- Home
- >
- UV Cure Adhesive
- >
- UV Cured Epoxy Potting
UV Cured Epoxy Potting
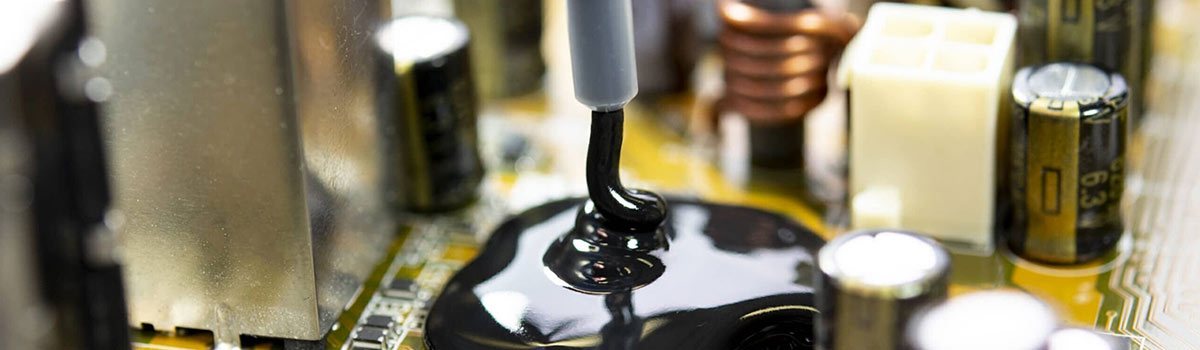
As a cutting-edge solution in the realm of electronic encapsulation, UV cured epoxy potting offers a range of benefits, from rapid curing times to exceptional durability. This page is designed to be your go-to resource for understanding the intricacies of UV cured epoxy potting systems. Whether you’re a seasoned professional or a curious enthusiast, explore the following sections to gain insights into the technology, applications, and various aspects of UV cured epoxy potting.
Table of Contents
ToggleWhat is UV Cured Epoxy Potting?
UV-cured epoxy potting is used in electronics manufacturing to encapsulate or protect electronic components using a specific type of epoxy resin cured or hardened using ultraviolet (UV) light. This technique creates a protective barrier around sensitive electronic parts, safeguarding them from environmental factors such as moisture, dust, chemicals, and physical impact.
Here’s a more detailed explanation of the critical elements involved in UV-cured epoxy potting:
- Epoxy Resin:Epoxy resin is a type of polymer that, when combined with a curing agent, undergoes a chemical reaction, forming a solid and durable material. Epoxy resins are known for their excellent adhesion, mechanical strength, and chemical resistance.
- UV-Curing:UV-curing is a process where the epoxy resin is formulated with photoinitiators. These photoinitiators react when exposed to specific wavelengths of ultraviolet light, initiating a rapid curing process. UV light triggers the cross-linking of molecules in the epoxy resin, transforming it from a liquid to a solid state.
- Potting involves enclosing electronic components within a protective material to shield them from environmental factors. In this case, the material used for potting is the UV-curable epoxy resin. The potting process provides insulation, protection against moisture, and mechanical support to the enclosed components.
The UV-cured epoxy potting process generally follows these steps:
- Mixing:The epoxy resin and curing agent are incorporated in the appropriate proportions. This mixture is then applied to the electronic components that require protection.
- Encapsulation:The electronic components are placed in a mold or container, and the mixed epoxy resin is poured or dispensed to encapsulate them fully.
- UV Exposure:The assembly is exposed to UV light, causing the epoxy resin to undergo a rapid curing process. This ensures the formation of a solid and protective encapsulation around the electronic components.
- Final Cure:Some formulations may require additional curing time, either through exposure to ambient conditions or, in some cases, further heat curing.
UV-cured epoxy potting is chosen for its advantages in terms of speed and efficiency. The quick curing time associated with UV light exposure allows for faster production cycles. Additionally, this method is suitable for applications where heat-sensitive components are involved, as the curing process generates minimal heat. The resulting encapsulation provides reliable protection, making it well-suited for electronic devices exposed to challenging operating environments.
How does the UV curing process work in epoxy potting?
UV curing in epoxy potting involves using ultraviolet (UV) light to initiate a chemical reaction that transforms a liquid epoxy resin into a solid, durable material. Epoxy potting is a common technique used to encapsulate electronic components, protecting them from environmental factors such as moisture, dust, and vibrations. Here’s a general overview of how the UV curing process works in epoxy potting:
Epoxy Resin Mixture:
- Epoxy resin is a two-part system consisting of a resin and a hardener. These components are mixed in precise ratios to initiate the curing process.
- The resin mixture typically includes photoinitiators, compounds that respond to UV light by initiating the polymerization of the epoxy resin.
Application:
- The mixed epoxy resin is applied to the electronic components or the area that needs encapsulation. This is typically done by pouring or injecting the liquid epoxy onto the target area.
Exposure to UV Light:
- Once the epoxy resin is in place, it is exposed to ultraviolet light. The light source is typically a UV lamp or LED with the appropriate wavelength to activate the photoinitiators in the resin.
Photopolymerization:
- The UV light activates the photoinitiators in the epoxy resin, causing them to undergo a chemical reaction known as photopolymerization.
- During photopolymerization, the resin molecules cross-link and form a three-dimensional network, creating a solid and durable structure.
Curing Time:
- The curing time depends on factors such as the intensity of the UV light, the type and concentration of photoinitiators, and the thickness of the epoxy layer.
- UV-curing epoxy systems often have relatively short curing times, making them suitable for applications where rapid processing is essential.
Completion of Curing:
- The curing process is complete once the epoxy has undergone sufficient UV exposure. The epoxy is solid and provides the desired encapsulation and protection for the electronic components.
The benefits of UV curing in epoxy potting include:
- Rapid curing times.
- Reduced energy consumption compared to heat-curing processes.
- The ability to achieve precise control over the curing process.
UV-cured epoxy is known for its high strength, chemical resistance, and excellent adhesion properties.
What are the critical components of UV-cured epoxy potting systems?
UV-cured epoxy potting systems typically consist of several critical components designed to work together to achieve efficient and reliable encapsulation of electronic components. These components include:
Epoxy Resin:
- The epoxy resin is the primary component of the potting material. It provides the structural integrity and protection for the electronic components. Epoxy resins are known for their excellent adhesion, high strength, and chemical resistance.
Hardener:
- Epoxy resins are typically two-part systems consisting of a resin and a hardener. The hardener initiates the curing process when mixed with the resin. The proper ratio between the resin and hardener is crucial for achieving optimal curing and performance.
Photoinitiators:
- Photoinitiators are compounds added to the epoxy resin mixture to respond to UV light. When exposed to UV radiation, photoinitiators undergo a chemical reaction that initiates the curing process (photopolymerization). The choice and concentration of photoinitiators affect the curing speed and efficiency.
UV Light Source:
- UV lamps or LEDs serve as the light source for curing the epoxy. These light sources emit ultraviolet radiation at specific wavelengths that activate the photoinitiators in the epoxy resin. UV LED technology is often preferred for its energy efficiency, longer lifespan, and precise control over the emitted wavelength.
Additives:
- Various additives may be included in the epoxy formulation to enhance specific properties. For example, fillers can be added to modify thermal conductivity or reduce shrinkage. Other additives may improve flexibility and flame resistance or provide special features depending on the intended application.
Stabilizers:
- Stabilizers are sometimes added to the epoxy formulation to prevent premature curing before exposure to UV light. This ensures the epoxy remains liquid until deliberately exposed to the UV light source.
Solvents or Diluents:
- Solvents or diluents may be included in the epoxy formulation to adjust viscosity and improve the flow of the liquid resin. These components can also impact the wetting properties and ease of application.
Surfactants:
- Surfactants may be used to improve the wetting and spreading of the epoxy on the surface of the electronic components. This helps achieve better coverage and minimizes voids in the cured epoxy.
Inhibitors:
- Inhibitors may be added to the epoxy formulation to control the curing process. These components can extend the epoxy pot life, allowing for more developed working times before exposure to UV light.
Combining these components in a well-formulated epoxy system ensures that the potting material cures efficiently, providing the desired protection and encapsulation for electronic components in various applications.
In what industries are UV-cured epoxy potting systems commonly used?
UV-cured epoxy potting systems find applications in various industries where efficient and precise encapsulation of electronic components is crucial. Some of the industries that commonly use UV-cured epoxy potting include:
Electronics and Electrical Devices:
- UV-cured epoxy potting is widely used in electronics to protect and encapsulate components such as circuit boards, sensors, and microelectronics. This helps prevent damage from moisture, dust, and environmental factors.
Telecommunications:
- Telecommunication equipment often requires effective potting to ensure the durability and reliability of sensitive electronic components. UV-cured epoxy is suitable for rapid processing and provides excellent protection against harsh environmental conditions.
Automotive:
- UV-cured epoxy potting encapsulates electronic control units (ECUs), sensors, and other vehicle components in the automotive industry. The rapid curing time is beneficial in automotive manufacturing processes.
Medical Devices:
- Medical devices often contain sensitive electronic components that require protection from moisture and other environmental factors. UV-cured epoxy potting is suitable for medical applications due to its fast curing time and biocompatibility in certain formulations.
Aerospace and Defense:
- The aerospace and defense industries use UV-cured epoxy potting for encapsulating electronic components in aircraft, satellites, and military equipment. UV-cured epoxy’s lightweight and high-performance characteristics make it suitable for these applications.
LED Lighting:
- UV-cured epoxy is commonly used in the manufacturing of LED lighting products. It allows for efficient encapsulation of LED components, ensuring durability and thermal stability.
Renewable Energy:
- Solar panels and other renewable energy systems often incorporate UV-cured epoxy for potting electronic components. The rapid curing time is advantageous in large-scale manufacturing processes.
Consumer Electronics:
- UV-cured epoxy is found in consumer electronic devices such as smartphones, tablets, and wearables. It provides protection against environmental factors while allowing for quick manufacturing cycles.
Optoelectronics:
- Optoelectronic devices, including optical sensors and communication equipment, benefit from the encapsulation provided by UV-cured epoxy potting systems.
Industrial Automation:
- In industrial automation systems, UV-cured epoxy is used to protect electronic components in control panels, sensors, and other automation equipment.
UV-cured epoxy potting offers advantages such as rapid processing times, high strength, and precise control over the curing process, making it a versatile solution for various industries where efficient and reliable encapsulation is essential.
What are the advantages of UV-cured epoxy potting over traditional potting methods?
UV-cured epoxy potting offers several advantages over traditional potting methods, typically involving thermally cured epoxies or other potting compounds. Here are some of the advantages of UV-cured epoxy potting:
Rapid Cure Time:
- UV-cured epoxy potting has a speedy cure time, often in seconds to minutes. This allows for quicker production cycles and increased efficiency in manufacturing processes.
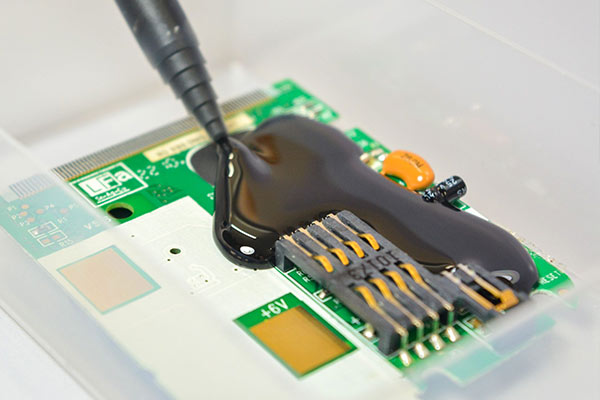
Energy Efficiency:
- UV curing requires less energy compared to thermal curing methods. The curing process is initiated by exposure to ultraviolet light, which consumes less power than the elevated temperatures needed for thermal curing.
Low Heat Generation:
- UV curing generates less heat compared to thermal curing. This is particularly beneficial when working with heat-sensitive components or materials that may be damaged or adversely affected by high temperatures.
Precise Control:
- UV curing offers precise control over the curing process. The curing reaction only occurs when exposed to UV light, allowing for accurate and controlled application of the epoxy. This is especially useful for intricate or complex electronic components.
Reduced Environmental Impact:
- UV-cured epoxies often contain fewer volatile organic compounds (VOCs) than thermally cured alternatives. This can contribute to a reduction in environmental impact and a safer working environment.
Improved Adhesion:
- UV-cured epoxies can provide excellent adhesion to various substrates, promoting better encapsulation and protection of electronic components. The rapid curing process helps ensure a strong bond with minimal risk of contaminants affecting the bond.
Reduced Wastage:
- The quick curing time allows for better control over the dispensing and potting, minimizing material wastage. This is particularly advantageous in high-volume production settings.
Enhanced Productivity:
- The fast cure time and reduced processing steps contribute to increased productivity. Manufacturers can achieve higher throughput and shorter turnaround times, leading to more efficient production lines.
Versatility:
- UV-cured epoxy potting is suitable for various applications and can be used with multiple substrates. Its versatility makes it an attractive option for diverse industries.
It’s important to note that the choice between UV-cured epoxy potting and traditional potting methods depends on specific application requirements, production processes, and the properties of encapsulated materials. Each method has its own set of advantages and considerations, and the optimal choice may vary based on the unique needs of a given project.
Are there any limitations or considerations when using UV-cured epoxy potting?
UV-cured epoxy potting is a popular method for encapsulating and protecting electronic components. While it offers several advantages, there are also limitations and considerations to keep in mind:
Material Compatibility:
- Ensure that the epoxy resin is compatible with the materials used in the electronic components. Some materials may be sensitive to UV exposure or not bond well with specific epoxy formulations.
UV Penetration:
- UV light might have difficulty penetrating densely packed or opaque components, leading to incomplete curing in shadowed areas. Consider the design of your electronics to allow adequate UV exposure to all surfaces.
Heat Sensitivity:
- UV-cured epoxy may generate heat during the curing process. Components sensitive to heat may be damaged, so it’s essential to consider the temperature limitations of the electronic parts being potted.
Moisture Sensitivity:
- Ensure that the cured epoxy provides a reliable barrier against moisture. If not properly fixed or if the epoxy formulation is not moisture-resistant, it could lead to corrosion or reduced insulation properties.
Shrinkage:
- Some UV-cured epoxies may experience shrinkage during the curing process. This could lead to stress on delicate components or compromise the overall stability of the encapsulation.
Adhesion:
- Proper surface preparation is crucial for good adhesion. Ensure that the surfaces to be potted are clean, free of contaminants, and suitable for bonding with the epoxy resin.
UV Light Source:
- The quality and intensity of the UV light source play a significant role in the curing process. Ensure that the UV light used matches the specifications recommended by the epoxy manufacturer.
Thermal Conductivity:
- UV-cured epoxy may have different thermal conductivity properties compared to other potting materials. Consider the thermal requirements of your application and ensure that the chosen epoxy meets those needs.
Regulatory Compliance:
- Check if the epoxy formulation complies with relevant industry standards and regulations, mainly if your electronic device will be used in specific environments or applications.
UV Exposure Time:
- The curing time depends on the UV exposure, and inadequate exposure may result in incomplete curing. Follow the manufacturer’s guidelines regarding UV exposure time and intensity.
Volume and Viscosity:
- Consider the volume and viscosity of the epoxy. Some formulations better suit small, intricate components, while others may work well for larger encapsulations.
Always refer to the specific recommendations and guidelines provided by the epoxy manufacturer to ensure the successful application of UV-cured epoxy potting for your electronic components. Testing and prototyping are also essential to validate the performance and reliability of the potting process in your particular application.
Can UV-cured epoxy potting be applied to sensitive electronic components?
UV-cured epoxy potting can be applied to sensitive electronic components in some cases, but it’s essential to consider several factors before using this method:
Sensitivity of Components:
- Some electronic components are sensitive to heat and UV light. Ensure that the components you are potting can withstand the curing process without damage.
UV-Curing Process:
- UV-cured epoxy typically requires exposure to ultraviolet light for a specific period to harden. Ensure that the UV exposure won’t harm or degrade the performance of your electronic components.
Temperature Sensitivity:
- UV-curing processes might generate heat. Ensure that the curing process doesn’t subject the components to temperatures that could adversely affect their functionality.
Compatibility with Epoxy:
- Certain materials used in electronic components may not be compatible with epoxy. It’s essential to check the epoxy’s specifications and compatibility with the materials used in your components.
Potting Material Selection:
- Choose an epoxy formulation that meets the specific requirements of your application. Various types of UV-cured epoxies are available with different properties, such as thermal conductivity, flexibility, and adhesion strength.
Application Precision:
- UV-cured epoxy potting may require precision in application and curing. Ensure that you can apply the epoxy precisely to avoid accidental contact with sensitive areas of the electronic components.
Post-Curing Inspection:
- After potting, thoroughly inspect the components to ensure that the epoxy has cured correctly and that there are no air bubbles, voids, or other issues that could impact the long-term reliability of the electronic device.
Always refer to the datasheets and specifications provided by the epoxy and electronic component manufacturers to ensure compatibility and proper application. It’s also a good idea to conduct small-scale tests or consult experts if you have any questions about the potting process.
What types of materials can be effectively encapsulated with UV-cured epoxy?
UV-cured epoxy is a versatile material that can effectively encapsulate a variety of substrates. Here are some common materials that can be encapsulated with UV-cured epoxy:
Electronics:
- PCBs (Printed Circuit Boards)
- LED components
- Sensors
- Microchips
Optical Components:
- Lenses
- Optical fibers
- Prism assemblies
Decorative Items:
- Flowers, insects, and other small objects for crafts and jewelry
3D Prints:
- Encapsulation of 3D printed things for added strength and protection
Photovoltaic Cells:
- Solar cells and modules
Medical Devices:
- Encapsulation of medical sensors and components
Microelectromechanical Systems (MEMS):
- MEMS devices and sensors
Artwork and Collectibles:
- Encapsulation of delicate or valuable items for preservation
Dental Applications:
- Encapsulation of dental prosthetics and other dental materials
Microelectronics and Nanotechnology:
- Nanostructures and microelectronic devices
Fiber Optics:
- Fiber optic connectors and splices
Industrial Components:
- Various industrial components requiring protection and reinforcement
It’s important to note that the effectiveness of encapsulation depends on factors such as the formulation of the UV-cured epoxy, the compatibility with the material being encapsulated, and the specific application requirements. Always refer to the manufacturer’s guidelines and conduct compatibility tests to ensure the desired performance.
How does the curing time of UV epoxy compare to other potting methods?
The curing time of UV epoxy can vary depending on the specific product and its formulation—UV epoxy cures rapidly when exposed to ultraviolet (UV) light. The UV light initiates the curing process, and it typically takes only a few seconds to a few minutes to harden completely.
Compared to other potting methods, such as traditional epoxy resins, silicone, or polyurethane potting compounds, UV epoxy tends to have a much quicker curing time. Conventional epoxy resins often require hours to heal; some formulations may take several days to reach full strength.
Silicone and polyurethane potting compounds also have curing times ranging from a few hours to several days, depending on the specific product and the environmental conditions.
Here are some general comparisons:
- UV Epoxy:Cures in seconds to minutes when exposed to UV light.
- Traditional Epoxy Resins:Typically take several hours to cure and may require even longer for complete curing.
- Silicone Potting Compounds:Cure times can vary, but they often take several hours to a day or more to fully cure.
- Polyurethane Potting Compounds:Cure times can range from a few hours to several days, depending on the formulation.
The choice of potting method depends on the specific application requirements, including the desired curing time, the type of materials being encapsulated, and other environmental factors. UV epoxy is often preferred when a fast cure time is critical, but it may not be suitable for all applications. It’s essential to consider the specific needs of your project and choose a potting method accordingly.
What are the temperature and environmental considerations for UV-cured epoxy potting?
UV-cured epoxy potting encapsulates electronic components or devices using epoxy resin that is cured or hardened using ultraviolet (UV) light. The temperature and environmental conditions during the UV-cured epoxy potting process are crucial for achieving optimal results. Here are some considerations:
The temperature of the Work Environment:
- Optimal Temperature:UV-cured epoxy potting is typically carried out at room temperature (around 20-25°C or 68-77°F). This temperature range ensures proper flow and curing characteristics of the epoxy resin.
- Avoid Extreme Temperatures:Extreme temperatures, both high and low, can affect the viscosity and curing speed of the epoxy resin. Avoid working in conditions that are too hot or too cold.
Substrate Temperature:
- Preheat Substrate if Necessary:In some cases, preheating the substrate (the surface of the electronic components or device being potted) slightly can help improve the flow and adhesion of the epoxy resin.
Humidity:
- Low Humidity is Preferred:Low humidity conditions are generally preferred during the UV-cured epoxy potting. High humidity can affect the curing process and may lead to incomplete curing or reduced mechanical properties of the epoxy.
UV Light Exposure:
- Use Proper UV Intensity:The UV light source used for curing should have the appropriate intensity and wavelength for the epoxy resin. Follow the manufacturer’s guidelines for UV exposure.
- Ensure Uniform Exposure:To achieve uniform curing, the UV light is evenly distributed across the entire potted area.
Epoxy Resin Characteristics:
- Choose Suitable Epoxy Resin:Different epoxy resins may have specific temperature and curing requirements. Select an epoxy resin that is compatible with the application and environmental conditions.
- Understanding Curing Time:The curing time of the epoxy resin may be influenced by temperature. Warmer temperatures can accelerate the curing process, while cooler temperatures may slow it down.
Ventilation:
- Adequate Ventilation:Ensure proper ventilation in the working area, mainly if the epoxy resin emits volatile compounds during curing.
Always refer to the specific product data sheets and technical documentation the epoxy resin manufacturer provided for detailed temperature and environmental consideration guidelines. Additionally, consider conducting small-scale tests or trials to optimize the process parameters for your specific application.
Are there specific safety precautions when working with UV-cured epoxy potting systems?
Yes, working with UV-cured epoxy potting systems requires specific safety precautions to ensure the well-being of individuals and achieve successful outcomes. Here are some general safety guidelines:
Personal Protective Equipment (PPE):
- Eye Protection:Wear safety goggles or a face shield to protect your eyes from UV radiation during curing.
- Skin Protection:Use gloves to prevent direct contact with the epoxy resin. Some people may develop skin sensitivities to epoxy, so protecting your skin is essential.
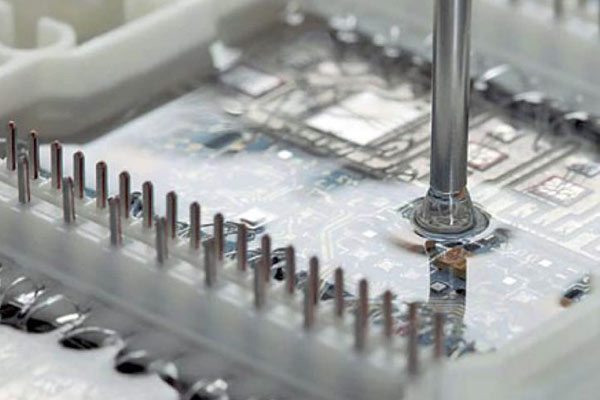
Ventilation:
- Work in a well-ventilated area or use an appropriate fume extraction system to minimize exposure to vapors emitted during curing.
UV Exposure:
- Avoid direct exposure to UV light. UV light used for curing can be harmful to the eyes and skin. Use barriers or curtains to contain the UV light within the working area.
Curing in Stages:
- Cure epoxy in stages rather than all at once. This allows for better control and minimizes the risk of incomplete curing.
Material Handling:
- Follow the manufacturer’s guidelines for handling and mixing the epoxy resin. Use the recommended mixing ratios and ensure thorough mixing for proper curing.
Temperature Control:
- Maintain the recommended temperature during the curing process. Extreme temperatures can affect the epoxy’s curing time and final properties.
Emergency Preparedness:
- Be familiar with the location of emergency exits, eyewash stations, and first aid facilities. Have a plan in case of accidental exposure or spills.
Training:
- Ensure that all personnel handling and curing UV-cured epoxy are adequately trained on the specific procedures and safety precautions.
Material Compatibility:
- Ensure that the potted substrates and materials are compatible with the epoxy resin. Some materials may be sensitive to the heat generated during the curing process.
Storage:
- Store epoxy materials in a cool, dry place and follow the manufacturer’s recommendations for storage conditions.
Always refer to the specific guidelines provided by the manufacturer of the UV-cured epoxy system you are using, as there may be variations in the recommendations based on the product’s formulation.
What are the key factors when selecting a UV-cured epoxy potting material?
Selecting the proper UV-cured epoxy potting material is crucial to achieving your application’s desired performance and reliability. Here are vital factors to consider when choosing a UV-cured epoxy potting material:
Application Requirements:
- Understand the specific requirements of your application, such as temperature resistance, electrical insulation, chemical resistance, and mechanical properties.
Curing Time:
- Consider the curing time of the epoxy. Some applications may require a faster curing process, while others may benefit from slower curing for better workability.
Viscosity:
- Viscosity affects the flow and penetration of the epoxy. Choose a viscosity that suits the application, considering factors like component encapsulation and ease of application.
Shrinkage:
- Evaluate the shrinkage characteristics of the epoxy during curing. Excessive shrinkage can lead to stress on components and affect the overall stability of the potting.
Adhesion:
- Ensure that the epoxy provides strong adhesion to the materials it will contact. Bonding is crucial for the stability and reliability of the potted components.
Chemical Resistance:
- Consider the chemical environment in which the potted components will operate. Select an epoxy with resistance to chemicals, solvents, and other substances in the application environment.
Thermal Stability:
- Evaluate the thermal stability of the epoxy, especially if the application involves exposure to high temperatures. Choose a material that can withstand the expected temperature range.
Electrical Properties:
- If electrical insulation is a requirement, ensure that the epoxy has the necessary dielectric strength and electrical insulation properties.
UV Stability:
- Consider the UV stability of the epoxy itself, especially if the potted components are exposed to sunlight or other sources of UV radiation.
Color and Appearance:
- Depending on the application, the color and appearance of the cured epoxy may be necessary. Some applications may require transparency or a specific shade for aesthetic reasons.
Cohesive Strength:
- Evaluate the epoxy’s cohesive strength to ensure sufficient support and encapsulation for the potted components.
Compliance and Certification:
- Ensure that the selected epoxy complies with relevant industry standards and certifications. This is particularly important in applications where regulatory compliance is required.
Supplier Reliability:
- Choose a reputable supplier that provides reliable and consistent epoxy products. Check for product documentation, technical support, and customer reviews.
Cost:
- Consider the overall cost of the epoxy material, including its purchase price, application efficiency, and any potential cost savings related to its performance and reliability.
By carefully considering these factors about your specific application requirements, you can choose a UV-cured epoxy potting material that meets the needs of your project and ensures long-term reliability.
Can UV-cured epoxy potting systems be used for outdoor applications?
UV-cured epoxy potting systems can be used for outdoor applications, but their suitability depends on several factors. Here are some considerations to keep in mind when using UV-cured epoxy potting systems in outdoor environments:
UV Resistance:
- UV-cured epoxies are generally considered UV-resistant, but the resistance level varies among products. Ensure that the epoxy you choose is designed for outdoor applications and protects against UV radiation.
Temperature Stability:
- Consider the temperature range of the outdoor environment. UV-cured epoxies should have good temperature stability to withstand fluctuations and extremes commonly encountered outdoors.
Moisture Resistance:
- Outdoor applications often expose materials to moisture. Ensure that the UV-cured epoxy has excellent moisture resistance to prevent degradation and maintain the integrity of the potted components.
Chemical Resistance:
- Evaluate the epoxy’s resistance to chemicals, pollutants, and other substances present in outdoor environments. This is crucial for maintaining the material’s performance and preventing degradation over time.
Physical Durability:
- Consider the physical stresses the potted components may encounter, such as mechanical impacts, vibrations, and weather-related stresses. Choose an epoxy with good physical durability to ensure the longevity of the encapsulated components.
Color Stability:
- UV exposure can cause color fading in some materials. If the color stability of the epoxy is essential for aesthetic reasons or for maintaining the visibility of components, choose a product with good color stability under UV exposure.
Application Thickness:
- The thickness of the applied epoxy layer can affect its UV resistance. Thicker layers provide better protection against UV radiation. Ensure that the recommended application thickness for UV resistance is followed.
Adhesion to Substrates:
- Verify that the UV-cured epoxy has strong adhesion to the substrates used in the outdoor application. Proper bonding is crucial for preventing water ingress and maintaining the overall effectiveness of the potting.
Long-Term Performance:
- Consider the long-term performance requirements of the outdoor application. UV-cured epoxies should be selected based on their ability to maintain performance over extended periods in outdoor conditions.
Regulatory Compliance:
- Ensure that the chosen UV-cured epoxy complies with any relevant industry standards and regulations for outdoor applications.
It’s essential to consult with the epoxy manufacturer and carefully review the product’s technical data sheets and specifications to ensure that it meets the specific requirements of your outdoor application. Additionally, conducting thorough testing and validation in simulated or actual outdoor conditions can help confirm the performance of the chosen UV-cured epoxy potting system.
How does UV exposure affect the long-term performance of epoxy-potted electronics?
UV exposure can have several effects on the long-term performance of epoxy-potted electronics. The impact largely depends on the formulation of the epoxy resin used, the duration and intensity of UV exposure, and the specific environmental conditions. Here are some ways UV exposure can affect epoxy-potted electronics:
Yellowing and Discoloration:
- Continuous exposure to UV radiation can lead to yellowing or discoloration of epoxy materials over time. This aesthetic change may not impact the functionality of the electronics but can affect the appearance.
Degradation of Physical Properties:
- Prolonged UV exposure can contribute to the degradation of the physical properties of epoxy resins. This may result in changes to the material’s hardness, flexibility, and overall durability, potentially impacting its ability to protect and support the electronics.
Loss of Transparency:
- UV exposure may cause UV-cured epoxy resins to lose transparency. If optical clarity is essential for the functionality of the potted electronics, UV-induced opacity can be a concern.
Reduced Adhesion:
- UV radiation can affect the adhesion properties of epoxy resins, leading to reduced bonding with the encapsulated components or the substrate. This can compromise the overall integrity of the potting.
Thermal Stability:
- UV exposure may contribute to decreased thermal stability, potentially affecting the epoxy’s ability to withstand high temperatures. This is particularly important in outdoor applications where electronics may be exposed to sunlight and elevated temperatures.
Cracking and Crazing:
- UV-induced degradation can result in the formation of microcracks or crazing in the epoxy material. This can compromise the protective barrier provided by the epoxy, allowing environmental factors such as moisture or contaminants to penetrate and affect the electronics.
Impact on Electrical Properties:
- While UV exposure may not directly impact the electrical properties of the epoxy, changes in material properties (such as increased resistivity due to degradation) could indirectly affect the electrical performance of the potted electronics.
Accelerated Aging:
- UV exposure can accelerate the aging process of epoxy materials, leading to a shortened lifespan of the potted electronics. This is particularly relevant in outdoor applications where the electronics are continuously exposed to sunlight.
To mitigate the effects of UV exposure on epoxy-potted electronics, it’s essential to choose UV-resistant epoxy formulations specifically designed for outdoor or UV-exposed environments. Manufacturers often provide information on the UV stability of their epoxy products, including recommendations for application thickness and expected performance under UV radiation.
Regular inspection and testing of epoxy-potted electronics in actual or simulated outdoor conditions can help assess the long-term performance and address any issues that may arise from UV exposure.
Are there specific guidelines for preparing surfaces before applying UV-cured epoxy potting?
Surface preparation is crucial in ensuring proper adhesion and the overall effectiveness of UV-cured epoxy potting. Here are some general guidelines for preparing surfaces before applying UV-cured epoxy potting:
Cleanliness:
- Ensure that the surfaces to be potted are clean and free from dirt, dust, grease, oils, and any other contaminants. Use appropriate cleaning agents and methods to achieve a thorough cleaning.
Mechanical Abrasion:
- Consider lightly abrading the surface to enhance adhesion depending on the substrate material. Mechanical abrasion, such as sanding or scuffing, creates a roughened surface that promotes better bonding.
Solvent Cleaning:
- For some substrates, solvent cleaning may be necessary to remove residual oils or contaminants. Use a solvent compatible with the substrate and the epoxy resin, and ensure that the solvent has completely evaporated before applying the epoxy.
Surface Activation:
- Some materials, such as plasma or corona, such as plasma or corona may benefit from surface activation treatments. These processes can modify the surface energy of the substrate and improve adhesion.
Moisture Control:
- Moisture can affect the curing and adhesion of epoxy resins. Ensure that the surfaces are dry before applying the UV-cured epoxy. In environments with high humidity, consider using a moisture-resistant epoxy.
Compatibility Testing:
- Perform compatibility testing to ensure the chosen epoxy resin adheres well to the specific substrate material. Some materials may require special primers or adhesion promoters.
Removal of Loose Particles:
- Remove any loose particles or debris from the surface that could interfere with the potting process or compromise the integrity of the epoxy bond.
Masking:
- Use masking materials to protect areas that should not be potted if necessary. This is particularly important if the potted components have specific contact points or if potting needs to be restricted to particular regions.
Surface Roughness:
- Consider the desired surface roughness for optimal adhesion. Some epoxy formulations may require a certain level of surface roughness to ensure a strong bond.
Temperature Considerations:
- Ensure the substrate and ambient temperatures are within the recommended range for the substrate material and the UV-cured epoxy. Extreme temperatures can affect the curing process and adhesion.
Primer Application:
- Applying a primer or adhesion promoter before potting can improve the bonding between the substrate and the epoxy resin. Follow the manufacturer’s recommendations regarding the use of primers.
Always refer to the specific guidelines provided by the manufacturer of the UV-cured epoxy resin for surface preparation instructions. Depending on the intended substrate and application, different epoxy formulations may have particular requirements. Following the manufacturer’s recommendations is essential for achieving the best results and ensuring the long-term performance of the potted components.
What role does viscosity play in UV-cured epoxy potting formulations?
Viscosity is an essential property in UV-cured epoxy potting formulations and plays a crucial role in the application and performance of the material. UV-cured epoxy potting formulations are commonly used for encapsulating electronic components, providing protection and insulation. Here are some critical aspects of viscosity in this context:
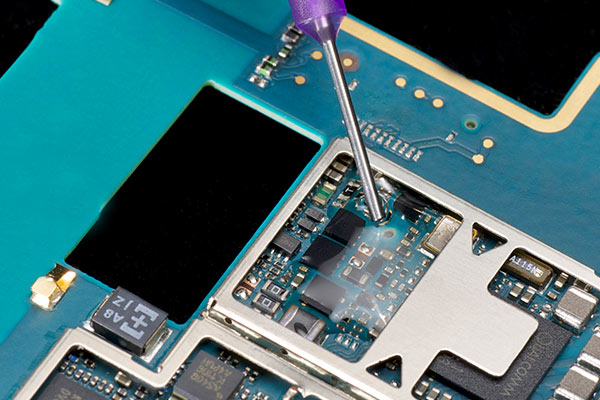
Ease of Application:
- Low Viscosity:A softer viscosity epoxy formulation is generally easier to handle and dispense. It allows for better flow and wetting of the components, ensuring that the epoxy can penetrate and encapsulate complex or delicate structures.
- High Viscosity:Conversely, higher viscosity formulations may be preferred for vertical or overhead applications, as they are less likely to sag or drip during curing.
Encapsulation and Penetration:
- Low Viscosity:Epoxy formulations with lower viscosity can better penetrate and encapsulate intricate or densely packed electronic components, ensuring the epoxy reaches and surrounds all critical areas.
- High Viscosity:Higher viscosity formulations may be used when a thicker layer of epoxy is desired for additional protection or when encapsulating components with more significant gaps or clearances.
Curing Depth:
- Low Viscosity:Lower viscosity formulations can facilitate deeper curing, allowing the UV light to penetrate and heal the epoxy throughout the encapsulated volume. This is particularly important for ensuring the complete cure of the epoxy.
- High Viscosity:Higher viscosity formulations may limit the depth of cure, primarily if the material cannot flow and spread quickly into confined spaces.
Controlled Flow:
- Viscosity Control:Maintaining a consistent viscosity is crucial for achieving uniform coverage and avoiding issues such as air entrapment or incomplete encapsulation. Proper viscosity control is essential for achieving reliable and consistent results in manufacturing processes.
Final Material Properties:
- Viscosity and Mechanical Properties:The epoxy formulation’s viscosity can influence the cured material’s mechanical properties. Adjusting the viscosity can impact the cured epoxy’s flexibility, hardness, and other mechanical characteristics.
It’s important to note that the specific requirements for viscosity in UV-cured epoxy potting formulations depend on the application, the types of electronic components being encapsulated, and the desired performance characteristics of the final product. Formulators often optimize the epoxy formulation’s viscosity to meet the intended application’s specific needs.
Can UV-cured epoxy potting be used for large-scale production?
UV-cured epoxy potting can be used for large-scale production in specific applications. Still, its suitability depends on various factors, such as the particular requirements of the production process, the size and complexity of the components being potted, and the desired properties of the final product. Here are some considerations:
- Speed of Cure:UV-cured epoxy offers a faster curing process than traditional epoxy potting methods, making it suitable for high-speed production lines. The quick curing time can contribute to increased efficiency and throughput.
- Precision and Control:UV curing provides precise control over the curing process. This is advantageous for applications that require specific curing conditions, and it allows for better control over the quality of the potting.
- Energy Efficiency:UV curing is typically more energy-efficient than other curing methods, as it relies on ultraviolet light rather than heat. This can result in cost savings and a more environmentally friendly production process.
- Material Compatibility:Ensure the UV-cured epoxy is compatible with the potted materials. Compatibility issues may arise with specific substrates or components, so it’s essential to conduct thorough testing to ensure the desired adhesion and performance.
- Equipment Investment:Implementing UV-cured epoxy potting may require an initial investment in UV-curing equipment. This includes UV lamps, conveyors, and curing chambers. Consider the cost of this equipment and its integration into your production line.
- Volume and Scale:UV curing may be well-suited for applications with more minor to medium-sized components. Large-scale production may require multiple UV curing stations or continuous curing systems to accommodate the size and volume of the products.
- Process Control and Monitoring:Implementing UV-cured epoxy potting on a large scale requires robust process control and monitoring systems. Ensure the curing conditions are consistent across the entire production line to maintain product quality.
- Regulatory Compliance:Consider any regulatory requirements or industry standards that may impact using UV-cured epoxy in your specific application. Ensure that the chosen materials and processes meet the necessary standards for your industry.
Before transitioning to UV-cured epoxy potting for large-scale production, it’s advisable to conduct thorough testing and optimization to ensure the process meets the desired production goals and quality standards. Additionally, consulting with experts in UV curing technology and epoxy formulations can provide valuable insights into your application’s feasibility and best practices.
What testing and quality control measures are recommended for UV-cured epoxy-potted devices?
UV-cured epoxy potting is commonly used to protect electronic devices from environmental factors such as moisture, vibration, and temperature fluctuations. To ensure the reliability and functionality of UV-cured epoxy-potted devices, it’s essential to implement thorough testing and quality control measures. Here are some recommendations:
Visual Inspection:
- Perform a visual inspection of the epoxy-potted devices to check for any visible defects, such as air bubbles, cracks, or incomplete potting.
Dimensional Inspection:
- Verify that the epoxy potting conforms to the specified dimensions. Ensure that no variations could affect the functionality or fit within the intended application.
Adhesion Testing:
- Assess the adhesion of the epoxy to the components and the enclosure. Perform tests to check for delamination or separation between the epoxy and the surfaces to which it is supposed to adhere.
UV Cure Quality Control:
- Monitor and control the UV curing process to ensure the epoxy cures completely and uniformly. Use appropriate UV intensity meters to measure and maintain consistent curing conditions.
Material Compatibility Testing:
- Please verify that the epoxy material is compatible with all its encapsulated components. Some materials may have adverse reactions with certain substances, leading to degradation over time.
Accelerated Aging Testing:
- Subject the epoxy-potted devices to accelerated aging tests to simulate the effects of prolonged exposure to environmental factors. This helps identify potential long-term issues such as yellowing, brittleness, or changes in electrical properties.
Thermal Cycling Testing:
- Perform thermal cycling tests to assess the device’s ability to withstand temperature variations. This is crucial for applications where the machine may be exposed to wide temperature ranges.
Moisture Resistance Testing:
- Test the epoxy-potted devices for moisture resistance. This can include humidity exposure tests or immersion in water to ensure that the potting material effectively protects against moisture ingress.
Electrical Testing:
- Conduct electrical tests to ensure that the encapsulated components function within specified parameters. Check for any changes in resistance, capacitance, or other electrical properties.
Vibration and Shock Testing:
- Subject the epoxy-potted devices to vibration and shock tests to simulate real-world conditions. Ensure that the potting material provides sufficient mechanical protection to prevent damage due to vibrations or shocks.
Corrosion Resistance Testing:
- If the device is intended for use in corrosive environments, perform corrosion resistance testing to ensure that the epoxy provides adequate protection against corrosion.
Documentation and Traceability:
- Maintain comprehensive documentation of the potting process, testing procedures, and results. This facilitates traceability and helps identify and address any issues that may arise during the quality control process.
Implementing these testing and quality control measures can help ensure the reliability and longevity of UV-cured epoxy-potted devices in various applications.
Are there any notable innovations or advancements in UV-cured epoxy potting technology?
There may have been further advancements in UV-cured epoxy potting technology. Here are some trends and potential improvements that were relevant at that time:
Fast-Curing Formulations:
- Advances in UV-cured epoxy formulations have focused on reducing curing times. Faster curing allows for increased production efficiency and shorter processing times.
Improved Thermal Conductivity:
- Enhancements in the thermal conductivity of UV-cured epoxy materials have been explored to address the thermal management needs of electronic components. This is especially important in applications where heat dissipation is a critical factor.
Enhanced Chemical Resistance:
- Innovations have been made to develop UV-cured epoxy formulations with improved resistance to chemicals, solvents, and other harsh environmental conditions. This is particularly valuable in applications where exposure to aggressive substances is a concern.
Optical Clarity and Light Transmission:
- Some applications, such as LED encapsulation, benefit from UV-cured epoxies with high optical clarity and light transmission properties. Improvements in these aspects contribute to the efficiency of optical devices.
Flexible and Toughened Formulations:
- There has been a focus on developing UV-cured epoxy materials that offer flexibility and toughness while maintaining good adhesion properties. This is especially important in applications where mechanical stresses or vibrations are a concern.
Bio-Based and Sustainable Materials:
- The industry has shown an interest in developing UV-cured epoxy formulations using bio-based or sustainable materials. This aligns with the broader trend toward environmentally friendly and renewable resources.
Nanoscale Additives:
- Incorporating nanoscale additives, such as nanoparticles or nanofillers, has been explored to enhance various properties of UV-cured epoxy materials, including mechanical strength, thermal conductivity, and barrier properties.
Innovative and Self-Healing Materials:
- Researchers have investigated integrating intelligent features, such as self-healing capabilities, into UV-cured epoxy materials. Self-healing materials can repair minor damage autonomously, improving the overall durability of the encapsulated devices.
Customizable Properties:
- Advancements have allowed users to customize specific properties of UV-cured epoxy formulations, such as viscosity, hardness, and flexibility. This customization capability provides versatility for different applications.
It’s important to note that the field of materials science and epoxy technology is dynamic, with ongoing research and development. I recommend checking recent scientific literature, industry publications, and updates from manufacturers and research institutions for the latest information on innovations and advancements in UV-cured epoxy potting technology.
How can users troubleshoot common issues related to UV-cured epoxy potting applications?
Troubleshooting common issues related to UV-cured epoxy potting applications involves a systematic approach to identify and address potential problems. Here are some common issues and corresponding troubleshooting steps:
Incomplete Curing:
- Issue:The epoxy does not cure fully, resulting in a sticky or tacky surface.
- Troubleshooting:
- Check the UV light intensity: Ensure that the UV light source provides the recommended intensity for the specified epoxy formulation.
- Verify curing time: Ensure the epoxy is exposed to UV light for the recommended duration.
- Check for shadowed areas: Ensure that all parts of the epoxy are exposed to UV light and there are no shadowed areas.
Yellowing or Discoloration:
- Issue:The epoxy exhibits yellowing or discoloration over time.
- Troubleshooting:
- Evaluate UV exposure: Excessive exposure to UV light can lead to discoloration. Ensure that the curing process follows recommended guidelines.
- Consider UV stabilizers: Some formulations include UV stabilizers to reduce discoloration. Check if your epoxy formulation consists of these additives.
Poor Adhesion:
- Issue:The epoxy does not adhere well to the substrate or components.
- Troubleshooting:
- Surface preparation: Ensure surfaces are clean, dry, and contaminant-free before applying the epoxy.
- Verify compatibility: Confirm that the epoxy formulation is compatible with the materials it is supposed to adhere to.
- Improve adhesion promoters: Consider using adhesion promoters or primers to challenge bonding substrates.
Cracking or Brittle Potting:
- Issue:The cured epoxy becomes brittle or develops cracks.
- Troubleshooting:
- Assess formulation: Check if the epoxy formulation is suitable for the intended application and if it provides the required flexibility.
- Evaluate thermal properties: Ensure the epoxy can withstand thermal expansion and contraction without cracking.
- Consider additives: Some formulations include toughening agents to improve flexibility and impact resistance.
Moisture Ingress:
- Issue:Moisture penetrates the epoxy, leading to functional or electrical problems.
- Troubleshooting:
- Verify curing conditions: Incomplete curing can compromise the epoxy’s ability to act as a barrier against moisture. Ensure proper UV exposure during curing.
- Inspect for voids: Voids or air bubbles in the cured epoxy may create paths for moisture ingress. Adjust the potting process to minimize voids.
Electrical Issues:
- Issue:Electrical components within the potted device are malfunctioning.
- Troubleshooting:
- Check for conductive contaminants: Ensure that no contaminants are present in the epoxy formulation or on the potted surfaces.
- Assess insulation properties: Verify that the epoxy provides adequate electrical insulation for the components.
Poor Thermal Management:
- Issue:The epoxy does not effectively dissipate heat, leading to overheating of components.
- Troubleshooting:
- Evaluate thermal conductivity: Choose an epoxy formulation with enhanced thermal conductivity or consider alternative thermal management solutions.
- Assess encapsulation design: Ensure that the encapsulation design allows for effective heat dissipation.
Viscosity Issues:
- Issue:The epoxy has difficulty flowing into intricate spaces or around components.
- Troubleshooting:
- Adjust viscosity: Choose an epoxy formulation with a viscosity suitable for the application, or consider heating the epoxy to reduce viscosity temporarily.
- Optimize the potting process: Modify the potting process to ensure that the epoxy adequately fills all spaces.
When troubleshooting UV-cured epoxy potting issues, it’s essential to carefully follow the manufacturer’s guidelines for both the epoxy formulation and the UV curing process. If problems persist, consulting with the epoxy manufacturer or seeking expert assistance in epoxy applications may be beneficial. Additionally, keeping detailed records of the potting process and any observed issues can aid in identifying patterns and solutions.
Conclusion:
In conclusion, UV cured epoxy potting systems represent a revolutionary approach to electronic encapsulation, offering efficiency, durability, and versatility. As technology continues to evolve, staying informed about the intricacies of UV cured epoxy potting becomes increasingly essential. We hope this guide has provided valuable insights into this fascinating field, empowering you with the knowledge needed to make informed decisions and leverage the full potential of UV cured epoxy potting systems in your applications. If you have further questions or need assistance, feel free to explore our related articles or reach out to our expert team.
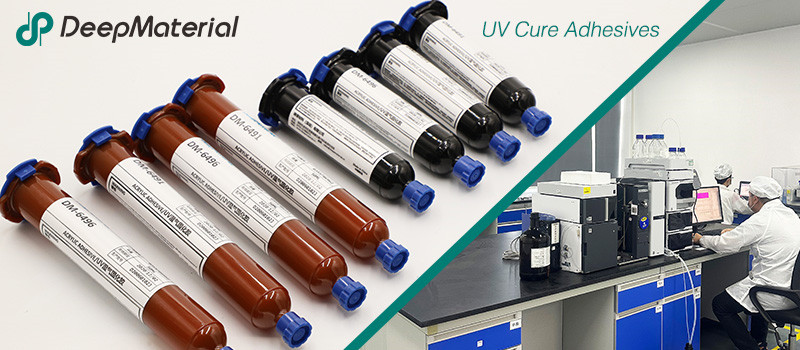
DeepMaterial
Based on the core technology of adhesives, DeepMaterial has developed adhesives for chip packaging and testing, circuit board level adhesives, and adhesives for electronic products. Based on adhesives, it has developed protective films, semiconductor fillers, and packaging materials for semiconductor wafer processing and chip packaging and testing. More…
UV Curing Adhesives
UV light cure have a number of benefits making them a popular choice among many product assembly and manufacturing applications. Many UV light cure adhesives can provide a nearly instantaneous bond to difficult substrates like glass and plastic. UV cure adhesives often require an accelerator or UV light for a bond to form.
Adhesive Blogs & News
The latest adhesive industry science and technology, Deepmaterial news, and market trends and forecasts.
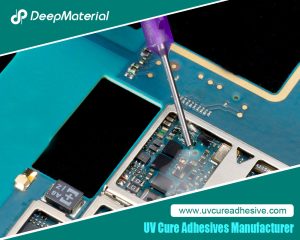
Biocompatibility of LED UV Glue Adhesive and Its Application Potential in Medical and Food Packaging Fields
Biocompatibility of LED UV Glue Adhesive and Its Application Potential in Medical and Food Packaging Fields LED UV glue adhesive has been widely applied in numerous fields due to its advantages such as rapid curing and easy operation. However, in fields with stringent safety requirements like medical and food packaging, its biocompatibility after curing becomes
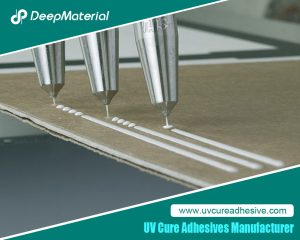
Biocompatibility of LED UV Glue Adhesive and Its Application Potential in Medical and Food Packaging Fields
Biocompatibility of LED UV Glue Adhesive and Its Application Potential in Medical and Food Packaging Fields LED UV glue adhesive has been widely applied in numerous fields due to its advantages such as rapid curing and easy operation. However, in fields with stringent safety requirements like medical and food packaging, its biocompatibility after curing
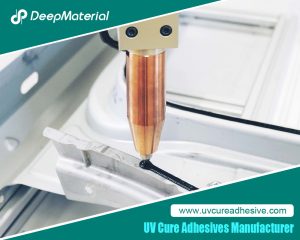
Exploring the Environmental Performance of UV Glue and Strategies for Optimizing Odor and VOC Content
Exploring the Environmental Performance of UV Glue and Strategies for Optimizing Odor and VOC Content UV glue, as an adhesive that achieves rapid curing through ultraviolet (UV) light irradiation, has been widely applied in numerous fields such as electronics, optics, healthcare, and automobiles, thanks to its advantages of fast curing speed, high bonding strength, and
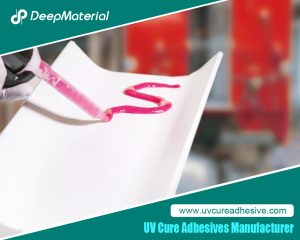
Compatibility Analysis and Countermeasures of LED UV Glue with Automated Production Equipment
Compatibility Analysis and Countermeasures of LED UV Glue with Automated Production Equipment LED UV glue has been widely used in modern manufacturing due to its advantages such as fast curing speed, high bonding strength, and environmental friendliness. However, in the automated production process, if there are problems with the adaptability between the glue and equipment
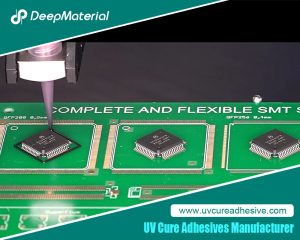
Influence of Viscosity and Thixotropy of Glue on the Quality of Glue Dots in the Dispensing Process and Solutions
Influence of Viscosity and Thixotropy of Glue on the Quality of Glue Dots in the Dispensing Process and Solutions The dispensing process is an important part of the application of LED UV glue adhesive, and the quality of this process directly affects the final performance of the product. The physical properties of the glue,
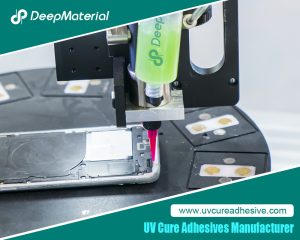
Aging Mechanism and Modification Strategies of LED UV Glue under Long-term Ultraviolet Irradiation
Aging Mechanism and Modification Strategies of LED UV Glue under Long-term Ultraviolet Irradiation LED UV glue, with its advantages of fast curing speed, high bonding strength, and environmental friendliness, has been widely used in fields such as optical device packaging, electronic assembly, and medical devices. However, in scenarios where it is exposed to ultraviolet environments