- Home
- >
- UV Cure Adhesive
- >
- UV Cure Silicone Adhesive
UV Cure Silicone Adhesive
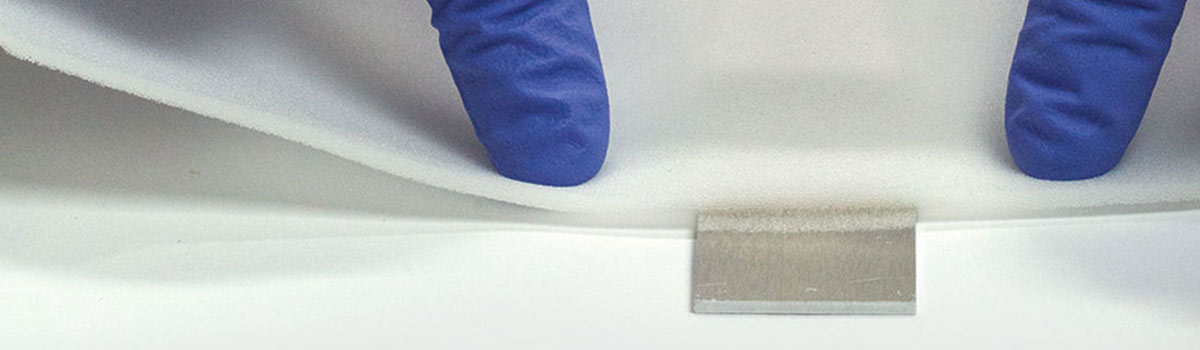
This innovative adhesive technology has revolutionized bonding processes, offering rapid curing and exceptional bonding strength. UV cure silicone adhesives find extensive applications in various industries, providing a reliable solution for bonding, sealing, and encapsulating diverse materials.
UV cure silicone adhesives are known for their versatility and efficiency. These adhesives offer quick assembly times and ensure a robust and durable bond by utilizing ultraviolet light for rapid curing. Whether you’re working on electronics, medical devices, or general manufacturing, UV cure silicone adhesives are a go-to choice for enhancing productivity and product performance.
Table of Contents
ToggleWhat is UV cure silicone adhesive?
UV-cure silicone adhesive is a type of adhesive that cures or hardens when exposed to ultraviolet (UV) light. Silicone adhesives are known for their flexibility, durability, and resistance to heat and chemicals. The UV-curing aspect adds a convenient and controlled curing process to the characteristics of silicone adhesives.
Here’s a brief overview of how UV-cure silicone adhesives typically work:
- Liquid State:The adhesive is initially liquid, making it easy to apply or coat onto surfaces.
- UV Exposure:Once the silicone adhesive is used, it requires exposure to ultraviolet light to initiate the curing process. UV light triggers a chemical reaction in the adhesive, causing it to polymerize and harden.
- Rapid Curing:The curing process is generally fast, often taking only a few seconds to minutes, depending on the specific product and the UV light intensity. This quick curing time is advantageous in various manufacturing processes, allowing for faster production cycles.
- Properties:UV-cure silicone adhesives retain the desirable properties of traditional silicone adhesives, such as flexibility, high-temperature resistance, and resistance to environmental factors. This makes them suitable for a wide range of applications.
UV-cure silicone adhesives find use in industries like electronics, medical devices, optics, and various manufacturing processes where a fast and controlled adhesive curing process is required. Curing on demand with UV light allows for precise bonding and sealing in applications where traditional curing methods might need to be more practical and time-consuming.
How does UV curing work in silicone adhesives?
UV curing in silicone adhesives is a process that involves the use of ultraviolet (UV) light to initiate and accelerate the curing (hardening) of the adhesive. Silicone adhesives are commonly used in various industries for bonding, sealing, and coating applications. The UV curing process in silicone adhesives typically follows these steps:
- Formulation of Silicone Adhesive:Silicone adhesives are initially formulated with photoinitiators. These chemicals are sensitive to UV light and can absorb UV radiation, leading to the initiation of the curing reaction.
- Application:The silicone adhesive is applied to the substrate or surfaces that need bonding or sealing. The adhesive is typically in a liquid or gel-like form at this stage.
- Exposure to UV Light:After application, the silicone adhesive is exposed to UV light. The light source is usually in the ultraviolet spectrum, with wavelengths typically between 200 and 400 nanometers. Commonly used UV sources include UV lamps or LEDs.
- Photoinitiator Activation:When the UV light comes into contact with the photoinitiators in the silicone adhesive, it triggers a chemical reaction. The photoinitiators absorb the UV radiation and undergo a photochemical reaction, generating free radicals or other reactive species.
- Curing Reaction:The generated free radicals or reactive species initiate the curing reaction in the silicone adhesive. The curing process involves the cross-linking of polymer chains in the adhesive, forming a three-dimensional network structure. This network structure is what gives the adhesive its cured and solid properties.
- Cured Silicone Adhesive:As the curing reaction progresses, the silicone adhesive hardens and forms a durable bond. The cured adhesive typically exhibits excellent adhesion, flexibility, and resistance to temperature, chemicals, and environmental factors.
The advantages of UV curing in silicone adhesives include fast curing times, reduced energy consumption, and the ability to control the curing process more precisely. UV curing is often associated with low-temperature curing, which is beneficial for heat-sensitive substrates. However, it’s important to note that the effectiveness of UV curing may depend on factors such as the adhesive formulation, substrate type, and specific application requirements.
What are the critical features of UV-cure silicone adhesives?
UV-cure silicone adhesives cure or set when exposed to ultraviolet (UV) light. These adhesives offer several critical features that make them suitable for various applications. Some of the key features include:
Rapid Curing:
- UV-cure silicone adhesives cure quickly when exposed to UV light, often in seconds or minutes. This fast curing time can significantly increase production efficiency.
Versatility:
- These versatile adhesives can bond to various substrates, including glass, metal, plastics, and ceramics.
Low Temperature Curing:
- UV-cure silicone adhesives typically cure at low temperatures, which is beneficial for heat-sensitive substrates and allows for use in a broader range of applications.
Low Volatility:
- Many UV-cure silicone adhesives have low volatility, minimizing the release of harmful fumes during the curing process. This can be important for applications where ventilation is limited.
Excellent Thermal Stability:
- UV-cure silicone adhesives often exhibit excellent thermal stability, maintaining their properties over a wide temperature range. This makes them suitable for applications that involve exposure to varying temperatures.
Flexibility and Elasticity:
- Silicone adhesives are known for their flexibility and elasticity. UV-cure silicone adhesives maintain these properties, providing durable and resilient bonds, especially in applications where movement or expansion and contraction are expected.
Chemical Resistance:
- Silicone adhesives, including UV-cure formulations, typically offer good resistance to chemicals, moisture, and weathering. This makes them suitable for outdoor applications or environments exposed to harsh conditions.
Optical Clarity:
- UV-cure silicone adhesives can offer optical clarity, making them ideal for applications where transparency or clarity is essential, such as in bonding glass or visual components.
Good Electrical Insulation:
- Silicone adhesives are known for their electrical insulation properties. UV-cure silicone adhesives can be used in electronic applications where insulation is critical.
Adhesion to Difficult Substrates:
- UV-cure silicone adhesives can provide strong adhesion to substrates traditionally challenging for other adhesive types, such as low-surface-energy materials.
Low Shrinkage:
- Many UV-cure silicone adhesives exhibit low shrinkage during curing, ensuring that the bonded components maintain their original dimensions.
It’s important to note that the specific features can vary between different formulations and manufacturers, so it’s advisable to consult the product datasheet or contact the manufacturer for detailed information on a particular UV-cure silicone adhesive.
In which industries are UV-cure silicone adhesives commonly used?
UV-cure silicone adhesives find applications in various industries due to their unique properties and curing mechanisms. Some of the sectors where UV-cure silicone adhesives are commonly used include:
- Electronics:In electronics, UV-cure silicone adhesives are used for bonding and sealing applications. They can provide excellent adhesion to electronic components without needing heat curing, which is beneficial for sensitive electronic devices.
- Medical Devices:These adhesives are used in the medical industry for bonding and sealing medical devices. Their biocompatibility and quick curing make them suitable for applications where fast assembly is essential.
- Optics:UV-cure silicone adhesives are used in the optics industry for bonding lenses, prisms, and other optical components. Their ability to cure rapidly under UV light helps quickly produce optical devices.
- Automotive:In the automotive industry, UV-cure silicone adhesives are employed for bonding and sealing applications. They are used in assembling various automotive components, such as sensors, lights, and electronic modules.
- Aerospace:UV-cure silicone adhesives find applications in the aerospace industry for bonding and sealing components. Their ability to cure quickly can be advantageous in producing aerospace systems and equipment.
- Consumer Electronics:The quick curing time of UV-cure silicone adhesives makes them suitable for assembly processes in the consumer electronics industry. They are used to manufacture products like smartphones, tablets, and other electronic devices.
- LEDs and Lighting:UV-cure silicone adhesives are commonly used to assemble LED components and lighting systems. They provide strong adhesion and are resistant to heat, making them suitable for these applications.
- Renewable Energy:In the renewable energy sector, UV-cure silicone adhesives are used for bonding and sealing components in solar panels and other energy systems. Their resistance to environmental factors and rapid curing contribute to efficient manufacturing processes.
It’s important to note that the use of UV-cure silicone adhesives continues to expand as technology advances and new applications are discovered. The unique properties of these adhesives make them valuable in situations where quick curing, flexibility, and high-performance bonding are essential.
What are the advantages of using UV-cure silicone adhesives over traditional adhesives?
UV-cure silicone adhesives offer several advantages over traditional adhesives, making them a popular choice in various industries. Here are some of the key advantages:
Rapid Cure Time:
- UV-cure silicone adhesives cure quickly when exposed to ultraviolet (UV) light. This allows for faster production processes, as the adhesive can cure within seconds or minutes.
Precise Control:
- The curing process of UV-cure adhesives is initiated and controlled by exposure to UV light. This allows for precise control over the curing time and process, minimizing the risk of over-curing or under-curing.
No Solvents or Volatile Organic Compounds (VOCs):
- UV-cure silicone adhesives typically do not contain solvents or VOCs, making them environmentally friendly. This can be particularly important in industries where solvent-based adhesives are restricted or regulated.
Low Heat Generation:
- UV-cure adhesives generate minimal heat during the curing process. This is advantageous when working with heat-sensitive materials, as it reduces the risk of damage or distortion.
Versatility:
- UV-cure silicone adhesives are versatile and can bond many substrates, including glass, metal, plastics, and ceramics. This versatility makes them suitable for diverse applications.
High Strength and Durability:
- Once cured, UV-cure silicone adhesives often exhibit high bond strength and durability. They can withstand various environmental conditions, including temperature extremes, moisture, and chemicals.
Improved Quality Control:
- The instantaneous cure of UV-cure adhesives allows for real-time quality control during manufacturing. Manufacturers can quickly assess the bond quality and make adjustments if needed.
Reduced Wastage:
- As UV-cure adhesives cure on-demand, there is less wastage than traditional adhesives that may continue to heal over time. This can result in cost savings and improved efficiency.
Enhanced Aesthetics:
- UV-cure adhesives often provide a clear and transparent bond line, improving the aesthetics of the final product. This is especially beneficial in applications where appearance is essential.
Reduced Labor Costs:
- The rapid curing nature of UV-cure adhesives can contribute to reduced labor costs as it allows for faster production cycles and shorter processing times.
It’s important to note that the suitability of UV-cure silicone adhesives depends on the application’s specific requirements, and considerations such as substrate compatibility, environmental conditions, and bonding strength should be considered when choosing an adhesive for a particular task.
Can UV-cure silicone adhesives bond different types of materials?
UV-cure silicone adhesives are versatile and can bond a variety of materials. These adhesives are known for forming strong bonds quickly when exposed to ultraviolet (UV) light. Here are some common materials that UV-cure silicone adhesives can bond:
- Glass:UV-cure silicone adhesives are often used to connect glass surfaces due to their transparency and ability to cure in the presence of UV light.
- Plastics:They can combine different types of plastics, including acrylics, polycarbonates, and some thermoplastics. However, the effectiveness may vary depending on the specific type of plastic.
- Metals:UV-cure silicone adhesives can bond various metals, such as aluminum, stainless steel, and others. The bond strength may depend on the surface condition and type of metal.
- Ceramics:These adhesives can effectively bond ceramic materials, providing a durable and robust bond.
- Wood:While not as common as other materials, UV-cure silicone adhesives can bond certain types of wood, especially when a transparent bond is desired.
- Rubber:They can click some kinds of rubber, but compatibility can vary depending on the adhesive’s specific formulation and the rubber type.
- Composites:UV-cure silicone adhesives can be suitable for bonding composite materials, such as fiberglass or carbon fiber.
It’s important to note that the effectiveness of the bond may depend on factors like surface preparation, the specific formulation of the adhesive, and the materials being bonded. Additionally, UV-cure adhesives may not be suitable for particular applications where shadowed areas prevent exposure to UV light during the curing process. Always follow the manufacturer’s guidelines and recommendations for your specific adhesive, and conduct compatibility tests if needed.
Are UV-cure silicone adhesives suitable for outdoor applications?
UV-cure silicone adhesives can be suitable for outdoor applications. Still, their performance may depend on the specific formulation of the adhesive and the environmental conditions to which it will be exposed. UV-cure silicone adhesives are known for their fast curing times and high bond strength, making them suitable for various applications.
However, it’s essential to consider the following factors when using UV-cure silicone adhesives for outdoor applications:
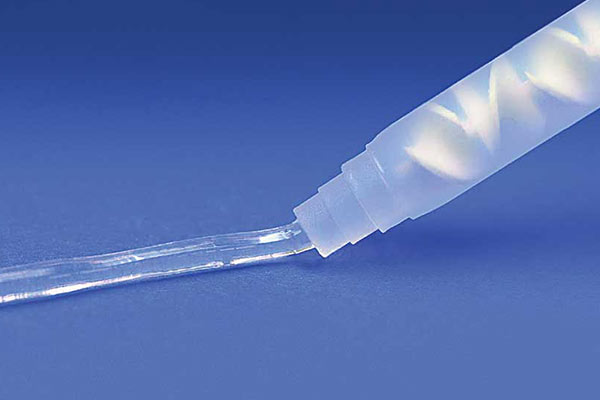
- UV Resistance:While these adhesives are cured with UV light, prolonged exposure to outdoor UV radiation can affect their long-term performance. Some formulations are designed to be more UV-resistant than others. Make sure to check the product specifications and choose an adhesive that is specifically labeled for outdoor use.
- Weather Resistance:Outdoor environments expose adhesives to weather conditions, including rain, temperature fluctuations, and humidity. Verify that the chosen UV-cure silicone adhesive has the weather resistance properties to withstand these conditions.
- Temperature Resistance:Consider the temperature variations in the outdoor environment. Some UV-cure adhesives may have temperature limitations, so choosing one that can withstand the expected temperature range is crucial.
- Moisture Resistance:Outdoor applications often involve exposure to moisture. Ensure the adhesive is formulated to resist water and moisture, preventing bond degradation over time.
- Substrate Compatibility:Verify that the UV-cure silicone adhesive is compatible with the materials it will bond. Different formulations may have varying adhesion properties on other surfaces.
- Manufacturer’s Recommendations:Always follow the manufacturer’s recommendations and guidelines for the specific UV-cure silicone adhesive you choose. This includes proper surface preparation, curing conditions, and other application-specific instructions.
It’s advisable to consult with the adhesive manufacturer or supplier to get specific recommendations based on your outdoor application requirements. Testing the adhesive in a small-scale, controlled outdoor environment before widespread use can provide valuable insights into its performance under real-world conditions.
How does temperature affect the curing process of UV-cure silicone adhesives?
Various factors influence the curing process of UV-cure silicone adhesives, and temperature is one of the critical parameters that can significantly impact the curing performance. Generally, the curing of UV-cure silicone adhesives involves using ultraviolet (UV) light to initiate a photochemical reaction, leading to the crosslinking of the silicone molecules and forming a solid and durable bond. Here’s how temperature can affect this process:
Reaction Rate:
- Higher Temperature:Generally, an increase in temperature accelerates chemical reactions. Higher temperatures can speed up the curing process of UV-cure silicone adhesives, as they provide more energy to the molecules, promoting faster crosslinking.
- Lower Temperature:Conversely, lower temperatures may slow down the curing reaction. This slowing effect might be desirable in some cases if a more controlled or extended curing time is needed.
Viscosity:
- Higher Temperature:Elevated temperatures can reduce the viscosity of the silicone adhesive, making it more fluid. This can be advantageous for applications with improved flow and wetting properties.
- Lower Temperature:Lower temperatures may increase the viscosity, making the adhesive thicker. This can be beneficial in vertical or overhead applications, as it helps prevent the adhesive from sagging or dripping.
Polymerization and Crosslinking:
- Higher Temperature:Increased temperature can facilitate the polymerization and crosslinking reactions, leading to a more complete and efficient curing process. However, excessively high temperatures may cause other issues, such as premature curing or thermal degradation.
- Lower Temperature:Cooler temperatures might hinder crosslinking, potentially resulting in incomplete curing. It’s essential to balance achieving a reasonable curing rate and avoiding adverse side effects.
Curing Uniformity:
- Temperature Control:Maintaining a consistent temperature during curing is crucial for uniform curing across the entire adhesive area. Inconsistent temperatures can lead to variations in curing rates and may result in uneven or incomplete curing.
It’s important to note that the optimal temperature for curing UV-cure silicone adhesives can vary based on the specific formulation of the adhesive, the intended application, and the manufacturer’s recommendations. Refer to the product’s technical data sheet for precise information on recommended curing conditions. Additionally, experimentation and testing under controlled conditions can help determine the ideal temperature for a particular application.
Are there specific safety considerations when working with UV-cure silicone adhesives?
Yes, working with UV-cure silicone adhesives requires specific safety considerations to ensure the individuals’ well-being. Here are some general safety guidelines:
Protective Equipment:
- Wear appropriate personal protective equipment (PPE) such as safety glasses, gloves, and, if necessary, a lab coat or apron.
- Ensure that PPE is compatible with the chemicals in the adhesive.
Ventilation:
- Use the adhesive in a well-ventilated area or local exhaust ventilation to minimize inhalation exposure.
- If working in a confined space, ensure proper ventilation or use a fume hood.
UV Exposure:
- UV-cure adhesives use ultraviolet light to cure. Avoid direct exposure to UV light, which can harm skin and eyes.
- Wear UV-blocking safety glasses or face shields designed for the specific wavelength emitted by the curing light.
Skin Protection:
- Prevent skin contact with the adhesive. If contact occurs, wash the affected area with soap and water immediately.
- Use barrier creams or gloves to protect the skin.
Eye Protection:
- In addition to UV-blocking glasses or face shields, consider using additional eye protection, such as safety goggles, to protect against splashes or accidental exposure.
Handling and Storage:
- Follow the manufacturer’s guidelines for handling, storage, and disposal of the adhesive.
- Store the adhesive in a cool, dry place and away from incompatible materials.
Emergency Procedures:
- Be familiar with emergency procedures, including the location of emergency showers, eye wash stations, and first aid kits.
- In case of accidental exposure, seek medical attention promptly.
Training:
- Ensure that personnel working with UV-cure silicone adhesives are adequately trained on safely handling and using these materials.
Read Material Safety Data Sheets (MSDS):
- Review the MSDS provided by the manufacturer for specific information on hazards, safe use, and emergency procedures related to the adhesive.
Always follow the specific safety recommendations provided by the manufacturer of the UV-cure silicone adhesive, as different products may have unique characteristics and requirements. If you need clarification on any aspect of working with these adhesives, consult the manufacturer or a safety professional for guidance.
What are the curing times and conditions for UV-cure silicone adhesives?
The curing times and conditions for UV-cure silicone adhesives vary depending on the product and formulation. UV-cure silicone adhesives are typically designed to cure rapidly when exposed to ultraviolet (UV) light. Here are some general guidelines, but it’s essential to refer to the manufacturer’s instructions and technical data sheet for accurate information:
Light Source:
- UV-cure silicone adhesives require exposure to a UV light source for curing.
- The curing process is initiated by UV light, and the adhesive will remain in a liquid or semi-liquid state until exposed to the appropriate light wavelength.
Intensity and Wavelength:
- The intensity and wavelength of the UV light can influence the curing time.
- Ensure that the UV light source used meets the specifications recommended by the adhesive manufacturer.
Curing Time:
- Curing times can range from a few seconds to several minutes, depending on the adhesive and application.
- Thicker layers may require longer curing times.
Temperature:
- UV-cure silicone adhesives may be sensitive to temperature. Some formulations may cure more effectively at elevated temperatures.
- Check the manufacturer’s recommendations for the optimum curing temperature.
Substrate:
- The type of substrate can also affect curing times. Some materials may inhibit or slow down the curing process.
Clean Surfaces:
- Ensure that the surfaces to be bonded are clean and free from contaminants, as this can affect adhesion and curing.
Adhesive Thickness:
- The thickness of the adhesive layer can impact curing times. Thicker layers may require more exposure time to UV light.
Safety Considerations:
- Follow the adhesive manufacturer’s safety guidelines, including wearing appropriate protective gear when handling UV-cure adhesives and using UV light sources.
Always refer to the specific technical data sheet or instructions provided by the manufacturer for accurate information on curing times and conditions for a particular UV-cure silicone adhesive. The manufacturer’s recommendations are crucial for achieving the best performance and ensuring the adhesive’s proper curing.
Can UV-cure silicone adhesives withstand extreme environmental conditions?
UV-cure silicone adhesives are known for their versatility and are used in various applications due to their excellent adhesion, flexibility, and resistance to temperature extremes. However, the specific performance of a UV-cure silicone adhesive in extreme environmental conditions can depend on the formulation of the adhesive and the nature of the conditions.
Here are some general points to consider:
- Temperature Resistance:Silicone adhesives, in general, have suitable temperature resistance. They can withstand both high and low temperatures. However, the specific temperature range will depend on the formulation of the adhesive. Some UV-cure silicone adhesives may be designed to withstand extreme temperatures, making them suitable for applications in harsh environments.
- UV Resistance:UV-cure adhesives are formulated to cure quickly when exposed to ultraviolet (UV) light. While the cured adhesive may resist UV exposure, prolonged and intense UV radiation can degrade the material. If the application involves continuous exposure to sunlight or other strong UV sources, choosing an adhesive specifically designed for UV resistance is essential.
- Chemical Resistance:Silicone adhesives, including UV-cure formulations, generally exhibit good chemical resistance. However, the specific resistance to certain chemicals will depend on the formulation. It’s essential to check the manufacturer’s specifications and choose an adhesive that meets the requirements of the intended environment.
- Flexibility:Silicone adhesives are known for their flexibility and elasticity, which makes them suitable for applications where movement or vibration is expected. This property can contribute to their ability to withstand environmental stresses.
- Moisture Resistance:Silicone adhesives are typically resistant to moisture and humidity. This makes them suitable for applications where exposure to water or high humidity is a concern.
- Adhesion Strength:The adhesive’s ability to bond to different substrates is crucial. UV-cure silicone adhesives are generally known for good adhesion to various surfaces, but the specific formulation may affect adhesion strength.
When considering UV-cure silicone adhesives for extreme environmental conditions, it’s essential to consult with the adhesive manufacturer, review product datasheets, and conduct testing if necessary. Some manufacturers may offer specialty formulations to meet specific requirements, such as increased temperature resistance or enhanced UV stability.
Are there specific storage requirements for UV-cure silicone adhesives?
Like many other materials, UV-cure silicone adhesives may have specific storage requirements to ensure their stability and effectiveness. Following the manufacturer’s storage guidelines is essential to maintain the adhesive’s performance and prevent premature curing or degradation. Here are some general considerations:
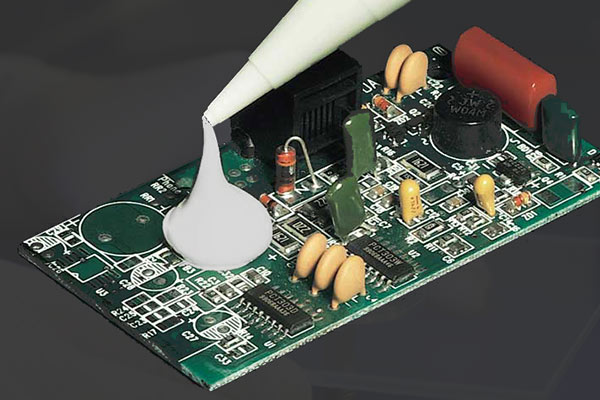
- Temperature:Store UV-cure silicone adhesives within the recommended temperature range specified by the manufacturer. Extreme temperatures can affect the adhesive’s properties. Typically, they should be stored in a cool, dry place.
- Light Exposure:UV-cure adhesives cure upon exposure to ultraviolet (UV) light. It’s crucial to keep them in opaque containers to prevent unintended curing. Exposure to ambient light or UV radiation can lead to premature curing and reduce the adhesive’s shelf life.
- Moisture:Moisture can also impact the performance of silicone adhesives. Ensure the storage environment is dry, and the adhesive is protected from direct contact with water or high humidity.
- Container Sealing:Keep the adhesive containers tightly sealed when not in use. This helps prevent moisture and air from entering the container, which can affect the adhesive’s properties.
- Shelf Life:UV-cure silicone adhesives typically have a limited shelf life. Be aware of the expiration date provided by the manufacturer, and use the adhesive before it expires for optimal performance.
- Chemical Compatibility:Store UV-cure silicone adhesives away from incompatible chemicals to prevent any reactions that could compromise the adhesive’s quality.
Always refer to the specific product datasheet, technical data, or instructions provided by the manufacturer for precise storage recommendations. Following these guidelines will help ensure that the UV-cure silicone adhesive remains effective and reliable for its intended applications.
What substrates are compatible with UV-cure silicone adhesives?
UV-cure silicone adhesives are known for their quick curing times and versatility. However, the compatibility of these adhesives with specific substrates can vary. It’s crucial to consult the manufacturer’s recommendations and conduct compatibility tests to ensure optimal performance. Generally, UV-cure silicone adhesives can bond well with a variety of substrates, including:
- Glass:UV-cure silicone adhesives often adhere well to glass surfaces, making them suitable for glass bonding or sealing applications.
- Metals:Many UV-cure silicone adhesives can bond to various metals, providing good adhesion to aluminum, stainless steel, and other metal surfaces.
- Ceramics:These adhesives can be compatible with ceramic materials, making them suitable for bonding or sealing applications in ceramic-based products.
- Plastics:UV-cure silicone adhesives may bond well to certain plastics, including acrylics, polycarbonates, and other thermoplastics. However, compatibility can vary, so testing is essential.
- Certain Rubbers:Some UV-cure silicone adhesives are compatible with specific rubber materials. However, compatibility can be substrate-specific, so checking with the adhesive manufacturer is essential.
- Wood:Depending on the formulation, UV-cure silicone adhesives may exhibit good adhesion to wood surfaces.
It’s important to note that while UV-cure silicone adhesives have broad compatibility, the specific formulation and application requirements can influence their performance on different substrates. Additionally, surface preparation, cleanliness, and contaminants can impact the bonding effectiveness. Refer to the product datasheet or contact the manufacturer for detailed information on substrate compatibility and application guidelines. Conducting small-scale compatibility tests on representative substrates is advisable to ensure the adhesive meets the specific requirements of your application.
Can UV-cure silicone adhesives be used in medical applications?
UV-cure silicone adhesives can be suitable for specific medical applications, but their use in such contexts depends on several factors and considerations. UV-cure adhesives, including those based on silicone, are known for their fast curing times and the ability to create strong bonds. However, some specific requirements and standards must be met to ensure safety and efficacy when it comes to medical applications.
Here are some factors to consider:
- Biocompatibility:Medical-grade adhesives must be biocompatible, meaning they should not cause adverse reactions when in contact with living tissues. Choosing UV-cure silicone adhesives that have been tested and certified for biocompatibility according to relevant standards, such as ISO 10993, is crucial.
- Regulatory Compliance:Medical devices and materials are subject to strict regulatory requirements in various regions, such as the U.S. Food and Drug Administration (FDA) in the United States and the European Medicines Agency (EMA) in the European Union. Ensure that the UV-cure silicone adhesive complies with the applicable regulations for medical use.
- Sterilization Compatibility:Medical devices often need to undergo sterilization processes. Check whether the UV-cure silicone adhesive is compatible with the sterilization methods required for specific medical applications, such as autoclaving or gamma irradiation.
- Chemical Resistance:Depending on the medical application, the adhesive should resist degradation from bodily fluids, cleaning agents, or other substances it might contact.
- Mechanical Properties:Assess whether the cured adhesive meets the mechanical requirements for the intended medical application. This includes flexibility, tensile strength, and adherence to different substrates.
Before using any adhesive in a medical setting, it is advisable to consult with the adhesive manufacturer and, if necessary, seek guidance from regulatory authorities. Additionally, involving a materials or biomedical engineer in the decision-making process can help ensure that the chosen adhesive meets the specific needs of the medical application and complies with relevant standards and regulations.
Are there color options available for UV-cure silicone adhesives?
UV-cure silicone adhesives are known for their fast curing time and versatility, making them suitable for various applications. Regarding color options for UV-cure silicone adhesives, it’s important to note that the availability of colors may depend on the specific product and manufacturer.
In general, UV-cure silicone adhesives are often transparent or clear in their uncured state. However, some manufacturers offer colored variations for specific applications. Standard colors include white, black, and various shades of gray. The choice of color can be crucial in applications where aesthetics or visibility are factors.
Suppose you have a specific color requirement for your project. In that case, check with adhesive manufacturers or suppliers to see if they offer UV-cure silicone adhesives in the desired color. Remember that the availability of colors may vary, and not all manufacturers may provide a wide range of options.
Additionally, it’s essential to consider the compatibility of the colored adhesive with your application requirements, as certain additives used for coloration might affect the adhesive’s properties. Always consult the product datasheet or technical specifications provided by the manufacturer for detailed information on the adhesive’s characteristics, curing properties, and suitability for your specific needs.
How do UV-cure silicone adhesives contribute to product design flexibility?
UV-cure silicone adhesives offer several advantages that contribute to product design flexibility. Here are some key aspects:
- Rapid Cure Time:UV-cure silicone adhesives cure quickly when exposed to ultraviolet (UV) light. This fast-curing process enables quick assembly and production, reducing overall manufacturing time. Manufacturers can achieve higher throughput and efficiency in the production line, allowing for more flexibility in adjusting production schedules and meeting tight deadlines.
- Precise Application:UV-cure adhesives provide precise control over the application process. They remain in liquid until exposed to UV light, allowing for accurate positioning and alignment of components before the curing process begins. This precision is crucial in applications where fine details or intricate designs are essential.
- Reduced Heat Generation:Unlike some other curing methods, UV curing generates minimal heat. This is particularly advantageous when working with temperature-sensitive materials or components. The low heat generation helps prevent damage to sensitive electronic components, plastics, or other materials that might be negatively affected by high temperatures during the curing process.
- Common Volatile Organic Compounds (VOCs):UV-cure silicone adhesives typically have low or no volatile organic compounds. This is important for meeting environmental and regulatory requirements. The absence of VOCs contributes to a cleaner and healthier working environment, making these adhesives suitable for various industries and applications.
- Versatility in Substrate Bonding:UV-cure silicone adhesives exhibit strong adhesion to many substrates, including glass, metals, plastics, and ceramics. This versatility allows designers to use these adhesives in diverse applications, providing flexible material selection for product components.
- Improved Process Control:The curing process of UV-cure adhesives can be easily controlled and adjusted, allowing designers to fine-tune the bonding characteristics based on specific application requirements. This level of control enhances the overall design flexibility and allows for customization to meet the needs of different products.
- Minimal Residue and Cleanability:UV-cure adhesives often leave minimal residue after curing. This characteristic simplifies the cleaning process and ensures that finished products look clean and aesthetically pleasing. This feature contributes to the overall design quality in applications where cosmetic aspects are crucial.
- Adaptability to Automation:The fast-curing nature of UV-cure silicone adhesives makes them well-suited for automated manufacturing processes. Automated dispensing and curing systems can be easily integrated into production lines, enabling high-volume and consistent production. This adaptability to automation enhances the scalability and flexibility of the manufacturing process.
UV-cure silicone adhesives provide designers with various benefits, including rapid curing, precise application, compatibility with multiple substrates, and environmental advantages. These characteristics contribute to increased product design flexibility across various industries.
Can UV-cure silicone adhesives be used for transparent bonding?
Yes, UV-cure silicone adhesives can be used for transparent bonding. UV-cure silicone adhesives are designed to cure or harden quickly when exposed to ultraviolet (UV) light. These adhesives are often used in applications where transparency is essential, such as bonding glass, plastics, and other transparent materials.
The critical advantage of UV-cure adhesives, including silicone-based ones, is their rapid curing time. When exposed to UV light, the adhesive can cure within seconds, creating a strong and transparent bond. This makes them suitable for applications requiring a fast and transparent bond.
It’s important to note that the specific properties of UV-cure silicone adhesives can vary between different formulations and manufacturers. Before using any adhesive for a particular application, it’s recommended to check the product specifications and guidelines provided by the manufacturer to ensure it meets the requirements of your project. Proper surface preparation and adhesive application techniques are crucial for achieving the desired bond strength and transparency.
What testing and quality control measures are associated with UV-cure silicone adhesives?
UV-cure silicone adhesives cure or harden when exposed to ultraviolet (UV) light. These adhesives are commonly used in various applications, including electronics, medical devices, and industrial bonding. To ensure the quality and performance of UV-cure silicone adhesives, several testing and quality control measures are typically employed:
Curing Time and Intensity Testing:
- Determine the optimal UV curing time and intensity required for the silicone adhesive. This involves testing different exposure times and UV light intensities to find the conditions that result in the best cure.
Viscosity Measurement:
- Monitor the viscosity of the uncured adhesive. Proper viscosity ensures easy application and good wetting of the bonded surfaces.
Adhesive Strength Testing:
- Assess the adhesive strength of cured samples. Depending on the application requirements, this can be done through various methods, such as peel, shear, or tensile testing,
Adhesion Testing:
- Evaluate the adhesive’s ability to bond to different substrates commonly used in the specific application. This includes testing on materials like metals, plastics, glass, and ceramics.
Shore Hardness Testing:
- Measure the hardness of the cured adhesive using a Shore hardness test. This helps ensure that the adhesive provides the desired hardness level for the application.
Chemical Resistance Testing:
- Examine the resistance of the cured adhesive to various chemicals it might encounter in its intended use. This is important for applications where the adhesive will be exposed to harsh environments.
Temperature Resistance Testing:
- Evaluate the performance of the adhesive under different temperature conditions. This is crucial in applications where the adhesive will be exposed to extreme temperatures.
UV Light Stability Testing:
- Assess the stability of the cured adhesive when exposed to prolonged UV light. This is important for applications that expose the adhesive to outdoor conditions.
Color Stability Testing:
- Evaluate the color stability of the cured adhesive over time, mainly if the adhesive is used in applications where aesthetics are essential.
Batch-to-Batch Consistency:
- Implement strict quality control measures to ensure consistency in the properties of the adhesive from one manufacturing batch to another.
Packaging and Storage Testing:
- Assess the impact of packaging and storage conditions on the adhesive’s performance. This includes evaluating the shelf life and stability of the uncured adhesive.
Regulatory Compliance Testing:
- Ensure the UV-cure silicone adhesive complies with relevant industry standards and regulations, mainly if used in medical device applications.
Regular and thorough testing throughout the production process helps guarantee the quality and reliability of UV-cure silicone adhesives in their intended applications.
Are there any limitations or considerations for using UV-cure silicone adhesives?
UV-cure silicone adhesives offer several advantages, such as rapid curing, low-temperature processing, and bonding of various substrates. However, like any material, they also have limitations and considerations that should be taken into account:
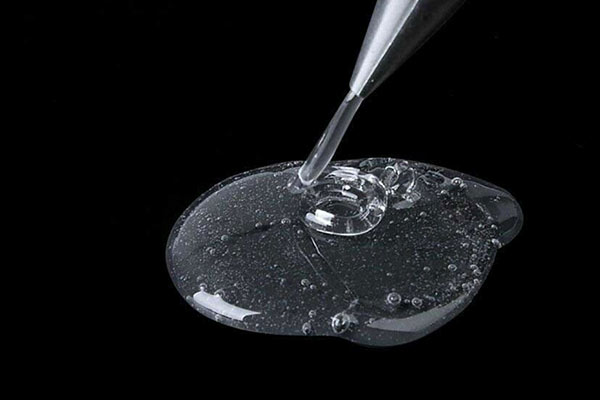
- UV Exposure:UV-cure silicone adhesives require exposure to ultraviolet (UV) light for curing. Adequate exposure is crucial to achieving the desired bond strength. Only complete curing may occur in shadowed areas or where the adhesive is adequately exposed to UV light.
- Substrate Compatibility:While UV-cure silicones can bond to various substrates, it’s essential to ensure compatibility with the specific materials involved in your application. Some substrates may be more challenging to bond than others, and surface preparation may be necessary to enhance adhesion.
- Temperature Sensitivity:UV-cure silicone adhesives may be sensitive to high temperatures during curing. Excessive heat can affect the performance of the adhesive or lead to incomplete curing. It’s essential to follow the manufacturer’s recommendations regarding temperature conditions.
- Thickness of Adhesive Layer:The curing process of UV-cure adhesives is influenced by the thickness of the adhesive layer. Thick layers may not cure as effectively as thin layers due to limited penetration of UV light. Manufacturers typically provide guidelines on the recommended thickness for optimal curing.
- Moisture Sensitivity:Some UV-cure silicone adhesives can be sensitive to moisture. Exposure to moisture during the curing process may impact the adhesive’s performance. Ensure the application environment is dry and moisture-free to achieve optimal results.
- UV Light Source:The type and intensity of the UV light source used for curing can affect the performance of UV-cure silicone adhesives. It’s essential to use a UV light source that matches the adhesive’s specifications and to follow the manufacturer’s guidelines for exposure times.
- Shelf Life:UV-cure adhesives typically have a limited shelf life. Ensure that you use the adhesive within its recommended storage period to avoid potential issues with curing and performance.
- Health and Safety Considerations:UV light can harm the skin and eyes. Take appropriate safety precautions, such as wearing protective equipment like gloves and goggles, and follow safety guidelines provided by the adhesive manufacturer.
Always refer to the specific product datasheet and technical documentation provided by the manufacturer for detailed information on the limitations, considerations, and optimal usage conditions of a particular UV-cure silicone adhesive.
Where can one purchase high-quality UV-cure silicone adhesives?
Remember that specific products, suppliers, and availability may have changed since then. Here are some general avenues where you can explore:
Specialty Chemical Suppliers:
- Companies specializing in manufacturing and distributing specialty chemicals often carry UV-cure silicone adhesives. Examples include Momentive, Dow, and Henkel.
Industrial Suppliers and Distributors:
- Industrial supply stores or distributors catering to manufacturing and assembly industries may stock UV-cure adhesives. Examples include Grainger or McMaster-Carr.
Online Marketplaces:
- Online platforms like Amazon, Alibaba, or specialized industrial supply websites often have a variety of UV-cure silicone adhesives. Review product specifications, read customer reviews, and purchase from reputable sellers.
Adhesive Specialty Stores:
- Some stores specialize in adhesives and sealants. Check with local or online specialty stores that focus on providing a wide range of adhesive solutions.
Manufacturer’s Websites:
- Visit the official websites of well-known adhesive manufacturers. Many manufacturers have online catalogs and product information to help you find the suitable UV-cure silicone adhesive for your application.
Local Distributors and Dealers:
- Contact local distributors or dealers that supply industrial adhesives. They may have partnerships with major manufacturers and can assist you in finding the right product.
Trade Shows and Exhibitions:
- Attend industry-specific trade shows, conferences, or exhibitions related to adhesives, sealants, or manufacturing. These events often feature multiple suppliers and provide opportunities for networking and product exploration.
Specialty Adhesive Manufacturers:
- Some manufacturers specialize exclusively in adhesives and sealants. Research and contact companies focusing on specialty adhesives to inquire about their UV-cure silicone offerings.
Before making a purchase, consider factors such as the specific requirements of your application, product specifications, and the supplier’s or manufacturer’s reputation. It’s essential to review technical data sheets and safety information provided by the supplier. Additionally, inquire about their customer support, shipping options, and return policies. Always ensure that the product meets your specific needs and standards.
Conclusion:
In conclusion, introducing UV-cure silicone adhesives has transformed the world of adhesives. This cutting-edge technology offers a fast, reliable, and versatile solution for bonding across various industries. UV curing efficiency, coupled with silicone’s exceptional adhesive properties, makes UV cure silicone adhesives a preferred choice for applications ranging from electronics to medical devices.
The advantages of rapid curing times, strong bonding capabilities, and adaptability to diverse substrates position UV cure silicone adhesives as a game-changer in manufacturing processes. The ability to withstand challenging environmental conditions, coupled with their compatibility with different materials, adds to the appeal of these adhesives.
As we navigate the ever-evolving landscape of materials and technologies, UV cure silicone adhesives stand out as a key player in enhancing product design flexibility and performance. Whether you are an engineer, manufacturer, or hobbyist, exploring the potential of UV cure silicone adhesives opens doors to innovative and efficient bonding solutions.
UV-cure silicone adhesives have made their mark in adhesives, promising a future where bonding is strong but also swift and adaptable. Embrace the power of UV cure silicone adhesives and unlock new possibilities in your projects and applications.
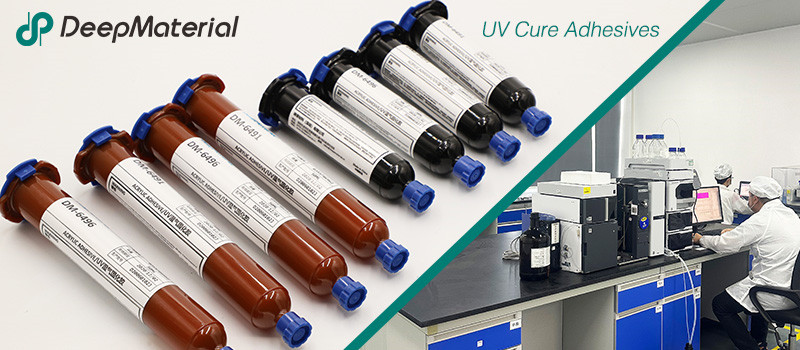
DeepMaterial
Based on the core technology of adhesives, DeepMaterial has developed adhesives for chip packaging and testing, circuit board level adhesives, and adhesives for electronic products. Based on adhesives, it has developed protective films, semiconductor fillers, and packaging materials for semiconductor wafer processing and chip packaging and testing. More…
UV Curing Adhesives
UV light cure have a number of benefits making them a popular choice among many product assembly and manufacturing applications. Many UV light cure adhesives can provide a nearly instantaneous bond to difficult substrates like glass and plastic. UV cure adhesives often require an accelerator or UV light for a bond to form.
Adhesive Blogs & News
The latest adhesive industry science and technology, Deepmaterial news, and market trends and forecasts.
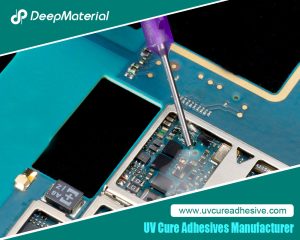
Technical Strategies for Balancing the Rapid Curing Property and Long Operating Time of UV Adhesives
Technical Strategies for Balancing the Rapid Curing Property and Long Operating Time of UV Adhesives UV adhesives have been widely used in many fields such as electronics, optics, and medicine due to their advantages of rapid curing, high bonding strength, and environmental protection. However, their rapid curing property also brings challenges in some application scenarios.
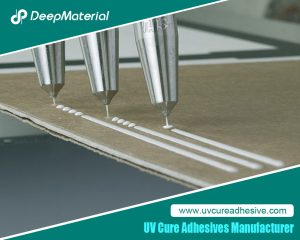
Biocompatibility of LED UV Glue Adhesive and Its Application Potential in Medical and Food Packaging Fields
Biocompatibility of LED UV Glue Adhesive and Its Application Potential in Medical and Food Packaging Fields LED UV glue adhesive has been widely applied in numerous fields due to its advantages such as rapid curing and easy operation. However, in fields with stringent safety requirements like medical and food packaging, its biocompatibility after curing
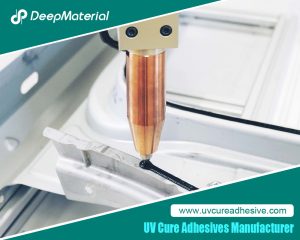
Exploring the Environmental Performance of UV Glue and Strategies for Optimizing Odor and VOC Content
Exploring the Environmental Performance of UV Glue and Strategies for Optimizing Odor and VOC Content UV glue, as an adhesive that achieves rapid curing through ultraviolet (UV) light irradiation, has been widely applied in numerous fields such as electronics, optics, healthcare, and automobiles, thanks to its advantages of fast curing speed, high bonding strength, and
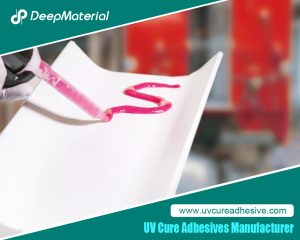
Compatibility Analysis and Countermeasures of LED UV Glue with Automated Production Equipment
Compatibility Analysis and Countermeasures of LED UV Glue with Automated Production Equipment LED UV glue has been widely used in modern manufacturing due to its advantages such as fast curing speed, high bonding strength, and environmental friendliness. However, in the automated production process, if there are problems with the adaptability between the glue and equipment
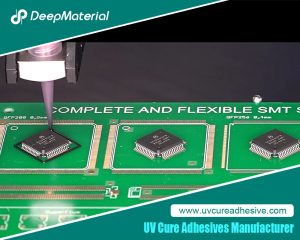
Influence of Viscosity and Thixotropy of Glue on the Quality of Glue Dots in the Dispensing Process and Solutions
Influence of Viscosity and Thixotropy of Glue on the Quality of Glue Dots in the Dispensing Process and Solutions The dispensing process is an important part of the application of LED UV glue adhesive, and the quality of this process directly affects the final performance of the product. The physical properties of the glue,
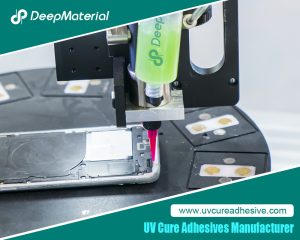
Aging Mechanism and Modification Strategies of LED UV Glue under Long-term Ultraviolet Irradiation
Aging Mechanism and Modification Strategies of LED UV Glue under Long-term Ultraviolet Irradiation LED UV glue, with its advantages of fast curing speed, high bonding strength, and environmental friendliness, has been widely used in fields such as optical device packaging, electronic assembly, and medical devices. However, in scenarios where it is exposed to ultraviolet environments