- Home
- >
- Material Bonding
- >
- UV Cure Adhesive For Metal
UV Cure Adhesive For Metal
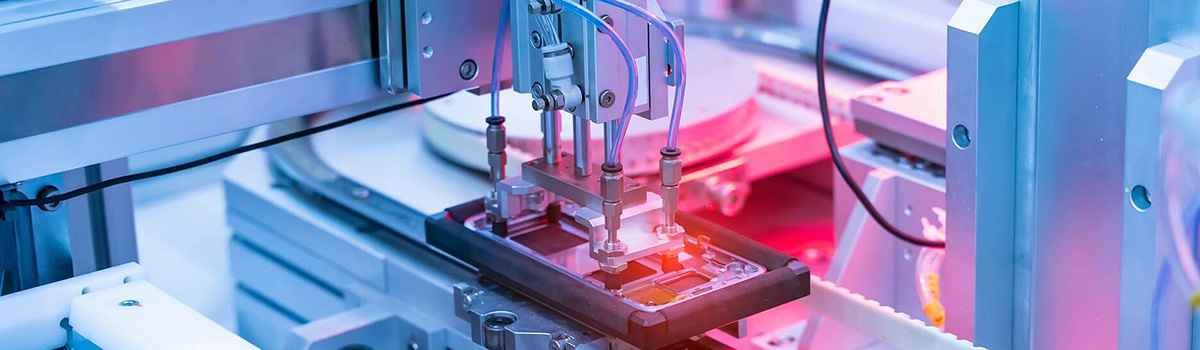
Table of Contents
ToggleWhat are the fundamental characteristics of UV cure adhesives?
UV cure adhesives cure or harden rapidly when exposed to ultraviolet (UV) light. These adhesives offer several advantages, making them popular in various industries. The fundamentals of UV cure adhesives can be summarized as follows:- Chemistry: UV cure adhesives typically consist of oligomers, monomers, photoinitiators, and other additives. When exposed to UV light, the photoinitiators undergo a photochemical reaction, initiating a polymerization process that transforms the liquid adhesive into a solid state.
- Curing Process: The curing process of UV adhesives is speedy, taking only seconds to minutes. This rapid curing time enhances efficiency in manufacturing processes, allowing for shorter production cycles and reduced energy consumption compared to traditional adhesive curing methods.
- Bond Strength: UV cure adhesives provide strong and durable bonds. The cured adhesive often exhibits excellent adhesion to various substrates, including plastics, glass, metals, and ceramics. The resulting bonds are resistant to heat, chemicals, and environmental factors.
- Precision and Control: UV curing offers precise control over the adhesive process. Manufacturers can control the intensity and duration of UV exposure, allowing for customization based on specific application requirements. This level of control contributes to the adhesive’s versatility in different industries.
- Versatility: UV cure adhesives find applications in diverse sectors such as electronics, medical devices, optics, and automotive. They are used for bonding, sealing, coating, and encapsulating components. The versatility stems from the ability to tailor the adhesive formulation to meet specific performance criteria.
- Environmental Considerations: UV cure adhesives are often solvent-free, contributing to a more environmentally friendly option than traditional solvent-based adhesives. The curing process also requires less energy, aligning with sustainability goals.
- UV Light Sources: The curing of adhesives curing relies on sources, typically provided by UV lamps or LED systems. These light sources emit specific wavelengths that match the absorption spectrum of the photoinitiators in the adhesive, ensuring adequate curing.
How does UV light curing work in the context of adhesive applications?
UV light curing is a rapid and efficient process in various industries, particularly in adhesives, coatings, and printing. The working mechanism of UV light curing involves several key steps:- Formulation of UV-Curable Materials: UV-curable materials, such as adhesives, inks, or coatings, are formulated with specific photoinitiators. These photoinitiators are chemical compounds sensitive to UV light and capable of initiating a photochemical reaction.
- Application of UV-Curable Material: The UV-curable material is applied as a liquid or a coating onto the substrate. It remains in a liquid state until exposed to UV light.
- Exposure to UV Light: The substrate coated with the UV-curable material is then exposed to UV light of a particular wavelength. This wavelength corresponds to the absorption spectrum of the photoinitiators within the formulation.
- Photoinitiator Activation: When the UV light interacts with the photoinitiators, they undergo a photochemical reaction, breaking down into reactive species such as free radicals or cations. These reactive species initiate the polymerization process of the monomers and oligomers in the material.
- Polymerization and Curing: The activated monomers and oligomers rapidly polymerize, forming a three-dimensional network of cross-linked polymers. This process is commonly known as curing. The speed of the curing reaction is one of the significant advantages of UV light curing, allowing for almost instantaneous hardening of the material.
- Formation of Solid Material: As the polymerization progresses, the liquid material transforms into a solid state. This solid state is characterized by strong bonds between the molecules, resulting in a durable and often transparent or explicitly cured material.
- Final Product: The cured material is ready for use once the UV light exposure is complete. The cured material typically exhibits desirable properties such as high strength, chemical resistance, and minimal shrinkage.
In what ways do contemporary adhesives excel when compared to traditional bonding techniques?
UV cure adhesives offer several advantages over traditional adhesives, making them popular in various industries. Here are some key advantages: Rapid Cure Time:- One of the most significant advantages of UV cure adhesives is their rapid curing capability. When exposed to ultraviolet (UV) light, these adhesives can cure within seconds, providing fast assembly and production processes. Traditional adhesives often require more healing time, leading to longer production cycles.
- UV cure adhesives allow for precise control over the curing process. Manufacturers can control the intensity and duration of UV light exposure, ensuring that the adhesive cures only when and where needed. This precision is particularly beneficial for intricate or delicate applications.
- UV cure adhesives cure at relatively low temperatures compared to some traditional adhesives. This feature is advantageous for bonding heat-sensitive materials, preventing damage or distortion during bonding.
- UV cure adhesives are often solvent-free, leading to lower levels of volatile organic compounds (VOCs) compared to some traditional adhesives. This can contribute to a healthier, safer working environment and help companies meet environmental regulations.
- UV cure adhesives can provide strong and durable bonds, often with improved adhesion compared to traditional adhesives. This can result in enhanced product performance and reliability.
- UV cure adhesives are versatile and can be formulated for various applications, including bonding, coating, and sealing. They can be tailored to meet specific performance requirements, making them suitable for multiple industries, such as electronics, medical devices, and automotive.
- Since UV-cure adhesives cure quickly and without the need for heat, there is often no need for solvents or other drying processes. This can lead to cleaner and more efficient manufacturing processes, reducing the likelihood of contamination or damage to sensitive components.
- UV cure adhesives can contribute to energy efficiency in manufacturing processes. Their rapid curing minimizes the time required for bonding, resulting in energy savings compared to traditional adhesives that may require longer or higher temperatures.
- The fast curing time of UV cure adhesives can lead to increased productivity in manufacturing processes. Speedier assembly and shorter cycle times contribute to higher throughput and overall efficiency.
What factors determine the compatibility of specific metals with UV cure adhesive applications?
UV cure adhesives are versatile and can be used with various materials, including certain metals. The compatibility of UV cure adhesives with metals depends on factors such as the composition of the adhesive, the specific type of metal, and the intended application. Here are some common kinds of metals that are generally compatible with UV cure adhesives: Aluminum:- UV cure adhesives can bond well with aluminum, making them suitable for automotive, aerospace, and electronics applications.
- Stainless steel is often compatible with UV-cure adhesives. These adhesives can be used for bonding stainless steel components in various applications.
- UV cure adhesives can bond effectively with copper, essential in electronic applications where copper components are prevalent.
- Like copper, brass is generally compatible with UV cure adhesives, allowing for bonding in applications with brass components.
- UV cure adhesives can be used with titanium, providing a fast and efficient bonding solution for applications in aerospace, medical devices, and other industries.
- Certain UV cure adhesives are formulated to bond with nickel surfaces, making them suitable for applications where nickel-plated components are involved.
- UV cure adhesives can be used with zinc-coated or galvanized surfaces, making them applicable in various industries, including construction and automotive.
- Many UV-cure adhesives are compatible with ferrous metals, such as carbon steel. These adhesives can be used for bonding and assembly in industries like manufacturing and construction.
Can you provide insights into any notable advancements or innovations related to the use of UV cure adhesives in the aerospace industry?
UV cure adhesives find various applications in the aerospace industry due to their unique properties, such as fast curing, precise control, and compatibility with different materials. Here are some specific applications of UV cure adhesives in the aerospace sector: Bonding Components:- UV cure adhesives are used for bonding components in the assembly of aircraft structures. They provide fast curing times, allowing for efficient production processes. The precise control over the curing process is crucial in ensuring strong and reliable bonds.
- In aerospace, composite materials are commonly used to create lightweight and high-strength structures. UV cure adhesives are employed in bonding composite materials, helping to assemble and reinforce components in aircraft parts manufacturing.
- UV cure adhesives are suitable for bonding electronic components and avionic systems in aircraft. The fast curing time is advantageous in producing electronic assemblies, and the adhesives can connect well with materials commonly found in electronics, such as metals and plastics.
- UV cure adhesives are used in the assembly of lighting systems for aircraft. They can bond light guides, lenses, and other components with precision, contributing to the overall reliability and performance of the lighting systems.
- UV cure adhesives are applied in the interior assembly of aircraft cabins. They can be used for bonding materials like plastics, metals, and composites to construct seating, panels, and other internal components.
- UV cure adhesives are used for rapid repairs and maintenance tasks in the aerospace industry. The ability to quickly cure the adhesive with UV light allows for expedited maintenance, minimizing downtime for aircraft.
- UV cure adhesives are employed in sealing and gasketing applications, helping to create airtight and watertight seals in critical areas of an airplane. This is important for maintaining the structural integrity and performance of aerospace components.
- UV cure adhesives are used to bond sensors and instrumentation systems on aircraft. The precise curing control ensures that sensitive electronic components are not subjected to excessive heat during bonding.
- Aerospace manufacturers continually seek ways to reduce aircraft weight to improve fuel efficiency. UV cure adhesives, lightweight and offering strong bonds, contribute to these weight-reduction efforts when used as alternatives to traditional mechanical fasteners.
- UV cure adhesives are employed in laminating panels and bonding various aircraft components. Their fast cure times enhance the efficiency of the manufacturing process.
How do quick-curing adhesives impact cycle times in production lines?
The quick curing properties of UV cure adhesives contribute significantly to enhanced productivity in various industries. Here are several ways in which quick-curing UV cure adhesives can improve productivity:
Shorter Processing Times:
UV cure adhesives cure rapidly when exposed to ultraviolet light, often within seconds. This quick curing time reduces the overall processing time in manufacturing and assembly operations. As a result, production cycles are shortened, leading to increased throughput.
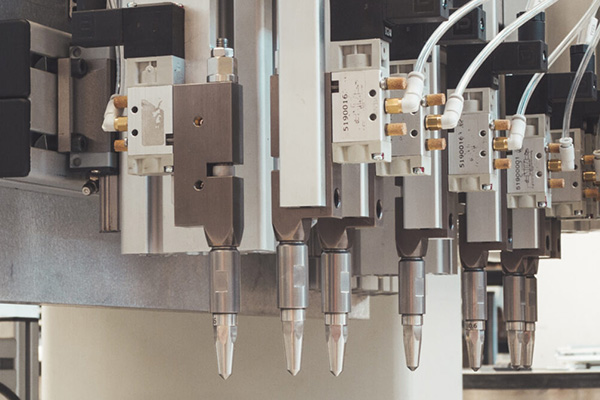
Faster Assembly Line Speeds:
The fast curing of UV adhesives allows for higher assembly line speeds. Manufacturers can move materials and components along the production line faster, leading to a higher volume of finished products within a given time frame.
Reduced Work-in-Progress Inventory:
Quick-curing UV adhesives enable manufacturers to minimize work-in-progress inventory. Components can move swiftly through the production process with shorter curing times, reducing the need for extensive intermediate storage of partially assembled materials.
Immediate Quality Control and Inspection:
The rapid cure time of UV adhesives allows for immediate quality control and inspection after the bonding process. This quick feedback loop enables manufacturers to promptly identify and address defects or issues, preventing the production of defective or substandard products.
Energy Efficiency:
Traditional adhesives may require elevated temperatures for curing, consuming more energy. UV cure adhesives cure at room temperature, eliminating the need for additional heat sources. This energy-efficient curing process contributes to cost savings and environmental sustainability.
Increased Equipment Utilization:
Quick-curing adhesives allow for increased utilization of bonding and assembly equipment. The fast cure times mean that equipment is kept from being tied up for extended periods, making it available in other production processes.
On-Demand Bonding:
UV cure adhesives provide on-demand bonding, allowing manufacturers to apply adhesive precisely when needed. This eliminates the need for adhesives to cure slowly, enabling a more flexible and responsive production schedule.
Just-In-Time Manufacturing:
Quick-curing UV adhesives align well with just-in-time manufacturing principles. Manufacturers can apply adhesives at the last moment in production, reducing the need for extensive inventories and optimizing resource utilization.
Improved Overall Equipment Efficiency (OEE):
With faster curing times and reduced downtime, manufacturing equipment’s overall efficiency (OEE) is improved. This metric considers availability, performance, and quality factors, and quick-curing adhesives positively impact these aspects.
Streamlined Prototyping and R&D:
In research and development (R&D) settings or during prototyping, quick-curing UV adhesives allow for rapid iteration and testing. This agility is valuable for product development, enabling engineers and designers to assess and modify designs quickly.
What is the impact of UV cure adhesives on traditional manufacturing processes?
The use of UV cure adhesives has a significant impact on manufacturing processes across various industries. The unique properties of UV cure adhesives influence efficiency, flexibility, and overall performance. Here are some critical implications on manufacturing processes:
Speed and Efficiency:
- The rapid curing time of UV cure adhesives significantly speeds up manufacturing processes. This allows for faster production cycles, increased throughput, and shorter lead times. Manufacturers can achieve higher levels of efficiency and produce more units in a given timeframe.
Reduced Downtime:
- Quick curing enables reduced downtime in manufacturing processes. As UV adhesives cure almost instantly when exposed to UV light, there is minimal waiting time for components to bond. This leads to more continuous and streamlined production.
Energy Savings:
- UV cure adhesives often cure at room temperature, eliminating the need for high-temperature curing processes. This results in energy savings compared to traditional adhesives that may require elevated temperatures for curing. The overall manufacturing process becomes more energy-efficient.
Improved Quality Control:
- Quick curing allows for immediate quality control and inspection of bonded components. Manufacturers can identify defects or issues promptly, reducing the likelihood of producing defective products. This contributes to higher overall product quality and customer satisfaction.
Enhanced Product Design Flexibility:
- The fast curing time of UV adhesives offers greater flexibility in product design and assembly. Manufacturers can explore innovative designs and adjust assembly processes with the assurance that the adhesive will cure rapidly, allowing for quick prototyping and iteration.
Reduced Work-in-Progress Inventory:
- With short curing times, there is less need for extensive work-in-progress inventory. Components can move swiftly through manufacturing, reducing the amount of partially assembled materials stored between production stages.
Precision and Consistency:
- UV cure adhesives offer precise control over the curing process. Manufacturers can apply the adhesive exactly where needed and cure it with precision. This leads to consistent and reliable bonds, which are crucial for manufacturing high-quality products.
Just-In-Time Manufacturing:
- Quick-curing adhesives align well with just-in-time manufacturing principles. Manufacturers can apply adhesives at the last moment, reducing the need for extensive inventories and optimizing resource utilization.
Clean and Environmentally Friendly:
- UV cure adhesives are often solvent-free, reducing the emission of volatile organic compounds (VOCs). This contributes to a more hygienic and environmentally friendly manufacturing process, aligning with sustainability goals.
Diverse Applications:
- UV cure adhesives are versatile and can be used in various applications, from bonding and sealing to coating and encapsulation. Their ability to adhere to different materials makes them suitable for multiple manufacturing processes across electronics, automotive, aerospace, and medical devices.
It’s important to note that while UV cure adhesives offer numerous benefits, their suitability depends on the specific requirements of the application and the materials involved. Manufacturers should conduct compatibility tests and consider factors such as the adhesive’s formulation, curing equipment, and environmental conditions to optimize their impact on manufacturing processes.
How does the ability to customize UV cure adhesive formulations contribute to the overall versatility and adaptability of the adhesive in different industries?
UV cure adhesives are highly versatile, and manufacturers often provide customization options and formulation variations to meet specific application requirements. Here are some aspects of customization and formulation variations in UV cure adhesives:
Chemical Formulation:
UV cure adhesives can be formulated with different chemical compositions to achieve specific performance characteristics. Variations in the monomers, oligomers, and photoinitiators used in the formulation can impact factors such as flexibility, adhesion strength, and chemical resistance.
Curing Speed:
Formulations can be adjusted to achieve different curing speeds. Some applications may require extremely fast curing times, while others may benefit from a slower, more controlled curing process. Manufacturers can tailor formulations to meet these specific speed requirements.
Viscosity and Rheology:
The viscosity and rheological properties of UV cure adhesives can be customized to suit the application method and the materials being bonded. This includes variations in thixotropy, shear thinning, and flow characteristics to ensure proper wetting and coverage.
Adhesion to Specific Substrates:
UV cure adhesives can be formulated to enhance adhesion to specific substrates such as metals, plastics, glass, or composites. Formulation variations can be made to improve bonding on challenging surfaces and ensure compatibility with diverse materials.
Flexibility and Toughness:
The flexibility and toughness of cured UV adhesives can be adjusted through formulation modifications. This is particularly important in applications where the bonded components may experience mechanical stress, temperature fluctuations, or other environmental factors.
Optical Clarity and Color:
For applications where optical clarity is crucial, such as in optical bonding or display assembly, UV cure adhesives can be formulated to provide transparent and colorless bonds. Alternatively, formulations with specific colors may be used for aesthetic purposes or to match the appearance of the substrates.
Temperature Resistance:
Some applications require UV cure adhesives to withstand elevated temperatures. Formulation variations can enhance the temperature resistance of the cured adhesive, making it suitable for use in environments with higher operating temperatures.
Low Outgassing:
In aerospace and electronics applications, where outgassing can be a concern, UV cure adhesives can be formulated with low outgassing properties. This is important in preventing contamination of sensitive components and optics.
Low Shrinkage:
UV cure adhesives may be formulated to exhibit low shrinkage during the curing process. Low shrinkage is desirable in applications where dimensional stability is critical, preventing distortion or stress on bonded components.
Specialized Applications:
Manufacturers may develop specialized formulations for specific applications, such as medical-grade adhesives for healthcare applications, or adhesives with high chemical resistance for harsh chemical environments.
Environmental Considerations:
Formulation variations may also take into account environmental considerations, such as the use of solvent-free formulations to reduce volatile organic compound (VOC) emissions.
Before selecting a UV cure adhesive, it’s crucial to consult with the adhesive manufacturer to discuss specific application requirements and to conduct compatibility and performance testing. This ensures that the chosen formulation meets the desired criteria for a particular use case. Customization options provide industries with the flexibility to tailor UV cure adhesives to their unique needs, contributing to improved performance and overall efficiency.
Are there instances where UV cure adhesives have been successfully used in applications with extreme conditions, and what were the outcomes?
The durability of UV-cure adhesives in harsh environmental conditions is crucial for ensuring long-term performance and reliability in various applications. UV cure adhesives can be formulated to exhibit resilience in challenging environments, and several factors contribute to their ability to withstand harsh conditions:
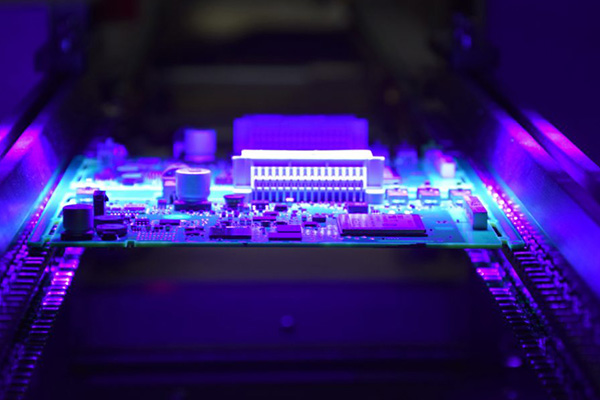
Chemical Resistance:
- UV cure adhesives can be developed to resist exposure to harsh chemicals, solvents, and corrosive substances. This is particularly important in applications where the adhesive may contact aggressive fluids or chemicals.
Temperature Resistance:
- Formulations can be tailored to provide enhanced temperature resistance, allowing the adhesive to maintain its integrity and bonding strength across various temperatures. This is crucial in applications where the bonded components may experience temperature fluctuations.
UV and Weather Resistance:
- UV cure adhesives are inherently resistant to UV radiation. However, additional formulation adjustments can be made to enhance their resistance to prolonged exposure to sunlight and outdoor weather conditions. This is important in applications such as outdoor signage or automotive components.
Moisture and Humidity Resistance:
- Some UV-cure adhesives can be formulated to resist the effects of moisture and humidity. This is particularly relevant in applications where the adhesive may be exposed to damp environments, preventing degradation over time.
Vibration and Shock Resistance:
- For applications where bonded components are subjected to vibration or mechanical shock, UV cure adhesives can be formulated to provide high levels of impact resistance. This helps prevent adhesive failure in dynamic environments.
Flexibility and Toughness:
- Formulation variations can enhance the flexibility and toughness of cured UV adhesives. This is beneficial in applications where the bonded materials may flex or move, preventing the adhesive from becoming brittle and prone to cracking.
Low Outgassing:
- In aerospace and electronics applications, where outgassing can be problematic, UV cure adhesives can be formulated with common outgassing properties to prevent contamination of sensitive components and optics.
Substrate Compatibility:
- UV cure adhesives can be designed to provide excellent adhesion to a wide range of substrates, including metals, plastics, glass, and composites. Ensuring compatibility with the specific materials in the application is crucial for long-term durability.
Abrasion Resistance:
- Some formulations can be optimized to resist abrasion and wear, making them suitable for applications where the bonded components may be subjected to friction or contact with abrasive materials.
Thermal Cycling Stability:
- UV cure adhesives can be formulated to withstand repeated thermal cycling without experiencing significant degradation. This is important in applications where the temperature varies over time.
It’s essential to work closely with adhesive manufacturers to select or customize a UV cure adhesive formulation that meets the specific environmental challenges of the intended application. Additionally, conducting thorough testing, including accelerated aging tests and exposure to simulated environmental conditions, can help ensure that the adhesive will perform reliably over an extended period in harsh environments.
How does the precision of UV cure adhesives support the miniaturization trend in electronic and medical device manufacturing?
UV cure adhesives offer exceptional precision in microjoining applications, making them well-suited for bonding small and delicate components in various industries. Here are ways in which UV cure adhesives provide precision in micro-joining applications:
Fast Curing Time:
- UV cure adhesives cure rapidly when exposed to ultraviolet light. The curing process typically takes a few seconds, allowing for quick and precise bonding of micro-sized components. This is crucial in microjoining applications where speed and precision are essential.
Controlled Application:
- UV cure adhesives can be applied with a high degree of precision. Dispensing systems, including automated dispensers or robotic systems, can use the adhesive precisely to the micro components. This controlled application ensures the adhesive is deposited only where needed, minimizing excess and waste.
Micrometer-Scale Thickness:
- UV cure adhesives can be formulated to achieve fragile bond lines, even at the micrometer scale. This level of precision is crucial in microjoining applications where minimal adhesive thickness is desired to avoid interference with the functionality of the assembled components.
Minimal Heat Generation:
- UV cure adhesives cure at room temperature, generating minimal heat during the curing process. This characteristic is advantageous when bonding heat-sensitive microcomponents, as it prevents thermal damage and ensures the stability of delicate materials.
Low Shrinkage:
- UV cure adhesives can be formulated to exhibit low shrinkage upon curing. This is essential in microjoining applications to prevent distortion or stress on the bonded components, ensuring that the alignment and dimensional accuracy of the microcomponents are maintained.
Compatibility with Various Substrates:
- UV cure adhesives are compatible with various substrates commonly found in microjoining applications, including metals, ceramics, glass, and plastics. This versatility allows for bonding diverse materials often encountered in microelectronics, optics, and medical device manufacturing.
Optical Clarity:
- UV cure adhesives can be formulated to provide visual clarity, making them suitable for applications where transparency is essential. This is particularly relevant in microjoining applications involving optical components, sensors, or displays.
Adhesion to Microscale Features:
- UV cure adhesives can adhere to microscale features, such as delicate patterns or surface microstructures. This capability is valuable in microjoining applications where intricate bonding is required.
Ease of Handling:
- UV cure adhesives are often supplied in convenient packaging and can be easily dispensed in controlled amounts. Their ease of handling contributes to the precision of the microjoining process, especially when working with small quantities of adhesive.
Customized Formulations:
- Manufacturers can provide customized formulations tailored to specific microjoining applications. Formulation adjustments can address the unique requirements of different materials, geometries, and environmental conditions.
Combining rapid curing, controlled application, and customization options makes UV cure adhesives a preferred choice for achieving precision in microjoining applications. This enables the reliable assembly of miniature components in electronics, optics, and medical devices.
How does the bonding strength of UV cure adhesives compare to that of conventional welding methods?
UV cure adhesive and conventional welding are two different methods used for joining materials, and each has advantages and limitations. Here’s a brief comparison of UV cure adhesive and traditional welding:
UV Cure Adhesive:
Process:
- UV Cure:UV cure adhesives are typically liquid or gel-like substances that harden or cure when exposed to ultraviolet (UV) light. The adhesive is applied to the joint, and UV light initiates the curing process, creating a solid bond.
Materials:
- Compatibility:UV cure adhesives are versatile and can bond various materials, including plastics, glass, and metals. However, the material selection is critical, and not all materials are suitable for UV-cure adhesives.
Precision:
- High Precision:UV cure adhesives offer high precision and are ideal for applications requiring delicate or intricate bonding.
Heat Sensitivity:
- Low Heat Generation:UV curing typically generates minimal heat, making it suitable for heat-sensitive materials.
Speed:
- Quick Bonding:UV cure adhesives can provide rapid curing times, making them ideal for high-speed production.
Ease of Use:
- Easy Application:Applying UV cure adhesives is generally clean and straightforward. However, proper surface preparation is crucial.
Conventional Welding:
Process:
- Heat-Based Joining:Conventional welding involves heating materials to their melting point and then allowing them to cool, creating a fused joint. Standard welding methods include arc welding, MIG (Metal Inert Gas), and TIG (Tungsten Inert Gas) welding.
Materials:
- Metal Emphasis:Conventional welding is primarily used for metals and is unsuitable for all materials, especially those that can be damaged by high heat.
Precision:
- Variable Precision:Welding can be precise, especially in skilled hands, but the level of precision may vary depending on the welding method.
Heat Sensitivity:
- High Heat Generation:Conventional welding generates high temperatures, making it unsuitable for heat-sensitive materials. It can also lead to distortion or changes in material properties.
Speed:
- Variable Speed:Welding can be slower than some adhesive methods, especially for larger or more complex joints.
Ease of Use:
- Skilled Labor Required:Welding often requires experienced operators and the process can be more difficult, involving safety precautions and the need for protective equipment.
Considerations:
- Application Requirements:Choose the method based on the specific requirements of the application, including material compatibility, joint strength, and precision.
- Heat Sensitivity:Consider whether the joined materials are heat-sensitive, as UV cure adhesives generate less heat than conventional welding.
- Speed and Production Volume:If rapid bonding is crucial, UV-cure adhesives might be more suitable for high-speed production processes.
- Skill Level:Welding often requires skilled operators, while UV cure adhesives may be easier to apply, requiring less specialized training.
Ultimately, the choice between UV cure adhesive and conventional welding depends on the joint’s specific application, material requirements, and desired characteristics.
What are the key quality control measures implemented in the production and application of UV cure adhesives?
Quality control measures for UV cure adhesives are essential to ensure consistent and reliable performance in bonded joints. Here are some key quality control measures for UV cure adhesives:
Material Inspection:
- Incoming Materials:Verify the quality of incoming raw materials, including the adhesive itself, substrates, and other components. Ensure that materials meet specified standards and are within acceptable tolerances.
Storage Conditions:
- Proper Storage:UV cure adhesives may have specific storage requirements, such as temperature and light exposure limitations. Ensure the adhesives are stored according to the manufacturer’s recommendations to maintain stability and effectiveness.
Equipment Calibration:
- UV Light Sources:Regularly calibrate and monitor UV light sources to ensure they emit the correct wavelength and intensity for proper curing. Inaccurate UV intensity can lead to incomplete curing and compromised bond strength.
Adhesive Application:
- Consistent Application:Implement controls to ensure the consistent application of the adhesive. This includes monitoring dispensing equipment, ensuring proper coverage, and maintaining the correct adhesive thickness.
Surface Preparation:
- Substrate Cleaning:Adequate surface preparation is crucial for adhesion. Ensure that substrates are clean and free from contaminants that could interfere with bonding. Implement proper cleaning procedures and monitor their effectiveness.
Curing Time and Temperature:
- Optimal Conditions:Monitor and control curing time and temperature to ensure the adhesive cures properly. Deviations from recommended curing conditions can affect bond strength and durability.
Adhesive Cure Verification:
- Testing Procedures:Establish testing procedures to verify the cure of the adhesive. Depending on the application requirements, this may involve periodic testing of cured samples using hardness testing, peel testing, or shear testing.
Batch-to-Batch Consistency:
- Batch Testing:Conduct batch testing to ensure consistency in adhesive properties across different batches. This includes testing viscosity, cure time, and other relevant properties.
Adhesive Performance Testing:
- End-Product Testing:Perform comprehensive testing on the final product to ensure it meets specified performance criteria. This may involve testing for strength, durability, and other relevant properties based on the application requirements.
Documentation and Record-Keeping:
- Traceability:Maintain detailed records of production processes, including adhesive application, curing conditions, and testing results. This documentation provides traceability and facilitates investigation in case of quality issues.
Employee Training:
- Skill Development:Ensure employees involved in the application and curing processes are adequately trained. Proper training helps minimize human errors and ensures consistent quality.
Customer Feedback and Field Performance:
- Monitoring Performance:Collect and analyze end-user feedback regarding the bonded products’ performance in real-world applications. This information can be valuable for continuous improvement.
A comprehensive quality control system helps ensure UV cure adhesive applications meet the required standards and deliver reliable performance over time. Regular audits and continuous improvement efforts contribute to the effectiveness of the quality control measures.
What strategies can manufacturers use to use UV cure adhesives cost-effectively in large-scale productions?
Manufacturers can employ several strategies to use UV cure adhesives cost-effectively in large-scale productions. UV cure adhesives offer advantages such as rapid curing, strong bonding, and environmental friendliness, but optimizing their use can help minimize costs. Here are some strategies:
Process Optimization:
- Analyze and optimize the curing process parameters, including UV light intensity, exposure time, and distance. This can help maximize efficiency and reduce energy consumption.
Material Selection:
- Choose UV cure adhesives that are specifically designed for the intended application. This ensures the adhesive meets performance requirements without over-specifying and incurring unnecessary costs.
Bulk Purchasing:
- Negotiate with suppliers for bulk purchasing discounts. Buying UV cure adhesives in larger quantities can reduce per-unit costs.
Automated Application Systems:
- Implement automated dispensing and curing systems to ensure precise application and reduce labor costs. Automation can also lead to consistent results, minimizing waste.
Training and Education:
- Train operators to ensure they understand the proper application and curing procedures. This can reduce errors and prevent waste caused by improperly cured adhesives.
Equipment Maintenance:
- Regularly maintain UV curing equipment to ensure optimal performance. Well-maintained equipment operates more efficiently, reducing downtime and overall production costs.
Energy-Efficient Equipment:
- Invest in energy-efficient UV curing equipment to minimize electricity costs. Consider LED-based curing systems, which are more energy-efficient than traditional mercury vapor lamps.
Waste Reduction:
- Minimize adhesive waste by accurately dispensing the required amount. Implement systems to collect and reuse any excess adhesive, reducing material costs.
Quality Control:
- Implement stringent quality control measures to catch defects early in the production process. This can reduce the need for rework and prevent the use of defective materials.
Supply Chain Optimization:
- Work closely with suppliers to optimize the supply chain, ensuring timely delivery of raw materials and reducing the risk of production delays that could incur additional costs.
Regulatory Compliance:
- Stay informed about regulatory requirements for UV cure adhesives in your industry. Ensuring compliance from the outset can prevent costly legal issues later.
Life Cycle Cost Analysis:
- Conduct a life cycle cost analysis to evaluate the overall costs of UV cure adhesives. Consider the upfront material costs and factors such as labor, energy, and waste disposal.
By implementing these strategies, manufacturers can enhance the cost-effectiveness of UV cure adhesives in large-scale productions while maintaining high-quality standards.
Can you elaborate on specific environmental considerations, such as emissions and recyclability, associated with UV cure adhesives versus conventional welding?
Certainly! UV cure adhesives and conventional welding are two different methods used in joining materials, and they come with distinct environmental considerations. Let’s delve into the ecological aspects, focusing on emissions and recyclability for both:
UV Cure Adhesives:
Emissions:
- Volatile Organic Compounds (VOCs):UV cure adhesives typically have lower VOC emissions compared to some conventional adhesives. VOCs can contribute to air pollution and have adverse health effects.
- Hazardous Air Pollutants (HAPs):UV cure adhesives often have reduced emissions of hazardous air pollutants, making them more environmentally friendly regarding air quality.
Energy Consumption:
- Lower Energy Usage:UV cure adhesives generally require less curing energy than heat-based processes, such as welding. This can contribute to lower overall energy consumption and reduced carbon footprint.
Recyclability:
- Challenges in Recycling:UV-cure adhesives can pose difficulties in recycling because they form a strong bond that may be difficult to break during the recycling process. However, developments in UV-curable materials with enhanced recyclability are ongoing.
Waste Generation:
- Minimal Waste:UV cure adhesives often generate less waste during bonding than welding, where excess material may be melted or burned off.
Conventional Welding:
Emissions:
- Particulate Matter and Gases:Welding processes, especially those involving heat, can produce significant amounts of particulate matter and gases. These emissions can contribute to air pollution and may contain substances harmful to human health.
Energy Consumption:
- Higher Energy Usage:Conventional welding processes, particularly those involving high temperatures like arc welding, can be energy-intensive. This higher energy consumption contributes to a larger carbon footprint.
Recyclability:
- Facilitates Recycling:Welded joints can be more easily disassembled and materials separated for recycling than adhesive bonds. This can be advantageous in terms of material recovery and recycling efficiency.
Waste Generation:
- Potential for More Waste:Welding processes may generate more waste in spatter, slag, and excess material compared to the generally cleaner application of adhesives.
Overall Considerations:
- The environmental impact of each method can vary depending on the specific application, materials used, and process parameters.
- Ongoing research and development in both fields aim to improve the environmental performance of adhesives and welding techniques.
- The choice between UV cure adhesives and conventional welding should consider the application’s specific requirements, performance criteria, and the project’s environmental goals.
Are there specific types of metals or applications where the limitations of UV cure adhesives become more pronounced in metal bonding?
UV cure adhesives are versatile and can bond various materials, including metals. However, certain limitations and considerations become more pronounced in specific types of metals or applications. Here are some factors to keep in mind:
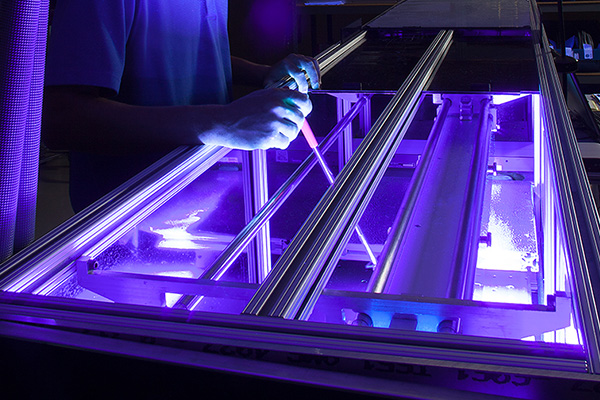
Metal Types:
Opaque or Highly Reflective Metals: UV light has difficulty penetrating opaque or highly reflective surfaces. Therefore, bonding metals like aluminum or stainless steel, which are highly reflective, can be more challenging with UV-cure adhesives. Surface preparation may be necessary to enhance bonding, such as roughening or applying an adhesion promoter.
Surface Conditions:
Oxidized or Contaminated Surfaces: Metals with oxidized or contaminated surfaces may not bond well with UV-cure adhesives. Proper cleaning and surface preparation are crucial for achieving a solid bond.
High Temperature Resistance:
Limited Heat Resistance: UV cure adhesives may have heat resistance limitations compared to conventional welding methods. Other bonding methods like welding might be more suitable if the bonded metal components are exposed to high temperatures during service life.
Joint Design and Strength Requirements:
High Structural Load Requirements: In applications where high structural load-bearing capacity is essential, welding may be preferred over UV-cure adhesives. Welded joints can offer robust mechanical strength, especially in heavy-duty or high-stress environments.
Application-Specific Challenges:
Harsh Environments: If the metal bonding application involves exposure to harsh environmental conditions, such as extreme temperatures, chemicals, or weathering, the UV cure adhesive’s resistance to these factors should be carefully evaluated.
Thickness of Adhesive Layer:
Limitations in Bond Line Thickness: UV cure adhesives typically cure in thin bond lines. If a thicker adhesive layer is required for a specific application, alternative bonding methods like structural adhesives or welding might be more suitable.
Cure Time:
Large Bonded Areas: The cure time of UV cure adhesives may become a limitation for large metal surfaces. Ensuring the adhesive has sufficient time to cure uniformly across the bonded area is essential.
Cost Considerations:
Material and Equipment Costs: Depending on the specific UV cure adhesive and the equipment required for curing, the cost may be a factor to consider. In some cases, welding may be a more cost-effective option for metal bonding.
What recent technological advancements have significantly influenced the effectiveness and versatility of UV cure adhesives compared to conventional welding methods?
Keep in mind that there might be further developments after that date. UV cure adhesives have significantly improved, making them more effective and versatile than conventional welding. Some key improvements include:
Faster Cure Times: UV curing technology advances have led to cure times faster. This is crucial for industries where rapid production is essential. Shorter curing times improve efficiency and allow for quicker assembly processes.
LED UV Technology: Traditional UV lamps have mainly been replaced or supplemented by LED UV technology. LED UV curing systems offer benefits such as longer life, reduced energy consumption, and more precise control over the curing process. They also emit less heat, making them suitable for temperature-sensitive applications.
Improved Formulations: Ongoing research and development efforts have resulted in the formulation of UV adhesives with enhanced properties, such as improved adhesion strength, flexibility, and resistance to environmental factors. These improvements broaden the range of applications for UV-cure adhesives.
Adhesive Customization: UV cure adhesives can be tailored to specific requirements, allowing manufacturers to choose formulations that best suit their needs. This customization capability enhances the versatility of UV adhesives in various industries and applications.
Compatibility with Diverse Substrates: UV cure adhesives have become more versatile regarding substrate compatibility. They bond well with various materials, including plastics, glass, metals, and composites. This versatility makes UV adhesives suitable for diverse electronics, automotive, and medical applications.
Reduced Environmental Impact: UV cure adhesives are generally considered more environmentally friendly than traditional adhesive and welding methods. The curing process is solvent-free, reducing emissions of volatile organic compounds (VOCs). This aligns with the growing emphasis on sustainability and eco-friendly manufacturing practices.
In-line Process Integration: UV cure adhesive systems can be easily integrated into automated production lines. This enables seamless and continuous manufacturing processes, improving overall production efficiency and reducing labor costs.
It’s advisable to check for more recent sources or industry updates to get the latest information on technological advancements in UV cure adhesives.
How do safety considerations differ between UV cure adhesive applications and conventional welding, especially regarding operator exposure and handling of materials?
UV cure adhesive applications and conventional welding involve different processes, and their safety considerations can vary significantly. Here are some critical differences in terms of operator exposure and handling of materials:
Operator Exposure:
UV Cure Adhesive Applications:
- UV cure adhesives typically contain photoinitiators that initiate curing when exposed to ultraviolet (UV) light. Operators must be cautious about UV radiation exposure, as prolonged exposure can harm skin and eyes.
- Operators should wear appropriate personal protective equipment (PPE) such as UV-resistant gloves, safety glasses with UV filters, and clothing that covers exposed skin.
Conventional Welding:
- Depending on the welded materials, welding processes generate intense heat and emit harmful fumes, including metal fumes and potentially toxic gases. Prolonged exposure to welding fumes can lead to respiratory issues.
- Welders should use appropriate respiratory protection, such as a powered air-purifying respirator (PAPR) or a supplied air respirator. Additionally, welding helmets with proper filters protect the eyes and face from intense light and UV radiation.
Handling of Materials:
UV Cure Adhesive Applications:
- UV cure adhesives are often used for bonding materials sensitive to heat. The adhesive is applied and then exposed to UV light, leading to a fast and low-temperature curing process.
- Bonded materials should be compatible with UV curing, and operators should follow manufacturer guidelines for proper application and curing.
Conventional Welding:
- Welding involves the melting and fusing of materials, and the choice of materials is crucial. Different metals and alloys have varying melting points, and welding parameters must be adjusted accordingly.
- Welders need to be trained in handling and positioning materials, understanding the properties of the materials being welded, and following safety protocols to prevent accidents and ensure the integrity of the weld.
Ventilation:
UV Cure Adhesive Applications:
- Adequate ventilation is essential to disperse any residual fumes released during curing. This is especially important in confined spaces.
Conventional Welding:
- Ventilation is crucial to remove welding fumes and gases produced during welding. Local exhaust ventilation systems or proper natural ventilation should be in place to protect operators from inhaling harmful substances.
What market trends indicate the adoption and preference for UV cure adhesives over conventional welding in specific industries?
Remember that the landscape may have evolved since then, and checking more recent sources for the latest information is advisable. As of my last update:
Precision and Miniaturization: UV cure adhesives are favored in industries where precision and miniaturization are critical, such as electronics and medical devices. Applying these adhesives in tiny quantities and quickly curing them with UV light makes them suitable for delicate and intricate assemblies.
Speed and Efficiency: UV cure adhesives offer rapid curing times, often within seconds, leading to increased production efficiency. This is particularly advantageous in industries where quick turnaround times are essential, such as automotive and consumer electronics.
Reduced Heat-Affected Zone (HAZ): Unlike welding, UV cure adhesives do not generate heat during curing, minimizing the heat-affected zone. This is crucial in applications where heat-sensitive materials are involved, such as in bonding plastic components or assembling electronic devices.
Versatility in Material Compatibility: UV cure adhesives exhibit good adhesion to various substrates, including plastics, glass, and metals. This versatility makes them attractive in industries where bonding dissimilar materials is common, such as assembling composite or multi-material components.
Environmental Considerations: UV cure adhesives are often solvent-free and emit fewer volatile organic compounds (VOCs) compared to some welding processes. This aligns with the growing emphasis on environmental sustainability and regulatory requirements in various industries.
Automation and Industry 4.0: UV cure adhesives can be easily integrated into automated manufacturing processes, aligning with the trend towards Industry 4.0 and intelligent manufacturing. The ability to automate adhesive application and curing contributes to increased efficiency and consistency in production.
Health and Safety: Welding processes can involve hazards such as fumes, sparks, and high temperatures. UV cure adhesives, a cold-curing process, eliminate some of these safety concerns. Industries focusing on worker safety may prefer UV-cure adhesives in specific applications.
It’s essential to note that market trends can change, and advancements may influence the adoption of UV cure adhesives in technology, cost considerations, and industry-specific requirements. Consulting industry reports market analyses, and relevant trade publications are recommended for the latest and most accurate information.
Are there specific industries or projects where the choice of UV cure adhesives led to notable efficiency, cost, or product quality improvements?
Some industries and projects where UV cure adhesives have been particularly advantageous include:
Electronics Manufacturing:
- Bonding and Encapsulation:UV adhesives are used for bonding and encapsulating electronic components due to their quick curing time, which improves production efficiency.
- Miniaturization:As electronic devices become smaller and more complex, UV adhesives are preferred for their ability to create precise and small bond lines.
Medical Devices:
- Sterilization Compatibility:UV adhesives are suitable for medical devices because they can be sterilized after curing without degradation, ensuring product quality.
- Biocompatibility:Some UV-curable adhesives are formulated to be biocompatible, making them suitable for medical applications.
Optical and Display Industry:
- Optical Bonding:UV adhesives assemble displays and optical devices, providing visual clarity and high bond strength.
- Reduced Heat Exposure:The low-temperature curing process of UV adhesives is beneficial for displaying heat-sensitive components.
Automotive Industry:
- Bonding and Sealing:UV adhesives are employed in automotive assembly for bonding and sealing applications due to their fast curing, contributing to shorter production cycles.
- Improved Aesthetics:UV-curable coatings enhance the appearance of automotive interiors and exteriors.
Aerospace Industry:
- Lightweighting:UV adhesives contribute to lightweighting efforts by providing strong bonds with minimal added weight.
- Reduced Processing Time:Quick curing times of UV adhesives are advantageous in aerospace manufacturing, where time is a critical factor.
3D Printing:
- Post-Processing:UV-curable adhesives are used in post-processing steps for 3D-printed parts, providing additional strength and stability.
Woodworking and Furniture:
- Faster Production:UV adhesives enable faster production in woodworking applications due to their rapid curing, reducing manufacturing cycle times.
- Improved Aesthetics:UV coatings enhance aesthetics and wood surface protection.
General Assembly and Bonding:
- Speed and Efficiency:UV adhesives are chosen in various general assembly applications for quick curing, allowing for faster production and assembly lines.
UV-curable adhesives in these industries and projects often lead to increased production speed, reduced energy consumption, enhanced product quality, and more precise bonding. However, it’s essential to carefully consider the specific requirements of each application to ensure that UV cure adhesives are the most suitable choice.
What potential advancements or research areas are being explored to further enhance the performance and applicability of UV cure adhesives compared to conventional welding?
Here are some potential areas of research and advancements:
Formulation and Chemistry:
- Researchers are developing new formulations and chemical compositions for UV cure adhesives to improve their strength, flexibility, and adhesion properties.
- Tailoring the chemistry of UV cure adhesives can enhance their resistance to environmental factors, such as temperature, humidity, and chemicals.
Curing Speed and Efficiency:
- Improving the speed of the UV curing process is a crucial area of focus. Faster curing times can lead to increased efficiency and productivity in manufacturing processes.
- Researchers are exploring new photoinitiators and light sources to accelerate the curing reaction without compromising the adhesive’s performance.
Substrate Compatibility:
- Enhancing the compatibility of UV cure adhesives with a wide range of substrates is crucial for their broader application. Researchers are working on formulations that adhere well to diverse materials, including metals, plastics, glass, and composites.
Optical Design and Light Sources:
- Advancements in optical design and development more efficient UV light sources contribute to improved curing uniformity and depth.
- Researchers are exploring using light-emitting diodes (LEDs) and other advanced light technologies to optimize curing.
Thermal Stability:
- Increasing the thermal stability of UV cure adhesives is essential for applications where the bonded materials may be subjected to elevated temperatures.
- Research focuses on developing adhesives to maintain integrity and bonding strength under varying thermal conditions.
Mechanical Properties:
- Optimizing the mechanical properties of UV cure adhesives, such as tensile strength, shear strength, and impact resistance, is crucial for their performance in different applications.
- Tailoring the adhesive properties based on the specific requirements of industries like automotive, electronics, and medical devices is ongoing.
Automation and Integration:
- Advancements are being made to integrate UV cure adhesive processes into automated manufacturing systems, allowing for higher precision and consistency.
- The development of robotics and automation technologies can enhance the application of UV cure adhesives in large-scale production.
Innovative Applications:
- Researchers are exploring new and innovative applications for UV cure adhesives, such as in flexible electronics, medical devices, and 3D printing.
Research in these areas is dynamic, and new developments may have occurred since my last update. Checking recent scientific literature, industry publications, and conference proceedings will provide the most up-to-date information on advancements in UV cure adhesives.
Conclusion:
In conclusion, UV cure adhesive for metal represents a breakthrough in adhesive technology, offering myriad benefits across diverse industrial sectors. From its rapid curing capabilities to enhanced precision in bonding, this adhesive has redefined the landscape of metal joining applications. As industries continue to seek efficient and reliable solutions, UV cure adhesive for metal stands as a testament to innovation, promising a future where metal bonding is not just a process but an art perfected through advanced adhesive technologies.
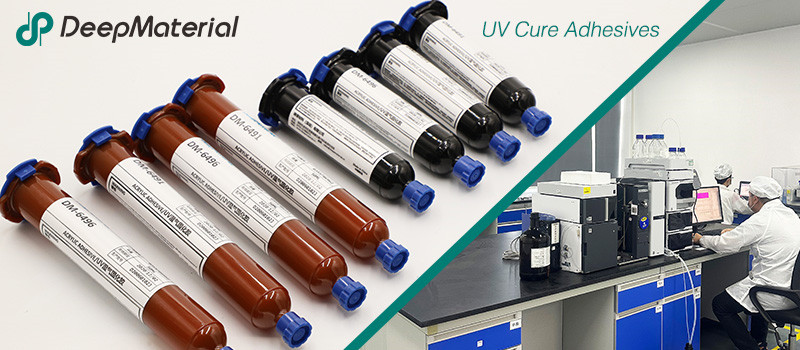
DeepMaterial
Based on the core technology of adhesives, DeepMaterial has developed adhesives for chip packaging and testing, circuit board level adhesives, and adhesives for electronic products. Based on adhesives, it has developed protective films, semiconductor fillers, and packaging materials for semiconductor wafer processing and chip packaging and testing. More…
UV Curing Adhesives
UV light cure have a number of benefits making them a popular choice among many product assembly and manufacturing applications. Many UV light cure adhesives can provide a nearly instantaneous bond to difficult substrates like glass and plastic. UV cure adhesives often require an accelerator or UV light for a bond to form.
Adhesive Blogs & News
The latest adhesive industry science and technology, Deepmaterial news, and market trends and forecasts.
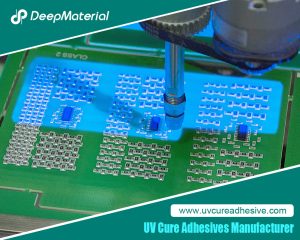
In – depth Analysis of the Main Characteristics of UV Adhesives for Touch Screens
In – depth Analysis of the Main Characteristics of UV Adhesives for Touch Screens In the manufacturing of modern electronic devices, the touch screen serves as a crucial component for human – machine interaction, and its performance and quality are of utmost importance. As a key material for effectively bonding various components of the touch
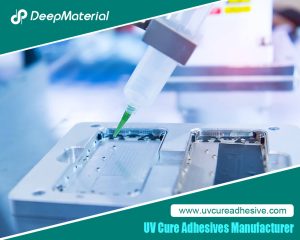
The Quantitative Influence of Crosslinking Density on the Flexibility and Hardness of Adhesives and the Formulation Optimization Strategy
The Quantitative Influence of Crosslinking Density on the Flexibility and Hardness of Adhesives and the Formulation Optimization Strategy This article systematically expounds the quantitative relationship between the crosslinking density and the flexibility and hardness of adhesives. Combining the theories of polymer physics with experimental analysis methods, it reveals the mechanism of the action of the
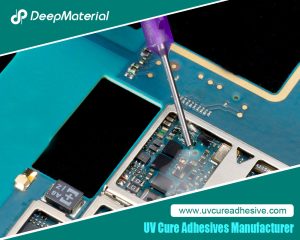
Technical Strategies for Balancing the Rapid Curing Property and Long Operating Time of UV Adhesives
Technical Strategies for Balancing the Rapid Curing Property and Long Operating Time of UV Adhesives UV adhesives have been widely used in many fields such as electronics, optics, and medicine due to their advantages of rapid curing, high bonding strength, and environmental protection. However, their rapid curing property also brings challenges in some application scenarios.
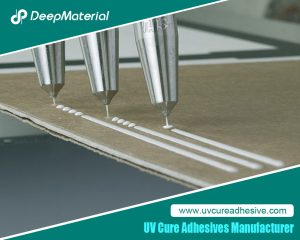
Biocompatibility of LED UV Glue Adhesive and Its Application Potential in Medical and Food Packaging Fields
Biocompatibility of LED UV Glue Adhesive and Its Application Potential in Medical and Food Packaging Fields LED UV glue adhesive has been widely applied in numerous fields due to its advantages such as rapid curing and easy operation. However, in fields with stringent safety requirements like medical and food packaging, its biocompatibility after curing
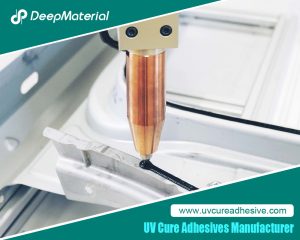
Exploring the Environmental Performance of UV Glue and Strategies for Optimizing Odor and VOC Content
Exploring the Environmental Performance of UV Glue and Strategies for Optimizing Odor and VOC Content UV glue, as an adhesive that achieves rapid curing through ultraviolet (UV) light irradiation, has been widely applied in numerous fields such as electronics, optics, healthcare, and automobiles, thanks to its advantages of fast curing speed, high bonding strength, and
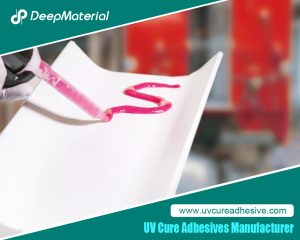
Compatibility Analysis and Countermeasures of LED UV Glue with Automated Production Equipment
Compatibility Analysis and Countermeasures of LED UV Glue with Automated Production Equipment LED UV glue has been widely used in modern manufacturing due to its advantages such as fast curing speed, high bonding strength, and environmental friendliness. However, in the automated production process, if there are problems with the adaptability between the glue and equipment