- Home
- >
- UV Cure Adhesive
- >
- UV Cure Polyurethane Adhesive
UV Cure Polyurethane Adhesive
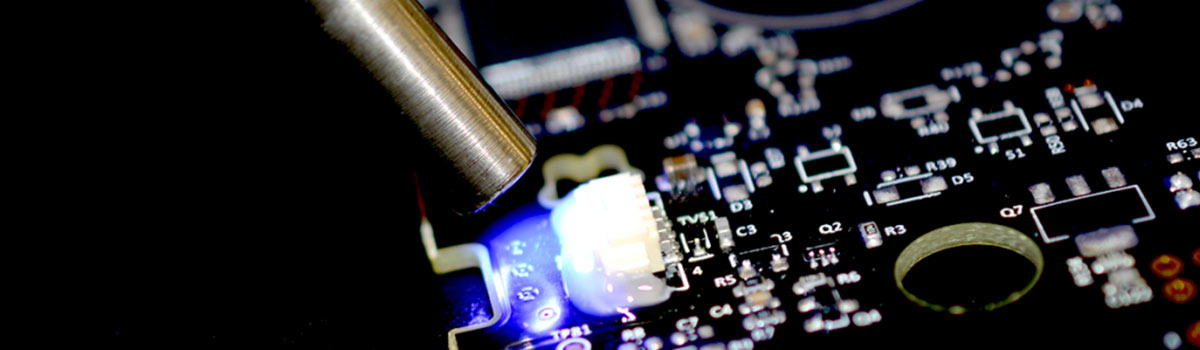
UV cure polyurethane adhesives offer a unique combination of versatility, strength, and efficiency. These adhesives are cured using ultraviolet light, providing rapid bonding for various applications. Whether you are in the manufacturing industry, doing DIY projects, or practicing professional craftsmanship, understanding the nuances of UV-cure polyurethane adhesives is crucial.
Table of Contents
ToggleWhat is UV-cure polyurethane adhesive?
UV-cure polyurethane adhesive is an adhesive that cures or hardens when exposed to ultraviolet (UV) light. Polyurethane adhesives are known for their strong bonding properties and versatility. They are widely used in various industries for bonding different materials, such as plastics, metals, glass, and wood.
The UV-curing aspect of the adhesive refers to the curing mechanism. When the adhesive is exposed to UV light, typically in the ultraviolet A (UVA) or ultraviolet B (UVB) range, a chemical reaction is initiated that leads to the hardening or curing of the adhesive. This process is often rapid, allowing for quick bonding and fixing of materials.
Here are some key characteristics and advantages of UV-cure polyurethane adhesives:
- Fast Curing:UV-cure polyurethane adhesives can cure very quickly, often within seconds to minutes, depending on the intensity of the UV light source.
- Precision:The curing process is highly controllable, providing precise control over the bonding process. This is particularly useful in applications where accurate positioning or alignment of parts is crucial.
- Low Heat Generation:UV curing generates minimal heat compared to other curing methods, which is beneficial when working with heat-sensitive materials.
- Common Volatile Organic Compounds (VOCs):UV-cure adhesives generally have lower VOC emissions than solvent-based adhesives, contributing to environmental and workplace safety.
- Bond Strength:Polyurethane adhesives are known for their muscular bond strength, and the UV-curing mechanism enhances their performance in bonding various substrates.
- Versatility:These adhesives can be used in multiple applications, including electronics, automotive, medical devices, and more, due to their versatility in bonding different materials.
It’s important to note that while UV-cure polyurethane adhesives offer many advantages, they may only be suitable for some applications. Factors such as substrate compatibility, bond strength requirements, and the need for UV light exposure should be considered when choosing an adhesive for a specific use case.
How does the UV curing process work?
UV curing is a process in which ultraviolet (UV) light is used to instantly cure or dry inks, coatings, adhesives, and other materials. This technique is commonly employed in various industries, such as printing, electronics, automotive, and medical devices. The UV curing process involves several key components:
UV Light Source:
- UV lamps or LED lights are used as the source of ultraviolet light. UV lamps emit a broad spectrum of UV light, while UV LED lights emit light at specific wavelengths.
Photoinitiators:
- Photoinitiators are chemicals added to the material to be cured (e.g., ink, coating, adhesive). These chemicals absorb the UV light and undergo a chemical reaction, generating free radicals or other reactive species.
Polymerization:
- The generated free radicals or reactive species initiate a polymerization reaction in the material. Polymerization is when small molecules (monomers) link together to form larger polymer chains. In the context of UV curing, this process leads to the solidification or curing of the material.
Intensity and Wavelength Control:
- The intensity and wavelength of the UV light are crucial factors in the curing process. Different materials require specific wavelengths of UV light for optimal curing. UV lamps or LED systems are designed to emit light at the appropriate wavelengths for the cured material.
Substrate Considerations:
- The cured material must allow UV light to penetrate, so the process is most effective with transparent or translucent substrates. Materials that block UV light may require additional considerations or modifications.
Instantaneous Cure:
- One of the significant advantages of UV curing is its speed. The curing process occurs almost instantly when the UV light is applied, leading to faster production times than traditional curing methods.
Controlled Process:
- The UV curing process offers better control over the curing reaction. The curing can be initiated and halted precisely, allowing for greater precision in manufacturing processes.
Applications:
- UV curing is used in various applications, such as printing (UV printing), coatings on wood, metal, and plastic, adhesives in electronics and medical devices, and producing optical fibers.
Overall, UV curing is a versatile and efficient process that provides a quick and controlled way to cure or dry a wide range of materials in industrial applications. The choice of UV lamps, photoinitiators, and process parameters depends on the specific requirements of the material and application.
What are the key advantages of using UV-cure polyurethane adhesive?
UV-cure polyurethane adhesives offer several key advantages, making them popular in various applications. Here are some of the key advantages:
- Rapid Cure Time:One of the most significant advantages of UV-cure polyurethane adhesives is their fast cure time. These adhesives cure almost instantly when exposed to ultraviolet (UV) light. This quick curing helps improve production efficiency by reducing assembly time and increasing overall productivity.
- Precision and Control:UV-cure adhesives provide precise control over the bonding process. Manufacturers can control the intensity and duration of UV exposure, allowing them to fine-tune the curing process for specific applications. This precision is crucial in industries where accurate bonding and fast curing are essential.
- Low Heat Generation:UV-curing does not generate significant heat during curing. This is particularly advantageous for bonding heat-sensitive materials or components, as it minimizes the risk of thermal damage or distortion.
- Versatility:UV-cure polyurethane adhesives are versatile and can bond many substrates, including plastics, glass, metals, and composites. Their versatility makes them suitable for various industries, such as electronics, medical devices, automotive, and aerospace.
- Chemical Resistance:Polyurethane adhesives are known for their excellent chemical resistance. This property, combined with the rapid curing enabled by UV light, makes UV-cure polyurethane adhesives suitable for applications where resistance to harsh chemicals or environmental conditions is crucial.
- Low VOC Emissions:UV-cure adhesives generally have softer volatile organic compound (VOC) emissions than traditional adhesives. This can contribute to a healthier and safer working environment, meeting regulatory requirements and environmental standards.
- High Strength and Durability:Polyurethane adhesives, in general, offer high bond strength and durability. UV-cure polyurethane adhesives maintain these desirable mechanical properties while benefiting from the rapid curing characteristics of UV technology.
- Reduced Need for Mechanical Fasteners:The fast-curing nature and strong bonding capabilities of UV-cure polyurethane adhesives often eliminate the need for additional mechanical fasteners like screws or rivets. This simplifies the assembly process and reduces weight and potential stress points in the bonded materials.
It’s important to note that while UV-cure polyurethane adhesives offer many advantages, they may not be suitable for all applications. Substrate compatibility, bonding requirements, and environmental conditions should be considered when choosing an adhesive for a specific application.
In which industries are UV-cure polyurethane adhesives commonly used?
UV-cure polyurethane adhesives find applications in various industries due to their unique properties and advantages. Some of the sectors where UV-cure polyurethane adhesives are commonly used include:
Electronics and Electrical Industry:
- Bonding and encapsulating electronic components.
- Potting and sealing of electronic devices.
Medical Devices:
- Assembly of medical devices.
- Bonding of medical equipment components.
Automotive Industry:
- Bonding and sealing automotive components.
- Assembly of interior and exterior parts.
Woodworking and Furniture:
- Bonding and laminating wooden components.
- Furniture assembly and production.
Glass Bonding:
- Joining glass components.
- Manufacturing glass products.
Optical Industry:
- Assembly of optical components.
- Bonding of lenses and optical devices.
Plastic and Composite Materials:
- Bonding and joining plastic components.
- Composite material manufacturing.
Aerospace Industry:
- Bonding and assembly of aerospace components.
- Use in space and aircraft applications.
Printing and Packaging:
- Adhesion in printing processes.
- Packaging applications.
Jewelry and Accessories:
- Bonding of jewelry components.
- Assembly of fashion accessories.
Construction and Building Materials:
- Bonding and sealing construction materials.
- Use in architectural applications.
DIY and Hobbyist Applications:
- Craft and hobby projects.
- DIY home repairs.
UV-cure polyurethane adhesives offer rapid curing, high bond strength, and the ability to bond a wide range of materials. However, their usage may vary depending on each industry’s specific product formulations and requirements.
Are these adhesives suitable for bonding different materials?
UV-cure polyurethane adhesives are generally versatile and suitable for bonding various materials. However, the specific suitability depends on the formulation of the adhesive and the materials you intend to connect. Polyurethane adhesives, in general, offer good flexibility, durability, and bond strength.
UV-cure adhesives are cured by exposure to ultraviolet light, which initiates a photochemical reaction that leads to the hardening or curing of the adhesive. This curing process is relatively fast and allows precise control over bonding operations.
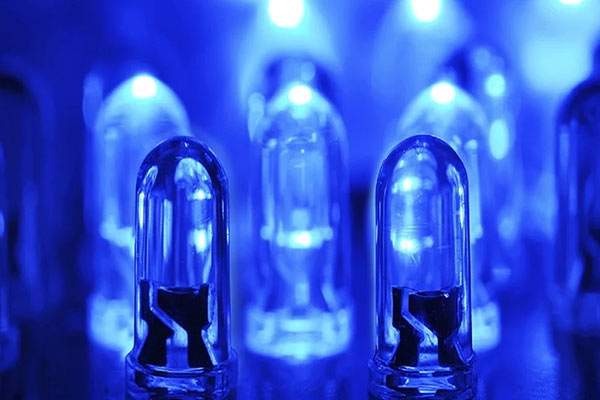
Polyurethane adhesives are known for their excellent adhesion to various substrates, including plastics, metals, glass, wood, and other materials. They are often chosen for applications requiring flexibility, impact resistance, and a strong bond.
Before using UV-cure polyurethane adhesives, it’s essential to check the product specifications and recommendations provided by the manufacturer. Different formulations may have varying properties; some may be better suited for specific materials or applications. Additionally, it’s crucial to ensure that the materials being bonded are compatible with the adhesive and that the surfaces are adequately prepared for bonding.
Always follow the manufacturer’s guidelines and recommendations for proper application and curing procedures to achieve optimal results. You may also contact the adhesive manufacturer directly for advice on the suitability of their product for your specific bonding needs.
What safety precautions should be taken when working with UV-cure adhesives?
Working with UV-cure adhesives requires careful attention to safety precautions to protect yourself and others. UV-cure adhesives typically contain chemicals that can be harmful if not handled properly. Here are some safety precautions to consider when working with UV-cure adhesives:
Protective Gear:
- Wear appropriate personal protective equipment (PPE) such as safety glasses or goggles with UV protection to shield your eyes from exposure to UV light.
- Use gloves made of materials resistant to the adhesive to protect your skin.
Ventilation:
- Work in a well-ventilated area or use local exhaust ventilation to minimize inhalation exposure.
UV Exposure:
- Avoid direct exposure to UV light. UV-cure adhesives cure quickly when exposed to UV light; prolonged exposure can cause skin and eye irritation.
Skin Protection:
- Avoid direct contact with the adhesive. In case of skin contact, immediately wash the affected area with soap and water.
Eye Protection:
- In case of eye exposure, flush the eyes with plenty of water for at least 15 minutes. Seek medical attention if irritation persists.
Handling and Storage:
- Follow the manufacturer’s guidelines for handling and storage. Keep containers tightly closed when not in use.
- Store UV-cure adhesives in a cool, dry place, away from direct sunlight.
Training and Education:
- Ensure that personnel working with UV-cure adhesives are adequately trained on handling and safety procedures.
Emergency Procedures:
- Know the location of emergency equipment, such as eye wash stations and emergency showers. Have a clear understanding of emergency procedures.
Read Safety Data Sheets (SDS):
- Familiarize yourself with the Safety Data Sheet for your specific UV-cure adhesive. SDS provides information on potential hazards, safe handling, and emergency procedures.
Equipment Safety:
- Regularly inspect and maintain UV curing equipment to ensure it functions correctly and safely.
Dispose of Waste Properly:
- Follow proper disposal procedures for used adhesives and associated materials by local regulations.
Always consult the specific safety guidelines provided by the manufacturer of the UV-cure adhesive you are using, as formulations may vary. Additionally, consider conducting a risk assessment to identify and mitigate potential hazards associated with your work environment’s specific materials and processes.
Can UV-cure polyurethane adhesives withstand harsh environmental conditions?
UV-cure polyurethane adhesives generally offer good resistance to harsh environmental conditions, but their performance can depend on specific formulations and the exact nature of the environmental exposure. Here are some factors to consider:
- UV Resistance:UV-cure adhesives are often chosen for their excellent UV resistance. They can maintain their strength and adhesion properties when exposed to sunlight, which is particularly important for applications exposed to outdoor conditions.
- Chemical Resistance:Polyurethane adhesives, in general, exhibit good chemical resistance. However, the specific chemical resistance of a UV-cure polyurethane adhesive may vary depending on the formulation. Some formulations may be more resistant to certain chemicals than others.
- Temperature Resistance:Polyurethane adhesives can generally withstand a wide range of temperatures. However, the exact temperature range can vary based on the specific formulation. It’s essential to check the product data-sheet or contact the manufacturer for information on the adhesive’s temperature resistance.
- Moisture Resistance:Many polyurethane adhesives provide good moisture resistance. This is crucial for applications where the adhesive may be exposed to humidity, rain, or other forms of moisture.
- Environmental Exposure:Consider the specific ecological conditions your application will face. For example, if the adhesive is used in marine environments, it should resist saltwater exposure. If exposed to industrial chemicals, the adhesive should have appropriate chemical resistance.
- Manufacturer’s Recommendations:Always refer to the manufacturer’s technical data sheets and product specifications for detailed information on the adhesive’s performance characteristics and suitability for specific environmental conditions.
It’s important to note that while UV-cure polyurethane adhesives can provide excellent performance in harsh conditions, the overall success of an adhesive in a particular application also depends on factors such as proper surface preparation, correct application techniques, and adherence to recommended cure times and conditions. If in doubt, consult the adhesive manufacturer for specific advice tailored to your application.
Are there specific applications where UV cure adhesives outperform other types?
UV-cure adhesives offer several advantages in specific applications, making them preferable over other types of adhesives in certain situations. Some of the critical applications where UV-cure adhesives outperform different types include:
- Rapid curing time:UV-cure adhesives cure almost instantly when exposed to ultraviolet light. This fast curing time is advantageous in high-speed production processes where quick bonding and assembly are crucial.
- Precision bonding:UV adhesives allow for precise control over the bonding process. The curing only occurs when the adhesive is exposed to UV light, allowing manufacturers to control when and where the bond forms. This precision is valuable in applications requiring intricate or delicate bonding.
- Low heat generation:Unlike other adhesives that rely on heat for curing, UV-cure adhesives generate minimal heat during the curing process. This characteristic makes them suitable for bonding heat-sensitive materials, preventing damage to sensitive components.
- Low VOC emissions:UV-cure adhesives often have softer volatile organic compound (VOC) emissions than solvent-based adhesives. This makes them environmentally friendly and suitable for applications where minimizing emissions is a concern.
- High bond strength:UV-cure adhesives can provide strong and durable bonds, making them ideal for various materials, including glass, plastic, and metal. The cured adhesive often exhibits excellent adhesion properties.
- Versatility in substrates:UV-cure adhesives are compatible with many substrates, making them versatile for different applications. They can bond materials that may be challenging for other adhesive types.
- No mixing required:UV adhesives typically come in single-component formulations, eliminating the need for mixing. This simplifies the application process and reduces the likelihood of errors associated with incorrect mixing ratios.
- Clean and efficient process:UV-cure adhesives are often solvent-free and do not involve additional chemicals during curing. This results in a cleaner and more efficient manufacturing process.
Common industries where UV-cure adhesives are frequently used include electronics, optics, medical devices, and particular automotive applications. However, it’s important to note that the choice of adhesive depends on various factors, including the application’s specific requirements, the materials being bonded, and environmental considerations. While UV-cure adhesives offer advantages in certain situations, there are also instances where other types of adhesives may be more suitable.
What are the limitations or considerations when using UV-cure polyurethane adhesives?
UV-cure polyurethane adhesives have several advantages, such as fast curing, low volatility, and high bond strength. However, they also come with some limitations and considerations that users should be aware of:
Substrate Sensitivity:
- UV-cure polyurethane adhesives may not adhere well to specific substrates, especially those inherently UV-absorbing or opaque. Substrate selection is crucial for successful bonding.
UV Penetration:
- The curing process relies on UV light penetration to activate the adhesive. Ensuring UV light can reach all areas of the adhesive joint is essential. Complex geometries or shadowed areas may not cure properly.
Thickness of Adhesive Layer:
- The curing depth of UV adhesives is limited, so the adhesive layer should be thin to ensure proper curing. If the layer is too thick, the UV light may not penetrate sufficiently, resulting in incomplete curing.
UV Light Intensity and Exposure Time:
- Proper curing depends on the UV light’s intensity and exposure duration. Inadequate exposure can lead to incomplete curing, affecting the bond strength and performance of the adhesive.
Sensitivity to Oxygen Inhibition:
- Some UV-cure adhesives are sensitive to oxygen inhibition, which means that the adhesive surface may not cure properly in the presence of oxygen. This is more of a concern for specific formulations, and manufacturers may provide solutions or recommendations to mitigate this issue.
Moisture Sensitivity:
- UV-cure polyurethane adhesives can be sensitive to moisture. Excessive moisture can hinder the curing process and affect the performance of the adhesive. It’s essential to store and handle these adhesives in a dry environment.
Temperature Sensitivity:
- The curing process may be temperature-dependent. Extreme temperatures can affect the cure rate, and manufacturers often provide guidelines regarding the suitable temperature range for curing.
UV Light Source Considerations:
- The type and quality of the UV light source used for curing can impact the performance of the adhesive. It’s essential to use the recommended UV light source specified by the adhesive manufacturer.
Health and Safety Considerations:
- UV-cure adhesives may contain components that can be harmful if not handled properly. Users should follow safety guidelines, wear appropriate protective equipment, and work in well-ventilated areas.
Post-Cure Handling:
- After curing, it’s essential to consider any post-cure handling requirements specified by the manufacturer. Some adhesives may require additional steps or time to achieve optimal properties.
It’s crucial to carefully follow the manufacturer’s guidelines and recommendations for the specific UV-cure polyurethane adhesive to ensure proper application and performance.
How does the curing time of UV cure adhesives compare to traditional adhesives?
The curing time of UV-cure and traditional adhesives can vary significantly, and it depends on various factors, such as the type of adhesive, the specific formulation, and the application requirements. Here’s a general comparison:
UV-Cure Adhesives:
- Speed:UV-cure adhesives are known for their rapid curing times. The curing process is initiated by exposure to ultraviolet (UV) light, which activates photoinitiators in the adhesive. This typically leads to fast curing within seconds or minutes.
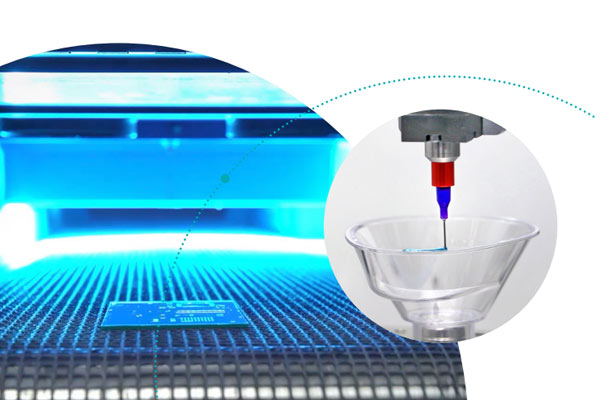
- Control:UV-cure adhesives offer precise control over the curing process since exposure to UV light can be easily regulated. This allows for quick and on-demand curing.
Traditional Adhesives (Non-UV):
- Speed:Traditional adhesives, which include solvent-based, water-based, or heat-cure adhesives, generally have slower curing times compared to UV-cure adhesives. The curing time can range from minutes to hours and sometimes even days.
- Factors Affecting Cure Time:
- Chemistry:The curing time depends on the chemical reactions involved in the curing process. For example, epoxy adhesives may take longer to cure than cyanoacrylate adhesives.
- Temperature and Humidity:Environmental conditions, such as temperature and humidity, can influence the curing time of traditional adhesives. Some adhesives may cure faster or slower under different conditions.
Considerations:
- Application Requirements:The choice between UV-cure and traditional adhesives often depends on the application’s specific needs. If rapid bonding and curing are crucial, UV-cure adhesives may be preferred.
- Substrate Compatibility:The type of materials being bonded is also a critical factor. Some substrates may be more suitable for UV-cure adhesives, while others may require the characteristics of traditional adhesives.
UV-cure adhesives are generally faster in terms of curing compared to traditional adhesives. However, the adhesive selection should be based on the application’s specific requirements, including substrate compatibility, bonding strength, and curing time constraints.
Can UV-cure polyurethane adhesives be used in underwater applications?
UV-cure polyurethane adhesives are generally not recommended for underwater applications. While they can offer solid bonds and rapid curing times in dry conditions when exposed to ultraviolet (UV) light, they may not perform well when submerged in water.
Water can interfere with the curing process of UV-cure adhesives, as moisture can scatter or absorb the UV light needed for the curing reaction. Additionally, water may affect the adhesive’s ability to bond properly and compromise its strength and durability.
For underwater applications, it’s often better to use adhesives specifically designed for such environments. Marine adhesives and sealants formulated to withstand the challenges posed by water exposure, including saltwater conditions, are available. Epoxy-based adhesives and polyurethane sealants designed for marine use may offer better performance in underwater applications.
Always refer to the manufacturer’s recommendations and specifications for any adhesive or sealant to ensure it suits your application’s specific conditions and substrates. If in doubt, consulting with the adhesive manufacturer or seeking the advice of a materials engineer can help you select the most appropriate product for your underwater bonding needs.
Are there any special storage requirements for UV cure adhesives?
UV cure adhesives, also known as ultraviolet (UV) light-curing adhesives, are commonly used in various industries for bonding and assembly applications. Proper storage is crucial to maintain the effectiveness of these adhesives. Here are some general guidelines for the storage of UV cure adhesives:
Protect from Light Exposure:
- UV cure adhesives are sensitive to UV light, which can prematurely cure or polymerize the adhesive in the container. Store UV-cure adhesives in opaque or amber-colored containers to protect them from light exposure.
Cool and Dry Environment:
- Store UV-cure adhesives in a cool, dry place to prevent moisture absorption and potential degradation of the adhesive. High humidity can negatively impact the performance of some UV-cure adhesives.
Temperature Stability:
- Adhesives should be stored within the temperature range specified by the manufacturer. Extreme temperatures can alter the chemical properties of the adhesive. Typically, the recommended storage temperature is mentioned on the product datasheet.
Ventilation:
- Adequate ventilation is essential to prevent the accumulation of fumes or gases released by the adhesive. Ensure proper ventilation in the storage area to maintain a safe working environment.
Seal Containers Tightly:
- When not in use, seal the containers tightly to prevent air and moisture from entering. This helps to maintain the quality and shelf life of the adhesive.
Shelf Life:
- Pay attention to the expiration or shelf life of the UV-cure adhesive. Using expired adhesives may result in reduced performance or incomplete curing.
Avoid Contamination:
- Contamination can affect the performance of UV-cure adhesives. Keep the storage area clean and ensure that tools and equipment used with the adhesive are free from contaminants.
Follow the Manufacturer’s Recommendations:
- Always follow the specific storage recommendations provided by the manufacturer. Different UV cure adhesives may have unique requirements based on their formulations.
It’s important to note that these are general guidelines, and specific recommendations may vary based on the formulation of the UV cure adhesive. Always refer to the product datasheet and the manufacturer’s instructions for precise storage requirements. If in doubt, contact the manufacturer for clarification and guidance on proper storage practices for a particular UV-cure adhesive.
What factors should be considered when selecting a UV-cure polyurethane adhesive?
Selecting a UV-cure polyurethane adhesive involves considering various factors to ensure that the adhesive meets the specific requirements of your application. Here are vital factors to consider:
Substrate Compatibility:
- Ensure that the adhesive is compatible with the materials you are bonding. Different polyurethane adhesives may have varying levels of adhesion to various substrates.
Curing Speed:
- UV-cure adhesives cure rapidly when exposed to ultraviolet light. Consider the required curing speed for your application, and choose an adhesive that can be fixed within the specified time frame.
UV Light Source:
- The type and intensity of the UV light source can impact the curing process. Verify the compatibility of the adhesive with the available UV light source, and ensure that the light source is suitable for your production environment.
Environmental Conditions:
- Consider the environmental conditions in which the adhesive will be used. Factors such as temperature, humidity, and exposure to chemicals can affect the performance of the adhesive. Choose an adhesive that can withstand the specific conditions of your application.
Bond Strength and Flexibility:
- Evaluate the required bond strength for your application. Additionally, consider the flexibility or rigidity needed in the bonded joints. Different formulations of UV-cure polyurethane adhesives may offer varying degrees of flexibility and strength.
Viscosity:
- The viscosity of the adhesive is essential for application purposes. Select a viscosity that suits your specific bonding method (e.g., dispensing, spraying) and ensures proper coverage and adhesion.
Cured Properties:
- Understand the cured properties of the adhesive, including hardness, elasticity, and resistance to environmental factors. These properties are crucial for the long-term performance of the bonded materials.
Application Method:
- Consider the application method, such as dispensing, spraying, or brushing. Ensure that the adhesive suits the chosen application method and can be easily integrated into your production process.
Regulatory Compliance:
- Verify whether the adhesive complies with relevant industry regulations and standards. This is especially important in industries with strict quality and safety requirements.
Cost Considerations:
- Assess the adhesive’s overall cost, considering not only the product cost but also factors such as application efficiency, curing time, and potential rework costs.
Supplier Support and Technical Assistance:
- Choose a reliable supplier that offers technical support and assistance. This can be valuable for troubleshooting, optimizing processes, and addressing any challenges during the application.
By carefully considering these factors, you can select a UV-cure polyurethane adhesive that best meets the specific needs of your application, ensuring optimal performance and durability.
Are these adhesives compatible with automated manufacturing processes?
UV-cure polyurethane adhesives can be compatible with automated manufacturing processes, but several factors must be considered. Here are some key points to keep in mind:
- Curing Time:UV-cure adhesives generally cure rapidly when exposed to ultraviolet (UV) light. This fast curing time can be advantageous in automated processes requiring quick bonding.
- UV Light Source:The automated manufacturing system must have an appropriate UV light source to activate the curing process. Ensure the system delivers sufficient UV intensity and coverage to cure the adhesive effectively.
- Substrate Compatibility:Verify that the adhesive is compatible with the bonded materials. Polyurethane adhesives are known for their versatility, but confirming compatibility with specific substrates used in your manufacturing process is essential.
- Application Method:Consider the application method of the adhesive in the automated process. Whether dispensed through nozzles, sprayed, or applied in another manner, the adhesive application process should be well-suited for automation.
- Consistency and Viscosity:The adhesive’s consistency and viscosity should suit the automated dispensing or application system. Consistent viscosity ensures uniform application and bonding.
- Adhesive Handling:Evaluate how well mechanical equipment can handle the adhesive. Some adhesives may have specific storage or handling requirements that need to be considered.
- Quality Control:Implement measures to ensure the adhesive is consistently applied and cured according to specifications. Automated systems may include sensors or cameras to monitor the application and curing process.
- Environmental Considerations:Ensure the manufacturing environment is conducive to UV curing. Factors such as ambient light, temperature, and humidity can impact the effectiveness of UV-cure adhesives.
- Testing and Validation:Before full-scale implementation, conduct testing and validation to confirm that the UV-cure polyurethane adhesive meets the required performance standards for your application.
Always consult with the adhesive manufacturer and, if needed, involve an adhesive application specialist to ensure that the chosen UV-cure polyurethane adhesive suits your specific automated manufacturing process.
What is the impact of UV-cure adhesives on the environment?
UV-cure adhesives can have both positive and negative environmental impacts, and the overall assessment depends on various factors, such as the specific formulation of the adhesive, the application process, and the disposal methods. Here are some considerations regarding the environmental impact of UV-cure adhesives:
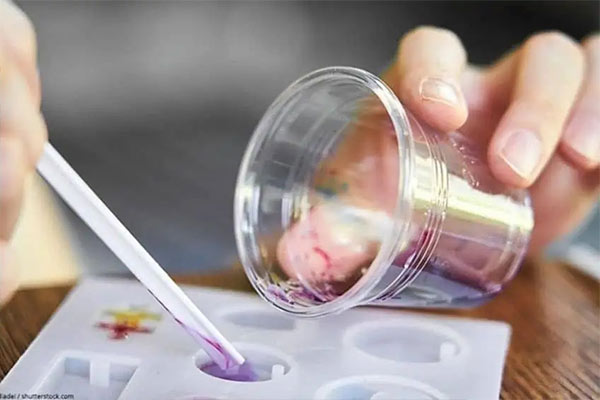
Positive Environmental Aspects:
- Low VOC Emissions:UV-cure adhesives typically have low or zero volatile organic compound (VOC) emissions. This is beneficial for indoor air quality and reduces the release of harmful substances into the atmosphere.
- Energy Efficiency:The curing process of UV-cure adhesives is generally quick and energy-efficient. Traditional adhesives may require heat or extended curing times, leading to higher energy consumption.
- Reduced Waste:As UV adhesives cure rapidly, there may be less material waste compared to slower-curing alternatives. The quick curing time allows for faster production cycles and less excess material.
- Long Shelf Life:UV-cure adhesives often have a longer shelf life than other adhesives, reducing the likelihood of material becoming obsolete and requiring disposal.
Negative Environmental Aspects:
- Chemical Composition:Some UV-cure adhesives may contain chemicals that are considered hazardous. Reviewing the Material Safety Data Sheet (MSDS) and formulation details is essential to identify any potentially harmful substances.
- Energy Consumption:While the curing process is energy-efficient, producing UV light for curing may require energy-intensive processes. This could have environmental implications depending on the energy source.
- Disposal:The disposal of cured UV adhesives may not pose a significant environmental risk, but unused or waste materials should be handled according to local regulations. Ensure proper disposal methods are followed to prevent environmental contamination.
- Raw Material Extraction:The production of the raw materials used in UV-cure adhesives may involve resource extraction and manufacturing processes contributing to ecological impacts. Consideration should be given to the sourcing of these materials.
- UV Light Concerns:While UV curing is relatively clean, prolonged exposure to UV light can have potential health and safety implications for workers. Proper protective measures should be implemented.
Manufacturers and users of UV-cure adhesives must know these considerations and take steps to minimize environmental impacts. This may include selecting adhesives with environmentally friendly formulations, optimizing curing processes, adhering to proper disposal practices, and staying informed about advancements in adhesive technology that address environmental concerns. Regulatory compliance and adherence to best practices in handling and disposal are crucial for minimizing the ecological footprint of UV-cure adhesives.
Can UV-cure polyurethane adhesives be removed or reversed after bonding?
UV-cure polyurethane adhesives are known for their rapid curing and strong bonding properties. Once cured, these adhesives typically form a strong and durable bond and are not designed to be easily reversed. Unlike other types of adhesives that can be softened or dissolved with specific solvents, UV-cure polyurethane adhesives undergo a chemical reaction during the curing process, creating a crosslinked network, making them resistant to solvents.
While it’s generally challenging to reverse the bonding of UV-cure polyurethane adhesives, there are a few potential methods you could consider:
Mechanical Methods:
- You can mechanically break or cut the related parts depending on the bonded materials. However, this method can be damaging to the materials involved.
Heat:
- Some polyurethane adhesives can be softened or weakened by applying heat. However, this method may not work well with UV-cure adhesives, as they tend to have high-temperature resistance.
Chemical Methods:
- Investigate if any chemicals can selectively break down or weaken the adhesive without causing damage to the bonded materials. However, finding a suitable chemical may be difficult, and this approach requires careful consideration of material compatibility.
Professional Assistance:
- If the related materials are valuable or unsure about the best method, seek assistance from professionals specializing in adhesive bonding or material removal.
Always exercise caution when attempting to reverse the bonding of adhesives, as aggressive methods can damage the materials you are working with. Additionally, it’s essential to consider safety precautions, especially when using heat or chemicals. If in doubt, consult with the adhesive manufacturer or seek guidance from experts in the field.
Are there any emerging trends or innovations in UV cure adhesive technology?
However, it’s important to note that technology is dynamic, and there may have been further advancements or changes since then. Here are some trends and innovations that were noteworthy up to my last update:
- Dual-Cure Systems: Some UV cure adhesives are designed to cure under UV light and through a secondary curing mechanism, such as heat or moisture. This provides flexibility in the curing process and allows for bonding in areas that may be shielded from direct UV light.
- LED UV Curing: LED UV curing systems are replacing or supplementing traditional UV lamps. LED technology offers advantages such as energy efficiency, longer life, and more precise control over the curing process. This innovation has been gaining traction due to its environmental benefits and cost-effectiveness.
- Low-Intensity UV Curing: The focus has been on developing UV cure adhesives that cure at lower UV light intensities. This trend aims to reduce the potential for damage to sensitive substrates and expands the range of materials that can be bonded.
- Adhesives for Challenging Substrates: Innovations in UV cure adhesives address the challenge of bonding difficult-to-adhere substrates, such as certain plastics, glass, and metals. Formulations are being optimized to enhance adhesion to a broader range of materials.
- Customized Formulations: There is a growing trend toward formulating UV cure adhesives based on specific application requirements. This includes adhesives tailored for flexibility, transparency, thermal resistance, or other performance characteristics.
- Green Initiatives: As with many industries, there is an increasing focus on sustainability in UV cure adhesive technology. This involves the development of adhesives with reduced environmental impact, such as formulations with fewer volatile organic compounds (VOCs) or those derived from renewable resources.
What role do UV cure adhesives play in the aerospace and automotive industries?
UV cure adhesives play a crucial role in the aerospace and automotive industries, providing several advantages in performance, efficiency, and manufacturing processes. Here are some essential parts and applications of UV cure adhesives in these industries:
Aerospace Industry:
- Lightweight Bonding:UV cure adhesives are often used in aerospace for bonding lightweight materials like composites and plastics. These adhesives offer a solid and durable bond without adding significant weight to the aircraft.
- Fast Cure Times:UV cure adhesives cure rapidly when exposed to ultraviolet light. This quick curing process is advantageous in aerospace applications where fast assembly and turnaround times are essential.
- Precision Bonding:UV cure adhesives provide precise control over the bonding process. This is critical in aerospace manufacturing, where precision and accuracy are paramount for aircraft components’ structural integrity and performance.
- Resistance to Harsh Conditions:Many UV cure adhesives exhibit excellent resistance to environmental factors such as temperature extremes, chemicals, and moisture, making them suitable for aerospace applications where components may be exposed to challenging conditions.
Automotive Industry:
- Assembly and Manufacturing:UV cure adhesives are used in automotive manufacturing for bonding various components. The fast cure times help streamline assembly processes, increasing overall production efficiency.
- Structural Bonding:In automotive design, UV cure adhesives contribute to structural bonding, especially for lightweight and electric vehicles. They provide a solid and durable bond between different materials, contributing to the overall strength and safety of the car.
- Sealing and Gasketing:UV cure adhesives are employed for sealing and gasketing applications, helping prevent leaks and ensure the integrity of automotive systems, such as fuel and electronic components.
- Design Flexibility:UV cure adhesives enable design flexibility by allowing for precise application and bonding in areas that might be challenging with traditional adhesives. This mainly benefits the automotive industry, where complex and innovative designs are standard.
- Environmental Considerations:UV cure adhesives often have lower volatile organic compound (VOC) emissions than traditional adhesives, aligning with the automotive industry’s focus on environmentally friendly manufacturing processes.
UV cure adhesives contribute to the aerospace and automotive industries by offering fast curing, precision bonding, and resistance to harsh conditions, ultimately enhancing final product performance, efficiency, and safety.
Are there specific maintenance requirements for bonded materials?
The maintenance requirements for bonded materials using UV cure adhesives vary depending on the application, materials involved, and environmental conditions. Here are some general considerations:
Monitoring Bonded Joints:
- Regular inspections are essential to monitor the condition of bonded joints. This is particularly important in critical applications such as aerospace and automotive, where the structural integrity of the connected components is crucial.
Environmental Exposure:
- Assess the ecological conditions to which the related materials are exposed. UV cure adhesives are often chosen for their resistance to environmental factors. Still, prolonged exposure to harsh conditions such as extreme temperatures, chemicals, or UV radiation can impact the adhesive’s performance over time.
Preventive Maintenance:
- Implement preventative maintenance measures to address potential issues before they become significant problems. This may include routine inspections, testing, and adherence to recommended maintenance schedules.
Repair and Replacement:
- In the event of damage or degradation, follow the recommended repair or replacement procedures provided by the adhesive manufacturer. Some adhesives may have specific guidelines for repairing bonded joints, so adhering to these instructions is crucial.
Cleaning and Surface Preparation:
- Proper cleaning and surface preparation are critical if maintenance involves re-bonding or repairing. Ensure that the surfaces to be bonded are clean, free of contaminants, and prepared according to the adhesive manufacturer’s recommendations.
Compatibility Testing:
- Before implementing any maintenance or repair, conduct compatibility testing to ensure the new adhesive or repair material is compatible with the existing bonded joint. Incompatibility can lead to adhesion issues and compromise the integrity of the joint.
Documentation:
- Maintain detailed records of the bonding process, including adhesive type, curing conditions, and any specific requirements outlined by the manufacturer. This information can be valuable for future maintenance and troubleshooting.
Training and Expertise:
- Ensure that personnel responsible for maintenance and repairs are adequately trained and have the necessary expertise in working with UV cure adhesives. This includes understanding the specific characteristics of the adhesive in the bonding process.
Consult Manufacturer Guidelines:
- Always refer to the manufacturer’s guidelines and recommendations for the particular UV cure adhesive. Adhesive manufacturers typically provide detailed instructions regarding maintenance, repair, and the expected service life of their products.
It’s important to note that the maintenance requirements can vary based on the type of UV cure adhesive, the substrates involved, and the application. Therefore, consulting with the adhesive manufacturer and following their guidelines is crucial to ensuring bonded materials’ long-term performance and reliability.
How does UV cure polyurethane adhesive cost compare to other adhesive options?
The cost of UV-cure polyurethane adhesive can vary depending on several factors, including the specific formulation, brand, and quantity purchased. UV-cure polyurethane adhesives are generally considered a high-performance option with several advantages, but they may also be more expensive compared to other adhesive options.
Here are some factors to consider when comparing the cost of UV-cure polyurethane adhesive to other adhesive options:
Upfront Equipment Costs:
- UV-cure adhesives require UV light sources for curing. The cost of UV curing equipment can be a significant upfront investment. Other adhesives may not require specialized equipment, affecting the overall cost comparison.
Speed of Cure:
- UV-cure adhesives typically cure very quickly compared to some other adhesives. The faster curing time can increase productivity and efficiency, potentially offsetting the higher upfront costs.
Application Process:
- The application process for UV-cure adhesives may be more automated, reducing labor costs. Other adhesives may require more manual application and longer curing times, impacting labor expenses.
Performance and Durability:
- UV-cure polyurethane adhesives are known for their high bond strength and durability. If the application demands such performance, the cost may be justified compared to other adhesives with lower performance characteristics.
Material Waste:
- Some adhesive options may result in more material waste during application or curing. UV-cure adhesives can be more precise in application, potentially reducing waste and material costs.
Specific Application Requirements:
- The specific requirements of your application will heavily influence the choice of adhesive. If UV-cure polyurethane adhesive best fits your needs, its potential benefits outweigh the initial cost considerations.
Conducting a thorough cost analysis based on your specific application, production volume, and performance requirements is essential. Additionally, consider consulting with adhesive suppliers or industry experts to get tailored advice based on your unique situation. While UV-cure polyurethane adhesives may be more expensive upfront, the overall cost-effectiveness depends on the specific circumstances of the application and the benefits the adhesive provides in terms of performance and efficiency.
Conclusion:
In conclusion, UV-cure polyurethane adhesive is a cutting-edge solution with many applications. From their rapid curing process to unmatched versatility, these adhesives reshape how industries approach bonding challenges. Whether you are an engineer, artisan, or hobbyist, exploring the intricacies of UV cure polyurethane adhesives can open new doors for enhanced efficiency and durability in your projects.
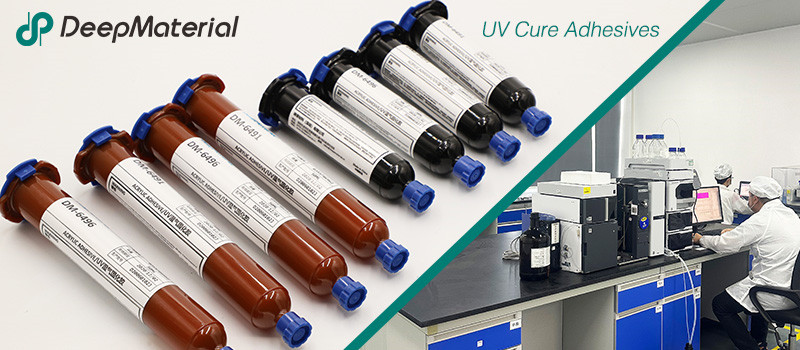
DeepMaterial
Based on the core technology of adhesives, DeepMaterial has developed adhesives for chip packaging and testing, circuit board level adhesives, and adhesives for electronic products. Based on adhesives, it has developed protective films, semiconductor fillers, and packaging materials for semiconductor wafer processing and chip packaging and testing. More…
UV Curing Adhesives
UV light cure have a number of benefits making them a popular choice among many product assembly and manufacturing applications. Many UV light cure adhesives can provide a nearly instantaneous bond to difficult substrates like glass and plastic. UV cure adhesives often require an accelerator or UV light for a bond to form.
Adhesive Blogs & News
The latest adhesive industry science and technology, Deepmaterial news, and market trends and forecasts.
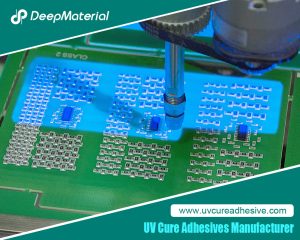
In – depth Analysis of the Main Characteristics of UV Adhesives for Touch Screens
In – depth Analysis of the Main Characteristics of UV Adhesives for Touch Screens In the manufacturing of modern electronic devices, the touch screen serves as a crucial component for human – machine interaction, and its performance and quality are of utmost importance. As a key material for effectively bonding various components of the touch
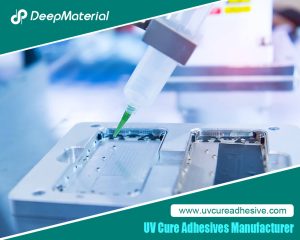
The Quantitative Influence of Crosslinking Density on the Flexibility and Hardness of Adhesives and the Formulation Optimization Strategy
The Quantitative Influence of Crosslinking Density on the Flexibility and Hardness of Adhesives and the Formulation Optimization Strategy This article systematically expounds the quantitative relationship between the crosslinking density and the flexibility and hardness of adhesives. Combining the theories of polymer physics with experimental analysis methods, it reveals the mechanism of the action of the
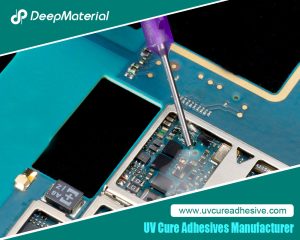
Technical Strategies for Balancing the Rapid Curing Property and Long Operating Time of UV Adhesives
Technical Strategies for Balancing the Rapid Curing Property and Long Operating Time of UV Adhesives UV adhesives have been widely used in many fields such as electronics, optics, and medicine due to their advantages of rapid curing, high bonding strength, and environmental protection. However, their rapid curing property also brings challenges in some application scenarios.
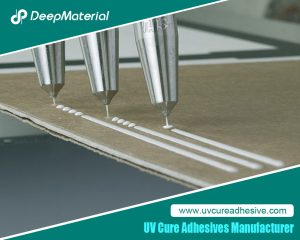
Biocompatibility of LED UV Glue Adhesive and Its Application Potential in Medical and Food Packaging Fields
Biocompatibility of LED UV Glue Adhesive and Its Application Potential in Medical and Food Packaging Fields LED UV glue adhesive has been widely applied in numerous fields due to its advantages such as rapid curing and easy operation. However, in fields with stringent safety requirements like medical and food packaging, its biocompatibility after curing
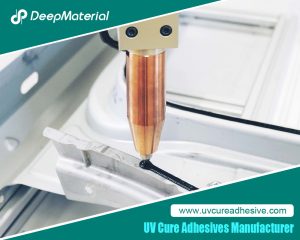
Exploring the Environmental Performance of UV Glue and Strategies for Optimizing Odor and VOC Content
Exploring the Environmental Performance of UV Glue and Strategies for Optimizing Odor and VOC Content UV glue, as an adhesive that achieves rapid curing through ultraviolet (UV) light irradiation, has been widely applied in numerous fields such as electronics, optics, healthcare, and automobiles, thanks to its advantages of fast curing speed, high bonding strength, and
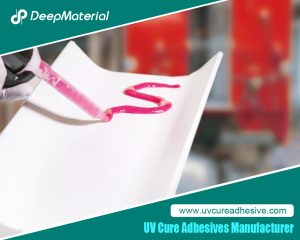
Compatibility Analysis and Countermeasures of LED UV Glue with Automated Production Equipment
Compatibility Analysis and Countermeasures of LED UV Glue with Automated Production Equipment LED UV glue has been widely used in modern manufacturing due to its advantages such as fast curing speed, high bonding strength, and environmental friendliness. However, in the automated production process, if there are problems with the adaptability between the glue and equipment