High Viscosity Adhesive
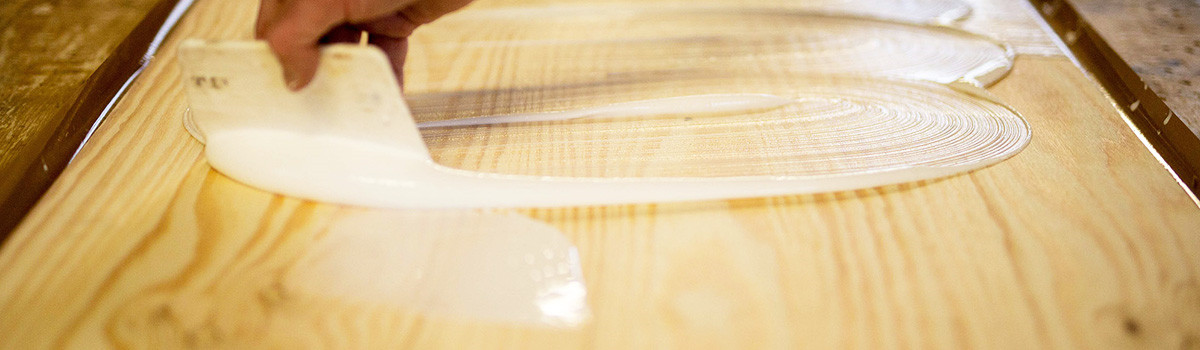
High-viscosity adhesives stand as titans among bonding solutions, wielding their remarkable prowess in creating resilient, unyielding bonds. Defined by their dense consistency, these adhesives are a testament to the sheer power viscosity wielded in the realm of adhesive performance. Their distinctive attribute lies in the thick, almost substantial nature that fosters unparalleled strength and durability in bonds. In this unveiling exploration, we delve into the intricate world of high-viscosity adhesives, deciphering their chemical composition, applications in woodworking, metal fabrication, and even their remarkable utility in marine environments.
Table of Contents
ToggleWhat defines high-viscosity adhesives and their primary characteristics?
High-viscosity adhesives are pivotal in various industries due to their unique properties and versatile applications. Understanding what defines high-viscosity adhesives and their primary characteristics is crucial for choosing suitable adhesives for specific purposes. Here’s an insightful exploration into the world of high-viscosity adhesives:
Definition of High-Viscosity Adhesives
- High-viscosity adhesives refer to a class of adhesives with a thicker consistency and higher resistance to flow.
- They possess a higher molecular weight and are more dense than low-viscosity adhesives.
Primary Characteristics of High-Viscosity Adhesives
- Thicker Consistency:High-viscosity adhesives have a dense, viscous texture that allows them to stay in place without running or dripping, making them ideal for vertical or overhead applications.
- Slow Flow Rate:Due to their high viscosity, these adhesives flow slower, offering better control during application.
- Muscular Bonding Strength:They create robust bonds, often offering exceptional shear and tensile strength, making them suitable for bonding a wide range of materials, including metals, plastics, and ceramics.
- Longer Cure Times:High-viscosity adhesives typically have longer curing or setting times, ultimately allowing for adjustments and alignment before the adhesive sets.
- Resistance to Temperature and Chemicals:Many high-viscosity adhesives exhibit excellent resistance to temperature variations and chemicals, ensuring durability in harsh environments.
- Gap Filling Properties:Their thick consistency enables them to fill more significant gaps and irregularities between surfaces, enhancing the overall bond strength.
Applications of High-Viscosity Adhesives
- Automotive Industry:These adhesives are commonly used for bonding components, sealing joints, and repairing parts due to their remarkable strength and resistance to temperature and chemicals.
- Construction and Building: Ideal for structural bonding, sealing, and installing panels or tiles in vertical or overhead applications.
- Electronics:Due to their excellent electrical insulation properties, electronics are used in assembling electronic components, securing circuit boards, and potting applications.
- Aerospace and Aviation:Employed for bonding composite materials, repairing aircraft parts, and assembling components that require high strength and durability.
- Medical Devices:Utilized for bonding medical equipment and devices due to their biocompatibility and resistance to sterilization methods.
How does viscosity impact adhesive performance and bonding strength?
In adhesive technologies, the viscosity of the adhesive plays a pivotal role in determining its performance and bonding strength. High-viscosity adhesives, specifically, showcase unique characteristics that significantly impact their effectiveness in bonding various materials. Understanding the correlation between viscosity and adhesive performance is crucial for achieving optimal results in bonding applications.
Viscosity: The Key to Adhesive Performance
- Definition of Viscosity:Viscosity refers to a fluid’s resistance to flow. In adhesives, it denotes the thickness or consistency of the substance.
- Impact on Flow and Application:Higher viscosity adhesives exhibit thicker consistency, resulting in slower flow rates. This characteristic affects how the adhesive spreads and adheres to surfaces during application.
- Gap-Filling Capabilities:High-viscosity adhesives fill gaps and irregularities between substrates, ensuring a stronger bond by providing more excellent contact between surfaces.
Influence on Bonding Strength
- Enhanced Stability:The thicker nature of high-viscosity adhesives contributes to better stability, preventing adhesive migration or runoff before curing.
- Increased Load-Bearing Capacity:High-viscosity adhesives offer higher load-bearing capabilities due to their ability to fill voids effectively, distributing stress more evenly across the bonded area.
- Improved Resistance to Shear Forces:These adhesives exhibit better resistance to shear forces, making them suitable for applications requiring durability and long-term bonding.
Factors Impacting Viscosity-Performance Relationship
- Temperature Sensitivity:Viscosity can be temperature-dependent. High-viscosity adhesives might become more fluid at elevated temperatures, affecting their bonding properties.
- Curing Time:Viscosity can influence the curing time of adhesives. High-viscosity adhesives might take longer to cure due to slower flow rates.
Optimal Application Scenarios
- Vertical or Overhead Applications:High-viscosity adhesives are ideal for vertical or overhead applications where thinner adhesives might drip or run off before curing.
- Bonding Porous or Rough Surfaces:Their gap-filling ability makes high-viscosity adhesives suitable for connecting porous or rough surfaces, enhancing the overall bond strength.
What are the key components or chemical compositions of these adhesives?
High-viscosity adhesives play a pivotal role in various industries, showcasing remarkable bonding capabilities. Their effectiveness stems from a sophisticated blend of chemical components meticulously formulated to meet diverse application requirements. Understanding the fundamental chemical compositions of these adhesives illuminates their significance and utility.
The key components of high-viscosity adhesives encompass a range of chemicals, each contributing distinct properties to the adhesive’s overall performance:
Polymer Resins
- Epoxy Resins:These resins, known for their exceptional bonding strength, provide robustness and durability to the adhesive.
- Polyurethane Resins:Offering flexibility and resistance to environmental factors, enhancing the adhesive’s adaptability.
Fillers and Reinforcements
- Silica, Glass Beads, or Ceramic Particles:These materials augment strength and stiffness, improving the adhesive’s structural integrity.
- Fibrous Materials:Including fibers like aramid, carbon, or glass reinforces the adhesive, enhancing its tensile strength and impact resistance.
Solvents and Diluents
- Volatile Organic Compounds (VOCs):Volatile Organic Compounds (VOCs) are utilized as solvents to manage viscosity and assist in the application process.
- Diluents:Altering viscosity and curing characteristics while improving adhesion to different substrates.
Curing Agents
- Amine-based Compounds:Accelerate the curing process in epoxy adhesives, enhancing their bonding capabilities.
- Isocyanates: Vital in polyurethane adhesives, initiating the crosslinking process for optimal bonding strength.
Modifiers and Additives
- Plasticizers:Enhance the adhesive’s flexibility, impact resistance, and elongation properties.
- Anti-oxidants and UV Stabilizers:Guard against degradation from environmental factors, extending the adhesive’s lifespan.
Resin Modifiers
- Epoxide Adducts:Enhance epoxy adhesives’ toughness and impact resistance, which is crucial for demanding applications.
- Hydroxyl-terminated polybutadiene (HTPB): Increases flexibility and resilience in specific formulations.
How does high viscosity contribute to the application and bonding process?
High-viscosity adhesive, often hailed as a game-changer in bonding solutions, is crucial in enhancing the application and bonding processes across various industries. With its unique properties, this specialized adhesive offers unparalleled advantages that contribute significantly to achieving robust bonds. Let’s explore why high viscosity is a key factor in optimizing the application and bonding processes.
Benefits of High-Viscosity Adhesive
Improved Gap Filling
- High-viscosity adhesive has a thicker consistency, allowing it to fill gaps and irregularities between surfaces.
- This property ensures that the adhesive can effectively bridge larger spaces, resulting in stronger bonds, especially in applications where surfaces might not be perfectly aligned.
Reduced Runoff and Drip
- The thicker nature of high-viscosity adhesive minimizes the likelihood of runoff and drip during application.
- The high viscosity of this adhesive proves particularly useful in vertical or overhead bonding scenarios where traditional adhesives, which have lower viscosity, may struggle to remain in place.
Enhanced Control during Application
- The higher viscosity provides better control over the application process, allowing for precise adhesive placement.
- This characteristic is invaluable in intricate bonding applications, where precision is essential to achieve optimal results.
Increased Bond Strength
- High-viscosity adhesives create a more substantial bond due to their ability to fill voids and ensure complete surface contact.
- The improved contact between surfaces enhances bond strength, making this adhesive ideal for exceptional durability applications.
Ideal for Porous Surfaces
- The thicker consistency of high-viscosity adhesives makes them well-suited for bonding porous surfaces.
- The relevance of this characteristic becomes particularly evident in applications where one or both surfaces are porous or uneven, enabling the adhesive to penetrate and bond within the material.
Extended Open Time
- High-viscosity adhesives often exhibit a longer open time, allowing for extended periods during which the adhesive remains workable.
- This characteristic is advantageous when complex assemblies or adjustments are necessary before the final bonding occurs.
How are high-viscosity adhesives utilized in woodworking and carpentry?
Woodworking and carpentry are intricate crafts that rely heavily on the quality and durability of adhesive bonds. High-viscosity adhesives are pivotal in ensuring robust and lasting connections within these trades. Their unique properties make them indispensable in various applications, revolutionizing how woodworkers approach their projects.
Here’s a closer look at how high-viscosity adhesives are utilized in woodworking and carpentry:
Enhanced Bonding Strength
- Greater Adhesive Thickness:High-viscosity adhesives boast thicker consistencies, enabling them to fill gaps and irregularities in wooden surfaces more effectively than their low-viscosity counterparts.
- Improved Load-Bearing Capacity:These adhesives create stronger bonds, enhancing the load-bearing capacity of joints and connections, crucial for furniture, cabinetry, and structural woodwork.
Diverse Application Scenarios
- Joinery and Framing:They excel in joinery, enhancing the structural integrity of joints in furniture, cabinets, and frames.
- Repair Work:High-viscosity adhesives are instrumental in repairing damaged wood, seamlessly bonding broken pieces, and reinforcing weakened areas.
- Laminations:Woodworkers use them for laminating multiple layers of wood, ensuring a secure and durable bond between the layers.
Adaptability to Various Wood Types
- Hardwoods and Softwoods:These adhesives exhibit versatility, effectively bonding hardwoods and softwoods and catering to various woodworking projects.
- Exotic Woods:They are particularly beneficial when working with exotic woods, ensuring reliable adhesion despite the challenges posed by varying wood densities and grain patterns.
Optimized Workability
- Extended Open Time:High-viscosity adhesives often provide an extended open time, allowing woodworkers more flexibility to adjust and assemble components before the adhesive sets.
- Reduced Run-off:Their thicker consistency minimizes run-off, preventing messy applications and ensuring precise bonding.
Environmental Resilience
- Moisture Resistance:Many high-viscosity adhesives offer excellent moisture resistance, which is crucial in woodworking projects that might be exposed to varying environmental conditions.
- Temperature Tolerance:They maintain their bonding strength across various temperatures, making them suitable for indoor and outdoor applications.
What role do they play in metal fabrication and assembly?
Metal fabrication and assembly are intricate processes that demand precision and durability. Amidst the array of techniques employed, high-viscosity adhesives are indispensable, playing a pivotal role in ensuring metal structures’ structural integrity and performance. These adhesives, characterized by their thick consistency, offer unique advantages in bonding metals together, fostering efficiency and reliability in manufacturing. Let’s delve into their significant role in the realm of metal fabrication and assembly:
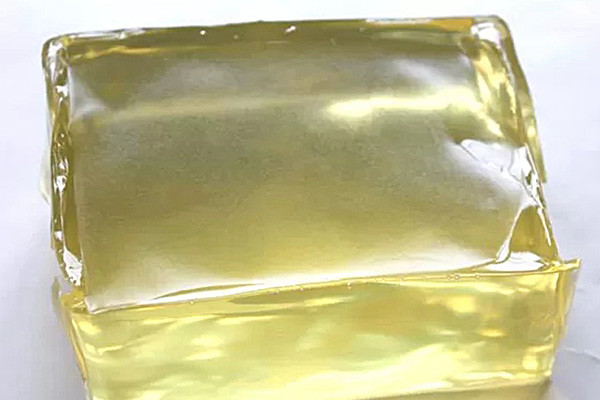
Enhanced Bonding Capabilities
- High-viscosity adhesives boast exceptional bonding capabilities, effectively adhering to steel, aluminum, and alloys.
- Their thicker consistency allows for better gap filling, compensating for irregularities and providing a robust bond, even in challenging conditions.
Stress Distribution and Joint Reinforcement
- In metal assembly, these adhesives serve as stress-distributing agents, evenly spreading mechanical loads across the bonded surface.
- They reinforce joints, mitigating the impact of vibration, thermal expansion, and contraction, thereby enhancing the overall structural stability of fabricated metal components.
Corrosion Resistance and Sealing Properties
- High-viscosity adhesives act as a protective barrier, sealing joints against moisture, chemicals, and corrosive elements, safeguarding the metal structure from degradation.
- Their sealing properties prevent galvanic corrosion, extending the lifespan of assembled metal parts and structures.
Streamlined Manufacturing Processes
- Utilizing high-viscosity adhesives streamlines the fabrication process by eliminating the need for additional mechanical fasteners like rivets or welding.
- These time and cost-saving efficiencies associated with reduced labor and material expenses contribute to an efficient production line.
Customization and Design Flexibility
- These adhesives offer flexibility in design, enabling the bonding of dissimilar materials and intricate geometries expanding the possibilities for innovative metal structures.
- Manufacturers can achieve tailored solutions for specific applications, meeting diverse requirements in the automotive and aerospace industries.
Environmental and Safety Benefits
- Unlike specific welding processes, high-viscosity adhesives emit no hazardous fumes or sparks, ensuring a safer working environment for operators.
- Their application often aligns with eco-friendly practices, promoting sustainability by reducing energy consumption and material waste.
Are there notable applications in marine and underwater environments?
In marine and underwater environments, where harsh conditions and constant exposure to moisture challenge material durability, high-viscosity adhesives emerge as unsung heroes. Their unique properties make them indispensable in various applications, ensuring structural integrity, longevity, and reliability amidst challenging marine settings. Let’s explore the notable applications of high-viscosity adhesives in these demanding environments:
Subsea Structural Bonding
- High-viscosity adhesives are critical bonding agents for underwater structures, effectively adhering to diverse materials such as metals, composites, and plastics.
- Their robust bonding capabilities withstand immense water pressure, providing a secure and durable connection between components, including hulls, frames, and reinforcements.
Sealing and Leak Prevention
- These adhesives act as effective sealants, preventing water ingress and corrosion in joints, seams, and gaps of vessels, submarines, and underwater infrastructure.
- They create a protective barrier, safeguarding against corrosion caused by saltwater and harsh marine elements, enhancing the longevity of submerged structures.
Repair and Maintenance
- In marine environments, quick and reliable repairs are crucial. High-viscosity adhesives facilitate efficient maintenance of damaged or worn-out parts underwater without requiring extensive disassembly.
- Their ability to bond underwater enables in-situ repairs, minimizing downtime and maintenance costs for ships, offshore platforms, and subsea equipment.
Attachment of Subsea Equipment
- These adhesives are key in affixing equipment and sensors to underwater surfaces, ensuring secure attachment without compromising structural integrity.
- They offer a versatile solution for installing instruments, cables, and sensors on submerged structures, enabling effective data collection and monitoring in marine research and exploration.
Protection Against Biofouling
- High-viscosity adhesives contribute to anti-fouling efforts by creating smooth surfaces, inhibiting the attachment of marine organisms like algae and barnacles.
- By reducing biofouling, these adhesives help maintain the efficiency and performance of vessels and underwater equipment.
Challenges in Marine Adhesive Applications
- Despite their resilience, challenges such as exposure to extreme pressures, temperature variations, and chemical interactions in marine environments may impact the longevity of adhesives.
- Ongoing research and development aim to address these challenges, enhancing the durability and performance of high-viscosity adhesives in underwater settings.
How are these adhesives employed in crafting and arts industries?
Adhesives play an indispensable role in crafting and arts, facilitating the creation of intricate designs, robust structures, and innovative projects. Among the plethora of adhesive options available, high-viscosity adhesives stand out for their unique properties and versatile applications within these creative domains.
What are High-Viscosity Adhesives?
- Definition:High-viscosity adhesives are thick, viscous substances with exceptional bonding strength and durability.
- Composition:Typically, these adhesives consist of polymers, resins, and additives that contribute to their high consistency.
Applications in Crafting and Arts
- Bonding Diverse Materials:High-viscosity adhesives excel in connecting various materials, including wood, metal, glass, plastic, fabric, and ceramics, making them a go-to choice for multi-material projects.
- Securing Structural Components:In sculpture and model-making, these adhesives provide structural integrity, holding intricate pieces together securely.
- Enhancing Surface Texture:Crafters use these adhesives to create textures and layers in mixed-media art, adding depth and dimension to their creations.
- Sealing and Finishing:They serve as effective sealants and finishes, protecting artworks from environmental factors and preserving their longevity.
Specific Applications
- Mosaic Art:High-viscosity adhesives are pivotal in mosaic crafting, ensuring durable bonds between small, irregularly shaped pieces of tile or glass.
- Jewelry Making:Crafters use these adhesives to affix gemstones, metal findings, and other embellishments onto jewelry pieces with precision and strength.
- Collage and Mixed Media:Artists leverage their thickness to adhere various materials onto canvases or surfaces, enabling intricate layering and collage work.
Benefits and Considerations
- Strength and Durability:These adhesives offer robust bonding, ensuring the longevity and resilience of crafted items.
- Controlled Application:Their viscosity allows for precise and controlled application, essential for intricate projects.
- Curing Time:While they offer excellent strength, some high-viscosity adhesives might require longer curing times, impacting project timelines.
What are the distinct advantages of using high-viscosity adhesives?
In adhesives, high-viscosity solutions stand out as a powerhouse, offering distinct advantages that cater to various industries and applications. Their unique properties and capabilities make them a preferred choice in diverse scenarios, showcasing unparalleled benefits that set them apart from other adhesive options.
Advantages
Exceptional Bond Strength
- High-viscosity adhesives boast superior bonding strength, creating robust connections between materials and ensuring durability and longevity in the assembled structures.
- Their ability to bond diverse materials, from metals to plastics and ceramics, makes them indispensable in industries requiring multi-material cohesion.
Versatile Applications
- Due to their compatibility with different surfaces and materials, these adhesives find extensive use across industries, from construction to electronics.
- Crafting and arts industries particularly benefit from their versatility, enabling intricate designs and sturdy structural connections.
Enhanced Control and Precision
- The high viscosity of these adhesives allows for controlled application, ensuring precision even in intricate projects or when bonding small components.
- Crafters and engineers appreciate the ability to apply these adhesives precisely, avoiding messy applications and ensuring the right amount of adhesive is used.
Gap-Filling Capabilities
- Their thick consistency allows them to fill gaps and irregularities between surfaces, enhancing the strength of the bond by creating a more comprehensive connection.
- This property makes high-viscosity adhesives ideal for applications where a seamless, gap-free connection is crucial for structural integrity.
Resistance to Environmental Factors
- Many high-viscosity adhesives resist moisture, chemicals, and temperature variations, ensuring the durability of the bond even in challenging environments.
- This resistance makes them suitable for applications where exposure to different conditions is expected, such as outdoor structures or electronic devices.
Long-Term Stability
- Once cured, these adhesives offer long-term stability, maintaining their bonding strength over extended periods without compromising performance.
- Industries often opt for high-viscosity adhesives for their projects when requiring reliable, enduring bonds.
Are there any limitations or challenges associated with their high thickness and application?
High-viscosity adhesive, a powerhouse in bonding materials, is renowned for its robust bonding capability and versatility across various industries. However, while its high thickness and strength offer significant advantages, they also present notable limitations and application challenges that necessitate consideration.
Limitations of High-Viscosity Adhesives
- Limited Flow Properties: The high viscosity in these adhesives restricts their flow, making precise application challenging in intricate or small areas.
- Longer Curing Time:Thicker adhesives often take longer to cure completely, affecting production timelines and efficiency.
- Incompatibility with Some Materials:Certain substrates may not effectively bond with high-viscosity adhesives, leading to adhesion failure.
- Temperature Sensitivity:Extreme temperatures can significantly impact the performance of these adhesives, altering their viscosity and compromising bonding strength.
Challenges in Application
- Precision Application:Due to their high thickness, achieving precision in applying these adhesives, especially in delicate assemblies, can be demanding.
- Uniform Coating:Ensuring a consistent and uniform coating across surfaces becomes challenging, impacting the overall bonding quality.
- Handling and Dispensing:Handling and dispensing high-viscosity adhesives require specialized equipment and meticulous control to prevent wastage and ensure accurate application.
- Surface Preparation:Proper surface preparation is crucial, as the adhesive’s thickness might hinder its ability to penetrate and bond effectively with substrates.
Mitigating Strategies
- Thinning Agents:Introducing compatible thinning agents can help reduce viscosity, enhancing flow without compromising bonding strength.
- Specialized Application Techniques:Utilizing specialized dispensing equipment and techniques tailored for high-viscosity adhesives can improve precision and uniformity in application.
- Surface Treatment:Employing surface treatments like primers or roughening techniques can enhance adhesion on challenging substrates.
- Temperature Control:Maintaining optimal temperature conditions during application and curing stages can mitigate performance issues caused by temperature sensitivity.
How does temperature and environmental conditions affect their performance?
High-viscosity adhesives play a pivotal role across industries, offering robust bonding solutions for various materials. However, their performance is significantly influenced by temperature and environmental conditions. Understanding these impacts is crucial for optimizing their efficacy in diverse applications.
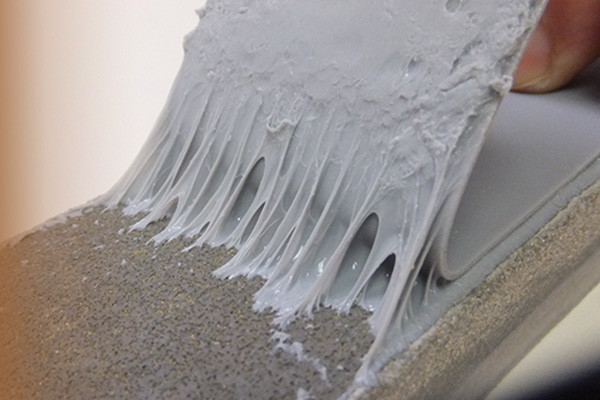
Temperature Variations
- Viscosity Changes:High-viscosity adhesives are sensitive to temperature fluctuations. As temperatures rise, these adhesives become less viscous, altering their flow properties. Conversely, colder temperatures can increase viscosity, making application challenging.
- Curing Process:Temperature directly affects the curing process of adhesives. Higher temperatures often accelerate curing, reducing the overall bonding time. Conversely, lower temperatures slow curing, prolonging the bonding process and potentially compromising bond strength.
- Thermal Stability:Extreme temperatures can compromise the adhesive’s thermal stability, affecting its overall performance. Excessive heat may lead to degradation or reduced bond strength, while extreme cold can cause brittleness or loss of adhesive properties.
Environmental Conditions
- Humidity Levels:High levels of humidity can impact adhesive performance. Moisture-sensitive adhesives may experience reduced bonding strength or slower curing rates in humid environments, potentially leading to inadequate bonding.
- Chemical Exposure:Environmental exposure to certain chemicals can adversely affect high-viscosity adhesives. Chemicals in the surroundings might react with the adhesive, altering its properties and diminishing its bonding capabilities.
- UV Radiation:Adhesives exposed to prolonged sunlight or UV radiation can undergo degradation. This exposure can lead to changes in adhesive composition, causing reduced bond strength and compromising the integrity of the bond over time.
Optimizing Performance
- Temperature Control:Maintaining controlled temperatures during storage and application is critical. Adhesive manufacturers often provide recommended temperature ranges for storage and application to ensure optimal performance.
- Surface Preparation:Proper surface preparation is vital for maximizing bond strength. Surfaces should be clean, dry, and contaminant-free to facilitate strong adhesion.
- Adhesive Selection:Considering environmental factors and application requirements, choosing the proper adhesive formulation becomes crucial. Some adhesives are designed to withstand specific environmental conditions better than others.
- Testing and Validation:Regular testing and validation of adhesive performance under varying temperatures and environmental conditions are essential. To guarantee the dependability of the adhesive in practical situations, it undergoes thorough testing.
How does the formulation of these adhesives impact their viscosity?
High-viscosity adhesives stand out in various industries due to their robust bonding capabilities. Their viscosity, a key characteristic, is directly influenced by the intricate formulation processes they undergo. Understanding how formulation impacts viscosity is fundamental to leveraging these adhesives effectively.
Ingredients and Proportions
- Resin Selection:The choice of resin significantly influences viscosity. Resins with higher molecular weights often result in higher viscosity adhesives. Conversely, lower molecular weight resins tend to yield more inferior viscosity adhesives.
- Fillers and Additives:Fillers and additives are crucial in adjusting viscosity. Fillers like silica or calcium carbonate can increase viscosity, while plasticizers or solvents may lower it. The proportions of these components determine the final viscosity of the adhesive.
Chemical Reactions and Crosslinking
- Polymerization: Polymerization reactions during adhesive formulation impact viscosity. Higher degrees of polymerization lead to longer molecular chains, resulting in higher viscosity due to increased entanglement of these chains.
- Crosslinking Agents:Including crosslinking agents influences viscosity by connecting polymer chains. More crosslinking typically leads to a thicker, higher-viscosity adhesive due to increased molecular entanglement.
Temperature and Cure Rate
- Cure Initiators:Formulation includes cure initiators that affect viscosity. Some initiators might initially decrease viscosity to facilitate application but then trigger a rapid increase in viscosity during the curing process.
- Temperature Sensitivity:Formulation components may respond differently to temperature changes. Some adhesives exhibit lower viscosity at higher temperatures, making application easier, while they thicken upon cooling, aiding in bond formation.
Role of Solvents
- Solvent-based Formulations:Solvents in formulations impact viscosity, initially lowering it for ease of application. As solvents evaporate during curing, viscosity increases, contributing to stronger bonds.
- Solvent Selection:Different solvents have varied impacts on viscosity. Some solvents evaporate quickly, leading to a rapid increase in viscosity, while others evaporate slowly, maintaining lower viscosity for a longer duration.
Optimizing Formulation for Application
- Tailored Viscosity:Formulation engineers tailor adhesives to specific viscosities to suit application requirements, ensuring optimal performance and ease of use.
- Consistency Control:Consistency in formulation is crucial to maintaining batch-to-batch viscosity uniformity, ensuring predictable adhesive performance.
- Application-specific Formulation:Adhesive formulations can be customized for different applications by adjusting ingredients and proportions to achieve the desired viscosity and bonding characteristics.
What role does temperature control play in maintaining optimal viscosity?
High-viscosity adhesives are essential in various industries, providing strong and durable bonds for multiple applications. However, achieving and maintaining optimal viscosity is crucial for the effectiveness of these adhesives. One key factor that significantly influences viscosity is temperature. In this article, we will explore the role of temperature control in ensuring the ideal viscosity of high-viscosity adhesives.
Why Viscosity Matters
Viscosity is a measure of a fluid’s resistance to flow, and for high-viscosity adhesives, it determines their ability to adhere to surfaces and form a reliable bond. Maintaining the correct viscosity is essential for several reasons:
- Application Consistency:Optimal viscosity ensures that the adhesive spreads evenly during application, preventing uneven bonding and potential weak points in the bond.
- Bond Strength:The adhesive’s viscosity directly impacts the bond’s strength. If the viscosity is too low, the adhesive may not provide sufficient coverage, leading to weakened bonds. On the other hand, if it’s too high, it may not spread adequately, resulting in incomplete bonding.
- Curing Process:Many high-viscosity adhesives rely on a curing process to achieve maximum bond strength. Proper viscosity ensures the adhesive cures uniformly, creating a solid and durable bond.
The Influence of Temperature on Viscosity
Temperature plays a pivotal role in determining the viscosity of high-viscosity adhesives. The relationship between temperature and viscosity can be summarized as follows:
- Temperature Sensitivity:High-viscosity adhesives are often temperature-sensitive, meaning their viscosity changes with temperature variations.
- Viscosity Reduction at Higher Temperatures:As the temperature increases, the viscosity of many adhesives tends to decrease. This reduction in viscosity allows for more accessible application and better penetration into substrate surfaces.
- Viscosity Increase at Lower Temperatures:Conversely, lower temperatures can lead to an increase in viscosity. The presence of contaminants can affect the adhesive’s flow properties, making the application challenging and potentially compromising the bond quality.
The Importance of Temperature Control
Maintaining optimal viscosity for high-viscosity adhesives requires precise temperature control throughout the application and curing processes. Temperature control is crucial for the following reasons:
- Consistent Performance:Precise temperature control ensures that the adhesive maintains its intended viscosity consistently, resulting in uniform application and bond strength.
- Enhanced Application Flexibility:Temperature control allows for adjustments based on specific application requirements, providing flexibility in various working conditions.
- Improved Curing:Controlling temperature during the process ensures that the adhesive cures uniformly, maximizing bond strength and durability.
Are there specific application techniques to optimize bonding with high-viscosity adhesives?
High-viscosity adhesives are a cornerstone in various industries, offering robust bonding solutions for diverse materials. However, achieving optimal bonding requires more than just applying the adhesive. Specific application techniques play a pivotal role in maximizing the efficacy of high-viscosity adhesives.
Here are essential techniques and applications to enhance bonding with high-viscosity adhesives:
Surface Preparation
- Cleaning:Ensure surfaces are free from dust, grease, and contaminants. Use solvents or cleaners suitable for the materials involved.
- Roughening: Abrade smooth surfaces to enhance adhesive contact and bonding strength, especially with non-porous materials like metals or plastics.
- Priming:Apply a primer designed for high-viscosity adhesives to promote adhesion, particularly on challenging surfaces.
Application Methods
- Uniform Application:Use precision applicators or dispensing equipment to apply the adhesive evenly across the bonding area.
- Temperature Control:Maintain optimal temperature conditions for the adhesive, as it can affect viscosity and curing time. Warm adhesives may flow better, while colder temperatures can slow down curing.
- Correct Quantity:Apply the right amount of adhesive; excessive or insufficient amounts can compromise bonding strength.
Bonding Techniques
- Clamping or Pressing:Apply pressure to the bonded surfaces using clamps or presses to ensure intimate contact between the adhesive and materials. These characteristics aid in reducing voids and enhancing the bond strength.
- Curing Conditions:Follow recommended conditions such as time and temperature for the adhesive to achieve its full strength potential.
- Mechanical Fasteners:Combine high-viscosity adhesives with mechanical fasteners for added strength and stability in load-bearing applications.
Specific Applications
- Automotive Industry:High-viscosity adhesives are used for structural bonding in car body assembly, providing durability and crash resistance.
- Aerospace Sector:These adhesives find application in aircraft assembly and bonding components for their lightweight, high-strength properties.
- Construction and Infrastructure:High-viscosity adhesives are employed for bonding heavy-load-bearing structures, offering resilience against various environmental conditions.
Considerations for Success
- Material Compatibility:Ensure compatibility between the adhesive and the bonded materials for optimal performance.
- Safety Measures:Adhere to safety guidelines and use appropriate personal protective equipment during adhesive handling and application.
- Testing and Validation:Conduct adhesive testing to validate bonding strength and durability under anticipated operating conditions.
How does proper surface preparation impact the effectiveness of these adhesives?
In industrial adhesives, high-viscosity adhesives ensure robust bonding for various applications. However, their effectiveness hinges significantly on proper surface preparation. In this article, we delve into the importance of surface preparation and how it directly impacts the performance of high-viscosity adhesives.
Surface Cleanliness
- High-viscosity adhesives adhere best to clean surfaces.
- Contaminants like dust, oils, or residues can compromise bond strength.
- Thorough cleaning ensures a pristine surface for optimal adhesive interaction.
Surface Roughness
- Adequate roughness enhances adhesive contact and bonding.
- Proper surface preparation, such as abrasion or etching, creates a microstructure conducive to adhesion.
- The increased surface area allows the adhesive to establish a stronger grip.
Adhesive Wetting
- Surface preparation facilitates proper wetting of the substrate by the adhesive.
- Complete wetting ensures intimate contact, reducing the chances of voids or air pockets in the bond line.
- Optimal wetting contributes to the adhesive’s ability to spread and form a uniform layer.
Removal of Oxides and Corrosion
- Metals may develop oxides or corrosion, hindering adhesion.
- Surface preparation methods like acid etching or priming eliminate these barriers.
- Clean metal surfaces enable high-viscosity adhesives to bond robustly with the substrate.
Compatibility with Substrates
- Different materials require specific surface preparation techniques.
- Proper surface preparation ensures compatibility between the substrate and adhesive.
- Compatibility is essential for long-term adhesion strength and durability.
Improved Adhesive Penetration
- High-viscosity adhesives may struggle to penetrate porous or uneven surfaces.
- Surface preparation methods, such as vacuum impregnation, enhance adhesive penetration.
- Its improved penetration results in a more effective bond throughout the substrate.
Environmental Factors
- Surface preparation considers environmental conditions.
- Humidity, temperature, and substrate condition impact the adhesive’s performance.
- Tailoring surface preparation to these factors ensures consistent and reliable bonding.
What are the standard methods for testing the strength of high-viscosity adhesives?
High-viscosity adhesives are the backbone for sturdy bonds across diverse industries, from construction to automotive and aerospace. Ensuring the reliability and strength of these bonds is crucial, making rigorous testing methodologies indispensable. Here, we explore the standard methods employed to assess the stability of high-viscosity adhesives:
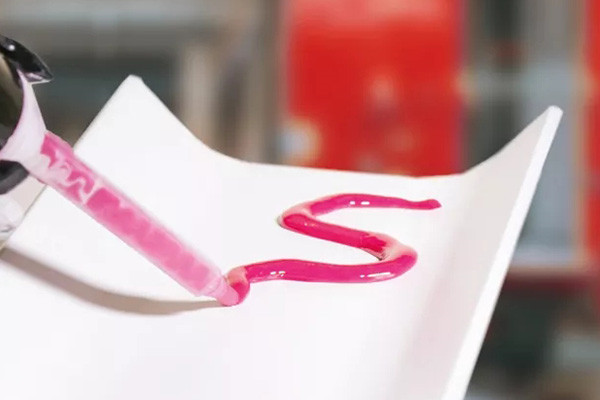
Lap Shear Testing
- Measures the adhesive strength by subjecting a bonded assembly to shear stress.
- They are commonly used for evaluating the strength of adhesives on flat substrates.
- This test provides insight into the cohesive strength of the adhesive itself.
Tensile Testing
- Determines the maximum tensile force an adhesive can withstand.
- It involves pulling apart bonded substrates in opposite directions until failure.
- Evaluates the bond’s ability to withstand tension, revealing both adhesive and cohesive properties.
Peel Testing
- Assesses the strength required to peel apart bonded materials.
- Measures the force needed to separate flexible substrates bonded with the adhesive.
- Reveals the bond’s resistance to delamination or separation under peeling stress.
Cleavage Testing
- The adhesion between two materials is evaluated by applying a force perpendicular to the bonded surfaces.
- Assess the resistance of the adhesive to splitting or separating substrates.
Climbing Drum Peel Testing
- Determines the peel strength of an adhesive at a constant rate while wrapped around a drum.
- They are commonly used for flexible laminates or films to measure the bond’s resistance to peeling forces.
Impact Testing
- Assesses the ability of the adhesive to withstand sudden impacts.
- It involves subjecting the bonded samples to a controlled impact to evaluate their resilience.
Environmental Testing
- The test evaluates adhesive strength under varying environmental conditions.
- Tests include exposure to temperature extremes, humidity, or chemicals to assess long-term durability.
Durability and Aging Tests
- Assess how the adhesive bond withstands aging and environmental stresses over time.
- It helps predict the adhesive’s longevity and performance in real-world conditions.
How is the reliability and durability of these adhesives evaluated considering their high thickness?
High-viscosity adhesives have become indispensable in various industries due to their ability to bond diverse materials effectively. Their distinct trait lies in their thick consistency, offering robust adhesion and structural support. However, due to their high thickness, evaluating their reliability and durability becomes a critical concern. Here’s an exploration of the methods and considerations in assessing these adhesives:
Characteristics of High-Viscosity Adhesives:
- Consistency:These adhesives possess a high thickness or viscosity, ensuring strong bonding capabilities.
- Versatility:They cater to various substrates, from metals and plastics to composites and ceramics.
- Curing Mechanism:Some may require heat or time to cure fully, affecting their bonding strength and durability.
Evaluation Methods for Reliability
- Shear Strength Tests:Assessing the adhesive’s resistance to forces applied parallel to the bonded surfaces.
- Tensile Testing:Evaluating the adhesive’s capacity to withstand pulling forces perpendicular to the bond.
- Peel Tests: Determining the adhesive’s ability to withstand delamination or separation under stress.
- Aging Studies:Monitoring the adhesive’s performance over time to gauge its long-term reliability.
Factors Impacting Durability
- Substrate Compatibility:Compatibility with various materials affects the adhesive’s long-term durability.
- Environmental Conditions:Exposure to moisture, temperature variations, and chemicals can impact adhesive performance.
- Application Method:Proper application techniques significantly influence the adhesive’s durability.
- Curing Time and Conditions:Inadequate curing might compromise the adhesive’s durability and reliability.
Challenges in Evaluation
- Thick Application:The thickness of high-viscosity adhesives poses challenges in achieving uniform application, affecting reliability.
- Non-Destructive Testing:Limited methods for non-destructive evaluation of thick adhesives can hinder comprehensive assessments.
Advanced Testing Techniques
- Ultrasonic Testing:Utilizing sound waves to assess bond integrity without damaging the bond.
- Thermal Imaging: Monitoring temperature changes during curing to ensure uniformity and strength.
- Microscopy and Spectroscopy:Analyzing adhesive structures and chemical compositions for defects or inconsistencies.
Industry Standards and Quality Control
- Adherence to Standards:Established industry standards ensure reliability and predictability in adhesive performance.
- Quality Control Measures:Stringent quality control procedures during manufacturing are crucial for ensuring consistent adhesive properties.
Are there specific tests for assessing long-term performance or resistance to varying stresses?
High-viscosity adhesives are invaluable in industries ranging from aerospace to construction, known for their ability to bond diverse materials. However, ensuring their long-term performance and resilience against varying stresses requires precise testing methodologies. Are there specific tests designed to evaluate these crucial aspects?
Understanding Long-Term Performance
High-viscosity adhesives serve critical functions in environments subject to dynamic stresses, temperature fluctuations, and exposure to harsh conditions. Assessing their long-term performance involves a series of comprehensive tests:
Accelerated Aging Tests
- Exposure to elevated temperatures and humidity mimics extended use over time.
- The evaluation process assesses changes in adhesive properties, encompassing strength, flexibility, and chemical resistance.
Environmental Chamber Testing
- Subjects adhesive to extreme temperature variations, moisture, and UV exposure.
- This assessment evaluates the durability of these adhesives under real-world environmental conditions.
Mechanical Stress Testing
- This test determines the adhesive performance under various loads, including shear and tensile stresses.
- Evaluates the adhesive’s ability to maintain structural integrity over extended periods.
Creep and Fatigue Testing
- Measures how an adhesive responds to constant stress or repeated loading.
- It helps identify potential deformations or failures over time.
Chemical Resistance Testing
- The examination involves assessing the adhesive’s resilience against various chemicals, solvents, and environmental contaminants.
- Ensures stability and functionality when exposed to corrosive elements.
Thermal Cycling Tests
- Subjects adhesives to alternating hot and cold cycles.
- Assesses their ability to withstand thermal expansion and contraction without compromising bonding strength.
Pull-off Tests
- Evaluates the adhesive bond strength by applying force perpendicular to the adhesive surface.
- It helps determine adhesion quality and durability.
Real-World Simulation Testing
- Mimics actual operating conditions the adhesive would face in its application environment.
- This analysis offers insights into the adhesive’s performance and reliability throughout its intended lifespan.
What advancements are anticipated in high-viscosity adhesive technology?
Due to their robust bonding capabilities, high-viscosity adhesives have long been pivotal in various industries, from construction to electronics. As technology evolves, so does the potential for advancements in high-viscosity adhesive technology. Here are the anticipated breakthroughs set to revolutionize this essential adhesive domain:
- Nanotechnology Integration:The integration of nanotechnology within high-viscosity adhesives is projected to enhance their performance significantly. Nano-sized particles incorporated into these adhesives promise superior strength, increased heat resistance, and improved adhesion on diverse surfaces.
- Enhanced Durability and Flexibility:Anticipate advancements that bolster the durability and flexibility of high-viscosity adhesives. Innovations may yield adhesives capable of withstanding extreme conditions, such as temperature variations, moisture, and chemical exposure, without compromising their bonding integrity.
- Environmental Sustainability:The future of adhesive technology leans toward sustainability. Expect advancements focusing on eco-friendly formulations, reducing volatile organic compounds (VOCs), and adopting renewable materials without sacrificing adhesive performance. Bio-based alternatives might emerge, minimizing environmental impact.
- Smart Adhesives:Advancements may introduce “smart” high-viscosity adhesives with unique functionalities. These adhesives could possess self-healing properties, adapt to minor damages, or exhibit stimuli-responsive behavior, enabling activation or deactivation under specific conditions.
- Improved Application Techniques:Anticipate advancements not only in adhesive composition but also in application techniques. Precision dispensing methods, automated application processes, and customized adhesive solutions tailored to specific industries may become more prevalent.
- Adherence to Industry Regulations:Future advancements in high-viscosity adhesive technology will likely align with stringent industry regulations. Expect developments focusing on compliance with safety standards, ensuring these adhesives meet or exceed regulatory requirements across different sectors.
- Digitalization and Data-Driven Solutions:Integrating digital technologies might revolutionize the adhesive industry. These approaches involve utilizing data-driven methods for adhesive selection, employing predictive analytics to assess performance, and developing virtual models to understand adhesive behavior in various applications.
- Multi-Substrate Bonding Capabilities:Future high-viscosity adhesives will exhibit improved bonding capabilities across diverse substrates, including metals, plastics, ceramics, and composites. This enhancement will cater to the evolving needs of industries requiring versatile bonding solutions.
High-viscosity adhesives form the backbone of many industrial processes, and their anticipated advancements signify a promising future. The convergence of innovative materials, sustainability initiatives, and technological progress is poised to redefine the capabilities and applications of these adhesives across various sectors.
How might these innovations impact various industries and reshape bonding techniques in the future?
The continuous evolution of high-viscosity adhesive technology is poised to impact various industries significantly, revolutionizing bonding techniques and ushering in a new era of possibilities. These innovations are anticipated to bring forth transformative changes across sectors:
- Construction Industry:High-viscosity adhesives are integral in construction for structural bonding. Innovations promising increased durability and flexibility will strengthen bonds between concrete, metals, and composites. This advancement could streamline construction processes, reducing reliance on traditional methods like welding and bolting.
- Automotive Sector:Advancements in high-viscosity adhesives can revolutionize vehicle assembly. Enhanced adhesives with superior strength and heat resistance may replace mechanical fasteners, reducing weight, enhancing fuel efficiency, and improving overall vehicle performance.
- Electronics Manufacturing:In the electronics industry, miniaturization is crucial. Nanotechnology integration in adhesives will enable finer bonding, supporting the assembly of smaller components with higher precision. Innovative adhesives could offer self-healing properties, ensuring circuit integrity and reliability.
- Aerospace and Defense:High-viscosity adhesives play a vital role in aerospace applications. Innovations fostering resilience against extreme conditions, such as temperature variations and high-stress environments, will elevate safety standards and durability in aircraft and defense systems.
- Medical Field:Advancements in high-viscosity adhesives may transform medical device manufacturing. Bio-compatible and sterilizable adhesives will be pivotal in producing medical equipment, enabling secure bonding in devices like implants and wearable medical tech.
- Renewable Energy Sector:As the demand for renewable energy grows, advancements in adhesives will impact the assembly of solar panels, wind turbines, and battery technologies. Adhesives that withstand harsh environmental conditions will ensure the longevity and efficiency of these energy systems.
These innovations will reshape bonding techniques by
- Enhancing Efficiency:High-viscosity adhesives with improved bonding capabilities will streamline manufacturing processes, reducing assembly time and labor costs.
- Enabling Versatility:Adhesives capable of bonding diverse substrates will offer flexibility in material selection, allowing for innovative designs and improved product performance.
- Promoting Sustainability:Eco-friendly formulations and reduced VOCs will align with sustainability goals, minimizing environmental impact across industries.
- Driving Automation:Advanced application techniques and innovative adhesives will integrate with automated systems, enabling precise and consistent application, thus boosting productivity.
CONCLUSION
In concluding this exploration into the realm of high-viscosity adhesives, it becomes evident that these formidable compounds stand as stalwarts of bond strength. Their remarkable attributes, from fostering durability in woodworking and metal fabrication to their surprising resilience in marine and arts industries, underscore their versatility and robustness. Despite their thick consistency posing challenges in application, the advantages they offer in bond strength remain unparalleled. The continual evolution of adhesive technology anticipates promising advancements, potentially reshaping various industries and paving the way for innovative bonding techniques. As we bid adieu to this discourse, it’s clear that high-viscosity adhesives aren’t merely solutions but catalysts, urging us to embrace their power for unparalleled bonding needs, fostering reliability and enduring strength where it’s needed most.
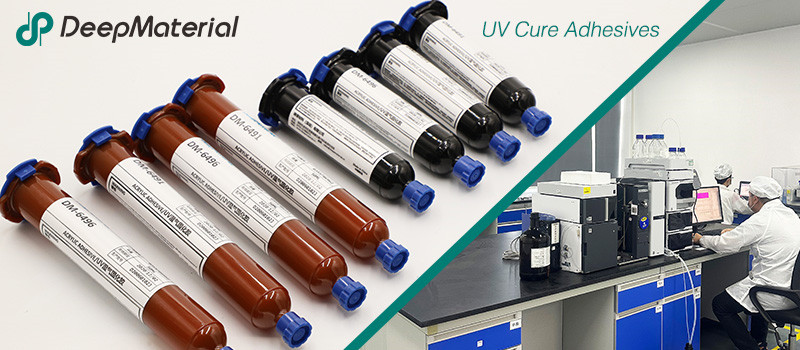
DeepMaterial
Based on the core technology of adhesives, DeepMaterial has developed adhesives for chip packaging and testing, circuit board level adhesives, and adhesives for electronic products. Based on adhesives, it has developed protective films, semiconductor fillers, and packaging materials for semiconductor wafer processing and chip packaging and testing. More…
UV Curing Adhesives
UV light cure have a number of benefits making them a popular choice among many product assembly and manufacturing applications. Many UV light cure adhesives can provide a nearly instantaneous bond to difficult substrates like glass and plastic. UV cure adhesives often require an accelerator or UV light for a bond to form.
Adhesive Blogs & News
The latest adhesive industry science and technology, Deepmaterial news, and market trends and forecasts.
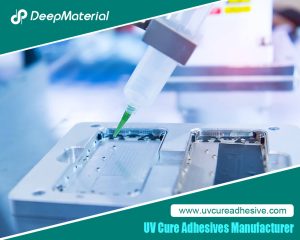
The Quantitative Influence of Crosslinking Density on the Flexibility and Hardness of Adhesives and the Formulation Optimization Strategy
The Quantitative Influence of Crosslinking Density on the Flexibility and Hardness of Adhesives and the Formulation Optimization Strategy This article systematically expounds the quantitative relationship between the crosslinking density and the flexibility and hardness of adhesives. Combining the theories of polymer physics with experimental analysis methods, it reveals the mechanism of the action of the
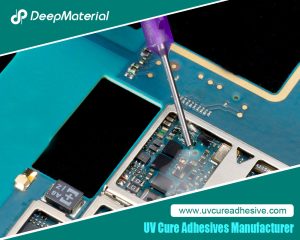
Technical Strategies for Balancing the Rapid Curing Property and Long Operating Time of UV Adhesives
Technical Strategies for Balancing the Rapid Curing Property and Long Operating Time of UV Adhesives UV adhesives have been widely used in many fields such as electronics, optics, and medicine due to their advantages of rapid curing, high bonding strength, and environmental protection. However, their rapid curing property also brings challenges in some application scenarios.
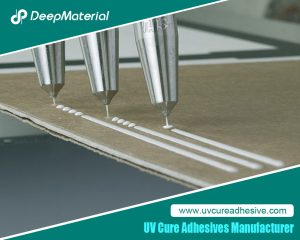
Biocompatibility of LED UV Glue Adhesive and Its Application Potential in Medical and Food Packaging Fields
Biocompatibility of LED UV Glue Adhesive and Its Application Potential in Medical and Food Packaging Fields LED UV glue adhesive has been widely applied in numerous fields due to its advantages such as rapid curing and easy operation. However, in fields with stringent safety requirements like medical and food packaging, its biocompatibility after curing
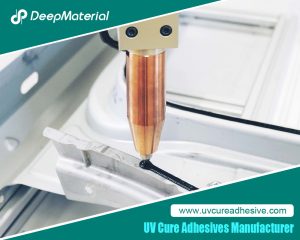
Exploring the Environmental Performance of UV Glue and Strategies for Optimizing Odor and VOC Content
Exploring the Environmental Performance of UV Glue and Strategies for Optimizing Odor and VOC Content UV glue, as an adhesive that achieves rapid curing through ultraviolet (UV) light irradiation, has been widely applied in numerous fields such as electronics, optics, healthcare, and automobiles, thanks to its advantages of fast curing speed, high bonding strength, and
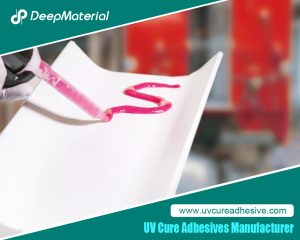
Compatibility Analysis and Countermeasures of LED UV Glue with Automated Production Equipment
Compatibility Analysis and Countermeasures of LED UV Glue with Automated Production Equipment LED UV glue has been widely used in modern manufacturing due to its advantages such as fast curing speed, high bonding strength, and environmental friendliness. However, in the automated production process, if there are problems with the adaptability between the glue and equipment
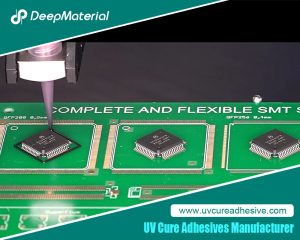
Influence of Viscosity and Thixotropy of Glue on the Quality of Glue Dots in the Dispensing Process and Solutions
Influence of Viscosity and Thixotropy of Glue on the Quality of Glue Dots in the Dispensing Process and Solutions The dispensing process is an important part of the application of LED UV glue adhesive, and the quality of this process directly affects the final performance of the product. The physical properties of the glue,