- Home
- >
- Application
- >
- Electric Car Adhesive
Electric Car Adhesive
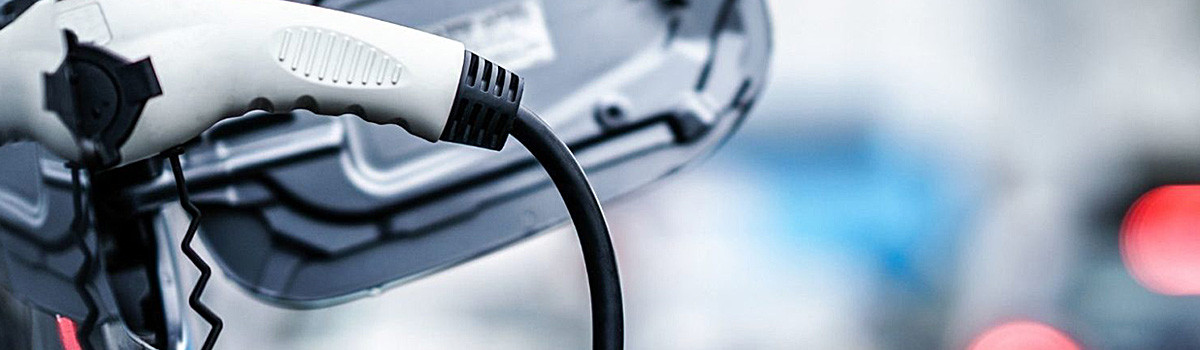
Electric Car Adhesive stands at the heart of pioneering advancements in the automotive world. In the dynamic landscape of electric vehicles (EVs), these adhesive solutions transcend mere components, serving as critical agents for progress. From reinforcing structural integrity to fostering sustainability and elevating safety standards, the role of Electric Car Adhesive is paramount. This exploration delves into the multifaceted significance of these adhesives, unraveling their pivotal contributions to electric cars’ efficiency, performance, and eco-friendliness.
Table of Contents
ToggleWhy are adhesives crucial in electric cars?
Electric cars have revolutionized the automotive industry, boasting eco-friendly features and cutting-edge technology. Among the many components that make these vehicles tick, adhesives stand out as unsung heroes, crucial in ensuring their efficiency, safety, and durability.
Here’s why adhesives are indispensable in the realm of electric cars:
Enhanced Structural Integrity
- Adhesives reinforce the structural integrity of electric vehicles, bonding components like batteries, frames, and panels seamlessly. Unlike traditional welding or mechanical fastening, adhesives distribute stress evenly, reducing the risk of cracks or failure.
- The bonding strength of adhesives contributes to the overall rigidity of the vehicle, enhancing its ability to withstand impacts and ensuring passenger safety.
Weight Reduction and Improved Efficiency
- Replacing mechanical fasteners like nuts and bolts adhesives helps reduce the weight of electric cars. This weight reduction enhances the vehicle’s efficiency, extending the electric car’s range on a single charge.
- Additionally, using adhesives allows for integrating dissimilar materials, such as bonding aluminum to carbon fiber or steel, further optimizing the car’s weight distribution without compromising strength.
Vibration Dampening and Noise Reduction
- Adhesives act as a cushion, absorbing vibrations and minimizing noise within the vehicle. This feature significantly enhances the driving experience by creating a quieter and smoother ride for passengers.
Sealing and Protection Against Environmental Factors
- Adhesives are vital in sealing electric car components, protecting them from moisture, dirt, and other environmental factors. This protection is crucial for sensitive electrical parts like batteries and wiring harnesses, ensuring longevity and performance.
Streamlining Manufacturing Processes
- The use of adhesives simplifies the assembly process in manufacturing, allowing for faster and more efficient production of electric cars. Compared to welding or mechanical joining, adhesive bonding often requires less energy and reduces the need for specialized equipment, contributing to cost-effectiveness and scalability in production.
What types of adhesives are used in electric cars?
Electric cars have revolutionized the automotive industry, boasting eco-friendly features and cutting-edge technology. Amidst their innovation lies a crucial yet often overlooked component: adhesives. These powerful bonding agents play a pivotal role in electric vehicle construction, assembly, and performance. Regarding electric cars, the choice of adhesive can significantly impact safety, efficiency, and durability.
Types of Adhesives Utilized in Electric Cars
- Structural Adhesives:These high-strength adhesives are paramount for joining structural components in electric cars. They provide robust bonding, enhancing the overall vehicle strength while reducing weight. Epoxy resins and acrylic adhesives fall under this category, delivering exceptional bonding capabilities for diverse materials used in car manufacturing.
- Thermal Interface Materials (TIMs): Electric vehicles rely heavily on thermal management systems to ensure optimal performance. TIMs, including thermally conductive adhesives, facilitate heat transfer between crucial components like batteries and heat sinks. Silicones and epoxies with enhanced thermal conductivity are employed to dissipate heat, ensuring the longevity of sensitive parts efficiently.
- Sealants:Electric cars require superior sealing to prevent water ingress and maintain the integrity of electrical components. Sealants, often made of silicone or polyurethane, create watertight seals around doors, windows, and electronic enclosures, safeguarding the vehicle against moisture and corrosion.
- Electrically Conductive Adhesives:Ensuring seamless electrical connections within electric cars is essential. Electrically conductive adhesives enable bonding while allowing the flow of electricity. Silver-filled epoxies or acrylics serve as effective conductive adhesives for joining electrical circuits, sensors, and other electronic parts.
- Acoustic and Vibration Damping Adhesives:Electric vehicles aim for a quiet and smooth ride. Adhesives with vibration-dampening properties attenuate noise and reduce vibrations caused by the vehicle’s components. These adhesives, often based on viscoelastic materials, enhance comfort while ensuring the longevity of parts by minimizing stress.
The significance of these adhesives goes beyond mere joining; they contribute to electric vehicles’ efficiency, safety, and longevity. Manufacturers continually innovate to develop adhesives that meet the evolving demands of the electric car industry, aiming for enhanced performance and sustainability.
How do adhesives contribute to the efficiency of electric cars?
Heralded for their eco-conscious design and technological prowess, electric cars owe a significant part of their efficiency to an often underestimated component: adhesives. Beyond mere bonding agents, adhesives play a pivotal role in enhancing the efficiency of electric vehicles in multiple ways.
Key Contributions of Adhesives to Electric Car Efficiency
- Weight Reduction:Adhesives enable the use of lighter materials in vehicle construction, reducing overall weight. This weight-saving strategy enhances the car’s energy efficiency, extending the range per charge. By replacing traditional welding or mechanical fasteners, adhesives trim excess weight without compromising structural integrity.
- Improved Aerodynamics:Seamlessly bonding components with adhesives allows smoother surfaces, reducing air resistance. Enhanced aerodynamics decrease drag, optimizing the vehicle’s efficiency by requiring less energy to maintain speed. Adhesives play a role in affixing components like spoilers or panels, ensuring a streamlined design for improved airflow.
- Thermal Management:Efficient heat dissipation is crucial in electric vehicles, especially concerning batteries and electronic components. Adhesives with thermal conductivity properties facilitate heat transfer, preventing overheating and maintaining optimal operating temperatures. It ensures battery longevity and consistent performance, directly impacting the car’s efficiency.
- Battery Performance and Safety:Adhesives are instrumental in assembling battery packs, securing cells, and creating solid yet flexible bonds. Properly bonded battery modules minimize internal movement, reducing the risk of damage and improving overall safety. Additionally, they contribute to the efficient distribution of electrical currents within the battery system, optimizing its performance.
- Sealing and Energy Conservation:Adhesives act as effective sealants, preventing leaks and ensuring the integrity of the vehicle’s structure. Adhesives minimize air infiltration by sealing gaps and joints, contributing to better insulation. It helps maintain a stable interior temperature, reducing the strain on heating or cooling systems and conserving energy.
Are these adhesives environmentally friendly?
Amidst the eco-conscious revolution in automotive technology, the significance of adhesives in electric cars transcends mere functionality. As the world pivots towards sustainable transportation, scrutiny intensifies on the environmental footprint of every vehicle component, including adhesives.
Environmental Considerations Surrounding Electric Car Adhesives
- Low Volatile Organic Compounds (VOCs): Modern adhesives for electric cars often prioritize formulations with reduced VOC content. These formulations diminish harmful emissions, ensuring a smaller ecological impact during production and throughout the vehicle’s lifespan.
- Recyclability and Disassembly:Manufacturers increasingly focus on adhesives that facilitate disassembly and component recycling. Certain adhesives allow for easier separation of bonded materials, enabling more efficient recycling processes and reducing waste.
- Bio-based and Renewable Sources:Advancements in adhesive technology incorporate bio-based and renewable materials, such as plant-based resins or biodegradable compounds. These alternatives aim to decrease dependency on fossil fuels and contribute to a more sustainable production cycle.
- Durability and Longevity:Adhesives that contribute to the longevity and durability of electric cars play a role in sustainability. These adhesives indirectly minimize resource consumption and waste generation over the vehicle’s lifecycle by reducing the need for frequent repairs or replacements.
- Energy Efficiency in Production:Some adhesive manufacturing processes emphasize energy efficiency and reduced resource consumption. These efforts further minimize the environmental impact associated with adhesive production.
The quest for genuinely sustainable adhesives continues, prompting collaboration between automotive manufacturers and adhesive suppliers. They aim to develop formulations that meet stringent performance standards and align with environmental goals, contributing to the overall sustainability of electric vehicles.
What challenges do manufacturers face in selecting the right adhesives for EVs?
As the automotive industry shifts gears towards electric vehicles (EVs), manufacturers face many challenges in ensuring these eco-friendly cars meet safety, performance, and durability standards. One crucial aspect often overlooked but pivotal in EV manufacturing is the selection of the right adhesives. These specialized adhesives play a vital role in ensuring electric cars’ structural integrity, efficiency, and longevity.
Challenges for Manufacturers
- Compatibility with EV Components:Electric vehicles have unique components like batteries, motors, and power electronics, demanding adhesives that can withstand high temperatures and harsh chemical environments. Selecting adhesives compatible with these components is crucial to prevent corrosion, maintain electrical insulation, and ensure long-term reliability.
- Thermal Management:EVs generate substantial heat during operation, especially in batteries and powertrain components. Adhesives must possess excellent thermal conductivity to dissipate heat efficiently without compromising adhesion or structural integrity. Failure in managing thermal stress can lead to reduced performance or even safety hazards.
- Vibration and Impact Resistance:Electric vehicles, like their conventional counterparts, face challenges from road vibrations and impacts. Adhesives must absorb these vibrations, ensuring the bonded components remain intact and secure over the vehicle’s lifespan. Choosing adhesives with high-impact resistance is pivotal to maintaining structural stability.
- Environmental Factors:EVs operate in various environmental conditions, from extreme temperatures to exposure to moisture and chemicals. Adhesives must be resilient to these conditions to prevent degradation and maintain their adhesive properties, safeguarding the vehicle’s structural integrity.
- Regulatory Compliance:With the burgeoning EV market, regulatory standards are evolving. Manufacturers need adhesives that comply with industry regulations and environmental norms without compromising performance. Adhering to these standards is vital for ensuring the safety and marketability of electric vehicles.
Addressing these Challenges
- Material Innovation:Research and development efforts are focused on creating specialized adhesive materials tailored for EV applications. Formulating adhesives with enhanced thermal conductivity, chemical resistance, and durability addresses specific challenges EV manufacturers face.
- Testing and Validation:Rigorous testing protocols are essential to evaluate the performance of adhesives in simulated EV operating conditions. Manufacturers conduct comprehensive tests to ensure that the selected adhesives meet the stringent reliability, safety, and longevity requirements.
- Collaboration and Knowledge Sharing:Collaboration between adhesive manufacturers, automotive engineers, and material scientists is crucial. Sharing expertise and knowledge aids in developing innovative adhesive solutions that cater specifically to the unique demands of electric vehicles.
How do adhesives impact the safety of electric vehicles?
Electric vehicles (EVs) are revolutionizing the automotive industry, and one crucial element ensuring their safety and structural integrity is often overlooked: adhesives. These specialized bonding agents play a pivotal role in constructing and maintaining EVs, influencing their safety in multifaceted ways.
Understanding the Impact
Enhanced Structural Integrity
- Adhesives fortify the bonding of materials, creating a unified structure that distributes stress and enhances the overall strength of an electric vehicle.
- This distributed stress minimizes the risk of deformities during collisions, safeguarding passengers and components within the vehicle.
Battery Encapsulation and Safety
- Adhesives seal and secure batteries in place, mitigating movement or vibration that could damage the cells and ensuring safer performance and longevity.
- By preventing moisture or debris from entering the battery compartments, adhesives contribute to the prevention of short circuits or corrosion, reducing the risk of electrical malfunctions.
Noise Reduction and Vibration Dampening
- Adhesives act as sound insulators, reducing noise and vibrations generated by the vehicle’s components, creating a quieter and more comfortable driving experience.
- This dampening effect also helps reduce wear and tear on components, thus prolonging their lifespan.
Thermal Management
- Adhesives aid in thermal conductivity and dissipation, helping to regulate temperatures within the vehicle, especially in critical areas like battery packs and electric motors.
- Maintaining optimal operating temperatures is vital for battery efficiency and safety, preventing overheating or thermal runaway scenarios.
Sustainability and Weight Reduction
- Advanced adhesives often contribute to lightweight construction methods, reducing the vehicle’s overall weight.
- Lighter vehicles improve energy efficiency and range while lessening environmental impact, aligning with the sustainable ethos of electric cars.
Challenges and Innovation
- As EV technology advances, adhesives must evolve to meet new demands, such as improved heat resistance and faster curing times, without compromising safety standards.
- Continuous research and development in adhesive technology aim to address these challenges, ensuring the highest safety standards for future electric vehicles.
Are there advancements in adhesive technology specific to electric cars?
The rapid evolution of electric vehicles (EVs) has spurred innovations in various facets of automotive technology. Among these, advancements in adhesive technology have emerged as a critical element, transforming how electric cars are designed, assembled, and performed on the road. Specifically, the development of electric car adhesives has garnered attention due to its pivotal role in enhancing vehicle efficiency, safety, and structural integrity.
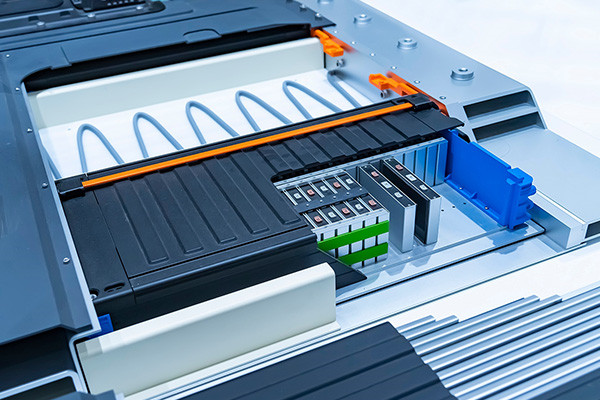
Here’s a closer look at the notable advancements in adhesive technology tailored for electric cars:
- Thermal Management:Electric vehicles generate substantial heat during operation, particularly in battery systems. Advanced adhesives with superior thermal conductivity properties are pivotal in efficiently dissipating heat, ensuring optimal temperature regulation within the vehicle’s components. This capability aids in prolonging the lifespan and enhancing the performance of EV batteries.
- Weight Reduction and Structural Integrity:Adhesives designed for electric cars contribute significantly to the overall weight reduction of the vehicle. By replacing traditional mechanical fasteners like screws and bolts, these adhesives create a bond that distributes stress evenly across surfaces, thereby enhancing structural integrity while simultaneously reducing the vehicle’s weight. It improves energy efficiency and extends the range of electric cars.
- Enhanced Battery Assembly:The assembly of electric car batteries demands precision and reliability. Advanced adhesives offer exceptional bonding strength, allowing for the secure attachment of battery cells and modules. Streamlining the manufacturing process ensures a robust and long-lasting battery pack and contributes to the vehicle’s overall safety.
- Corrosion Resistance:Electric vehicles operate in diverse environments, including varying temperatures and exposure to moisture. Adhesives formulated with superior corrosion-resistant properties shield vital components from environmental factors, ensuring prolonged durability and reliability of electric car systems.
- Noise Reduction and Vibration Dampening:EVs often operate quietly, and advanced adhesives play a role in reducing unwanted vibrations and noise within the vehicle. This enhancement in cabin comfort and noise reduction contributes to a superior driving experience.
Can adhesives enhance the performance of electric vehicles?
In the quest for enhancing the efficiency and performance of electric vehicles (EVs), one often overlooked yet crucial component is adhesives. These specialized bonding materials hold immense potential in shaping the future of EV technology, offering a range of benefits that contribute to their overall performance and durability.
The Role of Adhesives in Electric Cars
- Weight Reduction:Adhesives allow for the bonding of lightweight materials, reducing the vehicle’s overall weight. In electric vehicles (EVs), the importance of lighter cars is evident as they require less energy to move, ultimately extending the driving range per charge.
- Enhanced Structural Integrity:Unlike traditional welding or mechanical fastening, adhesives distribute stress across a larger area, strengthening the structure and minimizing vibrations. It leads to a quieter and more comfortable driving experience.
- Improved Safety:Adhesives reinforce the structural integrity of critical components, such as battery casings and body panels, contributing to the vehicle’s overall safety by providing an additional layer of protection.
- Sealing and Insulation:They create airtight seals, preventing moisture and contaminants from entering sensitive electrical components. Additionally, adhesives can provide thermal insulation, contributing to better temperature regulation within the vehicle.
- Flexibility and Design Freedom:Adhesives offer flexibility in design, allowing manufacturers to join dissimilar materials seamlessly. It enables innovative designs that were previously unattainable using traditional joining methods.
Cutting-Edge Adhesive Technologies
- Conductive Adhesives:These specialized adhesives facilitate electrical conductivity between components, which is crucial in EVs with abundant electrical connections. They enable efficient power transfer and signal flow throughout the vehicle.
- Thermal Management Adhesives:Given the heat generated by EV components, adhesives with superior thermal management properties play a pivotal role in maintaining optimal operating temperatures, thereby extending the lifespan of sensitive parts.
- High-Strength Structural Adhesives:These adhesives offer exceptional bonding strength, ensuring the structural integrity of the vehicle, particularly in crash-prone areas, thus enhancing overall safety.
Future Prospects
The integration of advanced adhesive technologies continues to evolve, with ongoing research focusing on developing adhesives that are stronger, more durable, and environmentally sustainable. Innovations address challenges such as extreme temperature variations and the need for faster curing times.
What role do adhesives play in the battery assembly of electric cars?
The surge of electric vehicles (EVs) has revolutionized the automotive industry, with the heart of these eco-friendly machines lying within their advanced battery systems. Beneath the sleek exteriors and cutting-edge technology, electric car adhesives are a critical element that binds the components together. These adhesives play a pivotal role in the battery assembly of electric cars, facilitating structural integrity, safety, and overall performance.
Adhesives act as the unsung heroes in the construction of electric car batteries, contributing significantly to the efficiency and durability of the vehicles. Here’s how they make a difference:
- Bonding Battery Cells:Adhesives are instrumental in securing battery cells within the pack. They create a robust and durable bond between cells, preventing movement or vibrations that could damage the battery or affect performance. This secure bonding also enhances the overall structural stability of the battery pack.
- Heat Dissipation:Electric car batteries generate heat during charging and discharging cycles. Adhesives are crucial in efficiently transferring heat away from the cells, which is instrumental in managing and regulating temperatures within safe limits. This heat dissipation capability extends the lifespan of the batteries and ensures optimal performance.
- Sealing and Protection:Adhesives serve as a sealing agent, safeguarding the battery components from moisture, dust, and other external elements. This protective barrier not only enhances the battery’s longevity but also minimizes the risk of short circuits or corrosion, which is crucial for the safety and reliability of the vehicle.
- Weight Reduction and Enhanced Design:Compared to traditional mechanical fasteners, adhesives offer a lightweight solution. Their application allows for more innovative and flexible designs, contributing to weight reduction in electric vehicles. The reduced weight improves the vehicle’s energy efficiency and range, addressing critical concerns in the EV industry.
- Noise and Vibration Dampening:Adhesives play a role in minimizing noise and vibrations within the battery pack, ensuring a quieter and smoother driving experience. By absorbing and reducing these unwanted disturbances, they contribute to the vehicle’s overall comfort.
How do adhesives influence the overall design of electric vehicles?
In the realm of electric vehicles (EVs), where innovation and sustainability collide, a lesser-known hero plays a pivotal role in their construction: electric car adhesives. These seemingly small components wield immense influence over these cutting-edge automobiles’ overall design and functionality.
Adhesives in EVs serve as more than just glue; they contribute significantly to the vehicle’s structural integrity, safety, weight reduction, and design flexibility. Here’s how these adhesives influence the landscape of electric vehicle design:
Enhanced Structural Integrity
- Adhesives reinforce the bonding between vehicle parts, creating a unified structure that enhances overall strength.
- They distribute stress and strain across a larger area, minimizing potential weak points in the vehicle’s body.
Weight Reduction and Improved Efficiency
- Unlike traditional welding methods, adhesives are lighter, reducing the vehicle’s weight and enhancing energy efficiency.
- By reducing weight, EVs can extend their range, making them more attractive and practical for consumers.
Design Flexibility and Aesthetic Appeal
- Adhesives allow for more creative freedom in design, enabling sleeker, aerodynamic shapes that enhance aesthetics and performance.
- Smooth, jointless surfaces achieved through adhesive application enhance the vehicle’s visual appeal.
Noise and Vibration Dampening
- Adhesives absorb vibrations and reduce noise, contributing to a quieter and more comfortable driving experience for EV owners.
Battery Integration and Thermal Management
- Adhesives are crucial in securing and insulating batteries within the vehicle, ensuring they remain stable and well-protected.
- They aid in thermal management, dispersing heat away from sensitive components, thereby enhancing battery performance and longevity.
Environmental Impact and Sustainability
- Many modern adhesives used in EVs are formulated to be environmentally friendly, aligning with the eco-conscious ethos of electric vehicles.
- As EVs strive for sustainability, using adhesives contributes to reducing the vehicle’s carbon footprint during production and operation.
Are there any limitations or drawbacks associated with using adhesives in electric cars?
The burgeoning electric vehicle (EV) industry has revolutionized automotive engineering, emphasizing sustainability and efficiency. One of the lesser-known but critical components in EV manufacturing is the use of adhesives. While adhesives are pivotal in enhancing structural integrity, durability, and weight reduction in electric cars, some limitations and drawbacks merit attention.
Advantages of Electric Car Adhesives
- Enhanced Structural Integrity:Adhesives are integral in bonding lightweight materials like aluminum and carbon fiber, reinforcing the vehicle’s structure without compromising strength.
- Weight Reduction:Compared to traditional welding methods, adhesives significantly reduce the weight of an EV, contributing to increased energy efficiency and extended battery range.
- Noise and Vibration Dampening: Adhesives effectively minimize noise and vibration within the vehicle, enhancing the overall driving experience for passengers.
Limitations and Drawbacks
- Temperature Sensitivity:Adhesives can be susceptible to extreme temperatures, affecting their bonding strength and integrity. High temperatures can cause adhesives to soften, potentially leading to structural issues.
- Long-term Durability:While adhesives undergo rigorous testing, their long-term durability in harsh environmental conditions, such as exposure to moisture or chemicals, remains a concern. It could impact the vehicle’s safety and structural stability over time.
- Repair Challenges:Unlike welding, repairing adhesive-bonded components requires specialized techniques and tools, making repairs more complex and potentially expensive.
- Initial Cost and Application Complexity: Incorporating adhesives into EV manufacturing demands specialized training and equipment, adding to the initial production cost.
Overcoming Challenges and Innovations
- Advanced Formulations:Researchers are constantly developing new adhesive formulations resistant to extreme temperatures and environmental conditions to enhance their durability and longevity.
- Technological Advancements:Emerging technologies, such as automated adhesive application systems and precise bonding techniques, aim to improve the application process and minimize errors.
- Hybrid Joining Techniques:Combining adhesives with mechanical fasteners or welding techniques can mitigate the drawbacks, ensuring a more robust bonding solution.
How does the application process of adhesives differ in electric cars compared to traditional vehicles?
The automotive industry is transforming towards electric vehicles (EVs), bringing forth innovative changes in manufacturing processes, including using adhesives. Adhesives play a pivotal role in traditional and electric cars, yet their application processes differ significantly, reflecting the unique demands of electric car design and production.
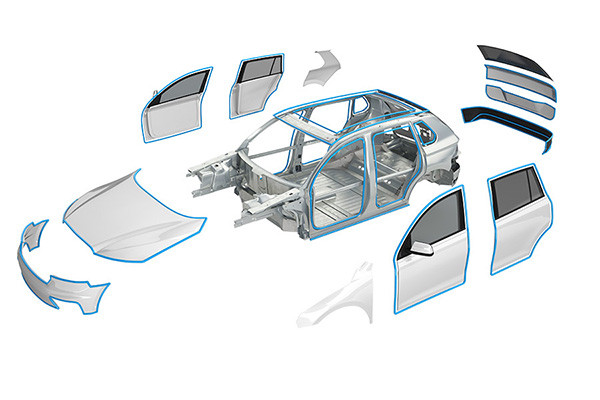
Traditional Vehicles: Conventional Adhesive Application
- Spot Welding Dominance:In traditional vehicles, spot welding has been a primary method for joining metal components, relying on intense heat to fuse materials.
- Manual Application:Adhesives, if used, were typically applied manually in specific areas to supplement welding, focusing on small-scale bonding or sealing purposes.
- Less Emphasis on Weight Reduction:Traditional vehicles often prioritize robustness over weight reduction, allowing less reliance on adhesives for structural integrity.
Electric Cars: Advanced Adhesive Integration
- Structural Reinforcement:Electric cars emphasize lightweight materials like aluminum and carbon fiber for increased efficiency. Adhesives play a more critical role in bonding these materials, providing structural reinforcement without compromising weight.
- Extensive Adhesive Usage:Adhesives in EVs cover larger surface areas, replacing or supplementing welding to a greater extent, contributing significantly to the vehicle’s overall strength and durability.
- Innovative Bonding Techniques:Automated adhesive application systems and precision bonding techniques are employed in EV manufacturing to ensure uniform and accurate distribution, optimizing the adhesive’s effectiveness.
Differences in Adhesive Application
- Material Compatibility:Electric car adhesives are formulated to bond diverse materials like aluminum and composites effectively, accommodating the unique materials used in EV construction.
- Weight Considerations: Adhesive application in EVs focuses on reducing weight while maintaining structural integrity, a crucial factor in maximizing the vehicle’s efficiency and range.
- Automation and Precision:Automated application systems in electric car manufacturing ensure consistent and precise adhesive placement, optimizing bonding effectiveness.
- Integration in Design:Adhesives are integral to the design process in electric cars, influencing structural layouts and component integration from the initial stages.
Future Directions and Innovations
- Adhesive Formulation Advancements:Continuous research aims to develop adhesives with improved durability, resilience to temperature variations, and enhanced bonding properties tailored explicitly for electric vehicle applications.
- Innovative Application Techniques:Ongoing advancements in application technologies seek to streamline the process, making it more efficient and cost-effective.
- Hybrid Bonding Solutions:Future trends may witness a combination of adhesive bonding with other techniques, such as mechanical fastening, to create hybrid solutions that offer enhanced strength and reliability.
Are there specific regulations or standards governing the use of adhesives in EV manufacturing?
In the ever-evolving landscape of electric vehicle (EV) manufacturing, adhesives play a crucial role in ensuring structural integrity, efficiency, and safety. As the automotive industry transitions toward greener solutions, questions arise regarding the regulations and standards governing the utilization of adhesives in EV manufacturing.
Key Points
Importance of Adhesives in Electric Cars
- Adhesives are vital in EV manufacturing, providing bonding solutions for lightweight materials like aluminum and carbon fiber.
- They contribute to reducing overall vehicle weight, enhancing fuel efficiency, and extending the driving range of electric cars.
Regulatory Framework for Adhesives in EVs
- Regulations vary across regions and countries, with some guidelines in place to ensure safety and quality standards.
- Organizations like the International Organization for Standardization (ISO) and the Society of Automotive Engineers (SAE) often develop standards and guidelines for adhesive use in automotive manufacturing.
Safety and Performance Standards
- Adhesives must meet stringent safety standards to withstand various stresses, including vibrations, temperature fluctuations, and collision impacts.
- These standards guarantee that adhesives maintain structural integrity throughout the vehicle’s lifespan.
Environmental Considerations
- With an increasing focus on sustainability, regulations may encompass environmental factors, encouraging eco-friendly adhesives with minimal ecological impact.
- This shift aligns with the broader goal of reducing the carbon footprint associated with manufacturing processes and the vehicle lifecycle.
Certification and Compliance
- Manufacturers typically need to comply with specific certifications or testing protocols to validate the quality and performance of adhesives used in EV production.
- Regular inspections and adherence to these standards are essential to ensure compliance and maintain high safety and quality standards.
Future Developments and Challenges
- As EV technology advances, regulations may evolve to address new materials, adhesive technologies, and their applications in electric vehicle manufacturing.
- Challenges persist in harmonizing global standards, given the diverse regulations across different markets, requiring concerted efforts from industry stakeholders and regulatory bodies.
What innovations can be expected in the field of electric car adhesives in the near future?
The future of electric car adhesives is teeming with possibilities, driven by the industry’s relentless pursuit of safer, more efficient, and environmentally sustainable solutions. These anticipated innovations promise to enhance electric vehicles’ performance and durability and signify a pivotal step toward reshaping the automotive industry’s landscape.
Core aspects
Advanced Bonding Materials
- Expect a surge in developing next-generation bonding materials explicitly tailored for electric car construction.
- Innovations might include stronger, lightweight adhesives designed to work seamlessly with diverse materials used in EVs, such as aluminum, carbon fiber, and composites.
Innovative Adhesives with Functionalities
- Anticipate the rise of ‘smart’ adhesives integrated with additional functionalities beyond bonding.
- These adhesives could embed sensors for structural health monitoring, offering real-time insights into the vehicle’s condition and structural integrity.
Increased Thermal Conductivity
- The focus will likely be on adhesives with enhanced thermal conductivity properties.
- This innovation is crucial for EVs as it facilitates better heat dissipation from critical components like batteries, contributing to their efficiency and longevity.
Self-Healing Adhesives
- Researchers are exploring self-healing adhesive technologies, which can autonomously repair minor damages, enhancing the durability and lifespan of bonded joints in electric cars.
Environmentally Conscious Adhesives
- Expect a continued push towards eco-friendly adhesives with reduced environmental impact.
- Innovations may involve bio-based adhesives derived from renewable sources, aligning with the sustainability goals of the EV industry.
3D Printing and Additive Manufacturing
- Integrating 3D printing and additive manufacturing techniques might revolutionize how adhesives are applied in electric car manufacturing.
- Customized bonding solutions could be developed on-site, optimizing the bonding process and reducing waste.
Adhesives for Autonomous Vehicles
- With the emergence of autonomous driving technology, adhesives may evolve to cater to the specific needs of self-driving vehicles.
- These adhesives might ensure robustness, reliability, and adaptability to support the intricate sensor systems and technologies required for autonomous driving.
Regulatory Compliance and Standardization
- As innovations progress, efforts will continue to align these advancements with stringent safety, quality, and regulatory standards.
- This emphasis on compliance will ensure the reliability and safety of new adhesive technologies in electric car manufacturing.
How cost-effective are these adhesives in the production of electric vehicles?
As the automotive industry surges toward sustainable alternatives, the electric vehicle (EV) sector stands out as a beacon of innovation. Within this realm, using electric car adhesives has emerged as a crucial factor in streamlining production processes and enhancing the cost-effectiveness of manufacturing electric vehicles.
The Role of Electric Car Adhesives
- Structural Integrity:Electric car adhesives are the backbone for maintaining structural integrity in EVs, ensuring components stay securely fastened.
- Weight Reduction:These adhesives contribute significantly to lightweighting, allowing automakers to reduce the overall weight of vehicles without compromising durability.
- Enhanced Safety:Unlike traditional welding methods, adhesives disperse stress across a larger area, improving crash performance and overall vehicle safety.
Cost Efficiency in EV Production
Electric car adhesives play a pivotal role in the cost efficiency of producing electric vehicles:
- Reduced Material Costs:Adhesives often require fewer materials compared to traditional joining methods like welding or fasteners, leading to decreased material expenses in the manufacturing process.
- Labor Savings:The application of adhesives can be quicker and more automated, reducing labor costs associated with assembly compared to intricate welding procedures.
- Energy Efficiency:As adhesives don’t require the intense heat associated with welding, they contribute to energy savings during manufacturing, thus lowering operational costs.
Environmental Impact and Long-Term Benefits
- Sustainability:Electric car adhesives are often formulated to be environmentally friendly, aligning with the sustainability goals of the EV industry.
- Extended Lifespan:Adhesives offer better corrosion resistance, extending the lifespan of EVs and reducing maintenance costs over time.
Challenges and Future Innovations
While electric car adhesives present numerous advantages, challenges persist:
- Rigorous Testing:Ensuring the durability and reliability of adhesives under varying conditions is crucial for long-term success.
- Technological Advancements:Continuous innovation is necessary to develop adhesives that withstand extreme temperatures, vibrations, and diverse environmental conditions.
Are there any significant differences in the adhesive requirements for various components of an electric car?
Amidst the innovative engineering and advanced technology powering these vehicles, the significance of adhesives often goes unnoticed. Yet, within electric cars, the adhesive materials used across various components play a pivotal role in their structural integrity and overall performance.
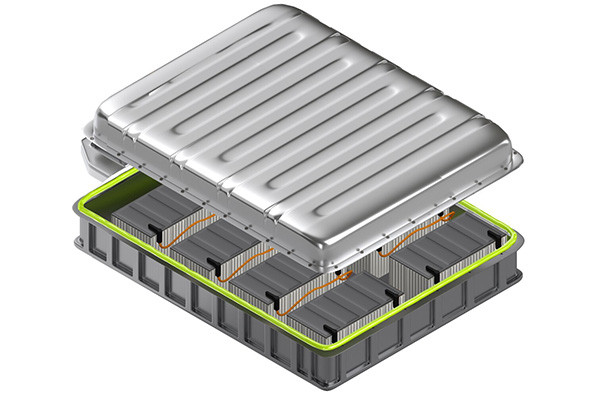
Are there substantial differences in adhesive requirements for the varied components of an electric car? Let’s delve into this intriguing aspect and unravel the nuances that make these adhesives indispensable:
Battery Systems
The heart of an electric vehicle lies in its battery system, and the adhesive requirements here are multifaceted:
- Thermal Conductivity:Adhesives must efficiently dissipate heat to ensure optimal battery performance and longevity.
- Chemical Resistance: Given the corrosive nature of battery components, adhesives need robust chemical resistance to maintain stability.
Body Structure
The structural integrity of an EV heavily relies on adhesive bonds within its body:
- Lightweighting:Adhesives aid in bonding lightweight materials, contributing to the vehicle’s overall weight reduction for enhanced efficiency.
- Crashworthiness:Adhesives reinforce structural components, which are pivotal in the vehicle’s safety and crash resistance.
Electric Motors and Drivetrain
Adhesives used in these critical components demand specialized characteristics:
- Vibration Damping:Adhesives must absorb vibrations and reduce noise to ensure smooth operation of the motor and drivetrain.
- High-Temperature Resistance:With the heat generated during operation, adhesives must withstand elevated temperatures without compromising performance.
Challenges and Innovations
While adhesive requirements vary across components, specific challenges persist in the EV industry:
- Compatibility:Ensuring compatibility between diverse materials used in EV components poses a challenge for adhesive selection.
- Environmental Sustainability:The push for eco-friendly solutions drives the need for adhesives with reduced environmental impact.
Innovation is underway to address these challenges
- Nanotechnology:Advancements in nanomaterials enhance adhesive properties, catering to specific requirements of EV components.
- Sustainable Formulations:Manufacturers are actively developing adhesives with renewable sources and reduced carbon footprint.
The Future Outlook
As the EV landscape evolves, the demand for specialized adhesives will continue to escalate:
- Customization:Tailoring adhesives to suit the unique requirements of different electric vehicle models will become more prevalent.
- Collaboration:Collaboration among automakers, adhesive manufacturers, and material scientists will drive innovations in this space.
How do adhesives contribute to noise reduction and vibration control in electric vehicles?
The automotive industry is accelerating towards a cleaner, greener future with the rise of electric vehicles (EVs). Alongside their eco-friendly advantages, EVs bring another significant benefit to the forefront: reduced noise pollution. Adhesives play a pivotal, albeit often overlooked, role in achieving this quieter driving experience, contributing to noise reduction and vibration control in electric cars.
Understanding the Significance
- Silent Revolution:Electric vehicles are inherently quieter than their combustion engine counterparts. However, they aren’t entirely noiseless. The absence of engine noise magnifies other sounds, like wind, tire, and road noise, making controlling these factors crucial for a serene cabin experience.
- Adhesive Solutions:Electric Car Adhesives, designed explicitly for EV manufacturing, are fundamental in curbing noise and controlling vibrations within these vehicles.
How Electric Car Adhesives Tackle Noise and Vibration
- Damping Vibrations:Adhesives act as damping agents, absorbing vibrations generated by various components in the vehicle. They mitigate the transfer of these vibrations, preventing them from spreading throughout the car’s structure.
- Enhancing Structural Integrity:These specialized adhesives reinforce the vehicle’s structural integrity by bonding different parts together. It reduces the likelihood of parts rattling or vibrating against each other, contributing to a quieter ride.
- Reducing Panel Resonance:Panels and components in an EV can produce unwanted noises due to resonance. Adhesives applied strategically dampen these resonating frequencies, minimizing the generation and transmission of noise.
Advantages of Adhesive Solutions in EVs
- Weight Efficiency:Unlike traditional mechanical fasteners, adhesives are lightweight, aiding in the overall weight reduction of EVs. It improves energy efficiency and contributes to a quieter ride by reducing weight-related vibrations.
- Flexibility in Design:Adhesives offer flexibility in design and manufacturing, allowing for seamless integration into the vehicle’s structure. This versatility enhances the car’s aerodynamics and noise reduction capabilities.
- Durability and Longevity:Electric Car Adhesives are engineered to withstand the unique demands of electric vehicles, ensuring durability over time. They maintain their effectiveness in noise reduction and vibration control, contributing to the longevity of the vehicle’s quiet performance.
The Future of Silent Mobility
As the automotive industry evolves, the focus on noise reduction in EVs will continue to grow. Electric Car Adhesives will undoubtedly play an increasingly vital role in achieving near-silent rides. Manufacturers continuously innovate adhesives, aiming for even better noise-dampening properties while ensuring they align with sustainability goals.
Can adhesives be recycled or reused in the EV manufacturing process?
As the world shifts towards sustainable mobility, electric vehicles (EVs) have emerged as a promising solution to reduce carbon emissions. Every component’s sustainability, including adhesives, in EV manufacturing plays a crucial role. The question arises: Can adhesives used in electric cars be recycled or reused within the manufacturing process? Let’s delve into this vital aspect of EV production.
Understanding Electric Car Adhesive Recycling
- Adhesive Composition:Electric Car Adhesives often consist of various materials, including polymers and compounds that provide bonding and structural integrity. These elements pose challenges for conventional recycling methods.
Challenges in Recycling Electric Car Adhesives
- Complexity of Composition:The intricate blend of materials in adhesives makes separating and recycling them difficult.
- Contamination Concerns:During their use, adhesives accumulate contaminants, consequently impacting their purity and rendering them unsuitable for recycling.
- Lack of Established Processes:Compared to other recyclable materials in automotive manufacturing, such as metals or plastics, established adhesive recycling processes are relatively limited.
Opportunities for Reusing Adhesives in EV Manufacturing
- Reclaimed Material Application:While direct recycling might pose challenges, repurposing adhesive materials in secondary applications within the manufacturing process holds promise.
- Remanufacturing:Adhesives from disassembled or decommissioned EVs could be reprocessed and utilized in non-critical components or secondary bonding applications during assembly.
Potential Solutions and Future Prospects
- Advancements in Recycling Technologies:Ongoing research focuses on developing innovative techniques to separate and recycle adhesive materials from end-of-life EVs efficiently.
- Circular Economy Integration:Implementing a circular economy approach encourages manufacturers to design adhesives with recyclability in mind, facilitating easier separation and reusability.
- Collaborative Initiatives:Collaborations between automotive companies, adhesive manufacturers, and recycling facilities can drive the development of standardized recycling processes for electric car adhesives.
Sustainable Impact and Benefits
- Environmental Conservation:Effective recycling or reusing of adhesives reduces waste and conserves resources, aligning with sustainability objectives.
- Resource Optimization:By repurposing adhesive materials, there’s potential to reduce the reliance on virgin materials in EV manufacturing, promoting resource efficiency.
What role will adhesives play in shaping the future of electric car technology?
As the automotive industry gears up for a profound transformation towards sustainability, electric vehicles (EVs) are at the forefront of this shift. Within the intricate framework of these innovative vehicles lies a crucial but often overlooked element – electric car adhesives. These compounds are set to play a pivotal role in shaping the future of electric car technology, offering a myriad of advantages that contribute to these vehicles’ efficiency, safety, and sustainability.
Enhanced Structural Integrity
- Weight Reduction:Adhesives enable the bonding of dissimilar materials, reducing the weight of EVs. It facilitates greater energy efficiency and extends the vehicle’s range.
- Strengthening Frames:Adhesives reinforce the structural integrity of electric cars, contributing to their durability and safety standards. It is particularly vital in crash safety and impact resistance.
Increased Efficiency and Performance
- Enhanced Thermal Management:Adhesives are crucial in managing heat distribution within electric vehicles, which optimizes battery performance and extends their lifespan.
- Improved Aerodynamics:By seamlessly bonding components, adhesives assist in creating smoother surfaces, reducing air resistance, and improving overall vehicle efficiency.
Advancements in Sustainability
- Reduced Emissions:The production and use of adhesives involve fewer emissions than traditional welding methods, aligning with the eco-friendly ethos of electric cars.
- Recyclability:Certain adhesives are designed for easy disassembly, facilitating component recycling and contributing to the circular economy in automotive manufacturing.
Innovation in Design and Manufacturing
- Flexibility in Design:Adhesives allow for more flexible designs, enabling the creation of unique and innovative vehicle shapes that were previously challenging to achieve.
- Streamlined Production Processes:Compared to welding, adhesive bonding offers faster and more precise assembly, contributing to more efficient manufacturing lines.
Safety and Comfort
- Noise and Vibration Dampening:Adhesives aid in reducing noise and vibrations, enhancing the overall comfort and driving experience for EV users.
- Corrosion Resistance:These compounds provide a protective layer, minimizing the risk of corrosion in electric vehicles, especially in components like battery enclosures.
The future of electric car technology is intricately linked with the evolution of adhesive technologies. However, challenges persist, such as ensuring the longevity and reliability of adhesive bonds under extreme conditions like temperature variations and high stress.
CONCLUSION
The evolution of the Electric Car Adhesive encapsulates a pivotal narrative within the electric vehicle revolution. As technology surges forward, these adhesives redefine manufacturing paradigms and epitomize the fusion of sustainability and innovation. Acknowledging their indispensable role in shaping EV design, safety, and efficacy, the future promises a tapestry of advancements and breakthroughs. It’s imperative to foster ongoing research and development, channeling the potential of Electric Car Adhesive toward a more sustainable, efficient, and transformative future for electric vehicles.
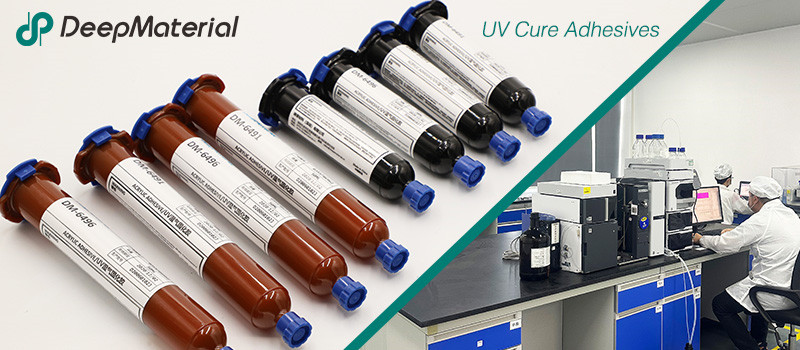
DeepMaterial
Based on the core technology of adhesives, DeepMaterial has developed adhesives for chip packaging and testing, circuit board level adhesives, and adhesives for electronic products. Based on adhesives, it has developed protective films, semiconductor fillers, and packaging materials for semiconductor wafer processing and chip packaging and testing. More…
UV Curing Adhesives
UV light cure have a number of benefits making them a popular choice among many product assembly and manufacturing applications. Many UV light cure adhesives can provide a nearly instantaneous bond to difficult substrates like glass and plastic. UV cure adhesives often require an accelerator or UV light for a bond to form.
Adhesive Blogs & News
The latest adhesive industry science and technology, Deepmaterial news, and market trends and forecasts.
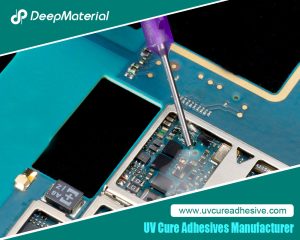
Biocompatibility of LED UV Glue Adhesive and Its Application Potential in Medical and Food Packaging Fields
Biocompatibility of LED UV Glue Adhesive and Its Application Potential in Medical and Food Packaging Fields LED UV glue adhesive has been widely applied in numerous fields due to its advantages such as rapid curing and easy operation. However, in fields with stringent safety requirements like medical and food packaging, its biocompatibility after curing becomes
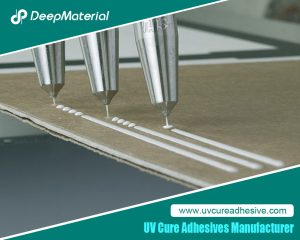
Biocompatibility of LED UV Glue Adhesive and Its Application Potential in Medical and Food Packaging Fields
Biocompatibility of LED UV Glue Adhesive and Its Application Potential in Medical and Food Packaging Fields LED UV glue adhesive has been widely applied in numerous fields due to its advantages such as rapid curing and easy operation. However, in fields with stringent safety requirements like medical and food packaging, its biocompatibility after curing
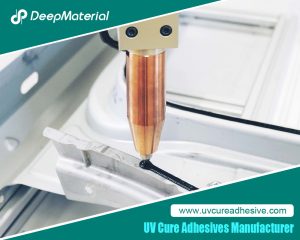
Exploring the Environmental Performance of UV Glue and Strategies for Optimizing Odor and VOC Content
Exploring the Environmental Performance of UV Glue and Strategies for Optimizing Odor and VOC Content UV glue, as an adhesive that achieves rapid curing through ultraviolet (UV) light irradiation, has been widely applied in numerous fields such as electronics, optics, healthcare, and automobiles, thanks to its advantages of fast curing speed, high bonding strength, and
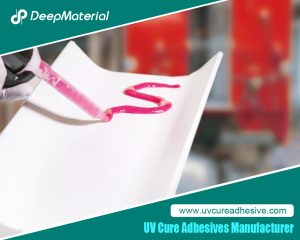
Compatibility Analysis and Countermeasures of LED UV Glue with Automated Production Equipment
Compatibility Analysis and Countermeasures of LED UV Glue with Automated Production Equipment LED UV glue has been widely used in modern manufacturing due to its advantages such as fast curing speed, high bonding strength, and environmental friendliness. However, in the automated production process, if there are problems with the adaptability between the glue and equipment
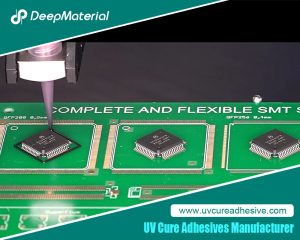
Influence of Viscosity and Thixotropy of Glue on the Quality of Glue Dots in the Dispensing Process and Solutions
Influence of Viscosity and Thixotropy of Glue on the Quality of Glue Dots in the Dispensing Process and Solutions The dispensing process is an important part of the application of LED UV glue adhesive, and the quality of this process directly affects the final performance of the product. The physical properties of the glue,
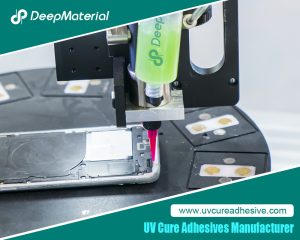
Aging Mechanism and Modification Strategies of LED UV Glue under Long-term Ultraviolet Irradiation
Aging Mechanism and Modification Strategies of LED UV Glue under Long-term Ultraviolet Irradiation LED UV glue, with its advantages of fast curing speed, high bonding strength, and environmental friendliness, has been widely used in fields such as optical device packaging, electronic assembly, and medical devices. However, in scenarios where it is exposed to ultraviolet environments