good adhesion to these materials are preferred.
Bonding Dissimilar Materials:
- Some UV adhesives are formulated to connect dissimilar materials, such as glass to metal or plastic to metal. These adhesives provide strong bonds and excellent adhesion to different surfaces.
Fast Curing:
- In specific applications, rapid curing is crucial for production efficiency. UV cure adhesives can be tailored to cure quickly under UV light, reducing assembly times.
Chemical Resistance:
- Applications in harsh chemical environments may require UV adhesives resistant to specific chemicals or solvents.
Temperature Resistance:
- For applications exposed to high temperatures, UV-cure adhesives with good thermal stability and resistance to heat may be necessary.
Low Shrinkage:
- Some applications require adhesives with minimal shrinkage during curing to prevent stress on bonded components.
Environmental Considerations:
- UV cure adhesives are available with formulations compliant with environmental regulations, such as those restricting volatile organic compounds (VOCs).
Before selecting a UV cure adhesive for a specific application, it’s essential to consider the materials being bonded, environmental conditions, curing requirements, and any regulatory or industry standards that may apply. Manufacturers typically provide technical data sheets with detailed information on the properties and recommended uses for their UV cure adhesive products.
Can UV adhesives withstand harsh environmental conditions?
UV adhesives, also known as ultraviolet-curing adhesives, can offer excellent performance in various environmental conditions, but their ability to withstand harsh conditions depends on the specific formulation and application. UV adhesives are typically cured using ultraviolet light, which initiates a photochemical reaction, transforming the liquid adhesive into a solid state.
Here are some factors to consider regarding the ability of UV adhesives to withstand harsh environmental conditions:
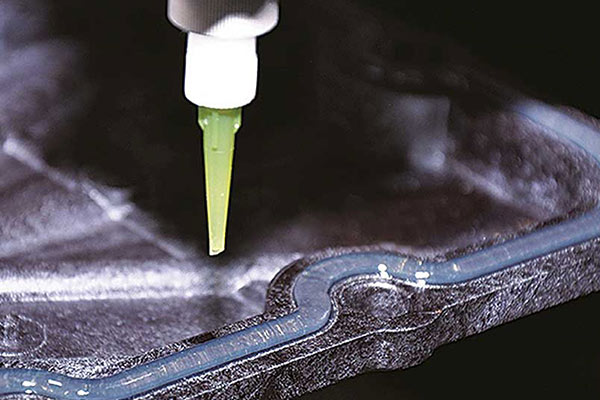
- Chemical Resistance:UV adhesives may resist certain chemicals, but the resistance level depends on the specific formulation. Some UV adhesives can resist exposure to solvents, oils, and other harsh chemicals.
- Temperature Resistance:The thermal stability of UV adhesives varies based on the formulation. Some UV adhesives can withstand high temperatures, while others may be more sensitive. It’s crucial to check the specifications and choose an adhesive that meets the temperature requirements of the intended application.
- UV Resistance:UV adhesives are generally cured by exposure to ultraviolet light. While they are designed to resist the effects of UV radiation, prolonged exposure to intense sunlight may cause some degradation over time. UV-resistant formulations are available for applications where prolonged exposure to sunlight is a concern.
- Moisture Resistance:Some UV adhesives offer good resistance to moisture, making them suitable for applications where exposure to humidity or water is a factor. However, not all UV adhesives are inherently moisture-resistant, so selecting the appropriate formulation for the intended environment is essential.
- Outdoor Applications:UV adhesives are commonly used in outdoor applications, such as bonding in the automotive, aerospace, and construction industries. UV adhesives with good weatherability can withstand outdoor conditions, but the specific formulation and the expected exposure conditions must be considered.
- Flexibility and Toughness:The flexibility and toughness of UV adhesives can influence their performance in harsh conditions, especially with dynamic forces or mechanical stresses. Some formulations are designed to provide flexibility and impact resistance.
Before selecting a UV adhesive for a specific application, it’s essential to consult with the adhesive manufacturer or supplier. They can provide information on the adhesive’s properties, recommended environmental conditions, and limitations. Additionally, conducting thorough testing and considering the application’s specific requirements will help ensure the adhesive’s suitability for harsh environmental conditions.
How does the cost of UV cure adhesives compare to traditional adhesives?
The cost of UV cure adhesives compared to traditional adhesives can vary depending on several factors, including the specific formulations, application requirements, and industry standards. Here are some general considerations:
Material Cost:
- UV cure adhesives can be more expensive per unit than some traditional adhesives. The materials used in UV cure adhesives often include photoinitiators and other additives that contribute to their curing properties. These materials may be costlier than those used in traditional adhesives.
Energy Costs:
- UV cure adhesives require ultraviolet light for curing, which may involve using UV lamps. While energy costs for curing can add to the overall expense, energy consumption can still be competitive or even lower than the costs associated with other traditional curing methods.
Production Speed:
- UV-cure adhesives often cure more quickly than conventional adhesives. This can increase production speed and efficiency, a significant cost-saving factor for industries with high-volume manufacturing processes.
Labor Costs:
- The faster curing time of UV cure adhesives may reduce labor costs associated with handling and waiting for adhesives to set. Faster curing allows for quicker assembly or bonding processes, potentially increasing productivity.
Waste Reduction:
- UV cure adhesives typically generate less waste compared to traditional adhesives. Traditional adhesives may require solvents or carry the risk of over-application, leading to more waste. The precise curing of UV adhesives can minimize these issues.
Equipment Costs:
- The initial investment in UV curing equipment, such as UV lamps and curing systems, can be higher than the equipment required for traditional adhesives. However, the long-term benefits of faster curing times and increased productivity may offset this initial cost.
Application Specifics:
- The choice between UV cure and traditional adhesives often depends on the specific application requirements. For some applications, the unique properties of UV cure adhesives (e.g., fast curing, bond strength) may justify the higher cost.
Regulatory Compliance:
- UV cure adhesives may offer advantages in meeting environmental and regulatory standards, as they often contain fewer volatile organic compounds (VOCs) than traditional adhesives. This can be a consideration in industries with stringent environmental regulations.
While UV cure adhesives may have a higher upfront cost, their speed, efficiency, and potential long-term savings in labor and waste reduction can make them a cost-effective choice for specific applications. It’s crucial to evaluate the application’s particular needs and consider the overall cost of ownership over time.
What equipment is required for curing UV adhesives?
UV adhesives typically require ultraviolet (UV) light sources to initiate the curing process. Here’s a list of equipment commonly used for curing UV adhesives:
UV Light Source:
- UV Lamp:Mercury vapor lamps and metal halide lamps are widely used. They emit UV light in the UVA and UVB spectra. Mercury lamps are cost-effective, while metal halide lamps provide a more intense and focused UV output.
- LED UV Lamps:Light-emitting diode (LED) UV lamps have gained popularity for UV curing due to their energy efficiency, instant on/off capabilities, and the ability to provide specific wavelengths. They are available in various wavelengths to match the absorption spectrum of different UV adhesives.
UV Intensity Measurement Tools:
- UV Radiometer:To measure the intensity of UV light, ensuring that it falls within the optimal range for curing the adhesive. This helps maintain consistency in the curing process.
Conveyor Systems:
- Conveyor Belt or Turntable:In industrial settings, a conveyor system may be used to consistently move products through the UV curing process. This ensures uniform exposure to UV light for efficient curing.
Light Shielding:
- Light Shield or Enclosure:To prevent ambient light from interfering with curing. UV adhesives are light-sensitive, so a controlled environment helps maintain the desired curing conditions.
Safety Equipment:
- UV-Blocking Safety Glasses:Operators and workers should wear protective eyewear that blocks UV light to prevent eye damage.
Cooling Systems:
- Cooling Fans or Water Cooling:Some UV lamps generate heat during operation. Cooling systems help manage the temperature and to avoid overheating.
Control System:
- Timer and Control Unit:To set and monitor the curing time accurately. This ensures the adhesive is exposed to UV light for the required duration.
Adhesive Dispensing Equipment:
- Dispensing Systems:Equipment for precisely applying the UV adhesive onto the surfaces to be bonded.
It’s important to note that the specific equipment needed may vary depending on the type of UV adhesive, the application, and the scale of the operation. Always refer to the manufacturer’s recommendations for the UV adhesive and the curing equipment to ensure proper curing and bond strength.
Are there limitations to using UV-cure adhesives?
Like any technology or material, UV-cure adhesives have limitations and considerations that users should know. Some of the critical limitations include:
- Substrate Transparency:UV-cure adhesives require substrates that are transparent to UV light. The adhesive may not cure properly if the bonded materials are not evident to UV light. For example, opaque or heavily pigmented materials may block the UV light from reaching the adhesive.
- Depth of Cure:UV light has a limited penetration depth. The adhesive may not cure properly if the bond line is too thick. It’s essential to consider the intensity and wavelength of the UV light source for the adhesive and substrate.
- Cure Time:UV-cure adhesives cure quickly, which can be advantageous in some applications. However, rapid curing can be challenging in situations where precise alignment is required or when working with large areas. It may be necessary to use fixtures or other methods to hold the parts in place until the adhesive is fully cured.
- Surface Contamination:Contaminants on the substrate surfaces can inhibit the curing process. It’s crucial to ensure that the surfaces to be bonded are clean and free from any substances that might interfere with the adhesive’s ability to cure under UV light.
- Light Access:The ability of UV light to reach all areas of the bond line is critical. If areas are shadowed or obstructed, the adhesive may not cure properly.
- Temperature Sensitivity:UV-cure adhesives can be sensitive to temperature. Extreme temperatures, either too high or too low, can affect curing. Manufacturers usually provide guidelines regarding the acceptable temperature range for proper curing.
- Cost:UV-cure equipment, including UV lamps and curing systems, can be more expensive than other adhesive curing methods. This initial cost should be considered in the overall cost of the bonding process.
- Limited Flexibility:Some UV-cure adhesives may not be suitable for applications where flexibility is a critical requirement. The cured adhesive may become brittle in certain conditions.
- Health and Safety:UV light can harm the skin and eyes. Proper safety precautions, such as protective equipment and adherence to safety guidelines, are essential when working with UV-cure adhesives.
Despite these limitations, UV-cure adhesives are widely used and offer many advantages in speed, precision, and overall performance in specific applications. It’s essential to carefully consider the requirements of your particular bonding application and assess whether UV-cure adhesives are a suitable choice.
Do UV adhesives provide a transparent bond?
UV (ultraviolet) adhesives are known for providing a transparent bond. UV adhesives are formulated to cure rapidly when exposed to ultraviolet light. The curing process involves the polymerization of the adhesive, resulting in a strong and transparent bond between the joined materials.
UV adhesives are commonly used in applications where optical clarity and transparency are essential, such as bonding glass, plastic, or other transparent materials. The rapid curing time is advantageous in manufacturing processes, allowing for quick assembly and handling of bonded components.
Remember that the bond’s transparency can also depend on the specific formulation of the UV adhesive and the materials being bonded. Some UV adhesives may have slight yellowing or may not be suitable for certain materials, so choosing the right adhesive for your specific application is essential. Additionally, factors such as the thickness of the adhesive layer and the surface characteristics of the materials can influence the final appearance of the bond.
Are there specific considerations for bonding large surfaces with UV adhesives?
Bonding large surfaces with UV adhesives presents unique challenges and considerations compared to smaller surfaces. UV adhesives, also known as ultraviolet-curing adhesives, cure or harden when exposed to ultraviolet (UV) light. Here are some specific considerations for bonding large surfaces with UV adhesives:
Uniform UV Exposure:
- Ensure that the entire bonding surface receives consistent exposure to UV light. Large surfaces may have shadowed areas or receive less UV light, leading to incomplete curing. Multiple UV light sources or carefully positioned lights may be necessary.
Light Intensity and Duration:
- Adjust the UV light intensity and curing time based on the size of the bonding area. Larger surfaces may require longer exposure or higher-intensity UV lights to ensure adequate curing.
Adhesive Thickness:
- The thickness of the adhesive layer can affect curing. UV light penetration is limited, so if the adhesive coating is too thick, it may not heal completely. Consider using adhesives with appropriate viscosity for the intended application.
Substrate Considerations:
- Different materials may have varying levels of UV light absorption or reflection. It’s essential to choose adhesives and substrates compatible with UV curing and account for any potential interference.
Preparation of Surfaces:
- Ensure that the surfaces to be bonded are clean and free from contaminants. Contaminants can hinder the curing process and compromise the bond strength.
Fixture and Alignment:
- Large surfaces may require unique fixtures or jigs to hold the parts in the correct alignment during curing. Proper alignment is crucial to achieving the desired bond strength.
Temperature Control:
- Some UV adhesives may be sensitive to temperature. It’s essential to consider the temperature conditions during bonding and curing to optimize the adhesive’s performance.
Safety Precautions:
- UV light can be harmful to the skin and eyes. When working with UV adhesives, follow safety guidelines and use appropriate protective equipment, such as gloves and UV-blocking eyewear.
Testing and Validation:
- Conduct thorough testing and validating the bonding process, especially when dealing with large surfaces. This may include bond strength testing, environmental testing, and other relevant assessments.
Adhesive Selection:
- Choose UV adhesives that are specifically designed for large surface applications. Some adhesives may be formulated to provide better flow and coverage over larger areas.
Always refer to the manufacturer’s guidelines and recommendations for the specific UV adhesive you use, as different products may have varying requirements and limitations.
Can UV-cure adhesives be used in medical applications?
UV-cure adhesives can be used in specific medical applications. Still, the suitability depends on several factors, including the specific adhesive formulation, the intended use, and the regulatory requirements for medical devices. UV-cure adhesives are known for their fast curing times, which can be advantageous in medical manufacturing.
Here are some considerations for using UV-cure adhesives in medical applications:
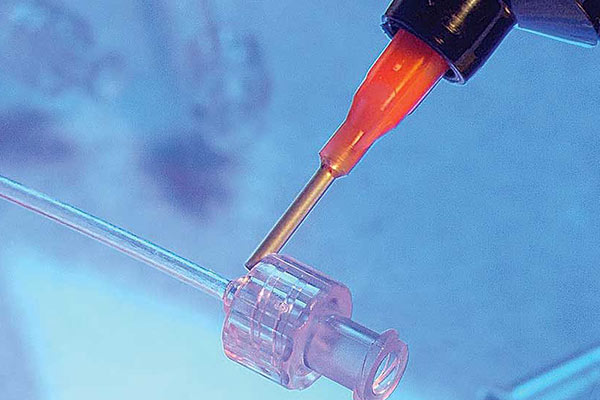
Biocompatibility:
- Medical adhesives must be biocompatible to ensure they do not cause adverse reactions when in contact with living tissues. Some UV-cure adhesives are formulated to meet the biocompatibility standards required for medical devices.
Curing Speed:
- The rapid curing of UV adhesives can be advantageous in medical assembly processes where quick bonding is necessary. This can contribute to increased manufacturing efficiency.
Transparency and Clarity:
- UV adhesives are available in formulations that offer transparency and clarity. This can be important for applications requiring visual inspection or openness, such as in specific medical devices.
Chemical Resistance:
- Consider the resistance of the adhesive to chemicals and bodily fluids, as medical devices may be exposed to various substances. Some UV adhesives are formulated to provide excellent chemical resistance.
Sterilization Compatibility:
- Ensure the UV adhesive is compatible with the sterilization methods required for the specific medical application. Standard sterilization methods include autoclaving, gamma irradiation, and ethylene oxide treatment.
Adhesive Flexibility:
- Depending on the medical device and its application, the flexibility of the cured adhesive may be crucial. Some UV adhesives are designed to maintain flexibility, which is essential in applications where the device may bend or flex.
Regulatory Compliance:
- Medical devices and materials used in medical applications are subject to strict regulatory requirements. It’s essential to ensure that the chosen UV-cure adhesive complies with relevant regulations, such as those set by the U.S. Food and Drug Administration (FDA) or other regulatory bodies in different regions.
Testing and Validation:
- Thoroughly test and validate the adhesive in the specific medical application. This may include assessing bond strength, biocompatibility, and other relevant performance criteria.
Application Method:
- Consider the application method of the adhesive. Some UV adhesives are suitable for manual application, while others may be more appropriate for automated dispensing systems.
Always consult with the adhesive manufacturer and, if applicable, seek guidance from regulatory authorities to ensure that the UV-cure adhesive chosen is appropriate for the intended medical application and complies with relevant standards and regulations.
What role do wavelength and intensity play in the curing process?
The roles of wavelength and intensity in the curing process depend on the context, as curing processes can vary across different industries and applications. However, I’ll provide a general overview, particularly in curing processes like UV (ultraviolet) curing, commonly used in areas such as adhesives, coatings, and printing.
Wavelength:
- UV Curing:In UV curing processes, the wavelength of the UV light is a critical factor. UV light is divided into bands, such as UV-A, UV-B, and UV-C. UV curing often utilizes UV-A and UV-B light. The choice of wavelength depends on the photosensitive properties of the curing material. Different materials have different absorption spectra, meaning they absorb light most efficiently at specific wavelengths. UV light initiates a photochemical reaction in the curing material, leading to polymerization, cross-linking, solidifying, or curing the material.
- Visible Light Curing:In some cases, visual light curing processes are used, which is achieved using light in the visible spectrum. Again, the specific wavelength used will depend on the photosensitivity of the material.
Intensity:
- UV Curing:The intensity of the UV light is a crucial parameter in the curing process. Higher intensity typically leads to faster curing. It is measured in terms of irradiance, which is the power per unit area of the light. The intensity of the light affects the rate of the photochemical reaction. Adequate intensity is necessary to ensure the curing reaction proceeds efficiently and uniformly.
- Visible Light Curing:Similar to UV curing, the intensity of visible light is also essential. Higher light intensity can accelerate the curing process.
The specific wavelength and intensity required depend on the curing process type and the cured material’s photosensitive properties. The goal is to provide the right energy to initiate and sustain the curing reaction without causing undesirable side effects such as overheating or damage to the cured material.
Are there innovations in UV cure adhesives in recent years?
Here are some general trends and innovations that were relevant up to that point:
- Faster Cure Times: Researchers worked on formulations that allowed even speedier curing times. This is crucial for industries where rapid production is essential.
- Improved Performance: Innovations aimed at enhancing the overall performance of UV-cure adhesives, such as increased bond strength, flexibility, and durability, were underway.
- New Applications: UV-cure adhesives have applications in new industries and areas, such as medical devices, electronics, and automotive manufacturing. Researchers were tailoring formulations to meet the specific requirements of these diverse applications.
- Environmental Considerations: There was an increased focus on developing UV-curable adhesives with reduced environmental impact. This includes formulations with lower volatile organic compounds (VOCs) and other environmentally harmful substances.
- Customization and Specialty Formulations: Companies were developing UV-cure adhesives that could be customized for specific applications, providing tailored solutions for different industries.
- Adhesive Substrates: Advances were being made to expand the range of substrates that UV-cure adhesives could effectively bond, allowing for more versatile applications.
How do temperature and humidity affect UV adhesive curing?
Temperature and humidity can significantly impact the curing process of UV (ultraviolet) adhesives. UV adhesives are commonly used in various industries for bonding and assembly applications, relying on ultraviolet light to initiate curing. The interaction between temperature, humidity, and UV curing can influence the overall performance of the adhesive. Here’s how:
Temperature:
- High Temperature:
- Acceleration: Elevated temperatures generally accelerate the curing process of UV adhesives. Higher temperatures can lead to faster polymerization and cross-linking reactions, reducing the curing time.
- Control: While higher temperatures may speed up the curing process, controlling the temperature within recommended limits is crucial. Excessive heat can lead to thermal degradation, reduced bond strength, or changes in the adhesive’s physical properties.
- Low Temperature:
- Slower Cure: Lower temperatures can slow down the curing process of UV adhesives. This can be a concern, especially in colder environments where the adhesive may take longer to reach its complete cure.
- Only complete Cure: Inadequate curing at low temperatures may result in complete cross-linking, reducing bond strength and compromised performance.
Humidity:
- High Humidity:
- Inhibition: High humidity can inhibit the curing of certain UV adhesives. The presence of moisture in the air can interfere with the UV light penetration and absorption by the adhesive, preventing adequate curing.
- Adhesive Selection: Some UV adhesives are formulated to be more tolerant to humidity, but choosing an adhesive suitable for specific environmental conditions is essential.
- Low Humidity:
- Faster Cure: Low humidity levels are generally favorable for UV curing. Dry conditions allow for better UV light penetration into the adhesive, promoting efficient curing.
- Control: Deficient humidity levels may increase brittleness in the cured adhesive, so maintaining a balance is essential.
Optimal Conditions:
- To achieve the best results, operating within the recommended temperature and humidity range specified by the adhesive manufacturer is essential.
- UV curing equipment should be calibrated and controlled to ensure consistent and reliable curing.
Testing and Validation:
- Perform testing and validation under the specific environmental conditions expected during the application to ensure the adhesive meets the desired performance criteria.
Understanding the interplay between temperature, humidity, and UV curing is crucial for achieving optimal results with UV adhesives. Adhesive manufacturers provide guidelines and recommendations for curing conditions, and adherence to these guidelines is essential for successful bonding applications.
Are there challenges associated with removing cured UV adhesives?
Removing cured UV adhesives can pose challenges because these adhesives are designed to create strong and durable bonds upon exposure to ultraviolet (UV) light. The fixed state makes them resistant to many solvents and mechanical forces. Here are some challenges associated with removing cured UV adhesives:
- Chemical Resistance:Cured UV adhesives are often chemically resistant, which means that common solvents may not be effective in breaking down the adhesive bond. This makes it challenging to find a suitable chemical agent for removal.
- Temperature Sensitivity:UV adhesives are typically formulated to cure under UV light and may become more resistant at higher temperatures. This can limit the effectiveness of heat-based removal methods.
- Surface Sensitivity:The substrate to which the UV adhesive is applied may be sensitive to certain chemicals or high temperatures. It’s essential to consider the material compatibility when choosing a removal method to avoid damaging the underlying surface.
- Mechanical Strength:Cured UV adhesives often exhibit high mechanical strength, making breaking or peeling apart the bonded surfaces difficult. More than mechanical methods such as scraping or abrasion might be required.
- Specialized Equipment:Effective removal may require specialized equipment, such as UV light sources for controlled re-curing of the adhesive or mechanical tools designed for adhesive removal.
- Time Factor:Over time, the bond between cured UV adhesive and the substrate may become increasingly difficult to break. Prompt action upon recognizing the need for removal can make the process more manageable.
- Adhesive Residue:Even after the bulk of the adhesive is removed, residue may be left on the surfaces. Additional cleaning steps may be necessary to eliminate any remaining traces.
To overcome these challenges, it’s recommended to consult the adhesive manufacturer’s guidelines for removal recommendations. Testing different removal methods on a small, inconspicuous area can help identify the most effective and least damaging approach for a specific application. In some cases, seeking assistance from adhesive experts or professionals who specialize in adhesive removal may be advisable.
What are the future trends and developments in UV cure adhesives?
However, the field is continually evolving, and there may have been further advancements since then. Here are some trends and developments that were relevant up to 2022:
Advanced Formulations:
- Ongoing research and development were focused on creating UV-cure adhesives with improved performance characteristics, such as higher strength, flexibility, and chemical resistance.
- Formulations designed for specific applications and industries, such as automotive, electronics, medical, and aerospace, were becoming more common.
Fast Cure and Increased Productivity:
- Efforts were being made to enhance the curing speed of UV adhesives to improve production efficiency. Faster cure times contribute to higher throughput in manufacturing processes.
Environmental Sustainability:
- Growing emphasis on environmentally friendly and sustainable materials has influenced the development of UV-cure adhesives with reduced environmental impact.
- Formulations with fewer volatile organic compounds (VOCs) and other harmful components were gaining attention.
Application in 3D Printing:
- UV-cure adhesives were being explored for use in 3D printing processes, offering rapid curing and high precision in creating layered structures.
Smart Adhesives:
- Integrating smart or responsive features into UV-cure adhesives, such as self-healing properties or adaptability to environmental conditions, was an area of interest.
Improved Substrate Compatibility:
- Efforts were underway to develop UV adhesives with enhanced compatibility for a broader range of substrates, including challenging materials like glass, plastics, and metals.
Niche Applications:
- Due to their unique curing properties, UV-cure adhesives have found applications in niche markets, such as medical devices, optical bonding, and flexible electronics.
UV LED Technology:
- The shift towards UV LED technology for curing processes became more prevalent. UV LED systems offer advantages such as energy efficiency, longer life, and precise control over the curing process.
Regulatory Compliance:
- Continued efforts were being made to develop UV-cure adhesives that meet or exceed regulatory standards, addressing health, safety, and environmental concerns.
Collaborative Research:
- Collaboration between adhesive manufacturers, researchers, and end-users increased to drive innovation and address specific industry needs.
Conclusion:
In conclusion, UV cure adhesives represent a cutting-edge solution in bonding technologies. Their rapid curing, versatility, and application-specific formulations make them a go-to choice for various industries. Armed with the knowledge from this guide, you’re equipped to explore the boundless possibilities UV cure adhesives offer in enhancing efficiency and performance across diverse applications. Dive into UV cure adhesives and discover a new dimension in bonding technology.