- Home
- >
- UV Cure Adhesive
- >
- UV Cure Anaerobic Adhesive
UV Cure Anaerobic Adhesive
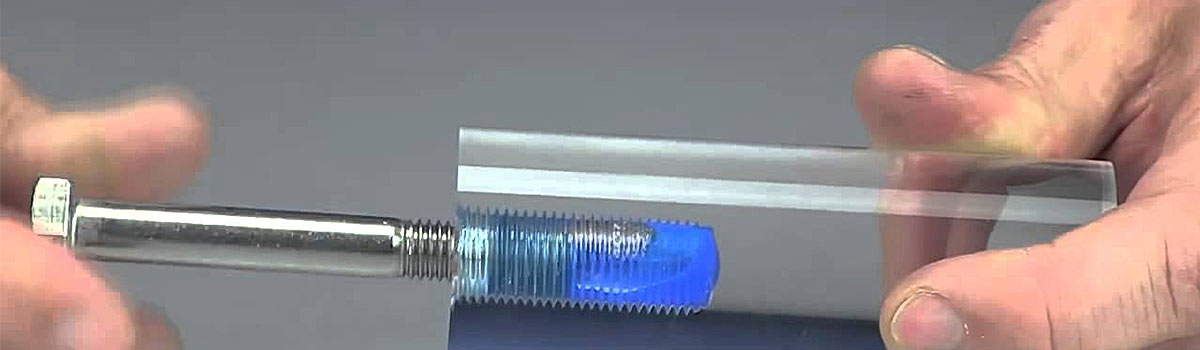
UV Cure Anaerobic Adhesive, a revolutionary solution in the field of bonding and sealing. UV Cure Anaerobic Adhesives are specially formulated to cure rapidly when exposed to ultraviolet (UV) light, providing quick and efficient bonding in anaerobic conditions. This adhesive type offers superior performance in applications where traditional adhesives fall short, ensuring robust and durable bonds.
Table of Contents
ToggleHow does UV Cure Anaerobic Adhesive work?
UV-curable anaerobic adhesives combine the benefits of anaerobic and ultraviolet (UV) light curing to create a unique bonding solution. Here’s an overview of how UV-cure anaerobic adhesives work:
Anaerobic Curing:
- Anaerobic adhesives:These adhesives are designed to cure without air (oxygen). They remain liquid as long as they are exposed to oxygen but cure (harden) when oxygen is excluded. Anaerobic adhesives, such as nuts and bolts, are commonly used for bonding threaded fasteners.
UV Light Curing:
- UV curinginvolves using ultraviolet light to initiate a chemical reaction that causes the adhesive to cure and harden. UV light triggers the polymerization of the adhesive, turning it from a liquid to a solid state.
Combining Anaerobic and UV Curing:
- In UV-cure anaerobic adhesives, the anaerobic curing mechanism keeps the adhesive liquid until it is exposed to UV light. This means that the adhesive remains workable as long as it is exposed to oxygen in the air.
Application Process:
- The application process typically involves applying the adhesive to the parts to be bonded, ensuring that the parts are correctly aligned. The adhesive remains liquid until the parts are assembled, preventing premature curing.
UV Exposure:
- Once the parts are made, UV light is applied to the bonded area. The UV light triggers the curing process, causing the anaerobic adhesive to harden and create a strong bond between the parts.
Advantages:
- The combination of anaerobic and UV curing provides several advantages, including:
- Control over the curing process: The adhesive only cures when exposed to UV light.
- Instant curing: UV curing allows for rapid bond formation.
- Anaerobic properties: The adhesive remains liquid until the parts are assembled, preventing premature curing.
Applications:
- UV-cure anaerobic adhesives are commonly used in applications where rapid curing, precise control over the curing process, and the benefits of anaerobic adhesives are desired. They are often employed in manufacturing, electronics, and assembly industries.
It’s important to note that the specific formulation of UV-cure anaerobic adhesives can vary among manufacturers, and the application process may be tailored to suit the requirements of particular bonding applications.
What are the advantages of using UV Cure Anaerobic Adhesive?
UV cure anaerobic adhesives offer several advantages in various applications. Here are some key benefits:
- Rapid Cure Time:UV cure anaerobic adhesives cure quickly when exposed to ultraviolet (UV) light. This immediate curing process allows for fast assembly and reduced production time.
- On-Demand Curing:The curing process is initiated by exposure to UV light, providing better control over the bonding process. This allows for precise positioning of components before curing begins.
- No Oxygen Inhibition:Unlike traditional anaerobic adhesives that rely on the absence of oxygen for curing, UV-cure anaerobic adhesives do not require an oxygen-free environment. This makes them more versatile and suitable for a broader range of applications.
- Versatility:UV cure anaerobic adhesives are universal and can be used for bonding a variety of substrates, including metals, plastics, and ceramics. This makes them suitable for diverse industrial applications.
- Reduced Wastage:Since the curing process is controlled by exposure to UV light, there is less likelihood of adhesive being wasted due to premature curing. This can result in cost savings and more efficient use of materials.
- Enhanced Bond Strength:UV cure anaerobic adhesives often exhibit high bond strength, providing reliable and durable connections between components.
- Environmental Benefits:UV cure adhesives typically contain fewer volatile organic compounds (VOCs) than solvent-based adhesives. This can contribute to a more environmentally friendly manufacturing process.
- Improved Productivity:UV cure anaerobic adhesives’ fast curing time and on-demand curing capability contribute to increased assembly process productivity. This is particularly beneficial in high-volume manufacturing settings.
- Reduced Heat Generation:UV cure adhesives generate less heat during curing than other adhesive technologies. This is advantageous for applications where heat-sensitive materials are involved.
- Enhanced Shelf Life:UV cure anaerobic adhesives often have a longer shelf life than other adhesives. This can benefit industries where products may be stored for extended periods before use.
It’s important to note that while UV cure anaerobic adhesives offer these advantages, the choice of adhesive depends on specific application requirements. It’s advisable to consider factors such as substrate compatibility, environmental conditions, and the overall performance needed for a particular application.
In which industries are UV Cure Anaerobic Adhesive commonly used?
UV cure anaerobic adhesives find applications in various industries due to their rapid curing, versatility, and other advantageous properties. Some of the sectors where UV cure anaerobic adhesives are commonly used include:
- Electronics Manufacturing:UV cure anaerobic adhesives are used to bond and encapsulate electronic components and devices. The quick curing time is beneficial in high-volume production settings.
- Medical Devices:These adhesives are utilized in the assembly of medical devices, such as catheters, sensors, and electronic components, where precision bonding and quick curing are essential.
- Automotive:UV cure anaerobic adhesives are employed in the automotive industry for bonding and sealing applications. They are used to assemble components such as sensors, connectors, and interior elements.
- Aerospace:In the aerospace sector, UV cure anaerobic adhesives are applied for bonding and sealing electronic components and in the assembly of aircraft interiors.
- Optics and Photonics:UV cure adhesives bond optical components, lenses, and fiber optics. Their ability to cure on demand and their precision make them suitable for these applications.
- Telecommunications:UV cure anaerobic adhesives are utilized to assemble telecommunications equipment, including the bonding of connectors, cables, and electronic components.
- LED and Lighting Industry:UV cure adhesives are commonly used to make LED components, where rapid curing and precision are essential for maintaining the performance of the lighting devices.
- Consumer Electronics:These adhesives are employed in the manufacturing of consumer electronics, including the bonding of components in smartphones, tablets, and other electronic gadgets.
- Industrial Equipment:UV cure anaerobic adhesives find applications in various industrial equipment where rapid assembly and reliable bonding are required.
- Medical Device Packaging:UV cure adhesives are used for bonding and sealing medical device packaging, ensuring a secure and sterile environment.
- Jewelry Manufacturing:In jewelry production, UV cure adhesives are employed for bonding and setting stones, offering precision and speed in the manufacturing process.
It’s important to note that the suitability of UV cure anaerobic adhesives depends on the specific requirements of each application. Substrate compatibility, cure time, and environmental conditions should be considered when selecting an adhesive for a particular industry or application.
Can UV Cure Anaerobic Adhesive bond different types of materials?
UV-curable anaerobic adhesives are typically designed for bonding similar or compatible materials. These adhesives are commonly used for bonding metals, glass, and certain plastics. The anaerobic curing mechanism involves excluding air (oxygen) and the presence of metal ions, which initiates the curing process. UV light is often used to create the curing reaction in these adhesives.
While UV-curable anaerobic adhesives can effectively bond similar materials, their compatibility with different materials may vary. It’s essential to check the product specifications and technical data sheet provided by the adhesive manufacturer to determine the compatibility with specific materials.
Factors influencing the bond strength and compatibility include:
- Surface Energy:Materials with similar surface energies often bond well. Adhesives may have difficulty bonding materials with significantly different surface energies.
- Chemical Compatibility:The adhesive should be chemically compatible with the related materials. Some materials may resist bonding with certain adhesives due to their chemical composition.
- Substrate Porosity:Adhesives may not work well on highly porous materials, as the adhesive may be absorbed into the substrate, affecting bond strength.
- Thermal Expansion Coefficients:If the materials being bonded have significantly different thermal expansion coefficients, it may affect the long-term stability of the bond, especially in varying temperature conditions.
- UV Transparency:Materials that are transparent to UV light allow for better penetration of the curing light, which can impact the effectiveness of the adhesive.
It’s advisable to conduct compatibility tests on a small scale before using UV-curable anaerobic adhesives for critical applications or when bonding different materials. Additionally, consulting with the adhesive manufacturer or technical support for specific guidance on the intended application is recommended.
What are the curing times for UV-cured anaerobic adhesives?
The curing times for UV cure anaerobic adhesives can vary depending on the specific product and its formulation. UV cure anaerobic adhesives typically cure rapidly when exposed to ultraviolet (UV) light. The curing process is initiated by exposure to UV light and is often referred to as light-activated curing.
Here are some general guidelines:
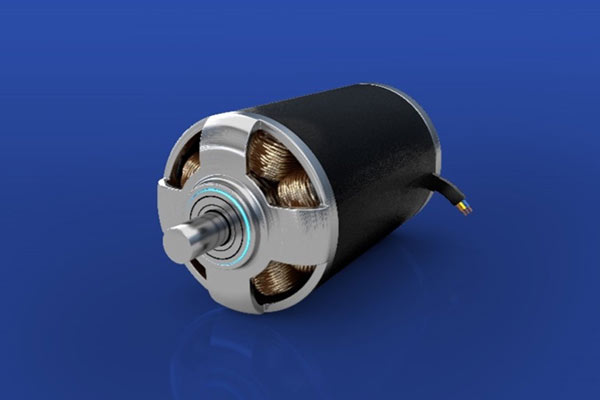
- Light Intensity:The curing time is influenced by the intensity of the UV light. Higher light intensities generally lead to faster curing times.
- Wavelength:The wavelength of the UV light source is crucial for initiating the curing process. Ensure that the wavelength of the UV light matches the requirements specified by the adhesive product.
- Thickness of the Adhesive:Thicker layers of adhesive may require longer exposure times to ensure complete curing throughout the depth of the adhesive.
- Adhesive Formulation:Different UV cure anaerobic adhesives may have different formulations, and the curing time can be influenced by the specific chemicals used in the adhesive.
- Temperature:In some cases, temperature can also affect the curing time. Warmer temperatures may accelerate the curing process.
It’s essential to refer to the product datasheet or technical specifications provided by the adhesive manufacturer. These documents usually include recommended curing times, light intensity requirements, and other important information specific to the product.
If you have a specific UV cure anaerobic adhesive in mind, I recommend checking the product documentation or contacting the manufacturer for precise information on curing times and conditions.
Are these adhesives resistant to environmental factors?
UV-cure anaerobic adhesives are unique formulations designed to cure rapidly when exposed to ultraviolet (UV) light. These adhesives offer several advantages, including fast curing times, high bond strength, and the ability to bond various substrates. However, their resistance to environmental factors can vary based on the specific formulation and intended application.
In general, UV-cure anaerobic adhesives exhibit good resistance to environmental factors such as temperature extremes, moisture, and chemicals. The rapid curing process initiated by UV light ensures that the adhesive forms a strong bond quickly, reducing the vulnerability to environmental conditions during the curing phase. Once cured, these adhesives can withstand various temperatures, making them suitable for indoor and outdoor applications.
UV-cure anaerobic adhesives are often known for their excellent chemical resistance. They can resist exposure to oils, solvents, and other harsh chemicals, making them suitable for use in environments where chemical exposure concerns them. This resistance benefits applications such as bonding components in automotive, electronics, and industrial settings.
However, it’s essential to note that the overall performance of UV-cure anaerobic adhesives can be influenced by factors such as the specific formulation, substrate materials, and the intended end-use conditions. While these adhesives offer good resistance to many environmental elements, it’s advisable to consult the manufacturer’s guidelines and conduct thorough testing to ensure compatibility with the specific application and environmental conditions.
UV-cure anaerobic adhesives generally resist environmental factors, including temperature extremes, moisture, and chemicals. Their rapid curing and strong bond formation make them suitable for various applications requiring quick and durable bonding.
Can UV Cure Anaerobic Adhesive be used for structural bonding?
UV-cure anaerobic adhesives are generally not recommended for structural bonding applications. Anaerobic adhesives, in general, are designed to cure in the absence of air (oxygen) and are commonly used for bonding rigid metal components such as shafts, gears, and bearings. They fill gaps between mating surfaces and cure when confined in the absence of air.
On the other hand, UV-cure adhesives cure when exposed to ultraviolet (UV) light. These adhesives are often used for bonding transparent or translucent materials, and they heal relatively quickly when exposed to the appropriate UV wavelength. However, their strength and durability may only be suitable for high-stress structural applications.
For structural bonding, especially in applications with a significant load or stress on the bonded joint, it’s generally recommended to use adhesives specifically designed for structural bonding. These adhesives are formulated to provide high strength, excellent adhesion, and durability under various conditions. Due to their stability and versatility, epoxy adhesives are a common choice for structural bonding.
Always refer to the manufacturer’s guidelines and product specifications to ensure the chosen adhesive suits your application. Consult adhesive experts or the manufacturer to select the most appropriate product if you have specific structural requirements.
How does temperature affect the curing process?
Curing refers to transforming a material into a more stable and durable state through chemical reactions. The effect of temperature on the curing process depends on the specific material or substance undergoing curing. Here are some general observations:
Rate of Reaction:
- In many curing processes, an increase in temperature often accelerates the rate of chemical reactions. This is described by the Arrhenius equation, which states that the reaction rate approximately doubles for every 10-degree Celsius increase in temperature. Higher temperatures provide more energy for molecules to react, leading to faster curing.
Activation Energy:
- Curing reactions often have an activation energy barrier that must be overcome for the reaction to occur. Higher temperatures supply the necessary energy to surpass this barrier, facilitating curing.
Viscosity Changes:
- Temperature can influence the viscosity of materials. In some curing processes, as temperature increases, the viscosity of the material may decrease. This can enhance the mobility of molecules and improve their ability to react, promoting the curing process.
Polymerization and Crosslinking:
- Higher temperatures can lead to increased polymerization or crosslinking for curing processes involving polymers, such as in the curing of resins or the vulcanization of rubber. This results in forming a stronger and more stable network within the material.
Controlled Curing:
- In certain applications, controlled curing at specific temperatures may be necessary to achieve desired material properties. This might involve carefully controlling the temperature during different stages of the curing process to achieve the desired balance of strength, flexibility, or other characteristics.
Thermal Stability:
- Some materials may undergo undesired reactions or degradation if exposed to excessively high temperatures during curing. It’s essential to consider the material’s thermal stability and choose an appropriate curing temperature to avoid adverse effects.
Uniformity of Curing:
- Maintaining a uniform temperature throughout the curing process is crucial for consistent material properties. Temperature variations can lead to uneven curing, resulting in non-uniform material characteristics.
Energy Consumption:
- The temperature at which curing occurs can also impact the energy consumption of the process. Higher temperatures generally require more energy but may lead to faster curing times.
The relationship between temperature and the curing process is complex and depends on the specific material and chemistry involved. It’s essential to consider factors such as the reaction kinetics, activation energy, and material properties to optimize the curing conditions for a particular application.
Are there safety considerations when working with UV Cure Anaerobic Adhesive?
Yes, there are safety considerations when working with UV-cure anaerobic adhesives. While UV-cure anaerobic adhesives offer several advantages, such as fast curing times and the ability to bond without air (anaerobic conditions), following safety guidelines to ensure proper handling and minimize potential risks is essential. Here are some general safety considerations:
Eye and Skin Protection:
- UV cure adhesives can emit ultraviolet (UV) light during curing. It is crucial to wear appropriate eye protection, such as UV-blocking safety goggles, to prevent eye damage.
- Skin exposure should be minimized, and gloves are recommended to protect the skin from contact with the adhesive.
UV Exposure:
- Avoid direct exposure to UV light from the curing process. Prolonged exposure to UV radiation can be harmful to the eyes and skin.
- Use UV shields or barriers to protect against unintentional exposure.
Ventilation:
- Work in a well-ventilated area to properly disperse any fumes or vapors released during the curing process.
Material Compatibility:
- Ensure that the adhesive is compatible with the materials being bonded. Some materials may be sensitive to certain chemicals in the adhesive.
Read and Follow MSDS (Material Safety Data Sheet):
- Familiarize yourself with the Material Safety Data Sheet for your specific UV cure anaerobic adhesive. The MSDS provides essential information on potential hazards, safe handling procedures, and emergency measures.
Storage:
- Store the adhesive according to the manufacturer’s recommendations, including temperature and humidity. Improper storage can affect the performance of the adhesive and pose safety risks.
Emergency Response:
- Be aware of emergency procedures and the location of safety equipment, such as eye wash stations and emergency showers, in case of accidental exposure.
Training:
- Provide adequate training to personnel working with UV cure anaerobic adhesives. This includes instruction on proper handling, storage, and emergency response procedures.
Equipment Maintenance:
- Regularly inspect and maintain UV curing equipment to ensure it functions correctly and safely.
Always consult the product documentation and guidelines provided by the manufacturer of the specific UV cure anaerobic adhesive you use. Following these safety considerations helps reduce the risk of accidents and ensures a safe working environment.
What are the critical features of UV Cure Anaerobic Adhesive products?
UV cure anaerobic adhesives are specialized products that cure in the presence of ultraviolet (UV) light and the absence of air (anaerobic conditions). These adhesives are commonly used in bonding applications requiring a fast and reliable cure. When selecting UV cure anaerobic adhesive products, consider the following key features:
Curing Time:
- Quick curing is a significant advantage of UV-cure anaerobic adhesives. Check the curing time specifications, and choose a product that aligns with your application requirements.
UV Light Compatibility:
- Ensure the adhesive is compatible with the specific UV light source you intend to use. Different formulations may require different wavelengths of UV light for adequate curing.
Substrate Compatibility:
- Verify that the adhesive is suitable for bonding the materials involved in your application. Some UV-cure anaerobic adhesives may work better on specific substrates, so matching the adhesive with the materials you are bonding is essential.
Viscosity:
- Viscosity affects the adhesive’s flow and penetration into tight spaces. Choose a viscosity level that suits your application, whether a low-viscosity adhesive for better penetration or a higher viscosity for gap-filling properties.
Temperature Resistance:
- Consider the operating temperature range of the adhesive. Ensure that it can withstand the temperatures it will be exposed to during the application’s lifespan.
Cured Mechanical Properties:
- Evaluate the mechanical properties of the cured adhesive, such as tensile strength, shear strength, and flexibility. These properties are crucial for determining the adhesive’s performance in specific applications.
Chemical Resistance:
- Assess the adhesive’s resistance to chemicals and environmental factors. Depending on the application, you may need an adhesive that can withstand exposure to certain chemicals, moisture, or other environmental conditions.
Shelf Life:
- Check the product’s shelf life to ensure that it remains effective for the duration you require. Proper storage conditions may also impact the shelf life of UV-cure anaerobic adhesives.
Ease of Use:
- Consider the ease of application and the conditions that are necessary for curing. Some UV-cure anaerobic adhesives may require controlled environments or specific application techniques.
Safety and Regulatory Compliance:
- Ensure that the adhesive complies with relevant safety standards and regulations. Check for information on hazardous components and follow recommended safety precautions.
Product Documentation and Support:
- Look for comprehensive product documentation that provides data on application guidelines, curing conditions, and troubleshooting. Good customer support from the manufacturer can also be valuable.
Always refer to the manufacturer’s technical data sheet and guidelines for specific product details and recommendations. Additionally, conducting small-scale testing in your application may be beneficial before full-scale implementation.
Can UV Cure Anaerobic Adhesives be used for medical applications?
UV-curable anaerobic adhesives are generally not recommended for direct use in medical applications, especially those involving prolonged contact with the human body or internal bodily fluids. Anaerobic adhesives, in general, are designed for bonding and sealing applications in industrial settings, such as manufacturing and assembly processes.
Medical-grade adhesives used in healthcare applications must meet specific biocompatibility and safety standards. They must be designed to be non-toxic, non-irritating, and compatible with the human body. Additionally, they should be resistant to bodily fluid sterilization processes and have appropriate mechanical properties for medical use.
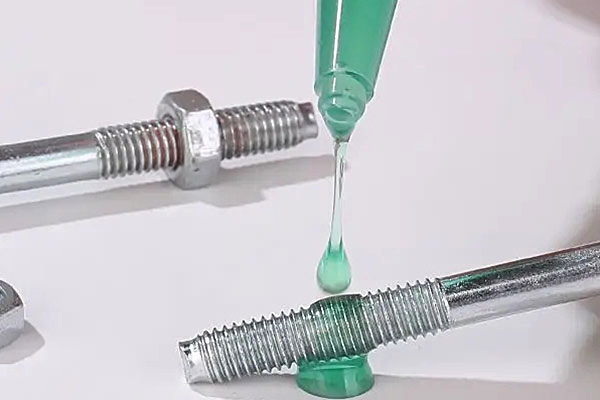
UV-curable adhesives may not fulfill the stringent requirements for medical adhesives while offering fast curing times and excellent bond strength. Medical-grade adhesives are often tested and certified for biocompatibility according to standards such as ISO 10993.
Suppose you are considering an adhesive for a medical application. In that case, it is crucial to consult with experts in medical device manufacturing, and it’s advisable to use adhesives specifically formulated and tested for medical purposes. Always follow regulatory guidelines and standards to ensure the safety and efficacy of the medical devices or components you are working on.
Are there variations in viscosity for different applications?
Yes, viscosity can vary significantly depending on the application and the specific requirements of the process or product involved. Viscosity is a measure of a fluid’s resistance to flow, and it is influenced by factors such as temperature, pressure, and the composition of the fluid.
Here are some examples of how viscosity variations are essential in different applications:
Industrial Processes:
- Fluids with specific viscosities may be required for optimal performance in manufacturing and industrial processes. For example, controlling viscosity is crucial in producing paints, coatings, and adhesives to ensure proper application and coating thickness.
Food and Beverage Industry:
- In the food and beverage industry, viscosity is a critical parameter in determining the texture and mouthfeel of products. Different foods like sauces, dressings, and beverages may require specific viscosity levels to meet consumer expectations.
Oil and Gas Industry:
- In the oil and gas industry, the viscosity of crude oil and other fluids is critical in the extraction, transportation, and refining processes. Viscosity affects the ease with which fluids can be pumped and transported through pipelines.
Biomedical Applications:
- In medical and biological applications, such as pharmaceuticals and biotechnology, controlling the viscosity of solutions is essential for ensuring proper dosing, injection, and flow characteristics.
Automotive and Lubricants:
- Motor oils, lubricants, and hydraulic fluids need specific viscosity ranges to ensure proper lubrication and functionality of engines and other mechanical components.
Polymer Processing:
- In polymer processing, such as extrusion or injection molding, controlling the viscosity of polymer melts is crucial for achieving the desired product properties and ensuring efficient processing.
Paint and Coatings:
- Viscosity is a critical parameter in the formulation of paints and coatings. It influences factors like ease of application, coverage, and the final appearance of the coated surface.
Cosmetics and Personal Care:
- In the formulation of cosmetic and personal care products, such as lotions, creams, and shampoos, viscosity plays a role in product stability, texture, and application properties.
In each of these cases, the specific viscosity requirements depend on the intended purpose and the desired characteristics of the final product or process. Therefore, understanding and controlling viscosity is essential for various industrial and scientific applications.
Do UV Cure Anaerobic Adhesives require special dispensing equipment?
UV cure anaerobic adhesives are typically designed to cure in the presence of ultraviolet (UV) light and the absence of air (anaerobic conditions). While they share the anaerobic curing characteristic with traditional anaerobic adhesives, the UV cure aspect distinguishes them.
Dispensing equipment for UV cure anaerobic adhesives is specialized but not drastically different from dispensing equipment used for standard anaerobic adhesives. Here are some considerations:
UV Light Source:
- UV cure anaerobic adhesives require a UV light source for curing. The dispensing equipment should be designed to work with the specific wavelength of UV light recommended for the adhesive.
Dispensing Systems:
- Dispensing equipment can include syringe dispensers, metered dispensing systems, or automated dispensing robots. These systems need to be compatible with the viscosity of the adhesive being dispensed.
UV Intensity Control:
- Some dispensing equipment may come with UV intensity control features to ensure the adhesive cures effectively. This is particularly important for achieving consistent and reliable results.
Material Compatibility:
- Check if the dispensing equipment is compatible with the materials used in the adhesive. Some UV-cure anaerobic adhesives may have particular requirements to consider when selecting dispensing equipment.
Curing Time and Speed:
- UV cure anaerobic adhesives generally cure quickly under UV light. The dispensing equipment should be able to deliver the adhesive efficiently, considering the required curing time.
Automation and Precision:
- Depending on the application, you may need dispensing equipment with automation and precision. Automated dispensing systems, including robotic arms, can ensure accurate and repeatable dispensing.
Dispensing Tips and Needles:
- The choice of dispensing tips or needles can affect the accuracy and precision of adhesive application. Ensure that the dispensing tips are suitable for the adhesive and application method.
Before purchasing dispensing equipment for UV cure anaerobic adhesives, it’s advisable to consult with the adhesive manufacturer or supplier. They can provide specific recommendations based on the characteristics of the adhesive and the intended application. Additionally, testing the compatibility of the adhesive with the dispensing equipment in a controlled setting is a good practice to ensure optimal performance.
What are the storage conditions for UV Cure Anaerobic Adhesive?
UV cure anaerobic adhesives are typically designed to cure when exposed to ultraviolet (UV) light and in the absence of air (anaerobic conditions). Proper storage conditions are crucial to maintaining the effectiveness of these adhesives. Here are some general guidelines for storing UV cure anaerobic adhesives:
- Temperature: Store the adhesive in a cool, dry place. Avoid exposure to extreme temperatures. Adhesives can often have recommended temperature ranges for storage, so adhering to those guidelines is essential.
- Light Exposure: UV cure adhesives are sensitive to UV light, and prolonged exposure can lead to premature curing. Therefore, storing these adhesives in opaque or amber-colored containers is crucial to protect them from ambient light.
- Air Exposure: Anaerobic adhesives cure in the absence of air. Ensure that the containers are tightly sealed when not in use to prevent air from entering and initiating the curing process prematurely.
- Moisture: Moisture can also affect the curing process of anaerobic adhesives. Store the adhesives in a moisture-free environment and seal the containers tightly to prevent moisture ingress.
- Shelf Life: Adhesives have a limited shelf life, and it’s essential to check the expiration date provided by the manufacturer. Using adhesives beyond their shelf life may reduce performance or incomplete curing.
- Orientation: Store the adhesive containers in the recommended orientation, as specified by the manufacturer. Some adhesives may need to be stored upright or inverted to prevent settling or separation of components.
Always refer to the manufacturer’s guidelines and product data sheets for specific storage recommendations for the UV cure anaerobic adhesive you use, as different formulations may have varying requirements. Following these guidelines helps ensure the adhesive remains in optimal condition and performs as intended.
Can these adhesives be used for bonding dissimilar materials?
You forgot to provide the specific names or types of adhesives you are referring to. Adhesives vary in composition and properties; some are formulated to work well with dissimilar materials. In general, adhesives are designed for bonding a wide range of materials, including metals, plastics, rubber, glass, and more.
Standard adhesives used for bonding dissimilar materials include:
- Epoxy Resin:Epoxy adhesives are versatile and can bond various materials, including metal, plastic, glass, and ceramics.
- Cyanoacrylate (Super Glue):Cyanoacrylate adhesives bond quickly and effectively with multiple materials, including plastics, metals, and rubber.
- Polyurethane Adhesives:Polyurethane adhesives are flexible and suitable for bonding dissimilar materials, such as wood to metal or plastic to metal.
- Acrylic Adhesives:Acrylic adhesives can bond materials like metals, plastics, and composites.
- Anaerobic Adhesives:These adhesives are designed for metal-to-metal bonding and work well in environments without oxygen. They are commonly used for thread-locking and retaining applications.
When selecting an adhesive for dissimilar materials, it’s essential to consider the specific materials involved, the intended application, and the environmental conditions the bond will be exposed to. Additionally, surface preparation and compatibility testing are crucial to ensure optimal adhesion. Always follow the manufacturer’s guidelines and recommendations for the selected adhesive.
What are the recommended surface preparations before applying UV Cure Anaerobic Adhesive?
Surface preparation is crucial for the successful application of UV-cure anaerobic adhesives. Here are some general recommendations for surface preparation:
- Cleanliness:Ensure that the surfaces to be bonded are clean and free of any contaminants such as dust, dirt, grease, oil, or moisture. Cleaning can be done using solvents like acetone or isopropyl alcohol. It is essential to use lint-free wipes to avoid leaving behind fibers.
- Mechanical Cleaning:Besides solvent cleaning, consider using automated means such as abrasion or sanding to remove any surface oxides, rust, or other contaminants. This promotes better adhesion by providing a rougher surface for the adhesive to grip.
- Surface Activation:Some materials may benefit from surface activation techniques like plasma treatment or corona treatment. These processes increase the substrate’s surface energy, improving the adhesive’s wetting and adhesion.
- Primers:In some cases, applying a primer specific to the bonded materials can enhance the adhesion of UV-cure anaerobic adhesives. The primer helps in promoting chemical bonding between the adhesive and the substrate.
- Compatibility Testing:Before full-scale application, it’s advisable to conduct compatibility testing to ensure that the adhesive works well with the specific materials involved. This is particularly important when dealing with substrates that may be chemically resistant or have low surface energy.
- Masking:Use masking materials or tapes to protect areas where the adhesive is not intended to bond. This prevents unintended bonding and ensures a neat application.
- UV Transparency:Ensure that the related materials allow UV light to penetrate to cure the adhesive. If the materials are opaque to UV light, consider using a transparent or translucent adhesive or adjusting the cure time and intensity accordingly.
- UV Cure Equipment Calibration:If using UV curing equipment, make sure it is properly calibrated to provide the correct intensity and duration of UV light for curing. Follow the manufacturer’s guidelines for the UV curing equipment.
Always refer to the specific manufacturer’s recommendations and guidelines for the UV-cure anaerobic adhesive being used, as different products may have variations in their requirements and specifications.
Are there limitations to the gap-filling capabilities of these adhesives?
Yes, there are limitations to the gap-filling capabilities of adhesives, which can vary depending on the type of adhesive used and the specific application. Here are some common limitations:
*Viscosity and Flow Properties:Some adhesives may have high viscosity or low flow properties, making it difficult for them to fill significant gaps or irregular surfaces effectively. In such cases, choosing an adhesive with the proper viscosity for the application is crucial.
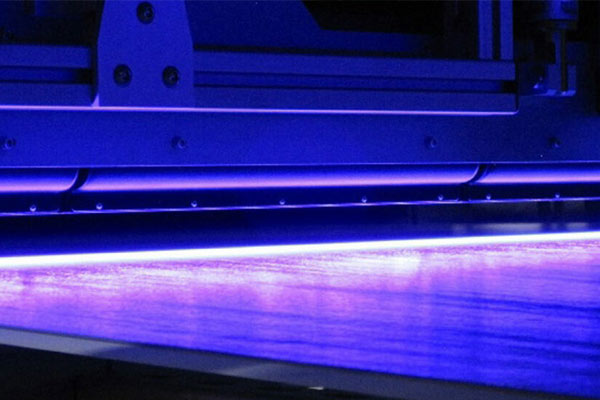
*Surface Preparation:Adhesives often require adequate surface preparation for optimal bonding. The adhesive may not effectively fill gaps or bond well if surfaces are contaminated, dirty, or uneven. Good surface preparation, such as cleaning and roughening, is essential for successful gap-filling.
*Material Compatibility:Adhesives are designed for specific materials or material groups. Some adhesives may not adhere well to particular substrates, and the bonding strength may be compromised. It’s essential to consider the compatibility of the adhesive with the materials being bonded.
*Curing Time and Conditions:The curing time and conditions of the adhesive can impact its gap-filling capabilities. Some adhesives may shrink during curing, affecting their ability to fill gaps. Additionally, temperature and humidity conditions during curing can influence the final bond strength.
*Bond Thickness:Adhesives are often designed for specific bond thicknesses. If the gap is too large, it may be easier for the adhesive to maintain proper contact between the surfaces, reducing bonding strength.
*Temperature and Environmental Factors:Some adhesives have limitations, and exposure to extreme temperatures may affect their performance. Environmental factors such as exposure to moisture, chemicals, or UV light can also impact the gap-filling capabilities of certain adhesives.
*Mechanical Stress:Adhesives may not perform well under extreme mechanical stress or dynamic loading conditions. If the bonded materials experience significant movement or stress, the adhesive may not be able to maintain a solid and durable bond.
*Cost and Availability:Specialty adhesives designed for specific gap-filling applications may be more expensive or challenging. In some cases, balancing performance requirements with cost constraints can be a limitation.
It’s essential to carefully read and follow the manufacturer’s guidelines for the specific adhesive used, considering the intended application, substrate materials, and environmental conditions to achieve the best results.
How does UV intensity affect the curing process?
UV (ultraviolet) curing is commonly used in various industries, such as printing, coatings, adhesives, and electronics, to cure or harden materials using ultraviolet light. The UV intensity plays a crucial role in the effectiveness of the curing process. Here’s how UV intensity affects the curing process:
Initiation of Photopolymerization:
- UV curing typically involves photopolymerization, where UV light initiates a chemical reaction in the presence of photoinitiators. Photoinitiators absorb UV light and then generate reactive species, such as free radicals or cations, which start the polymerization of the material.
- Higher UV intensity results in more photons reaching the photoinitiators, leading to a faster and more efficient initiation of the polymerization process.
Curing Speed:
- UV intensity is directly proportional to the curing speed. A higher UV intensity allows for quicker polymerization, leading to faster curing times. This is particularly important in industrial processes where rapid production is desirable.
Depth of Cure:
- UV intensity affects the depth to which the material can be cured. Higher UV intensity generally enables deeper curing, as the UV light can penetrate the material more effectively. This is important for ensuring that the entire thickness of a coating or adhesive is properly cured.
Uniformity of Cure:
- Uneven UV intensity can result in uneven curing. It’s essential to ensure that the UV light is evenly distributed across the material surface to achieve uniform curing. Inconsistent curing can lead to defects and reduced performance of the cured material.
Energy Consumption:
- Higher UV intensity often requires more energy. While high intensity is beneficial for faster curing, balancing intensity with energy consumption and cost considerations is crucial.
Control of the Curing Process:
- UV intensity needs to be carefully controlled to optimize the curing process. This control is often achieved using equipment such as UV lamps or LED systems, and the parameters may be adjusted based on the specific requirements of the material being cured.
Material Sensitivity:
- Different materials have varying sensitivity to UV light. Some materials may require higher UV intensity for efficient curing, while others may be more sensitive and cure effectively at lower intensities.
UV intensity is a critical parameter in the UV curing process. Proper control and optimization of UV intensity ensure efficient and uniform curing, impacting factors such as curing speed, depth of cure, and overall product quality.
Are there post-cure considerations for UV-cure anaerobic adhesive bonds?
UV-cure anaerobic adhesives are used for bonding applications where anaerobic conditions (absence of air or oxygen) are essential for curing. These adhesives cure in the presence of ultraviolet (UV) light and the lack of oxygen. After the initial curing process, there are several post-cure considerations to ensure the bond achieves its maximum strength and durability:
- Full Cure Time:Ensure that the adhesive has undergone the total curing time recommended by the manufacturer. This time may vary depending on adhesive formulation, bond thickness, and the specific UV light source.
- Intensity and Wavelength of UV Light:Confirm that the UV light source used for curing provides the recommended intensity and wavelength specified by the adhesive manufacturer. Inadequate UV exposure can lead to incomplete curing, affecting the bond strength.
- Temperature:Adhesive curing can be temperature-sensitive. Check if there are specific temperature requirements during or after the curing process. Some adhesives may benefit from additional heat to enhance cure and post-cure strength.
- Light Shielding:Once the initial curing is complete, protecting the bonded assembly from further exposure to UV light is crucial. Prolonged exposure to UV light can degrade the adhesive and compromise bond performance over time.
- Surface Residue:Remove any surface residue or unreacted adhesive that may be present after curing. This can be done using appropriate cleaning agents recommended by the adhesive manufacturer. Residual uncured material can affect the bond’s integrity.
- Testing and Quality Control:Perform quality control tests to ensure the adhesive bond meets the required specifications. This may involve various mechanical tests, such as shear or tensile strength, to verify the bond’s performance.
- Environmental Conditions:Consider the environmental conditions to which the bonded assembly will be exposed. Some adhesives may require additional steps or considerations for optimal performance in specific environments, such as exposure to heat, chemicals, or moisture.
- Post-Cure Validation:Some applications may benefit from a post-cure validation process. This involves subjecting the bonded assembly to specific conditions (temperature, humidity, etc.) to ensure the bond maintains its strength and integrity over time.
Always refer to the specific guidelines and recommendations provided by the adhesive manufacturer for post-cure considerations. These guidelines will help ensure that the bonded assembly meets the required performance standards and durability expectations.
What are the alternatives to UV Cure Anaerobic Adhesive in specific applications?
Alternatives to UV-cure anaerobic adhesives can be considered based on the application’s specific requirements. Here are some alternative adhesive types that may be suitable for specific applications:
- Cyanoacrylate Adhesives (CA or Super Glue):Cyanoacrylate adhesives are fast-curing, single-component adhesives that bond quickly to various substrates, including plastics, rubber, and metals. They cure through a reaction with surface moisture.
- Epoxy Adhesives:Epoxy adhesives are versatile and offer high bond strength. They are suitable for bonding various materials, including metals, ceramics, glass, and plastics. Epoxies are available in different formulations, such as one-part or two-part systems, and can be cured at room temperature or with heat application.
- Polyurethane Adhesives:Polyurethane adhesives provide flexibility and excellent resistance to impact and vibration. They are suitable for bonding dissimilar materials, such as metal to plastic or wood. Polyurethane adhesives can also provide good chemical resistance.
- Acrylic Adhesives:Acrylic adhesives offer fast cure times and high bond strength. They are suitable for bonding various materials, including metals, plastics, and composites. Acrylic adhesives can be formulated for specific requirements such as flexibility or high-temperature resistance.
- Anaerobic Adhesives (Non-UV):Traditional anaerobic adhesives cure without air and are activated by metal ions. They are commonly used for thread locking, sealing, and retaining applications. While they do not rely on UV light for curing, they still require oxygen to be excluded during the curing process.
- Silicone Adhesives:Silicone adhesives offer flexibility, resistance to high temperatures, and good electrical insulation properties. They are suitable for bonding materials like glass, ceramics, and certain plastics. Silicone adhesives are often used in applications requiring a flexible bond.
- Hot Melt Adhesives:Hot melt adhesives are solid at room temperature and melt when heated, providing a quick bond upon cooling. They are commonly used in packaging, woodworking, and automotive assembly industries.
- Pressure-Sensitive Adhesives (PSA):PSA adheres to surfaces upon applying slight pressure. They are often used in applications such as tapes, labels, and graphic films. PSA offers convenience in application but may provide a different structural strength than other adhesives.
The choice of adhesive depends on factors such as substrate materials, required bond strength, environmental conditions, cure time, and the specific demands of the application. It’s essential to consider these factors and conduct testing to ensure that the selected adhesive.
It is suitable for the intended purpose. Additionally, always follow the manufacturer’s recommendations and guidelines for the chosen adhesive to achieve optimal performance and durability.
Conclusion:
In conclusion, UV Cure Anaerobic Adhesive stands as a cutting-edge solution, offering rapid curing, strong bonds, and versatility across various applications. Whether in manufacturing, construction, or medical industries, the advantages of UV Cure Anaerobic Adhesive make it a go-to choice for professionals seeking efficient and reliable bonding solutions in anaerobic environments. Stay informed as we delve deeper into each of these aspects, providing you with a comprehensive understanding of UV Cure Anaerobic Adhesive.
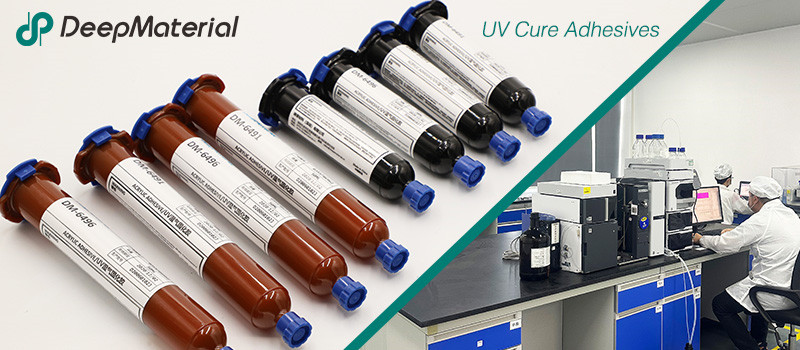
DeepMaterial
Based on the core technology of adhesives, DeepMaterial has developed adhesives for chip packaging and testing, circuit board level adhesives, and adhesives for electronic products. Based on adhesives, it has developed protective films, semiconductor fillers, and packaging materials for semiconductor wafer processing and chip packaging and testing. More…
UV Curing Adhesives
UV light cure have a number of benefits making them a popular choice among many product assembly and manufacturing applications. Many UV light cure adhesives can provide a nearly instantaneous bond to difficult substrates like glass and plastic. UV cure adhesives often require an accelerator or UV light for a bond to form.
Adhesive Blogs & News
The latest adhesive industry science and technology, Deepmaterial news, and market trends and forecasts.
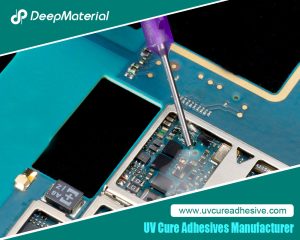
Biocompatibility of LED UV Glue Adhesive and Its Application Potential in Medical and Food Packaging Fields
Biocompatibility of LED UV Glue Adhesive and Its Application Potential in Medical and Food Packaging Fields LED UV glue adhesive has been widely applied in numerous fields due to its advantages such as rapid curing and easy operation. However, in fields with stringent safety requirements like medical and food packaging, its biocompatibility after curing becomes
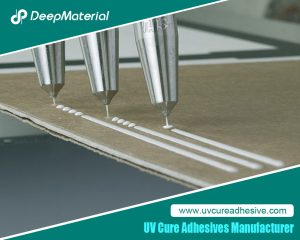
Biocompatibility of LED UV Glue Adhesive and Its Application Potential in Medical and Food Packaging Fields
Biocompatibility of LED UV Glue Adhesive and Its Application Potential in Medical and Food Packaging Fields LED UV glue adhesive has been widely applied in numerous fields due to its advantages such as rapid curing and easy operation. However, in fields with stringent safety requirements like medical and food packaging, its biocompatibility after curing
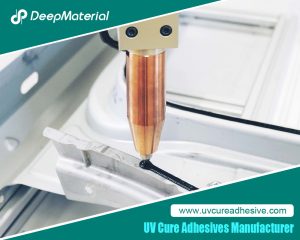
Exploring the Environmental Performance of UV Glue and Strategies for Optimizing Odor and VOC Content
Exploring the Environmental Performance of UV Glue and Strategies for Optimizing Odor and VOC Content UV glue, as an adhesive that achieves rapid curing through ultraviolet (UV) light irradiation, has been widely applied in numerous fields such as electronics, optics, healthcare, and automobiles, thanks to its advantages of fast curing speed, high bonding strength, and
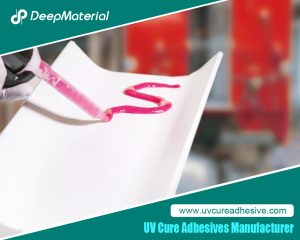
Compatibility Analysis and Countermeasures of LED UV Glue with Automated Production Equipment
Compatibility Analysis and Countermeasures of LED UV Glue with Automated Production Equipment LED UV glue has been widely used in modern manufacturing due to its advantages such as fast curing speed, high bonding strength, and environmental friendliness. However, in the automated production process, if there are problems with the adaptability between the glue and equipment
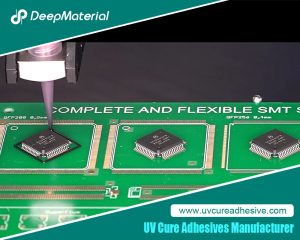
Influence of Viscosity and Thixotropy of Glue on the Quality of Glue Dots in the Dispensing Process and Solutions
Influence of Viscosity and Thixotropy of Glue on the Quality of Glue Dots in the Dispensing Process and Solutions The dispensing process is an important part of the application of LED UV glue adhesive, and the quality of this process directly affects the final performance of the product. The physical properties of the glue,
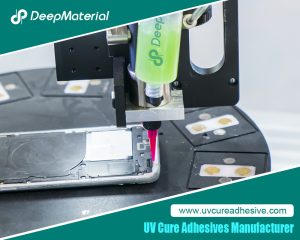
Aging Mechanism and Modification Strategies of LED UV Glue under Long-term Ultraviolet Irradiation
Aging Mechanism and Modification Strategies of LED UV Glue under Long-term Ultraviolet Irradiation LED UV glue, with its advantages of fast curing speed, high bonding strength, and environmental friendliness, has been widely used in fields such as optical device packaging, electronic assembly, and medical devices. However, in scenarios where it is exposed to ultraviolet environments