High Peel Strength Adhesive
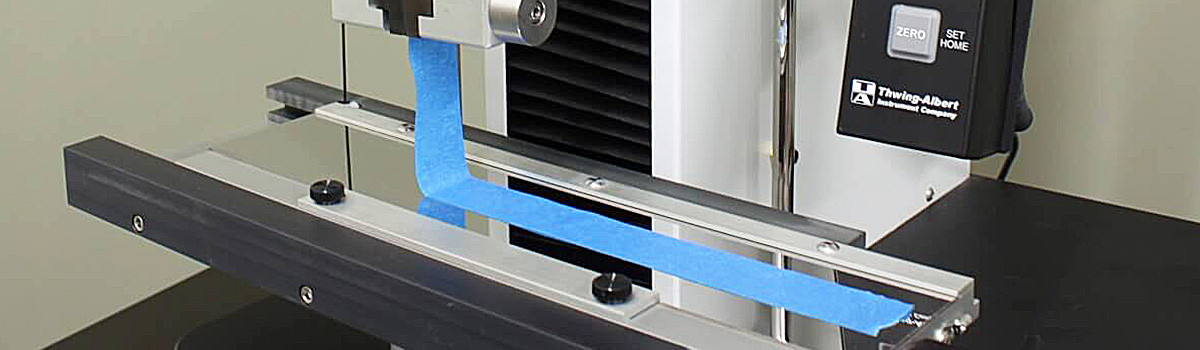
In the intricate world of modern bonding techniques, few elements hold as much significance as the remarkable prowess of High Peel Strength Adhesives. As the bedrock of industrial bonding, these adhesives wield an unparalleled ability to fuse diverse materials with a tenacity that defies conventional limits. Their emergence has revolutionized numerous sectors, becoming the cornerstone of innovation in automotive, aerospace, electronics, healthcare, and beyond. Understanding the quintessence of high peel strength in adhesives is to delve into the essence of durability, versatility, and reliability in contemporary applications. Let us explore these adhesive marvels, dissecting their characteristics, applications, limitations, and the promising vistas they unfurl for myriad industries. High Peel Strength Adhesives are the unsung heroes catalyzing transformation across sectors, propelling us into an era where bonding capabilities reach unprecedented heights.
Table of Contents
ToggleWhat characterizes high peel strength in adhesives?
In adhesives, the term “peel strength” holds significant importance. It defines the force required to peel apart two bonded materials. High peel strength adhesives stand out for their exceptional ability to withstand separation forces. Understanding the characteristics behind this strength unveils the secrets to their effectiveness.
Characteristics of High Peel Strength Adhesives
- Chemical Composition:High peel strength adhesives often comprise specialized chemical compounds tailored for intermolecular solid bonding. These compositions contribute significantly to their robust adhesive properties.
- Bonding Surface Preparation:These adhesives demand meticulous surface preparation. Ensuring the bonding surfaces are clean, dry, and free from contaminants enhances their adhesion, leading to superior peel strength.
- Flexibility and Elasticity:High peel strength adhesives possess a balance of flexibility and elasticity. This characteristic allows them to distribute stress evenly across the bonded surfaces, resisting peeling forces effectively.
- Adhesive Thickness:The thickness of the adhesive layer plays a vital role in determining its peel strength. High peel strength adhesives often maintain an optimal thickness range, ensuring maximum bonding efficiency.
- Temperature Resistance:Many high peel strength adhesives exhibit exceptional resistance to temperature fluctuations. They maintain their adhesive properties across a broad temperature range, enhancing their reliability in various environments.
- Chemical Resistance:Certain formulations are engineered to resist degradation when exposed to chemicals or harsh substances. This attribute makes them suitable for applications in challenging industrial environments.
- Substrate Compatibility:These adhesives demonstrate compatibility with a diverse range of substrates, including metals, plastics, composites, and more. This versatility expands their applicability across multiple industries.
- Long-Term Durability:High peel strength adhesives are designed for longevity. They retain their bonding capabilities over extended periods, ensuring durability and reliability in bonded assemblies.
The Applications of High Peel Strength Adhesives
- Automotive Industry:These adhesives are used extensively in automotive assembly bonding components where high peel strength is essential for structural integrity.
- Aerospace and Aviation:Critical aerospace applications rely on high peel strength adhesives for bonding lightweight materials without compromising strength.
- Electronics Manufacturing:These adhesives ensure durable and reliable connections from circuit board assembly to affixing components.
- Construction Sector:High peel strength adhesives are used for bonding building materials, providing solid and lasting connections.
How do high peel strength adhesives differ from other types of adhesives?
Adhesives are the unsung heroes behind countless applications, from everyday household repairs to critical industrial bonding. Among the plethora of adhesive types, high peel strength adhesives stand out for their distinctive characteristics, setting them apart from other variants in the market. Understanding these differences sheds light on the unique attributes of high peel strength adhesives.
Distinguishing Features of High Peel Strength Adhesives
- Peel Resistance:High peel strength variants resist separation forces, unlike other adhesives. They exhibit superior bonding capabilities, specifically tailored to withstand peeling stresses without compromising adhesion quality.
- Bonding Mechanism:While conventional adhesives rely on various mechanisms, such as chemical adhesion or cohesion, high peel strength adhesives prioritize a powerful interfacial bond. This focus on adhesion at the interface leads to increased peel strength.
- Specialized Formulations:High peel strength adhesives often boast specialized formulations containing additives or unique compounds. These formulations are engineered to enhance peel strength while maintaining other essential adhesive properties.
- Surface Preparation Requirements:Unlike some adhesives that may tolerate minor surface imperfections, high peel strength adhesives demand meticulous surface preparation. They require clean, dry, and well-prepared bonding surfaces for optimal performance.
- Flexibility and Durability:One of the key distinctions lies in the balance between flexibility and durability. High peel strength adhesives maintain this equilibrium, ensuring resilience against peeling forces while accommodating movement or stress in bonded materials.
- Application Variability:While some adhesives are limited in their applications, high peel strength adhesives offer versatility. They cater to various industries and bonding needs, from automotive and aerospace to electronics and construction.
- Performance in Challenging Environments:High peel strength adhesives perform remarkably in challenging conditions. They withstand temperature fluctuations, chemical exposures, and harsh environments better than conventional adhesives.
- Long-Term Reliability:Unlike certain adhesives that might weaken or degrade over time, high peel strength adhesives maintain their strength and adhesion properties over extended periods. This longevity ensures durability in bonded assemblies.
Understanding these fundamental differences highlights the niche position of high peel strength adhesives in the adhesive market. Their unique blend of attributes, particularly emphasizing exceptional peel resistance and robust bonding, makes them a preferred choice for applications where reliability and durability are paramount.
What factors contribute to achieving high peel strength?
High peel strength adhesive, a crucial component in numerous industries, exhibits a formidable ability to maintain adhesion under stress. Achieving this level of reliability isn’t a stroke of luck; it’s a result of meticulous formulation and consideration of several contributing factors. Let’s delve into the key elements that empower adhesives to reach exceptional peel strength:
Material Selection
- Adhesive Composition:The fundamental basis of high peel strength lies in the adhesive’s composition. Certain materials like acrylics, epoxies, and polyurethanes are known for their superior peel strength.
- Substrate Compatibility:The adhesive’s ability to bond with diverse substrates significantly influences its peel strength. Compatibility testing ensures the adhesive works optimally across different materials.
Adhesive Application and Preparation
- Surface Preparation:Adequate surface preparation, including cleaning and roughening, enhances the substrate’s receptiveness to the adhesive, fostering better adhesion.
- Application Technique: The method of applying the adhesive, whether by spraying, rolling, or brushing, impacts its penetration and coverage, influencing peel strength.
Environmental Factors
- Temperature and Humidity:Environmental conditions during application and curing profoundly affect peel strength. Optimal temperature and humidity levels facilitate proper curing and adhesion.
- Chemical Exposure:Exposure to chemicals or environmental factors post-application can impact the adhesive’s long-term strength. Resilience to such exposures is crucial for maintaining peel strength.
Curing Process
- Time and Temperature:The curing process is pivotal. Ensuring the adhesive cures at the right temperature for the specified duration is critical for achieving high peel strength.
- Pressure Application:Applying pressure during curing helps create better contact between the adhesive and the substrate, optimizing peel strength.
Formulation Enhancements
- Additives and Fillers:Incorporating additives or fillers can enhance the adhesive’s properties, improving its ability to resist peel forces.
- Crosslinking Agents: Introducing crosslinking agents strengthens the molecular structure of the adhesive, boosting its peel strength.
Testing and Quality Control
- Adhesion Testing:Rigorous testing methods, including peel testing, ascertain the adhesive’s peel strength under various conditions, ensuring consistency and reliability.
- Quality Assurance:Continuous monitoring and refinement of the manufacturing process ensure adherence to standards and consistency in adhesive performance.
Design Considerations
- Joint Design:The design of the joint where the adhesive is applied impacts the stress distribution and, consequently, the peel strength.
- Thickness and Coverage:Ensuring adequate adhesive thickness and coverage in the joint area is crucial for optimal peel strength.
What are the primary categories or types of high peel strength adhesives available?
In adhesives, one critical characteristic often sought after is high peel strength. High peel strength adhesives play a crucial role in various industries, offering robust bonding solutions that withstand the test of time and stress. Let’s delve into the primary categories or types of high peel strength adhesives available in the market.
Categories of High Peel Strength Adhesives
Acrylic Adhesives
- They are known for their versatility and weather resistance.
- They are ideal for outdoor applications because they withstand harsh environmental conditions.
- Exhibit excellent peel strength on various substrates, including metals, plastics, and composites.
Rubber-Based Adhesives
- They offer exceptional flexibility and elasticity, making them suitable for bonding materials with different expansion rates.
- They are commonly used in applications requiring vibration damping or where substrates have varying coefficients of thermal expansion.
Modified Epoxy Adhesives
- Enhanced with additives to improve flexibility and peel strength.
- Provide strong adhesion to metals, ceramics, and some plastics.
- It is ideal for applications where high temperature and chemical resistance are essential.
Polyurethane Adhesives
- Offer high peel strength combined with good impact resistance.
- Suitable for bonding dissimilar materials and where dynamic stresses are expected.
Silicone Adhesives
- They are known for their excellent thermal stability and resistance to extreme temperatures.
- Provide high peel strength along with good resistance to moisture and chemicals.
- They are often used in automotive, aerospace, and electronic applications.
Application Areas
Automotive Industry
- High peel strength adhesives are vital in automotive assembly for bonding panels, trim, and structural components, ensuring durability and crash resistance.
Construction Sector
- They are used in the structural bonding of panels, laminates, and insulation materials, contributing to the strength and longevity of buildings.
Electronics and Aerospace
- Critical for bonding components in electronic devices and aircraft assembly, providing resistance to vibration and thermal cycling.
Factors Influencing Selection
Substrate Compatibility
- Different adhesives exhibit varying compatibility with substrates, necessitating careful consideration during selection.
Environmental Conditions
- The operating environment, including temperature, humidity, and exposure to chemicals, determines the suitability of the adhesive.
Application Technique
- Application method and curing process impact the overall performance and bond strength.
How are high peel strength adhesives utilized in the automotive sector?
In the fast-paced realm of automotive engineering, the quest for reliable, lightweight, and durable solutions is perpetual. Enter high peel strength adhesives, a crucial innovation revolutionizing the industry’s approach to bonding components. These adhesives offer a potent combination of resilience, flexibility, and bonding power, becoming a game-changer in automotive manufacturing. Here’s how they are utilized in the automotive sector:
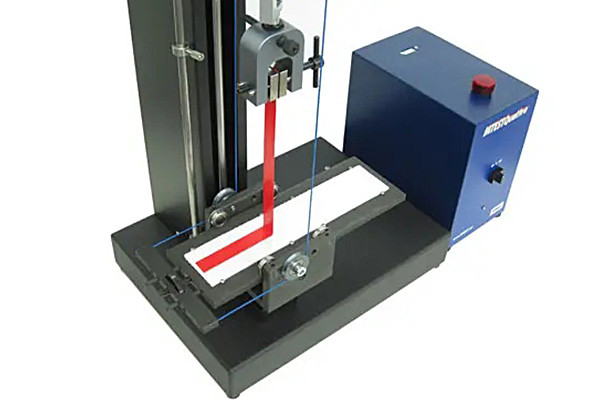
Optimized Structural Integrity
- High peel strength adhesives are pivotal in reinforcing structural integrity within vehicles.
- They offer superior bonding capabilities, allowing for assembling different materials like metals, composites, and plastics.
- By distributing stress and load across bonded joints, these adhesives enhance overall structural performance, contributing to the vehicle’s safety and longevity.
Weight Reduction and Fuel Efficiency
- One of the primary concerns in automotive design is reducing weight to enhance fuel efficiency.
- High peel strength adhesives enable the bonding of lightweight materials without compromising strength, leading to lighter vehicles.
- This weight reduction positively impacts fuel efficiency and decreases emissions, aligning with the industry’s sustainability goals.
Enhanced Manufacturing Efficiency
- These adhesives streamline manufacturing by offering faster curing times and simplified application methods.
- Their ability to bond dissimilar materials eliminates the need for traditional joining techniques like welding or mechanical fasteners, saving time and labor costs.
- Manufacturers benefit from increased production efficiency and cost-effectiveness without sacrificing quality.
Noise and Vibration Dampening
- High peel strength adhesives act as effective noise and vibration dampeners.
- Creating a strong bond between components reduces the chances of rattling or vibrations within the vehicle, leading to a quieter and smoother ride experience.
Resistance to Harsh Environments
- Automotive applications demand materials that can withstand extreme conditions, including temperature variations and exposure to chemicals or moisture.
- High peel strength adhesives exhibit excellent resistance to these harsh environments, ensuring long-term durability and reliability of bonded components.
Future Trends and Innovations
- Ongoing research focuses on enhancing the properties of these adhesives further, such as increasing heat resistance or developing bio-based alternatives for sustainability.
- Innovations in adhesive technology aim to cater to evolving automotive designs, including electric and autonomous vehicles, by adapting adhesives to new materials and manufacturing methods.
What role do they play in aerospace and aviation applications?
High peel strength adhesives, an integral component in aerospace and aviation, ensure safety, structural integrity, and performance across various applications. These specialized adhesives possess unique characteristics that make them indispensable in the industry.
Functions of High Peel Strength Adhesives
- Structural Bonding:High peel strength adhesives form robust bonds between different materials used in aircraft construction, such as composites, metals, and alloys. This bonding capability reinforces structural components, reducing the risk of failure and enhancing overall safety.
- Weight Reduction:The lightweight nature of these adhesives contributes significantly to the overall weight reduction of aircraft. By implementing this, you can achieve better fuel efficiency and reduce operating costs, all while ensuring the structural integrity of your system remains intact.
- Vibration Dampening:They effectively dampen vibrations, which is crucial in an aviation context where excessive vibration can compromise the structural integrity of an aircraft over time.
- Resistance to Extreme Conditions:High peel strength adhesives are formulated to endure extreme variations in temperature, pressure, and exposure to chemicals and fuels commonly found in the aerospace industry.
Applications in Aerospace and Aviation
- Composite Panel Bonding:These adhesives play a vital role in bonding composite panels used in aircraft construction, ensuring seamless integration and structural stability.
- Wing and Fuselage Assembly:They are crucial in assembling wings, fuselages, and other structural components, providing strength while reducing reliance on traditional fasteners, thereby minimizing stress points.
- Interior and Exterior Component Bonding:From interior cabin components to exterior panels and surfaces, these adhesives facilitate the bonding of various parts, contributing to the overall durability and aesthetics of the aircraft.
- Repair and Maintenance:High peel strength adhesives are also used in repair and maintenance activities, enabling quick and reliable fixes for minor damages without compromising the aircraft’s structural integrity.
The Future of High Peel Strength Adhesives in Aerospace
Continuous advancements in adhesive technology are expected to bring forth even more robust, lighter, and adaptable formulations. Research focuses on developing adhesives with improved bonding capabilities, enhanced resistance to extreme conditions, and reduced environmental impact.
Are there notable applications in electronics and technology?
In electronics and technology, the adhesive that holds compounds together plays an integral yet often overlooked role. Among the array of adhesives, one stands out for its exceptional performance, the High Peel Strength Adhesive. This adhesive type has garnered attention for its robust bonding capabilities and has found notable applications across various sectors, particularly in electronics and technology.
Understanding High Peel Strength Adhesive
What is High Peel Strength Adhesive?
High Peel Strength Adhesive is an adhesive renowned for its ability to withstand forceful peeling or pulling apart. Its robust bonding properties make it ideal for applications requiring resilience against stress and strain.
Composition and Properties
High peel strength adhesives are typically composed of acrylic, rubber, or silicone-based compounds, which possess flexibility, durability, and strong adhesion to various substrates.
Applications in Electronics and Technology
Electronic Component Assembly
- Bonding Circuit Boards:High Peel Strength Adhesive secures delicate components like microchips, resistors, and capacitors onto circuit boards, ensuring stability during operation and protection against vibrations.
- Display Technology:In the manufacturing of LED displays, touchscreen panels, and OLED screens, this adhesive type plays a pivotal role in bonding layers together, ensuring durability and resilience to external forces.
Wearable Technology
- Smart Devices:High Peel Strength Adhesive is instrumental in assembling components of wearable devices like smartwatches, fitness trackers, and medical sensors. It ensures the structural integrity of these devices despite constant movement and usage.
Automotive Electronics
- Bonding Sensors and Control Units:In modern vehicles, this adhesive secures sensors, control units, and wiring harnesses, contributing to the reliability and longevity of electronic systems within automobiles.
Aerospace and Defense
- Avionics and Military Applications:High Peel Strength Adhesive is vital in aerospace and defense for bonding critical electronic systems, ensuring they withstand extreme conditions and vibrations.
Advantages and Future Prospects
- Enhanced Reliability:Its ability to resist peeling ensures a robust and reliable bond, crucial in applications where security and stability are paramount.
- Miniaturization:As technology advances, components become smaller and more intricate. High Peel Strength Adhesive aids in bonding these miniature components securely.
- Continued Innovation:Ongoing research focuses on developing more potent formulations and adapting this adhesive for emerging technologies like flexible electronics and nanotechnology.
How are these adhesives utilized in healthcare and medical device manufacturing?
In healthcare and medical device manufacturing, high peel strength adhesives have revolutionized various processes, ensuring reliability, safety, and efficiency. These adhesives, renowned for their robust bonding capabilities, are pivotal in advancing medical technologies, facilitating intricate procedures, and enhancing patient care.
Adhesive Applications in Healthcare
- Wound Care:High peel strength adhesives are crucial in producing advanced wound dressings and surgical tapes. These adhesives provide secure yet gentle attachment, ensuring the dressings remain in place without causing discomfort or skin irritation to patients.
- Medical Device Assembly:The assembly of medical devices demands adhesives that can withstand stringent conditions. These adhesives enable the bonding of diverse materials used in manufacturing devices like catheters, sensors, and monitors, ensuring durability and reliability in their functionality.
- Drug Delivery Systems:Adhesives create transdermal patches and drug delivery systems. They aid in the controlled release of medications through the skin, maintaining adherence and stability of the patch during usage.
Advantages of High Peel Strength Adhesives in Healthcare
- Reliable Bonding:These adhesives offer strong and consistent bonding between different substrates, ensuring the integrity of medical devices and equipment.
- Biocompatibility:High-quality medical-grade adhesives are formulated to be biocompatible, minimizing the risk of adverse reactions when in contact with the human body.
- Sterilization Compatibility:They can withstand various sterilization methods such as autoclaving, ethylene oxide, and gamma irradiation, which is essential for medical devices that require frequent sterilization.
- Flexibility and Conformability:Adhesives with high peel strength possess flexibility and conformability, allowing them to adhere well to irregular surfaces or body contours without compromising strength.
Impact on Patient Care and Industry
- Enhanced Patient Comfort:These adhesives in wound care and medical dressings ensure better adhesion without causing discomfort or skin damage, promoting faster healing and improved patient comfort.
- Improved Device Performance:Medical devices assembled using high peel strength adhesives exhibit superior performance, reliability, and longevity, contributing to better healthcare outcomes.
- Streamlined Manufacturing Processes:These adhesives enable efficient and streamlined manufacturing processes, reducing production time and costs while maintaining high-quality standards.
What are the distinct advantages of using high peel strength adhesives?
In adhesive technologies, high peel strength adhesives stand out for their exceptional bonding capabilities. These adhesives possess unique advantages that make them indispensable across various industries and applications. Here are the distinct benefits of utilizing high peel strength adhesives:
Superior Bonding Strength
- High peel strength adhesives offer unparalleled bonding strength, ensuring a robust and durable bond between surfaces.
- They adhere to diverse materials, including metals, plastics, ceramics, and composites, providing reliable connections even in demanding environments.
Enhanced Performance in Stressful Conditions
- These adhesives exhibit resilience in extreme temperatures, harsh weather conditions, and fluctuating environments, maintaining their adhesive properties when stressed.
- They resist degradation, ensuring the integrity of the bond despite exposure to moisture, chemicals, or UV radiation.
Flexibility and Adaptability
- High peel strength adhesives accommodate varying substrates and surface textures, adapting to irregularities and rough surfaces to create a strong bond.
- Their flexibility allows for expansion and contraction without compromising the bond, making them suitable for applications where materials undergo movement or vibration.
Increased Productivity and Efficiency
- Rapid-curing formulations of these adhesives expedite production processes, reducing assembly time and enhancing overall productivity.
- Their ability to bond dissimilar materials eliminates the need for mechanical fasteners, streamlining assembly and reducing material costs.
Design Versatility
- High peel strength adhesives enable innovative and intricate designs by eliminating the constraints imposed by traditional joining methods.
- They facilitate the creation of lightweight structures and enable the bonding of materials with varying coefficients of thermal expansion without compromising performance.
Environmental Benefits
- These adhesives often contribute to eco-friendly practices by reducing the need for bulky fasteners and minimizing material waste during manufacturing.
- Their efficient bonding capabilities often result in lighter and more energy-efficient final products, supporting sustainability initiatives.
Are there any limitations or challenges associated with their application?
High Peel Strength Adhesives (HPSAs) are revered for their robust bonding capabilities in various industries. However, despite their effectiveness, certain limitations and challenges often accompany their application, necessitating a nuanced understanding for optimal usage.
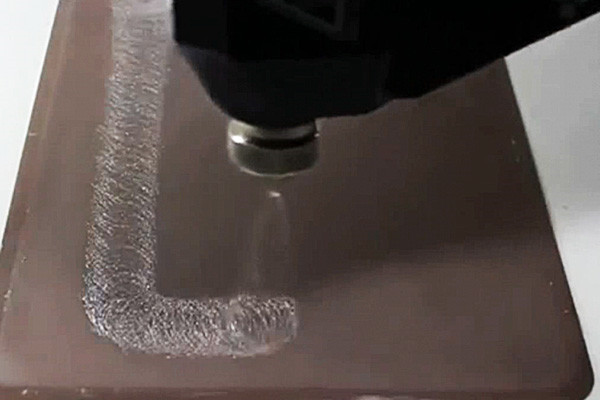
Key Attributes of High Peel Strength Adhesive
- Exceptional Bonding: Offers robust adhesion between diverse substrates.
- Versatility:Applicable across industries, including automotive, aerospace, and electronics.
- Resilience:Withstands extreme temperatures, moisture, and environmental factors.
- Enhanced Performance:This adhesive is ideal for applications that require durable, long-lasting bonds.
Limitations Associated with High Peel Strength Adhesive
- Surface Sensitivity:Adhesion effectiveness can be influenced by surface texture and cleanliness, requiring meticulous surface preparation.
- Temperature Dependency:Performance might fluctuate significantly under extreme conditions, affecting bonding strength.
- Substrate Compatibility: Not universally compatible with all substrates, demanding compatibility tests for optimal adhesion.
- Application Complexity:Certain formulations necessitate precise application techniques, affecting usability for novice users.
Challenges in Application
- Surface Preparation: Thorough cleaning and priming are crucial, demanding additional time and resources.
- Temperature Control:Managing optimal temperature during application becomes critical for consistent and reliable bonding.
- Compatibility Testing:Conducting compatibility tests for diverse substrates adds complexity and time to the process.
- Expertise and Training:Skill and expertise are required to apply some HPSAs precisely, leading to a learning curve for users.
Overcoming Challenges
- Advanced Surface Preparation Techniques:Employing innovative methods to enhance surface cleanliness and texture.
- Temperature Management Systems:One can implement controlled environments or specialized tools to regulate temperatures during application.
- Formulation Development:Continual improvement in formulations to mitigate substrate compatibility issues.
- Training Programs: Offering comprehensive training to users for optimal application techniques.
How do environmental factors affect the performance of these adhesives?
Adhesives are vital in various industries, securing bonds and ensuring durability. High Peel Strength Adhesives stand out for their robustness in holding materials together under stress. However, their performance isn’t immune to environmental factors. Understanding how these elements impact these adhesives is crucial for maintaining their efficacy in diverse conditions.
Environmental Factors
Temperature Extremes
- High Temperatures:Excessive heat can soften adhesives, reducing their peel strength.
- Low Temperatures:Cold environments can make adhesives brittle, compromising their ability to withstand peeling forces.
Humidity Levels
- High Humidity:Moisture can seep into adhesives, causing them to swell or degrade, affecting peel strength.
- Low Humidity:Dry conditions may lead to adhesive shrinkage, affecting bond integrity and peel strength.
UV Exposure
- Ultraviolet radiation can degrade adhesives over time, especially those lacking UV stabilizers, reducing peel strength.
- Long-term exposure to sunlight can cause discoloration and chemical breakdown, impacting adhesive performance.
Chemical Exposure
- Contact with certain chemicals can alter adhesive properties, affecting their peel strength.
- Compatibility with specific substances needs consideration to maintain adhesive effectiveness.
How Environmental Factors Influence Adhesive Performance:
Chemical Composition
- Adhesives with specific formulations exhibit better resistance to environmental factors.
- Factors such as polymer types and additives are crucial in determining resilience.
Testing and Evaluation
- Rigorous testing under simulated environmental conditions helps assess adhesive performance.
- Accelerated aging tests aid in predicting the long-term effects of environmental exposure.
Mitigation Strategies
- Formulating adhesives with additives that enhance resistance to environmental stressors.
- Employing protective coatings or barriers to shield adhesives from adverse conditions.
Adaptive Designs
- Developing adhesive systems tailored for specific environments boosts performance and longevity.
- Customizing adhesive properties to withstand prevalent environmental challenges.
How does surface preparation impact peel strength?
The adhesive’s ability to bond strongly and endure stresses relies significantly on how well the surface is prepped before application. A meticulous surface preparation ensures maximal adhesion, while negligence in this phase can compromise the adhesive’s performance. Let’s delve into how surface preparation impacts the peel strength of high peel strength adhesives:
Cleanliness is Key
- Contaminants like dirt, dust, oils, and residues hinder adhesion by creating a barrier between the adhesive and the surface.
- Thorough cleaning using suitable solvents or cleaners is imperative to eliminate these contaminants.
Surface Roughness
- An adequately roughened surface facilitates a stronger mechanical bond by providing more surface area for the adhesive to grip onto.
- Methods like abrasion, sanding, or chemical etching enhance surface roughness, optimizing adhesion.
Chemical Compatibility
- Understanding the surface material and its compatibility with the adhesive is crucial.
- Some materials may require primers or surface treatments to enhance adhesion by promoting chemical compatibility.
Moisture and Humidity Control
- Moisture can significantly affect adhesion, especially in high-humidity environments.
- Ensuring dry surfaces and controlling humidity during application are essential to prevent adhesive weakening.
Surface Activation
- Some substrates benefit from treatments that activate the surface for better bonding.
- Plasma treatment or corona discharge are examples of methods used to activate surfaces, improving adhesion.
Adhesive Selection and Application
- The choice of adhesive should align with the surface properties and environmental conditions.
- Proper application techniques, including the correct pressure and temperature, also impact peel strength.
Impact of Poor Surface Preparation
Neglecting surface preparation can lead to several issues:
- Reduced peel strength:Inadequate bonding due to contaminants or poor surface conditions.
- Premature failure:The adhesive might not endure stresses, leading to early detachment.
- Wastage:Subsequent rework or product failures due to weak adhesion can incur additional costs.
What role do temperature and curing conditions play in peel strength?
High peel strength adhesives are integral in various industries, offering robust bonding solutions. However, temperature and curing conditions significantly influence their peel strength. Let’s explore the correlation between these factors:
Temperature Influence
Temperature profoundly affects the adhesive’s performance and peel strength. Here’s how:
Activation and Chemical Reaction
- Elevated temperatures often accelerate the curing process of adhesives.
- Increased temperature initiates chemical reactions within the adhesive, enhancing its bonding properties.
- Optimal temperatures can improve the adhesive’s ability to penetrate surfaces, fostering stronger adhesion.
Viscosity and Flow
- Higher temperatures reduce the viscosity of adhesives, enhancing their flow.
- Improved flow allows the adhesive to effectively cover the bonding surfaces, contributing to better adhesion strength.
- However, excessively high temperatures might cause premature curing or evaporation, compromising bonding quality.
Curing Conditions Impact
Curing conditions refer to the environment or specific conditions required for the adhesive to set correctly. Consider these aspects:
Time and Dwell Period
- Adequate curing time is crucial for the adhesive to attain its maximum strength.
- Dwell periods, or the duration the adhesive is held under specific conditions, impact its peel strength.
- Insufficient curing time or premature exposure to stress can result in weaker bonds.
Humidity and Moisture
- Some adhesives are sensitive to moisture content during curing.
- Controlled humidity levels can affect the adhesive’s chemical reaction and bond formation.
- Excessive moisture might hinder the curing process, affecting peel strength adversely.
Optimizing Peel Strength
Achieving optimal peel strength with high peel strength adhesives necessitates meticulous control of temperature and curing conditions:
- Conduct thorough testing to determine the ideal temperature range for the specific adhesive and application.
- Adhere strictly to recommended curing conditions specified by the adhesive manufacturer.
- Implement controlled environments, ensuring consistent humidity levels and sufficient curing time.
- Regularly monitor and adjust conditions during curing to prevent deviations affecting peel strength.
Are there specific substrate combinations that maximize peel strength?
In adhesive applications, the term “peel strength” holds paramount importance. It refers to the force required to separate two adhered surfaces in a peel test. High peel strength adhesives play a pivotal role in various industries, from automotive to electronics, because they maintain robust bonding under stress. But the burning question persists: Are there specific substrate combinations that maximize peel strength?
Here’s a closer look at the correlation between high peel strength adhesives and optimal substrate combinations:
Understanding High Peel Strength Adhesives
- High peel strength adhesives are engineered to endure substantial mechanical stress and environmental factors, offering superior performance in demanding applications.
- They possess a solid, cohesive force that maintains adhesion even under challenging conditions, preventing premature failure.
Factors Influencing Peel Strength
- Adhesive Formulation:The peel strength of the adhesive is determined significantly by the composition and formulation within various applications. Chemical properties and flexibility impact the adhesive’s ability to adhere to different substrates.
- Surface Preparation: Proper cleaning and treatment of the substrate surfaces are vital. Surface roughness, cleanliness, and compatibility with the adhesive significantly affect peel strength.
- Substrate Combination:The combination of substrates dramatically influences the overall peel strength. Matching the adhesive to specific substrate materials is essential for optimal performance.
Maximizing Peel Strength through Substrate Combinations
- Compatibility Testing:Conducting compatibility tests between the adhesive and various substrates helps identify the ideal combination that maximizes peel strength.
- Material Selection:Choosing substrates with complementary properties to the adhesive, such as similar flexibility or surface energy, enhances peel strength.
- Surface Modification:Implementing surface treatments like primers or coatings can improve the adhesion properties of substrates, consequently boosting peel strength.
Optimizing Application Techniques
- Applying the adhesive within a recommended temperature and pressure range enhances its bonding capabilities.
- Ensuring uniformity and adequate coverage during application contributes to achieving higher peel strength.
How does proper adhesive selection enhance peel strength?
Regarding bonding materials, achieving optimal peel strength ensures durability and longevity in various applications. Selecting a suitable adhesive plays a pivotal role in determining the peel strength of bonded surfaces. Specifically, high peel strength adhesives are designed to provide superior resistance to forces applied in a peeling motion. Understanding how proper adhesive selection enhances peel strength is crucial in achieving reliable and robust bonds.
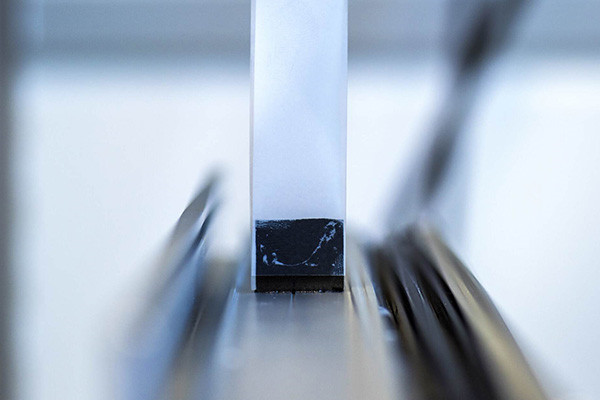
Factors Influencing Peel Strength
- Adhesive Composition:The formulation of high peel strength adhesives involves specific compounds that enhance their ability to withstand peeling forces. These formulations often incorporate polymers and additives tailored to promote adhesion under varying conditions.
- Surface Preparation:Proper surface preparation is vital for optimizing peel strength. Adhesives adhere best to clean, dry, and adequately roughened surfaces, ensuring maximum contact and bonding efficacy.
Benefits of Proper Adhesive Selection
- Enhanced Bonding Performance:High peel strength adhesives exhibit superior bonding capabilities, creating robust connections that resist peeling forces, thereby reducing the risk of material separation.
- Improved Durability:By selecting adhesives tailored to the specific materials and environmental conditions, the durability of bonded assemblies significantly increases. The formulation ensures longevity even under challenging circumstances.
- Reduced Failure Risks:Carefully selecting high peel strength adhesives minimizes the likelihood of bond failure, preventing potential safety hazards and costly rework.
Application Areas
- Automotive Industry:High peel strength adhesives are extensively used in the automotive sector for bonding various components, ensuring structural integrity and safety in vehicles.
- Construction Sector:In construction, these adhesives play a vital role in bonding materials like metals, plastics, and composites, enhancing the strength and reliability of structures.
- Electronic Devices:The delicate nature of electronic devices demands solid and reliable bonds. High peel strength adhesives secure components, preventing detachment due to stress or environmental factors.
What are the standard methods for testing peel strength?
Peel strength is a critical parameter determining the adhesive’s ability to withstand external forces in adhesives. High Peel Strength Adhesives play a pivotal role in various industries, ensuring the integrity of bonds under challenging conditions. Rigorous testing methods are employed to ascertain their performance. Here, we delve into the standard techniques for testing peel strength, shedding light on the crucial procedures that validate the strength of these adhesives.
Peel Test
- Purpose:Assess the adhesive’s resistance to separation.
- Procedure:A bonded sample is subjected to a controlled force, peeling apart at a specified angle and speed.
- Measurement:Peel strength is measured in force per unit width.
180-Degree Peel Test
- Purpose:Evaluate the adhesive’s performance under extreme conditions.
- Procedure:The sample is peeled back at a 180-degree angle, simulating a more severe separation force.
- Measurement:Similar to the peel test, the force required is quantified.
T-Peel Test
- Purpose:Measures the peel strength for flexible materials.
- Procedure:The sample is shaped as a ‘T,’ and separation occurs by pulling the arms of the ‘T’ in opposite directions.
- Measurement:Peel strength is calculated based on the force needed to initiate and propagate separation.
Floating Roller Peel Test
- Purpose:Evaluate the adhesive’s performance under continuous peel conditions.
- Procedure:The sample is wrapped around a roller, and a weight is suspended, causing continuous peeling.
- Measurement:Peel strength is assessed over a given distance of continuous peeling.
Loop Tack Test
- Purpose:Measures the adhesive’s ability to form an instant bond upon contact.
- Procedure:A sample is brought into contact with a surface and rapidly separated.
- Measurement:The force required to separate the adhesive is quantified.
Climbing Drum Peel Test
- Purpose:Evaluate the peel strength of laminated structures.
- Procedure:A sample is wrapped around a drum, and a weight is applied, causing peeling.
- Measurement:Peel strength is measured based on the force required for continuous peeling.
Floating Roller Tack Test
- Purpose: Assesses the tackiness of an adhesive.
- Procedure: Similar to the Floating Roller Peel Test, but measures the force needed to initiate separation.
- Measurement:Evaluate the adhesive’s instant bonding capability.
How is the reliability of high peel strength adhesives assessed?
High peel strength adhesives play a pivotal role in various industries, offering robust bonding solutions for diverse applications. However, ensuring their reliability is crucial for maintaining product integrity and safety. Assessing the reliability of these adhesives involves comprehensive evaluation techniques to guarantee their performance under various conditions.
Critical Factors in Assessing Reliability
- Peel Strength Testing:The primary method involves determining the force required to peel apart bonded materials. This test measures the adhesive’s ability to withstand stress during separation, reflecting its reliability in real-world applications.
- Substrate Compatibility:Assessing how well the adhesive interacts with different substrates is crucial. Compatibility testing involves evaluating the adhesive’s performance on various materials intended to bond.
- Environmental Resistance:High peel strength adhesives must endure diverse ecological conditions. Testing involves subjecting bonded materials to temperature extremes, humidity, and chemical exposure to gauge the adhesive’s resilience.
- Aging Studies:Adhesive reliability often relies on its long-term performance. Accelerated aging studies simulate prolonged exposure to UV radiation and temperature fluctuations to predict the adhesive’s durability over time.
- Failure Analysis:Understanding why adhesives fail is essential. Analyzing the mode of failure provides insights into improving formulation or application methods to enhance reliability.
Assessment Techniques
- ASTM Standards:Many assessments follow standardized protocols outlined by the American Society for Testing and Materials (ASTM). These standards ensure consistency and reliability in testing methodologies.
- Pull Testing Equipment: Specialized equipment measures peel strength accurately. The results help validate adherence to industry-specific standards and requirements.
- Microscopic Examination:Analyzing the bonded interface at a microscopic level reveals bonding quality, interface uniformity, and potential weaknesses that might affect reliability.
- Real-world Simulation Tests: Mimicking real-world conditions aids in predicting adhesive performance in practical applications, offering invaluable insights into its reliability.
The Importance of Reliability Assessment
- Product Safety:Ensuring high peel strength adhesive reliability is crucial in industries like aerospace, automotive, and healthcare, where failure can lead to severe consequences.
- Quality Assurance:Reliable adhesives contribute to product quality and customer satisfaction, reducing the risk of recalls or warranty issues.
- Cost Savings:Rigorous reliability assessment prevents failures, reducing costly rework, downtime, and material wastage.
Are there innovative techniques for evaluating long-term performance?
High Peel Strength Adhesives have become integral in various industries, promising exceptional bonding in challenging conditions. However, ensuring their long-term performance remains a critical concern for engineers and manufacturers. Are there innovative techniques available for evaluating their endurance and reliability? Let’s explore:
Traditional Assessments vs. Innovative Techniques
- Conventional methods like accelerated aging tests and stress-strain analyses offer insights but may not accurately replicate real-world conditions or long-term behavior.
- Innovative techniques focus on simulating extended-use scenarios, providing a more comprehensive understanding of adhesive performance over time.
Environmental Simulation Chambers
- These chambers recreate extreme conditions such as temperature variations, humidity, UV exposure, and chemical aggressiveness to test adhesives’ durability over an extended period.
- Real-time monitoring within these chambers allows for precise observation of how adhesives respond and degrade in diverse environments.
Micromechanical Testing
- Utilizing advanced microscopy and nanotechnology, researchers examine the microstructure of adhesive bonds, observing changes and defects at a microscopic level.
- This technique aids in understanding the evolution of bond interfaces identifying potential failure mechanisms before they manifest macroscopically.
Accelerated Creep Testing
- Accelerated creep testing simulates long-term stress conditions by subjecting adhesive joints to sustained loads over an extended period.
- This method helps predict the adhesive’s behavior under continuous stress, which is vital for applications with constant strain requirements.
Sensor Technology Integration
- Innovations in sensor technology allow for the real-time monitoring of adhesive performance.
- Embedded sensors provide continuous data on factors like temperature, stress, and strain, offering a dynamic understanding of how adhesives endure in real-world scenarios.
Machine Learning and Predictive Models
- Combining historical performance data with machine learning algorithms enables the creation of predictive models.
- These models forecast the long-term behavior of high peel strength adhesives, aiding in proactive decision-making for product development and maintenance.
What advancements are anticipated in high peel strength adhesive technology?
High peel strength adhesive technology continues to evolve, catering to diverse industrial needs. As industries demand more resilient, versatile, and efficient adhesive solutions, advancements in this field are anticipated to meet these challenges head-on.
Advancements Expected
- Nano-Enhanced Formulations:The integration of nanotechnology enhances adhesive properties, including improved bonding strength, durability, and resistance to environmental factors.
- Customized Adhesive Solutions:Tailoring adhesives to specific industry requirements ensures their compatibility with various substrates and environmental conditions.
- Multi-Substrate Bonding:Innovations enabling adequate bonding between dissimilar materials expand application possibilities across automotive, aerospace, and electronics industries.
- Improved Temperature Resistance:Anticipated advancements in high peel strength adhesives aim to withstand extreme temperatures, ensuring stability in harsh operating environments.
- Green and Sustainable Adhesives:Development of eco-friendly formulations with reduced environmental impact, meeting the growing demand for sustainable manufacturing practices.
- Rapid Cure and Handling:Introduction of faster curing adhesives that allow for quicker assembly processes, improving productivity without compromising bonding strength.
- Enhanced Flexibility and Toughness:Future adhesives may possess increased flexibility and toughness, vital for applications subjected to dynamic stress or movement.
- Smart Adhesive Systems:Integration of sensors or functionalities within adhesives for monitoring structural integrity, enabling predictive maintenance in various applications.
- Bio-Inspired Adhesives:Drawing inspiration from natural adhesives found in organisms, creating adhesives with exceptional bonding capabilities, even in challenging conditions.
- Digitalization and Manufacturing Innovations:Adopting digital technologies in manufacturing optimizes adhesive application methods for precise and efficient bonding.
How might these innovations impact various industries in the coming years?
Innovation in adhesive technology, specifically developing high peel strength adhesives, is set to revolutionize various industries in the coming years. These advanced adhesives possess superior bonding capabilities and offer versatile applications across multiple sectors, heralding transformative changes.
Innovations
- Enhanced Bonding Properties:High peel strength adhesives exhibit unparalleled adhesive capabilities, bonding diverse materials like metals, plastics, and composites with exceptional strength and durability.
- Customizable Formulations:These adhesives can be tailored to meet specific industry requirements, offering variations in viscosity, curing time, and adhesion strength.
- Temperature and Environmental Resistance:With resistance to extreme temperatures and environmental factors, these adhesives provide reliability in harsh conditions, making them ideal for demanding applications.
Potential Industry Impacts
- Automotive Sector:High peel strength adhesives are poised to transform automotive manufacturing processes. They enable lightweight construction, improve structural integrity, and facilitate the assembly of composite materials, enhancing vehicle performance and safety.
- Electronics and Technology:In electronic device manufacturing, these adhesives offer improved bonding for delicate components, ensuring durability and longevity. They also enable miniaturization and support assembling smaller, more complex devices.
- Aerospace and Aviation:With their ability to withstand high-stress environments and temperature variations, these adhesives will find extensive use in aircraft assembly, reducing weight while maintaining structural integrity.
- Construction and Infrastructure:High peel strength adhesives will revolutionize construction by facilitating the bonding of diverse materials, enhancing building strength, and streamlining construction processes.
- Medical and Healthcare:In the medical field, these adhesives can assemble medical devices and implants, ensuring secure and reliable bonding without compromising biocompatibility.
- Packaging Industry:Improved adhesive strength will revolutionize packaging, offering secure seals for various materials and enabling sustainable packaging solutions.
CONCLUSION
High Peel Strength Adhesives stand tall with their unparalleled bonding capabilities as the linchpin in modern industrial applications. From the sturdy foundations of automotive construction to the intricate medical device manufacturing needs, their impact reverberates across sectors. As we draw the curtain on this exploration, their significance remains resolute. With their inherent advantages and evolving technologies, these adhesives promise not just durability and versatility but also a pathway to future advancements. The possibilities they unravel for diverse industries are limitless, poised to reshape methodologies and elevate standards.
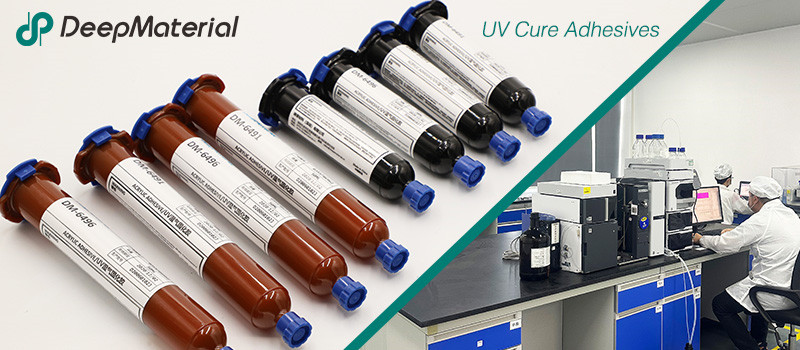
DeepMaterial
Based on the core technology of adhesives, DeepMaterial has developed adhesives for chip packaging and testing, circuit board level adhesives, and adhesives for electronic products. Based on adhesives, it has developed protective films, semiconductor fillers, and packaging materials for semiconductor wafer processing and chip packaging and testing. More…
UV Curing Adhesives
UV light cure have a number of benefits making them a popular choice among many product assembly and manufacturing applications. Many UV light cure adhesives can provide a nearly instantaneous bond to difficult substrates like glass and plastic. UV cure adhesives often require an accelerator or UV light for a bond to form.
Adhesive Blogs & News
The latest adhesive industry science and technology, Deepmaterial news, and market trends and forecasts.
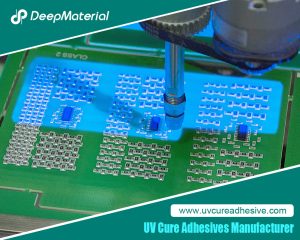
In – depth Analysis of the Main Characteristics of UV Adhesives for Touch Screens
In – depth Analysis of the Main Characteristics of UV Adhesives for Touch Screens In the manufacturing of modern electronic devices, the touch screen serves as a crucial component for human – machine interaction, and its performance and quality are of utmost importance. As a key material for effectively bonding various components of the touch
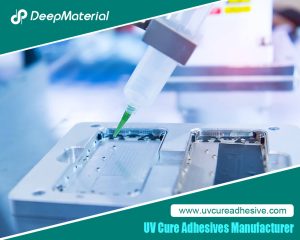
The Quantitative Influence of Crosslinking Density on the Flexibility and Hardness of Adhesives and the Formulation Optimization Strategy
The Quantitative Influence of Crosslinking Density on the Flexibility and Hardness of Adhesives and the Formulation Optimization Strategy This article systematically expounds the quantitative relationship between the crosslinking density and the flexibility and hardness of adhesives. Combining the theories of polymer physics with experimental analysis methods, it reveals the mechanism of the action of the
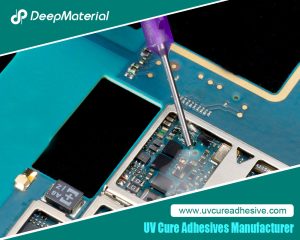
Technical Strategies for Balancing the Rapid Curing Property and Long Operating Time of UV Adhesives
Technical Strategies for Balancing the Rapid Curing Property and Long Operating Time of UV Adhesives UV adhesives have been widely used in many fields such as electronics, optics, and medicine due to their advantages of rapid curing, high bonding strength, and environmental protection. However, their rapid curing property also brings challenges in some application scenarios.
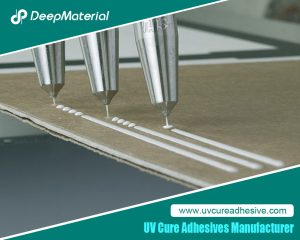
Biocompatibility of LED UV Glue Adhesive and Its Application Potential in Medical and Food Packaging Fields
Biocompatibility of LED UV Glue Adhesive and Its Application Potential in Medical and Food Packaging Fields LED UV glue adhesive has been widely applied in numerous fields due to its advantages such as rapid curing and easy operation. However, in fields with stringent safety requirements like medical and food packaging, its biocompatibility after curing
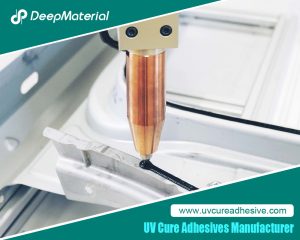
Exploring the Environmental Performance of UV Glue and Strategies for Optimizing Odor and VOC Content
Exploring the Environmental Performance of UV Glue and Strategies for Optimizing Odor and VOC Content UV glue, as an adhesive that achieves rapid curing through ultraviolet (UV) light irradiation, has been widely applied in numerous fields such as electronics, optics, healthcare, and automobiles, thanks to its advantages of fast curing speed, high bonding strength, and
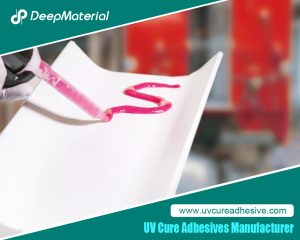
Compatibility Analysis and Countermeasures of LED UV Glue with Automated Production Equipment
Compatibility Analysis and Countermeasures of LED UV Glue with Automated Production Equipment LED UV glue has been widely used in modern manufacturing due to its advantages such as fast curing speed, high bonding strength, and environmental friendliness. However, in the automated production process, if there are problems with the adaptability between the glue and equipment