Low Temperature Adhesive
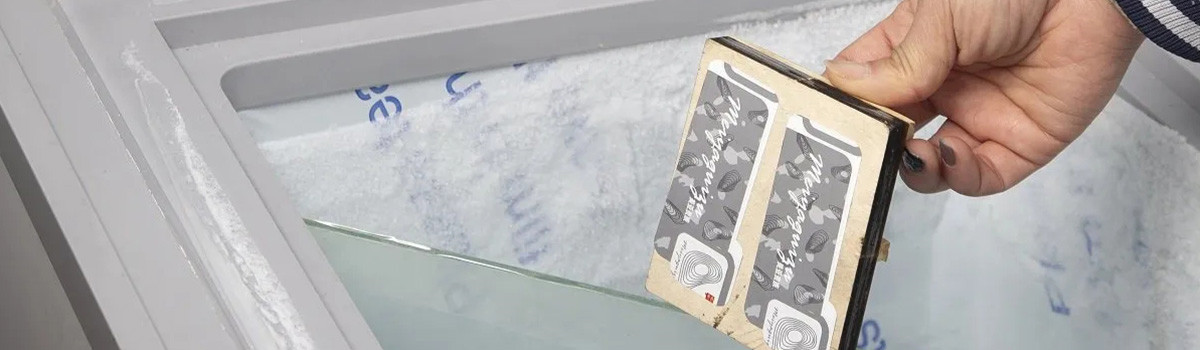
In the intricate tapestry of modern manufacturing and crafting, the role of adhesives is both vital and ever-evolving. Amid this landscape, a revolutionary advancement has emerged: low temperature adhesives. These compounds, with their unique formulation and exceptional properties, stand at the forefront of innovation, offering a transformative solution to bond materials at lower temperatures than traditional adhesives. From industrial applications to creative pursuits, the advent of these adhesives marks a paradigm shift, promising enhanced efficiency, versatility, and sustainability. Let’s embark on a journey into the realm of low temperature adhesives, exploring their composition, capabilities, and the myriad of possibilities they present across diverse industries and everyday tasks.
Table of Contents
ToggleWhat are Low Temperature Adhesives?
Low temperature adhesives refer to a specialized category of bonding agents designed to function effectively and maintain structural integrity at lower temperature ranges. These adhesives possess distinctive characteristics that set them apart in various applications, particularly in scenarios where conventional adhesives might fail due to temperature constraints. Key aspects defining low temperature adhesives include:
- Temperature Resilience:These adhesives are formulated to retain their adhesive properties even in environments with significantly lower temperatures, ensuring stability and bonding efficacy.
- Flexible Application Range:They exhibit versatility, functioning across a spectrum of temperatures, often extending from sub-zero conditions to moderately low levels.
- Enhanced Formulations:Manufacturers engineer these adhesives with specialized chemical compositions and additives that enable them to maintain bonding strength despite exposure to cold environments.
- Diverse Applications:Low temperature adhesives find utility in various industries, from automotive and aerospace sectors requiring bonding in extreme conditions to electronics and packaging industries necessitating adhesive performance in refrigerated settings.
- Improved Cure Time:Some variants of these adhesives offer accelerated curing mechanisms, facilitating quicker bonding even in colder environments where conventional adhesives might struggle to set effectively.
Overall, low temperature adhesives showcase a unique blend of resilience, adaptability, and efficacy, making them indispensable in applications where maintaining bonding integrity in colder climates or environments is paramount. Their specialized formulations enable industries to address challenges posed by temperature extremes, ensuring reliable and durable bonds despite adverse thermal conditions.
How do Low Temp Adhesives Differ from Standard Adhesives?
Low temperature adhesives stand apart from standard adhesives due to their specialized properties designed to perform optimally in specific conditions. Their distinction lies in several key aspects:
- Lower Activation Temperature:Low temperature variants exhibit a lower activation threshold, unlike standard adhesives. They remain solid at room temperature but efficiently activate and bond materials at much lower temperatures, often around 250°F (121°C) or even lower. This characteristic makes them ideal for bonding heat-sensitive materials that cannot withstand high temperatures.
- Flexibility and Versatility:These adhesives offer versatility in bonding a wide range of materials, including plastics, fabrics, foams, and metals. Their flexibility allows for application in various industries, such as electronics, automotive, and medical devices, addressing specific needs in each sector.
- Quick Setting Time:Low temp adhesives typically boast a fast curing or setting time once activated. This attribute reduces production time and enhances efficiency in assembly lines or applications requiring rapid bonding without compromising bond strength.
- Enhanced Stability:They demonstrate excellent stability, maintaining their adhesive properties even in extreme temperatures. This stability ensures a durable and long-lasting bond, crucial for applications subject to temperature variations or harsh environmental conditions.
These unique properties present several advantages:
- Preservation of Material Integrity:By operating at lower temperatures, these adhesives prevent damage or distortion to sensitive materials, preserving their structural integrity during bonding.
- Expanded Application Possibilities:Their ability to bond heat-sensitive substrates widens the scope of applications in industries where traditional high-temperature adhesives may be unsuitable, enabling manufacturers to explore new design options.
- Efficiency and Cost-effectiveness:Their quick setting time reduces production cycles and overall costs by streamlining manufacturing processes, making them an economical choice for high-volume production lines.
- Reliability in Varied Environments:The stability of Low temp adhesives ensures a reliable bond even in extreme environments, offering longevity and durability crucial for applications exposed to fluctuating temperatures or harsh conditions.
Low temperature adhesives exhibit unique properties that set them apart from standard adhesives. Their lower activation temperature, versatility, quick setting time, and enhanced stability provide several advantages, including preserving material integrity, expanding application possibilities, enhancing efficiency, and ensuring reliability in diverse environments. These characteristics make them valuable for industries seeking efficient, durable, and adaptable bonding solutions.
What Are the Primary Components of Low Temperature Adhesives?
Low temperature adhesives comprise several key components, each contributing to their unique properties and performance:
Polymer Base
At the core of low temperature adhesives lies a diverse array of polymer bases, each tailored for specific applications. These adhesives often utilize polyethylene, polyvinyl acetate (PVA), or modified copolymers designed explicitly for lower activation temperatures. These polymer bases are the adhesive’s foundation, providing the essential bonding structure and determining its overall properties.
Functional Additives
Complementing the polymer base are functional additives that enhance and modify the adhesive’s characteristics. Resins like epoxy or acrylic compounds are frequently integrated to fortify the adhesive, augmenting its strength, flexibility, and adhesion capabilities. Additives, such as plasticizers or tackifiers, may also be introduced to adjust the viscosity, tackiness, or curing speed, optimizing the adhesive for specific applications.
Strengthening Fillers
Low temperature adhesives should be used to bolster mechanical properties. These fillers, which may include silica, calcium carbonate, or microspheres, serve to improve strength, impact resistance, and thermal conductivity. Reinforcements, like fibers or nanoparticles, may also be included to fortify specific mechanical attributes based on the adhesive’s intended use.
Activation Agents
Low-temp adhesives are critical to their functionality and feature activation agents or catalysts that facilitate bonding at reduced temperatures. These compounds expedite the activation and curing process at the designated lower temperature range, ensuring efficient and robust bonding between materials while maintaining stability and durability.
Application Aids
Specific formulations may include solvents or carriers to facilitate application processes. These agents adjust the viscosity for ease of use and temporarily aid in adhesion before the adhesive completes its curing cycle. Their presence streamlines the application process and contributes to the adhesive’s overall performance.
These primary components’ intricate combination and precise formulation culminate in low temperature adhesives capable of bonding effectively at reduced temperatures while exhibiting specific mechanical, chemical, and application-related attributes. These components collectively determine the adhesive’s suitability for industries requiring robust bonding solutions in lower temperature environments.
How Do Low Temperature Adhesives Work?
Low temperature adhesives use a sophisticated bonding process that leverages specific mechanisms to create durable bonds, even at reduced temperatures. The bonding process involves several key steps and mechanisms:
- Activation at Lower Temperatures:Unlike traditional adhesives that require higher temperatures for activation, low temperature variants initiate their bonding process at significantly reduced temperatures, often around 250°F (121°C) or lower. This characteristic allows them to bond materials without subjecting them to excessive heat, making them ideal for heat-sensitive substrates.
- Adhesive Application:The adhesive is applied to the surfaces intended for bonding. Depending on the formulation, these adhesives may come in various forms—liquids, solids, or films—allowing for diverse application methods such as spraying, brushing, or roll-coating.
- Chemical Interaction and Wetting:The adhesive facilitates chemical interaction and wetting by chemically interacting with the substrate surfaces upon application. This interaction involves wetting, where the adhesive spreads across the surface, maximizing contact between the adhesive and the material. This step is crucial for achieving strong adhesion.
- Curing and Setting:Activation agents or catalysts within the adhesive begin the curing process at lower temperatures, initiating chemical reactions that transform the adhesive from a liquid or semi-solid state to a solid state. This curing stage may involve cross-linking of polymer chains or polymerization processes, contributing to bond formation.
- Bond Development:As the adhesive cures, it establishes a firm bond between the surfaces. The adhesive’s molecular structure intertwines with the substrate, creating a strong and durable connection. The resulting bond exhibits good mechanical strength, adhesion, and resistance to environmental factors.
- Strength Development Over Time:While the initial bond forms during curing, low temperature adhesives may continue to strengthen. This gradual enhancement of bond strength ensures the longevity and reliability of the adhesive joint.
The underlying mechanisms involve a combination of chemical reactions, surface interactions, and molecular adhesion to create robust bonds between materials at lower temperatures. These adhesives’ ability to initiate and complete the bonding process effectively at reduced temperatures while maintaining excellent adhesive properties makes them indispensable in industries requiring reliable bonding solutions for heat-sensitive substrates and applications.
What Are the Key Benefits of Using Low Temperature Adhesives?
Low temperature adhesives present a spectrum of advantages, from preserving material integrity and offering versatility in application to enhancing efficiency, durability, and cost-effectiveness across industries. Their ability to cater to heat-sensitive materials while ensuring strong, reliable bonds at reduced temperatures makes them a valuable solution in various manufacturing and assembly processes.
Preservation of Material Integrity
- Heat-Sensitive Material Compatibility:low temperature adhesives are specifically formulated to bond materials sensitive to high temperatures, safeguarding their structural integrity during bonding.
- Prevents Distortion or Damage:By activating at lower temperatures, these adhesives prevent distortion, warping, or degradation of delicate materials, ensuring their quality remains intact.
Versatility and Application Flexibility
- Wide Range of Material Compatibility:These adhesives offer compatibility with an extensive array of materials, including plastics, fabrics, metals, and more, making them versatile across diverse industries.
- Adaptability to Various Environments:Their ability to bond dissimilar materials and perform well in different environmental conditions enhances their applicability in numerous settings.
Efficiency and Time-Saving
- Quick Activation and Curing:low temperature adhesives exhibit rapid activation and curing times, streamlining production processes by reducing wait times and accelerating assembly lines.
- Increased Productivity:The efficiency in bonding at lower temperatures enhances overall productivity by facilitating quicker bonding cycles and faster turnaround times.
Durability and Reliability
- Stable Bonding Performance:These adhesives offer stable and durable bonding performance even in fluctuating temperature environments, ensuring the long-term reliability of the bonded components.
- Mechanical Strength:The bonds formed by low temperature adhesives exhibit strong mechanical properties, providing robust connections that withstand varying stressors.
Cost-Effectiveness and Waste Reduction
- Optimized Material Usage:Their compatibility with heat-sensitive materials reduces material wastage by preventing bonding damage, contributing to production cost savings.
- Lower Energy Consumption:Operating at lower temperatures reduces energy consumption during the bonding process, leading to potential cost reductions in manufacturing operations.
What Are the Main Applications of Low Temperature Adhesives?
Low temperature adhesives find diverse applications across industries where bonding materials at reduced temperatures is essential. From electronics and automotive manufacturing to medical devices, textiles, aerospace, and packaging, these adhesives are critical in ensuring strong, reliable bonds while preserving the integrity of heat-sensitive substrates in a wide range of applications.
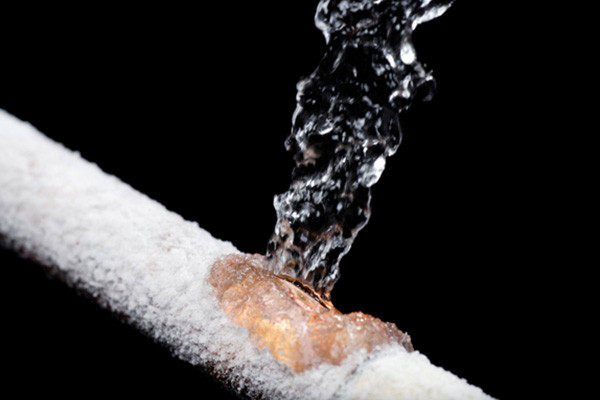
Electronics Assembly and Component Bonding
- Bonding Circuitry:low temperature adhesives find extensive use in electronics for bonding sensitive components and circuitry without subjecting them to high heat, ensuring their functionality remains uncompromised.
- Potting and Encapsulation:They are employed in potting and encapsulation processes, securing delicate electronic components within protective casings without damaging heat-sensitive parts.
Automotive Industry
- Interior Components:These adhesives are utilized in bonding interior components like upholstery, trims, and dashboard fixtures in vehicles, offering solid and durable bonds without affecting sensitive materials.
- Lightweight Material Bonding:In the quest for lighter vehicle designs, low-temp adhesives are essential for bonding lightweight materials like composites and plastics used in modern automotive construction.
Medical Device Manufacturing
- Disposable Medical Devices:low temperature adhesives play a pivotal role in bonding components for disposable medical devices, ensuring sterile packaging and functionality without compromising the integrity of heat-sensitive materials.
- Surgical Instrument Assembly:They assemble surgical instruments, bonding various components to maintain sterilization standards and equipment functionality.
Textile and Fabric Industry
- Textile Bonding:These adhesives facilitate bonding in textile manufacturing, securing seams, laminating fabrics, and attaching patches or embellishments without causing damage or altering the fabric’s properties.
- Apparel Production:In producing garments and footwear, low temperature adhesives are used for attaching elements like patches, trims, and decorations, ensuring solid and flexible bonds without compromising delicate materials.
Aerospace and Aviation
- Composite Material Bonding:They are crucial in bonding composite materials used in aircraft construction, allowing for lightweight and robust structural elements without subjecting them to high temperatures during assembly.
- Cabin Interior Assembly:low temperature adhesives are employed in assembling interior components in aircraft cabins, ensuring secure bonding of lightweight materials used in seating, panels, and fixtures.
Packaging and Labeling
- Carton and Box Sealing:In packaging applications, these adhesives efficiently seal cartons and boxes without compromising packaging materials, ensuring secure closures in heat-sensitive packaging.
- Label Attachment:They are used for label attachment on various packaging materials, providing strong adhesion while preserving the integrity of the labeled surface.
Are Low Temperature Adhesives Environmentally Friendly?
Low temperature adhesives have garnered attention for their potential environmental benefits, prompting questions about their eco-friendliness. These adhesives operate at lower temperatures during application, offering several potential advantages that contribute to their environmental profile:
- Reduced Energy Consumption:Low temperature adhesives require less heat during application, leading to decreased energy usage compared to traditional high-temperature adhesives. This reduction in energy consumption translates to lower carbon emissions and a smaller environmental footprint.
- Less Impact on Substrates:The lower application temperature of these adhesives can be gentler on materials, minimizing damage or distortion to sensitive substrates. This characteristic extends the lifespan of materials, reducing the need for replacements and, consequently, lessening waste generation.
- Potential for Biodegradability:Some low temperature adhesive formulations utilize environmentally friendly components that can be biodegradable or derived from renewable resources. This aspect contributes to a more sustainable end-of-life cycle for adhesive products.
Despite these potential benefits, the environmental friendliness of low temperature adhesives is subject to various factors, including the specific formulation, manufacturing processes, and end-of-life considerations:
- Chemical Composition:Some low temperature adhesives may still contain chemicals that could harm the environment. Assessing the chemical composition and potential toxicity is crucial in determining their environmental impact.
- Manufacturing Practices:The production process of these adhesives can influence their environmental footprint. Practices such as energy-efficient manufacturing, waste reduction, and recycled materials can enhance their eco-friendliness.
- Disposal and Recycling:Proper disposal and recycling methods for products containing these adhesives are essential. They are understanding how these materials break down or can be reclaimed after their use is crucial for minimizing their environmental impact.
While low temperature adhesives show promise in reducing energy consumption and minimizing substrate damage, their overall environmental friendliness depends on multiple factors. Careful consideration of their chemical composition, manufacturing practices, and end-of-life management is essential to assess and improve their sustainability. As technology advances and awareness grows, optimizing these adhesives for a more eco-friendly impact remains an ongoing goal in the adhesive industry.
What Factors Influence the Effectiveness of Low Temperature Adhesives?
The effectiveness of low temperature adhesives relies on a complex interplay of material properties, adhesive formulation, application methods, and environmental conditions. Understanding and optimizing these factors are crucial for achieving solid and durable bonds in various applications while harnessing the benefits of lower application temperatures.
Material Properties
The effectiveness of low temperature adhesives hinges significantly on the properties of the materials involved:
- Substrate Compatibility:Matching the adhesive properties with the substrates is critical. Adhesives must bond well with various materials while considering their porosity, surface energy, and composition. Compatibility issues can compromise bond strength.
- Temperature Sensitivity:Understanding the temperature limitations of both the adhesive and the materials being bonded is essential. Extreme temperatures might affect the adhesive’s efficacy, causing it to weaken or fail.
Adhesive Formulation
The formulation of low temperature adhesives dramatically influences their performance:
- Chemical Composition: Variations in adhesive chemistry impact bonding strength, flexibility, and curing time. Some formulations prioritize eco-friendliness or specific material bonding properties, affecting their effectiveness.
- Viscosity and Flow:The viscosity of the adhesive determines its flow and ability to fill gaps between substrates. An optimal viscosity ensures proper coverage and bonding strength.
Application Process
The method of applying low temperature adhesives plays a crucial role in their effectiveness:
- Application Temperature:While these adhesives operate at lower temperatures, ensuring the appropriate temperature during application is crucial for proper bonding. Deviations can affect the adhesive’s performance.
- Curing Time and Conditions:Understanding the curing process and providing the necessary time and environmental conditions, such as humidity and pressure, is pivotal for achieving the desired bond strength.
Environmental Factors
Environmental conditions can impact the effectiveness of low temperature adhesives:
- Humidity and Moisture:Some adhesives might be sensitive to moisture, affecting their bonding capabilities. Controlling humidity levels during application and curing is essential for optimal performance.
- Chemical Exposure:Exposure to certain environmental chemicals or contaminants can compromise the adhesive’s properties, leading to reduced effectiveness.
How Strong Are Bonds Created by Low Temperature Adhesives?
Low temperature adhesives are pivotal in various industries due to their versatility and applicability. Understanding the strength of bonds they create is essential for assessing their efficacy in different scenarios.
Testing Methodology
- Tensile Testing: Assessing the adhesive’s strength by subjecting bonded materials to tension.
- Shear Testing:Determining resistance to forces parallel to the bond line.
- Peel Testing:Evaluating adhesion by measuring the force required to separate bonded materials.
Factors Influencing Bond Strength
- Surface Preparation:The cleanliness and treatment of substrates.
- Adhesive Properties:The strength of bonds created by low temperature adhesives is influenced by viscosity, curing mechanism, and chemical composition.
- Environmental Conditions:Temperature, humidity, and exposure to external elements impact long-term durability.
Durability Assessment
- Accelerated Aging:We simulate prolonged use or expose the adhesive bonds to harsh environmental conditions for durability assessment.
- Cyclic Testing:Subjecting bonds to repetitive stress or temperature changes.
- Real-World Applications:We conduct field testing to assess how the bonds perform in real-world operating conditions.
Case Studies and Findings
- Comparison with High-Temperature Adhesives:We assess the performance of the adhesive in extreme conditions to understand its behavior under challenging environments.
- Long-Term Stability:Examining bond strength over extended periods.
Failure Analysis: Understanding reasons for bond failure and improving formulations.
Evaluating bond strength and durability of low temperature adhesives involves a multifaceted approach, encompassing various testing methodologies and considerations. This comprehensive assessment aids in optimizing their usage across industries, ensuring reliable and enduring bonds in diverse applications.
Are There Any Safety Concerns Associated with Low Temperature Adhesives?
Safety considerations are paramount when assessing low temperature adhesives in various applications. Understanding potential safety concerns is crucial for ensuring these adhesives’ proper handling and application, minimizing risks to both users and the environment.
Chemical Composition
- Toxicity Levels:Some adhesives may contain chemicals that pose health risks upon exposure.
- Volatile Organic Compounds (VOCs):Emission of VOCs during application can have adverse health effects and contribute to air pollution.
- Allergenic Properties:Certain adhesive components might trigger allergic reactions in sensitive individuals.
Handling and Application
- Skin Contact:Prolonged or repeated adhesive exposure can cause irritation or dermatitis.
- Inhalation:Inhalation of adhesive fumes or vapors, especially in poorly ventilated areas, can lead to respiratory issues.
- Eye Contact:Contact with eyes might result in irritation or more severe eye damage.
Environmental Impact
- Ecotoxicity: Disposal of adhesives containing harmful chemicals can negatively impact ecosystems.
- Persistence and Bioaccumulation:Some adhesive components may persist in the environment and accumulate in organisms, causing long-term ecological harm.
- Waste Disposal:Proper disposal methods are crucial to prevent environmental contamination.
Safety Measures and Mitigation
- Ventilation:Adequate ventilation in workspaces minimizes exposure to fumes.
- Personal Protective Equipment (PPE):Using gloves, masks, and eye protection reduces direct contact and inhalation risks.
- Substitution and Alternatives: Exploring less hazardous adhesive formulations or alternative bonding methods.
Careful handling, adherence to safety guidelines, and choosing less toxic adhesives can mitigate safety concerns associated with low temperature adhesives. Understanding the potential risks enables the implementation of measures to ensure safe usage and disposal practices, promoting user safety and environmental health.
Can Low Temperature Adhesives Withstand Extreme Conditions?
Low temperature adhesives have revolutionized various industries, offering versatile bonding solutions. But do these adhesives hold up under extreme conditions? Let’s explore their resilience against heat, cold, and moisture.
Resistance to Heat
- Thresholds:Low temperature adhesives exhibit remarkable stability even when exposed to moderate heat. Many can withstand temperatures up to 200°F (93°C) without compromising their bonding strength.
- Applications:In industries like electronics, where heat dissipation is critical, these adhesives prove invaluable, ensuring components stay firmly bonded despite elevated temperatures.
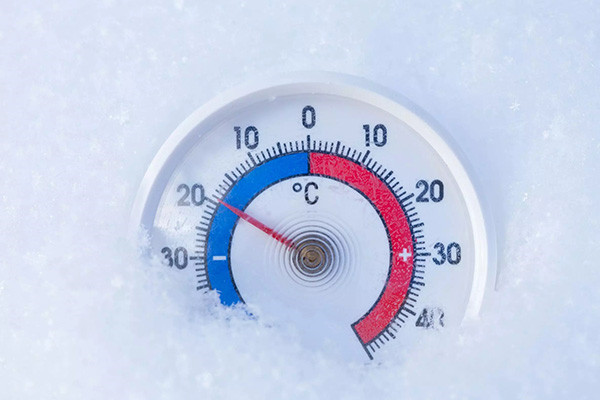
Cold Tolerance
- Flexibility:Unlike conventional adhesives that may become brittle in cold environments, low temperature adhesives retain flexibility and bonding efficacy in sub-zero conditions.
- Applications:Ideal for automotive industries where parts endure extreme cold, these adhesives maintain integrity, preventing structural failures in freezing temperatures.
Moisture Resistance
- Hydrophobic Properties:Many low temperature adhesives boast hydrophobic characteristics, repelling moisture and preventing the weakening bonds even in high-humidity environments.
- Applications:In marine or outdoor applications where exposure to moisture is constant, these adhesives ensure durability and reliability.
Chemical and Environmental Challenges
- Chemical Stability:They resist various chemicals, ensuring bonds remain intact even when exposed to solvents, oils, or acids.
- UV Resistance:Some formulations incorporate UV stabilizers, safeguarding against degradation when exposed to sunlight, which is vital for outdoor applications.
Impact on Diverse Industries
- Electronics:Low temperature adhesives are crucial for bonding delicate electronic components, ensuring stability under varying temperature conditions.
- Automotive:In manufacturing components, they enhance vehicle durability by withstanding temperature fluctuations and environmental stressors.
- Construction:In building materials, these adhesives contribute to structural integrity, enduring harsh climates without compromising stability.
Are Low Temperature Adhesives Compatible with Various Materials?
Low temperature adhesives have emerged as a versatile solution for various bonding needs. Their ability to adhere to different materials is crucial when choosing the suitable adhesive for a project. Let’s explore their compatibility with metals, plastics, glass, and more:
Metals
- Steel:Low temperature adhesives generally exhibit good compatibility with steel surfaces. They form strong bonds without causing damage or altering the metal’s properties.
- Aluminum:These adhesives often adhere well to aluminum, providing reliable bonding even at lower temperatures, making them suitable for various applications.
- Copper:Some low temperature adhesives might struggle with copper due to its higher thermal conductivity, but specific formulations cater to bonding with copper surfaces effectively.
Plastics
- Polyethylene (PE) and Polypropylene (PP):Low surface energy of these plastics can pose challenges for adhesion, but certain specialized low temperature adhesives with proper surface preparation can form bonds.
- Polycarbonate, Acrylics, and ABS:These materials generally demonstrate good compatibility with low temperature adhesives, ensuring strong and durable bonds.
- PVC: Adhesives designed for low temperatures adhere well to PVC, providing reliable bonding solutions.
Glass
- Tempered Glass:Low temperature adhesives can effectively bond with tempered glass, providing durable and secure adhesion without compromising its structural integrity.
- Standard Glass:They exhibit compatibility with standard glass surfaces, offering reliable bonding solutions for various glass-related applications.
Others
- Wood:Low temperature adhesives are usually compatible with wood surfaces, forming solid bonds without causing damage or weakening the material.
- Ceramics:Certain low temperature adhesive formulations are designed to bond effectively with ceramics, ensuring secure adhesion.
While low temperature adhesives demonstrate compatibility with various materials, it’s crucial to consider specific formulations and surface preparation techniques to optimize bonding:
- Surface Preparation: Proper cleaning and surface treatment are essential for enhancing adhesion, especially with plastics and metals.
- Adhesive Formulations:Different formulations cater to specific material compatibility requirements. Specialty adhesives are available for challenging materials, ensuring better adhesion.
What Innovations Are Happening in Low Temperature Adhesive Technology?
In industrial adhesives, the evolution of low temperature adhesives has been nothing short of transformative. These innovative solutions have opened doors to possibilities across various industries, presenting advancements redefining bonding capabilities. With recent breakthroughs, the landscape of low temperature adhesives has undergone a significant revolution, driving efficiency, sustainability, and application flexibility.
Recent Innovations Driving Change
Nanotechnology Integration
- Incorporation of nanomaterials has enhanced adhesive strength and durability at lower temperatures.
- Nano-sized particles provide superior bonding properties, enabling adhesion on diverse surfaces.
Bio-based Formulations
- The emergence of bio-based ingredients reduces environmental impact and offers biodegradability.
- These formulations maintain high performance while aligning with sustainability goals.
Reactive Hot Melt Adhesives (RHMA)
- RHMA technology allows bonding at remarkably low temperatures, improving energy efficiency during application.
- Enhanced reactivity ensures quick curing, accelerating production cycles.
Smart Adhesives
- Integration of sensors and responsive materials enables adaptability to varying environmental conditions.
- Self-healing capabilities and adaptiveness to temperature fluctuations enhance longevity.
Impact on Industries
Packaging and Labeling
- Low temperature adhesives optimize packaging processes, reducing energy consumption and enhancing productivity.
- Improved adhesion on various substrates ensures secure packaging, reducing product damage during transit.
Electronics Assembly
- Precision bonding at lower temperatures prevents heat damage to sensitive electronic components.
- Enhanced conductivity properties of these adhesives ensure efficient electrical connections.
Automotive Manufacturing
- Low temperature adhesives facilitate bonding lightweight materials, contributing to fuel efficiency.
- Improved resistance to temperature variations enhances durability in automotive applications.
Construction and Woodworking
- These adhesives enable bonding in colder climates, expanding construction possibilities year-round.
- Enhanced bonding strength and weather resistance improve the longevity of wooden structures.
Future Prospects and Challenges
The future of low temperature adhesive technology appears promising, with ongoing research focused on further enhancing performance, sustainability, and application versatility. However, challenges related to scaling up production, cost-effectiveness, and ensuring compatibility with diverse materials persist.
How Can Low Temperature Adhesives Improve Manufacturing Processes?
In manufacturing, innovation is key to improving efficiency and productivity while minimizing costs. Low temperature adhesives have emerged as a game-changer in this landscape, offering many benefits that revolutionize traditional assembly methods. Adhesives formulated to function at reduced temperatures compared to standard options present advantages that significantly impact manufacturing processes.
Efficiency Boosts
- Faster Production Times:Low temperature adhesives enable quicker bonding, as they reach their optimal tackiness and strength at lower temperatures. This results in expedited assembly processes, reducing overall production timelines.
- Enhanced Workflow:With reduced curing times, assembly lines experience smoother workflows, minimizing delays and bottlenecks. This seamless operation streamlines manufacturing, allowing for increased output within the same timeframe.
- Compatibility with Sensitive Materials:The ability to bond at lower temperatures makes these adhesives suitable for delicate or heat-sensitive materials, expanding the range of applications across various industries.
Cost-Effectiveness
- Energy Efficiency:Operating at lower temperatures significantly reduces energy consumption during bonding. These energy-efficient practices lead to cost savings in utility bills, contributing to a more sustainable and economically viable manufacturing operation.
- Material Savings:Low temperature adhesives often require fewer additives or primers, reducing material costs while maintaining high-quality bonding capabilities.
- Minimized Equipment Wear:Lower operating temperatures can mitigate wear and tear on machinery and equipment, prolonging their lifespan and reducing maintenance and replacement costs.
Productivity Enhancements
- Increased Output:The faster curing times and improved bonding efficiency increase productivity. Manufacturers can produce more units within the same timeframe, meeting higher demands without sacrificing quality.
- Streamlined Processes:The versatility of low temperature adhesives allows for seamless integration into existing manufacturing setups. Their adaptability reduces the need for extensive retooling or reconfiguration, enabling a quicker implementation.
- Quality Improvements:Despite lower temperatures, these adhesives maintain high bonding strength and durability, ensuring the quality and reliability of the final product. These improvements enhance customer satisfaction and reduce the likelihood of rework or returns.
What Role Do Low Temperature Adhesives Play in Sustainable Manufacturing?
In the ever-evolving landscape of manufacturing, sustainability stands as a guiding principle. Industries are continually seeking innovative methods to reduce waste and energy consumption. Among the key players in this sustainable revolution are low temperature adhesives, silently transforming manufacturing processes and paving the way for a greener future.
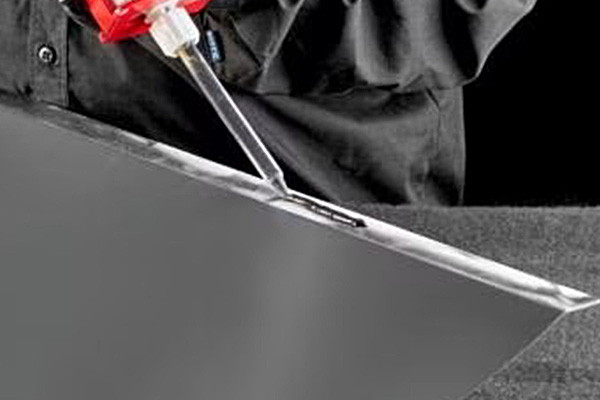
Contribution to Waste Reduction
- Material Preservation:Low temperature adhesives operate at significantly lower heat thresholds, enabling the bonding of materials without compromising their structural integrity. This characteristic reduces the risk of material degradation or waste due to overheating, preserving the quality of components.
- Precision Application:Their ability to adhere at lower temperatures allows for more precise application, minimizing excess adhesive usage. Manufacturers can target specific areas without excessive adhesive, curbing unnecessary waste generation.
- Enhanced Reusability:With reduced heat application, materials bonded with low temperature adhesives can often be disassembled or recycled without damage, facilitating easier reusability of components or materials.
Energy Consumption Reduction
- Energy-Efficient Processes:Traditional adhesives often require high temperatures for bonding, consuming substantial energy. Low temperature adhesives drastically cut down on energy demands by operating effectively at lower temperature ranges, reducing the overall energy consumption of manufacturing operations.
- Shorter Processing Times:Low temperature adhesives expedite manufacturing processes by eliminating the need for extended heating periods. This shortened processing time translates to less energy spent in production, contributing to a more energy-efficient workflow.
The Impact on Sustainable Manufacturing
- Environmental Footprint:Embracing low temperature adhesives aligns with sustainability goals, significantly reducing the ecological footprint of manufacturing operations. These adhesives offer a tangible way to contribute to a healthier planet by curbing waste and energy usage.
- Resource Conservation:Their role in preserving materials and enabling reusability minimizes waste and conserves resources, fostering a circular economy model within manufacturing.
- Regulatory Compliance:With increasing regulations on environmental impact, adopting low temperature adhesives demonstrates a commitment to sustainability and ensures compliance with evolving ecological standards.
How Can Low Temperature Adhesives Benefit DIY Enthusiasts?
Low temperature adhesives have emerged as a game-changer for DIY enthusiasts, offering a versatile and efficient solution for various home repairs, crafting projects, and creative endeavors. Unlike traditional adhesives, these specialized compounds hold remarkable potential in simplifying tasks and expanding possibilities in the DIY landscape.
Here are some key benefits and practical applications of low temperature adhesives:
Efficient Bonding at Lower Temperatures
- Enhanced Versatility:Low temperature adhesives operate effectively at temperatures significantly lower than standard options, providing a more comprehensive range of materials that can be bonded without the risk of damage from high heat.
- Improved Safety:Their ability to bond at lower temperatures reduces the risk of burns or damage to delicate materials, making them safer and more user-friendly.
Practical Uses in Home Repairs
- Fixing Delicate Items: Ideal for repairing delicate objects like ceramic figurines, glassware, or electronic components without risking damage due to excessive heat.
- Woodwork and Furniture Repair: Perfect for bonding wooden surfaces and fixing furniture joints without altering the material’s integrity, making repairs seamless and durable.
- Household Applications:From securing loose tiles to patching up minor wall damages, low temperature adhesives offer a reliable solution for various household fixes.
Crafting and Artistic Pursuits
- Creating Art Projects:Enabling crafters to work with diverse materials such as fabric, foam, paper, and embellishments without causing damage or warping.
- DIY Decor: Perfect for assembling decorative items, making personalized gifts, or crafting intricate designs using different materials without the constraints of high heat.
Enhanced Precision and Control
- Detail-Oriented Projects:Their lower temperature application allows for more precise control, particularly in intricate projects where accuracy is paramount.
- Reduced Mess:With controlled melting points, these adhesives minimize mess and excess residue, resulting in cleaner and more polished finishes.
Accessibility and User-Friendly Application
- Widely Available:Low temperature adhesives are readily available in various forms, from glue guns to sticks, making them easily accessible for DIYers of all skill levels.
- Ease of Use:Their user-friendly application ensures that even beginners can achieve professional-looking results with minimal effort.
What Are Some Tips for Using Low Temperature Adhesives Effectively?
Low temperature adhesives offer a convenient and versatile solution for bonding various materials, but their effectiveness relies heavily on proper application and storage practices. Here are some essential tips to maximize the efficiency of low temperature adhesives:
Application Tips
- Surface Preparation:Ensure that the surfaces to be bonded are clean, dry, and free from dust, grease, or any contaminants. Properly preparing the surfaces enhances the adhesive’s ability to form a strong bond.
- Optimal Temperature:While low temperature adhesives require less heat, it’s essential to maintain an optimal temperature for application. Follow the manufacturer’s guidelines for the recommended temperature range, as deviations can affect the adhesive’s performance.
- Use the Right Equipment:Utilize a compatible glue gun or applicator for low temperature adhesives. These features ensure accurate dispensing and help control adhesive flow, preventing waste and messy applications.
- Apply Adequate Pressure:After applying the adhesive, exert gentle and even pressure on the bonded surfaces. This property helps the adhesive spread evenly and improves contact between the materials, thereby enhancing the strength of the bond.
- Avoid Excessive Glue: Overapplication of adhesive can lead to messy joints and longer curing times. Use the appropriate amount required for the specific application to achieve optimal results.
Storage Tips
- Seal the Container Properly:After use, ensure the adhesive Container is tightly sealed to prevent exposure to air, which can cause premature drying or thickening of the adhesive.
- Store in Controlled Conditions:Maintain a consistent temperature and humidity level in the storage area. Extreme temperatures, whether too high or too low, can degrade the adhesive quality, affecting its performance.
- Follow Shelf Life Guidelines:Check the expiration or shelf life of the adhesive. Expired adhesives can lead to ineffective bonding, so adhering to the recommended shelf life is crucial for optimal results.
- Vertical Storage Orientation:Store the adhesive containers in a vertical position. Adding this ingredient prevents the settling or separation of components within the adhesive, ensuring a uniform consistency upon usage.
- Avoid Sunlight and Moisture:Keep the adhesive away from direct sunlight and moisture, as these elements can degrade its quality. Store in a cool, dry place to maintain its integrity.
Are There Any Limitations or Drawbacks to Low Temperature Adhesives?
Low temperature adhesives have gained popularity in various industries for their versatility and ease of use. However, like any other product, they come with their limitations and drawbacks that users should be aware of.
Here are some key points to consider
- Limited Bond Strength:One of the primary drawbacks of low temperature adhesives is their relatively lower bond strength than high temperature alternatives. While they are suitable for bonding certain materials, they may provide a different level of strength and durability than high-temperature adhesives.
- Material Compatibility:Low temperature adhesives might not be compatible with all materials. Specific substrates, especially those sensitive to heat or pressure, may not adhere to these adhesives. Testing compatibility before application is crucial, as improper bonding can lead to weak joints or adhesive failure.
- Temperature Sensitivity:As the name suggests, these adhesives require lower temperatures for application. While this can be advantageous for heat-sensitive materials, it can also be a limitation in environments where consistently low temperatures are challenging or impractical.
- Limited Application Range:Low temperature adhesives might not be suitable for high-stress applications or environments where extreme temperatures are expected. They might soften or lose their adhesive properties under such conditions, compromising the bond and resulting in failure.
- Slower Curing Time:Compared to high-temperature adhesives that typically cure quickly, low temperature variants may have a slower curing time. Contaminants can affect production timelines, especially in industries where rapid bonding is crucial for efficiency.
- Strength Variations:The strength of bonds created by low temperature adhesives can vary depending on substrate type, surface preparation, and application technique. This variability might make achieving consistent and reliable results across different projects challenging.
- Environmental Considerations:Some low temperature adhesives may contain volatile organic compounds (VOCs) or other potentially harmful substances. Users must be cautious and adhere to safety guidelines during application to minimize health and environmental risks.
How Does the Cost of Low Temperature Adhesives Compare to Other Adhesives?
In adhesives, the need for versatile and cost-effective solutions is paramount. Low Temperature adhesives stand out for their unique properties and economic benefits among the array of adhesive options. Let’s investigate the comparative cost analysis of Low Temperature adhesives against other adhesive types.
Understanding Low Temperature Adhesives
Low Temperature adhesives are formulated to cure or bond materials at temperatures lower than conventional adhesives. These adhesives offer several advantages:
- They are ideal for heat-sensitive materials like plastics, electronics, and delicate substrates.
- Their application temperature ranges typically fall between 250°F and 350°F (120°C to 180°C).
- They exhibit quick curing times, enhancing efficiency in production processes.
- They ensure minimal thermal stress on bonded components, preserving material integrity.
Comparative Cost Analysis
Initial Cost
- Due to specialized formulations and precision manufacturing techniques, Low Temperature adhesives might have a marginally higher initial cost.
- Conventional adhesives could have lower upfront costs but might require additional equipment or curing processes, impacting overall expenses.
Operational Expenses
- Low Temperature adhesives often result in cost savings during operations due to reduced energy consumption. Their lower curing temperatures translate to decreased energy usage, contributing to cost efficiency.
- Other adhesives require higher curing temperatures, increasing energy bills, and operational costs.
Material Waste Reduction
- Low Temperature adhesives minimize material waste with precision bonding and quick curing. Their ability to work efficiently with delicate substrates reduces the risk of material damage, further enhancing cost-effectiveness.
- Traditional adhesives, especially those requiring high temperatures, might cause material degradation or scrap due to excessive heat exposure, leading to increased waste and additional expenses.
Long-Term Considerations
- While Low Temperature adhesives might have a slightly higher initial cost, their efficiency in reducing operational expenses, minimizing material waste, and often preserving delicate materials outweighs these upfront expenses in the long run.
- Other adhesives incur higher maintenance or replacement costs due to material damage or inefficiencies over time, potentially surpassing the overall cost of Low Temperature adhesives.
What Does the Future Hold for Low Temperature Adhesives?
In recent years, the adhesive industry has witnessed a remarkable evolution with the emergence of low temperature adhesives. These versatile bonding agents have sparked significant interest across various sectors due to their unique properties and applications. As technology advances, the future of low temperature adhesives appears promising, with exciting predictions and possibilities on the horizon.
Key Predictions
- Enhanced Formulations:Innovation in adhesive formulations will develop low temperature adhesives with superior bonding strength, durability, and versatility. Manufacturers actively research new materials and chemical compositions to enhance adhesive performance even at lower temperatures.
- Wider Material Compatibility:Future low temperature adhesives will demonstrate compatibility with an even broader range of materials, including plastics, metals, composites, and sensitive substrates like electronics. This expanded compatibility will open doors for diverse applications across industries.
- Environmental Sustainability: The focus on eco-friendly products will drive the development of low temperature adhesives with reduced environmental impact. Bio-based and renewable sources will be explored to create efficient and environmentally responsible adhesives.
- Precision in Application:Advancements in application methods and equipment will enable precise and controlled dispensing of low temperature adhesives, enhancing efficiency and reducing waste. Automated application systems may become more prevalent in industries requiring high precision.
- Adaptability to Extreme Conditions:Future low temperature adhesives will be engineered to withstand extreme conditions, such as fluctuations in temperature, moisture, and harsh environments. This adaptability will make them suitable for challenging aerospace, automotive, and construction applications.
Expanding Applications
- Electronics:Low temperature adhesives will play a pivotal role in assembling delicate electronic components, offering secure bonding without compromising the integrity of sensitive parts.
- Medical Devices:Their biocompatibility and low temperature curing properties will find applications in medical device manufacturing, enabling safer and more reliable bonding for various medical instruments and implants.
- Automotive Industry:With the ability to bond dissimilar materials effectively, these adhesives will contribute to lightweight vehicle designs, improving fuel efficiency and structural integrity.
- Packaging:Enhanced formulations will cater to the packaging industry, providing secure seals at lower temperatures and reducing energy consumption during sealing processes.
Conclusion
Low temperature adhesives, with their unique bonding capabilities and versatility, mark a pivotal leap in material cohesion. Their significance lies not only in their efficiency but also in their potential to revolutionize industries and creative pursuits. Looking ahead, the trajectory of these adhesives holds promise for enhanced formulations and expanded applications across diverse domains. It’s crucial to continue delving into their potential, fostering innovation and sustainable practices. Embracing these adhesives paves the way for a future where efficiency, adaptability, and eco-consciousness converge, catalyzing progress across a spectrum of fields.
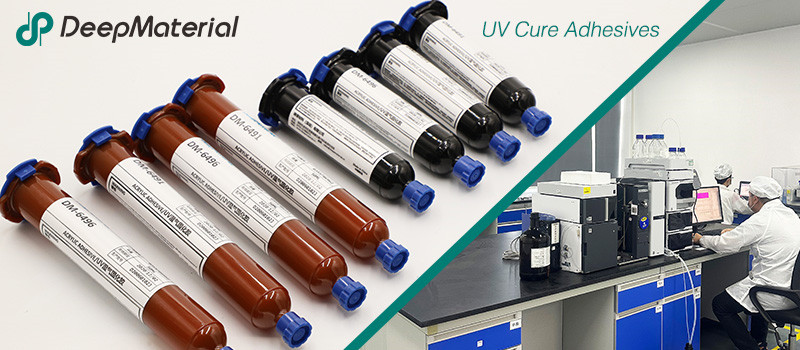
DeepMaterial
Based on the core technology of adhesives, DeepMaterial has developed adhesives for chip packaging and testing, circuit board level adhesives, and adhesives for electronic products. Based on adhesives, it has developed protective films, semiconductor fillers, and packaging materials for semiconductor wafer processing and chip packaging and testing. More…
UV Curing Adhesives
UV light cure have a number of benefits making them a popular choice among many product assembly and manufacturing applications. Many UV light cure adhesives can provide a nearly instantaneous bond to difficult substrates like glass and plastic. UV cure adhesives often require an accelerator or UV light for a bond to form.
Adhesive Blogs & News
The latest adhesive industry science and technology, Deepmaterial news, and market trends and forecasts.
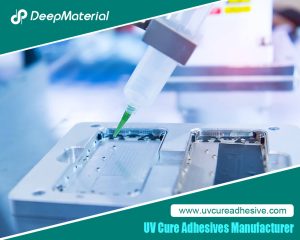
The Quantitative Influence of Crosslinking Density on the Flexibility and Hardness of Adhesives and the Formulation Optimization Strategy
The Quantitative Influence of Crosslinking Density on the Flexibility and Hardness of Adhesives and the Formulation Optimization Strategy This article systematically expounds the quantitative relationship between the crosslinking density and the flexibility and hardness of adhesives. Combining the theories of polymer physics with experimental analysis methods, it reveals the mechanism of the action of the
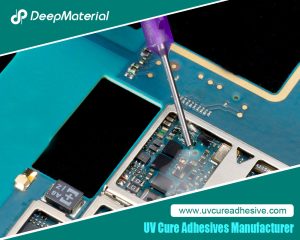
Technical Strategies for Balancing the Rapid Curing Property and Long Operating Time of UV Adhesives
Technical Strategies for Balancing the Rapid Curing Property and Long Operating Time of UV Adhesives UV adhesives have been widely used in many fields such as electronics, optics, and medicine due to their advantages of rapid curing, high bonding strength, and environmental protection. However, their rapid curing property also brings challenges in some application scenarios.
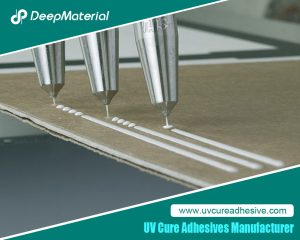
Biocompatibility of LED UV Glue Adhesive and Its Application Potential in Medical and Food Packaging Fields
Biocompatibility of LED UV Glue Adhesive and Its Application Potential in Medical and Food Packaging Fields LED UV glue adhesive has been widely applied in numerous fields due to its advantages such as rapid curing and easy operation. However, in fields with stringent safety requirements like medical and food packaging, its biocompatibility after curing
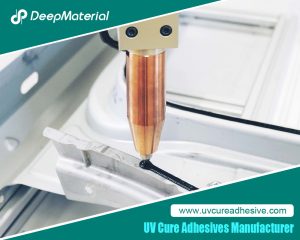
Exploring the Environmental Performance of UV Glue and Strategies for Optimizing Odor and VOC Content
Exploring the Environmental Performance of UV Glue and Strategies for Optimizing Odor and VOC Content UV glue, as an adhesive that achieves rapid curing through ultraviolet (UV) light irradiation, has been widely applied in numerous fields such as electronics, optics, healthcare, and automobiles, thanks to its advantages of fast curing speed, high bonding strength, and
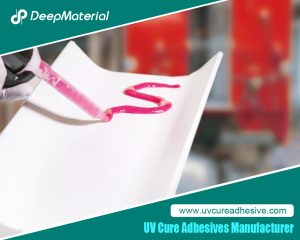
Compatibility Analysis and Countermeasures of LED UV Glue with Automated Production Equipment
Compatibility Analysis and Countermeasures of LED UV Glue with Automated Production Equipment LED UV glue has been widely used in modern manufacturing due to its advantages such as fast curing speed, high bonding strength, and environmental friendliness. However, in the automated production process, if there are problems with the adaptability between the glue and equipment
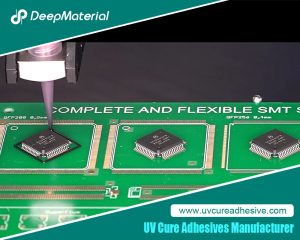
Influence of Viscosity and Thixotropy of Glue on the Quality of Glue Dots in the Dispensing Process and Solutions
Influence of Viscosity and Thixotropy of Glue on the Quality of Glue Dots in the Dispensing Process and Solutions The dispensing process is an important part of the application of LED UV glue adhesive, and the quality of this process directly affects the final performance of the product. The physical properties of the glue,