- Home
- >
- Application
- >
- TWS Headset Adhesive
TWS Headset Adhesive
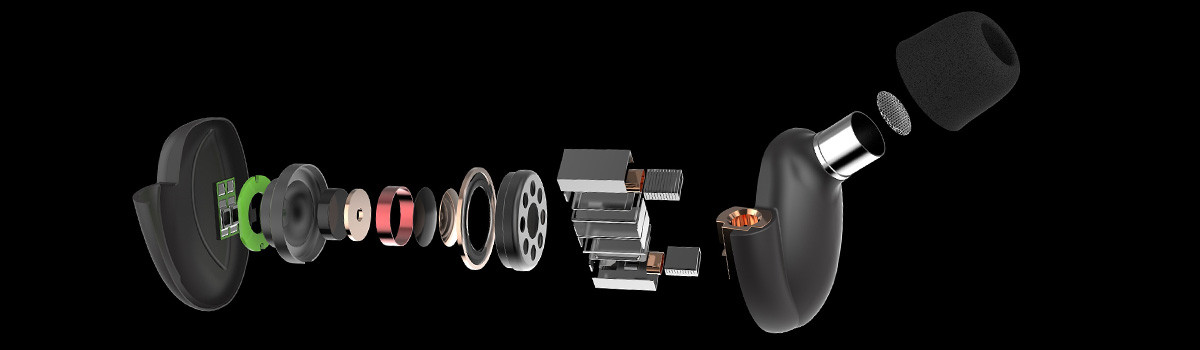
TWS (True Wireless Stereo) Headset Adhesives. As technology advances, TWS headsets have become an integral part of our daily lives, offering a seamless audio experience without the constraints of wires. However, ensuring the longevity and reliability of these devices often requires the right adhesive solutions. This guide will explore various aspects of TWS headset adhesives, addressing common questions and providing insights into this essential component.
Table of Contents
ToggleWhat is TWS Headset Adhesive, and what is its importance?
“TWS” typically stands for “True Wireless Stereo,” which refers to wireless audio devices such as earbuds or headphones that do not have a physical connection between the left and right units. These devices often rely on Bluetooth technology for wireless connectivity.
If someone is referring to “TWS Headset Adhesive,” it could potentially be a specialized adhesive designed for repairing or securing components of True Wireless Stereo headsets. In electronic devices like TWS headsets, adhesives are often used to bond components together or secure certain elements within the device’s housing.
The importance of such adhesives in the context of TWS headsets or any electronic device lies in their ability to provide structural integrity, prevent component movement, and maintain the overall functionality of the device. Adhesives can be crucial for ensuring that delicate electronic components stay in place, especially in compact and intricate devices like TWS headsets.
How Does Adhesive Contribute to TWS Headset Durability?
Adhesive plays a crucial role in contributing to the durability of True Wireless Stereo (TWS) headsets. TWS headsets are compact devices with individual earbuds, a charging case, and various electronic components. The adhesive is used in several key areas to enhance the durability and structural integrity of these devices:
- Assembly of Components:TWS headsets comprise numerous small components, such as speakers, microphones, batteries, and circuit boards. The adhesive is often used to bond these components securely during manufacturing. This helps prevent the internal parts from shifting or coming loose over time, which is especially important in portable devices that may experience vibrations and movement.
- Sealing and Water Resistance:Many TWS headsets are designed to be water-resistant or even waterproof to some extent. Adhesives are used to create seals that protect the internal components from moisture, sweat, and other environmental factors. This is essential for ensuring the longevity of the headset, especially since exposure to water can lead to corrosion and damage to electronic components.
- Structural Integrity:Adhesives are employed to reinforce the structural integrity of the headset, particularly in areas where different materials meet or where stress points may occur. By bonding materials, adhesives can provide additional strength and prevent components from breaking or separating, even under stress or impact.
- Cable Management:TWS headsets often include internal wiring to connect the various components. Adhesives can be used to secure and organize these cables, preventing them from getting tangled or damaged. This helps maintain the electrical connections and ensures the headset functions correctly over time.
- Vibration Damping:TWS headsets are frequently subjected to vibrations during regular use, such as when the user is walking or jogging. Adhesives with vibration-damping properties can be applied to reduce the impact of vibrations on internal components, thereby preventing potential damage and improving the overall durability of the headset.
- Aesthetics and Design:Adhesives also play a role in the overall design and aesthetics of TWS headsets. They allow for seamless integration of different materials, create smooth surfaces, and contribute to a sleek and attractive appearance.
Adhesive contributes significantly to the durability of TWS headsets by securing components, providing water resistance, enhancing structural integrity, managing cables, dampening vibrations, and contributing to the device’s overall design. These factors collectively contribute to a longer lifespan and improved performance of the TWS headset.
Are TWS Headset Adhesives Different from Traditional Adhesives?
The term “TWS headset adhesives” is not a standard or specific category of adhesives. TWS stands for True Wireless Stereo, a wireless audio technology often used in earbuds. Discussing adhesives in the context of TWS headsets likely refers to the adhesives used in the manufacturing and assembly of these earbuds.
Generally, the adhesives used in electronic devices, including TWS headsets, may have specific characteristics tailored to the materials and components involved. The choice of adhesive can depend on the bonded materials, the manufacturing process, and the desired properties like strength, flexibility, and conductivity.
However, there is no inherent difference between adhesives used in TWS headsets and those used in other electronic devices or products. Adhesives come in various types, such as epoxy, cyanoacrylate (super glue), silicone, and others, and their suitability depends on the application’s specific requirements.
Suppose you are referring to the adhesive used in constructing the earbuds themselves. In that case, manufacturers typically choose adhesives that provide a secure bond between components, ensure durability, and are compatible with the materials used in the earbuds’ construction.
TWS headset adhesives are not fundamentally different from traditional adhesives. The choice of adhesive depends on the specific needs of the manufacturing process and the materials involved, regardless of whether it’s for TWS headsets or other electronic devices.
Which Materials are Compatible with TWS Adhesives?
“TWS” typically refers to “Two-Component Epoxy Adhesives,” which consist of two parts: a resin and a hardener. The compatibility of these adhesives depends on the materials being bonded. Generally, epoxy adhesives are versatile and can connect well with various materials. Here are some common materials that are compatible with TWS (Two-Component Epoxy) adhesives:
Metals:
- Aluminum
- Steel
- Stainless steel
- Copper
Plastics:
- PVC (Polyvinyl chloride)
- ABS (Acrylonitrile Butadiene Styrene)
- Polycarbonate
- Nylon
Ceramics:
- Porcelain
- Ceramic tiles
Wood:
- Hardwood
- Softwood
- Plywood
Glass:
- Borosilicate glass
- Tempered glass
Composites:
- Fiberglass
- Carbon fiber-reinforced composites
Rubber:
- Some types of rubber, depending on the formulation
Stone:
- Granite
- Marble
Electronic Components:
- TWS adhesives are often used to bond components like circuit boards in electronic applications.
It’s important to note that the specific formulation of the epoxy adhesive and the surface preparation of the bonded materials can affect the bond strength and compatibility. Additionally, some materials may require surface treatment (such as abrasion or chemical treatment) to improve adhesion.
Always refer to the manufacturer’s guidelines and recommendations for the specific epoxy adhesive you are using, as they may provide information on compatibility with different materials and any necessary surface preparations. Testing the adhesive on a small, inconspicuous area before complete application is also a good practice, especially in critical applications.
What Role Does Adhesive Play in Water Resistance of TWS Headsets?
Several factors influence the water resistance of True Wireless Stereo (TWS) headsets, and the adhesive used in their construction can play a role in this regard. Here are some ways in which adhesive contributes to water resistance:
- Sealing Components:Adhesives are often used to seal the various components of TWS headsets, such as the housing, buttons, and seams. By creating a tight seal, adhesive helps prevent water from entering the sensitive electronic components of the headset. This is crucial for maintaining the device’s functionality and preventing damage from moisture.
- Bonding and Encapsulation:Adhesives bond different parts of the TWS headset together. This bonding process not only ensures the structural integrity of the device but also prevents water from infiltrating through gaps or openings. Some adhesives also provide a protective layer or encapsulation around electronic components, shielding them from direct contact with water.
- Material Compatibility:The choice of adhesive is essential in ensuring compatibility with the materials used in constructing the TWS headset. Water-resistant adhesives are often designed to adhere well to plastics, metals, and other materials commonly found in electronic devices. This compatibility helps maintain the integrity of the seals and bonds over time, even when exposed to moisture.
- Durability and Longevity:Water-resistant adhesives are typically designed to withstand the rigors of daily use and exposure to environmental factors. They are chosen for their durability and resistance to degradation over time. This is important for maintaining the water resistance of the TWS headset throughout its lifespan.
- Testing and Certification:Adhesive choices may be part of manufacturers’ overall design and engineering considerations when testing TWS headsets for water resistance. The adhesive and other components contribute to the overall water-resistant design, and the final product may undergo specific testing procedures to ensure it meets certain standards (e.g., IPX4, IPX7) for water resistance.
Notably, achieving water resistance in electronic devices involves design elements, material choices, and manufacturing processes. Adhesives are just one component of this overall strategy, and manufacturers often use a combination of techniques and materials to enhance the water resistance of TWS headsets.
How do you properly apply adhesive for TWS Headset Repairs?
Repairing a TWS (True Wireless Stereo) headset often involves using adhesive to secure components or to reattach parts that may have come loose. Here’s a general guide on how to properly apply adhesive for TWS headset repairs:
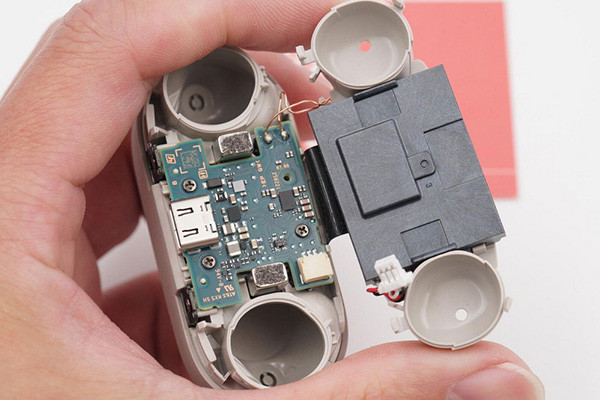
Materials Needed:
- Adhesive:Use an appropriate adhesive for electronics. Standard options include cyanoacrylate (super glue) or a specialized electronics adhesive.
- Cleaning Supplies:Isopropyl alcohol and lint-free wipes to clean surfaces before applying adhesive.
- Precision Tools:Tweezers, small screwdrivers, or other tools needed for disassembly and reassembly.
- Clamps or Pressure:Depending on the repair, you might need clamps or some form of pressure to hold parts together while the adhesive sets.
Steps:
Disassembly:
- Carefully disassemble the TWS headset, noting where each component is located.
- If you’re reattaching a specific part, ensure the surfaces are clean and free from old adhesive or debris.
Cleaning:
- Clean the surfaces that will be bonded using isopropyl alcohol and a lint-free cloth. This ensures a strong bond by removing dirt, oils, or residues.
Choosing the Right Adhesive:
- Select an adhesive suitable for electronics and the materials you are bonding. For TWS headsets, cyanoacrylate (super glue) is commonly used due to its fast bonding properties. However, be cautious as some adhesives can damage certain materials, so choose one safe for plastics and electronics.
Applying the Adhesive:
- Apply a small amount of adhesive to one of the surfaces. Be precise, as too much adhesive can create a messy repair.
- If you’re reattaching a minor component, use a toothpick or a precision applicator to control the adhesive applied.
Pressing Surfaces Together:
- Carefully press the surfaces together, ensuring proper alignment. Hold them in place until the adhesive starts to set. This may take a few minutes, depending on the type of adhesive used.
Clamping (if necessary):
- For some repairs, it may be helpful to use clamps to hold the components together while the adhesive cures. Make sure the clamps do not damage other parts of the headset.
Drying Time:
- Follow the recommended drying or curing time for the adhesive. This information is usually provided on the adhesive’s packaging.
Reassembly:
- Once the adhesive has fully cured, reassemble the TWS headset following the reverse order of disassembly.
Remember to exercise caution during the repair process and be patient to allow the adhesive to set correctly. If in doubt, refer to the manufacturer’s guidelines or seek professional help.
Are There Specific Adhesives for TWS Headset Battery Issues?
Repairing or replacing the battery in a TWS (True Wireless Stereo) headset can be a delicate process, and using a suitable adhesive is crucial to ensure proper functionality and safety. Here are some considerations:
Battery Type:
- TWS headsets typically use lithium-ion or lithium-polymer batteries. These batteries can be sensitive to heat and pressure, so using adhesives compatible with these battery types is essential.
Adhesive Type:
- Use a double-sided adhesive tape that is specifically designed for electronic devices. It should be thin yet strong enough to hold the battery securely. Make sure the adhesive is not conductive to avoid any short circuits.
Thermal Properties:
- TWS headsets can generate heat during operation. Choose an adhesive that has good thermal conductivity to help dissipate heat away from the battery. This can contribute to the overall longevity and safety of the device.
Removability:
- Consider using adhesives that allow for easy removal of the battery in case it needs to be replaced again in the future. This can make future repairs more manageable.
Water Resistance:
- If the TWS headset is designed to be water-resistant or waterproof, choose an adhesive that is also water-resistant to maintain the device’s original level of protection.
Manufacturer Recommendations:
- Check the manufacturer’s guidelines or recommendations for repairing the specific TWS headset model. They may provide information on the type of adhesive to use.
Professional Repair:
- If you are not confident in your ability to repair the TWS headset yourself, or if it is still under warranty, consider taking it to a professional repair service or contacting the manufacturer for assistance.
Always exercise caution when working with electronic devices, especially with batteries. Suppose you are uncertain about the repair process or the type of adhesive to use. In that case, it’s advisable to seek professional assistance to avoid causing further damage to the device or compromising safety.
Can Adhesives Help in Noise Isolation for TWS Earbuds?
While adhesives themselves may not directly contribute to noise isolation in TWS (True Wireless Stereo) earbuds, they can play a role in their overall design and assembly, which may indirectly impact noise isolation.
Here are a few ways in which adhesives can be involved:
- Sealing Components:Adhesives can be used to fill the various components of the earbuds, such as the outer shell, speakers, and electronic components. A well-sealed design can help prevent sound leakage and improve noise isolation.
- Assembly of Components:Adhesives are commonly used in the assembly process of electronic devices, including TWS earbuds. Properly bonding components together contributes to the structural integrity of the earbuds, preventing gaps or loose connections that compromise noise isolation.
- Vibration Damping:Adhesives with vibration-damping properties can help reduce the transmission of vibrations through the earbuds. Vibrations can sometimes contribute to unwanted noise, and by dampening them, adhesives can indirectly aid in noise control.
- Isolation of Microphones:TWS earbuds often have built-in microphones for features like phone calls or voice commands. Adhesives can be used to isolate these microphones from other components, reducing the transmission of unwanted ambient noise.
It’s important to note that while adhesives can contribute to the physical aspects of noise isolation, the primary factors influencing noise isolation in earbuds are the ear tips or cushions’ design and the overall fit in the user’s ears. Ear tips that create a good seal in the ear canal are crucial for blocking external noise.
Additionally, some TWS earbuds have active noise cancellation (ANC) features that use electronic components to cancel out external sounds actively. In such cases, the design of the ANC system and the quality of the earbuds’ firmware play a significant role in noise isolation.
While adhesives can be part of the overall construction process and contribute to the physical aspects of noise isolation, the primary factors for adequate noise isolation in TWS earbuds are the design of the earbuds, the quality of ear tips or cushions, and, in some cases, the presence of active noise cancellation technology.
Are TWS Headset Adhesives Environmentally Friendly?
The environmental friendliness of adhesives used in TWS (True Wireless Stereo) headsets depends on the specific type of adhesive and its composition. Adhesives can vary widely in terms of their environmental impact. Here are some considerations:
- Traditional Adhesives:Some adhesives may contain volatile organic compounds (VOCs) or harmful chemicals. These types of adhesives can have adverse environmental effects during manufacturing, use, and disposal. It’s essential to consider the composition of the adhesive to assess its environmental impact.
- Eco-Friendly Adhesives:Manufacturers are increasingly aware of environmental concerns and are developing more environmentally friendly adhesives. These adhesives may be water-based, solvent-free, or made from renewable resources. Choosing adhesives with these characteristics can contribute to a more eco-friendly product.
- Recyclability:The recyclability of TWS headsets can also be influenced by the adhesives used. Some adhesives may make it challenging to disassemble and recycle components, while others may allow for easier separation of materials during the recycling process.
- Adhesive Disposal:The end-of-life disposal of TWS headsets can be a concern. Adhesives that break down naturally over time or are biodegradable can be more environmentally friendly in the long run. However, the overall environmental impact will depend on the headset’s other components and materials.
To determine the environmental friendliness of adhesives in TWS headsets, you may want to consider the following:
- Check Product Specifications:Look for information provided by manufacturers about the materials used in their TWS headsets, including adhesives. Some companies prioritize eco-friendly practices and materials and may highlight this in their product information.
- Certifications:Some adhesives may carry certifications or labels indicating that they meet specific environmental standards. Look for certifications such as RoHS (Restriction of Hazardous Substances) or other environmentally conscious labels.
- Company Sustainability Practices:Research the sustainability practices of the TWS headset manufacturer. Companies committed to sustainability may have initiatives to reduce their environmental impact, including the choice of materials, including adhesives.
The environmental friendliness of adhesives in TWS headsets depends on the specific adhesive type and the manufacturer’s practices. Choosing products with eco-friendly adhesives and considering the overall sustainability of the headset can contribute to a more environmentally responsible choice.
What Precautions Should I Take When Handling TWS Adhesives?
Handling TWS (Two-Part Epoxy) adhesives requires careful attention to ensure safety and adequate bonding. Here are some precautions you should take when working with TWS adhesives:
- Read the Product Data Sheet (PDS):Familiarize yourself with the specific TWS adhesive you are using by reading the product data-sheet provided by the manufacturer. This document contains crucial information about the adhesive’s properties, recommended applications, and safety guidelines.
- Wear Personal Protective Equipment (PPE):Always wear appropriate personal protective equipment, including gloves and safety glasses or goggles, to protect your skin and eyes from contact with the adhesive.
- Work in a Well-Ventilated Area:Use TWS adhesives in a well-ventilated area or under an adequate fume hood to prevent inhalation of vapors. Good ventilation helps disperse any potentially harmful fumes and reduces the risk of exposure.
- Avoid Skin Contact:Minimize skin contact with TWS adhesives. If contact occurs, wash the affected area immediately with soap and water. Some people may develop sensitivities or allergic reactions, so taking precautions is essential.
- Use Disposable Mixing Tools:When preparing TWS adhesives, use disposable mixing tools such as plastic or wooden sticks. Avoid using metal tools, as they can induce premature curing.
- Accurate Mixing Ratios:Follow the manufacturer’s instructions for the correct mixing ratio of the two components. Use absolute measuring tools to balance the resin and hardener properly.
- Mix Thoroughly:Mix the adhesive’s two components thoroughly to achieve a uniform consistency. Inadequate mixing can result in incomplete curing and compromised bond strength.
- Apply promptly:TWS adhesives typically have a limited working time (pot life) once mixed. Apply the adhesive promptly to the surfaces to be bonded within this timeframe to ensure optimal adhesion.
- Secure Proper Bonding Conditions:Ensure that the surfaces to be bonded are clean, dry, and free from contaminants. Follow the recommended substrate preparation procedures outlined in the product data-sheet.
- Use Adequate Restraints:Once the adhesive is applied, use appropriate restraints or clamps to hold the bonded surfaces together until the adhesive cures. Follow the recommended curing time before subjecting the bond to stress or load.
- Dispose of Waste Properly:Dispose of unused or expired TWS adhesive according to local regulations. Some epoxy products may have specific disposal instructions due to their chemical composition.
Following these precautions and the manufacturer’s guidelines, you can work safely with TWS adhesives and achieve reliable bonding results.
How Long Does it Take for TWS Adhesives to Cure?
The curing time for TWS (Two-Part Wood System) adhesives can vary depending on the formulation. TWS adhesives typically contain two components—a resin and a hardener—that must be mixed before application. Once mixed, a chemical reaction begins, leading to the curing or hardening of the adhesive.
Curing times can range from a few minutes to several hours, and in some cases, it may take even longer for the adhesive to reach its maximum strength. It’s essential to refer to the product’s technical data sheet or the manufacturer’s instructions for accurate information on curing times.
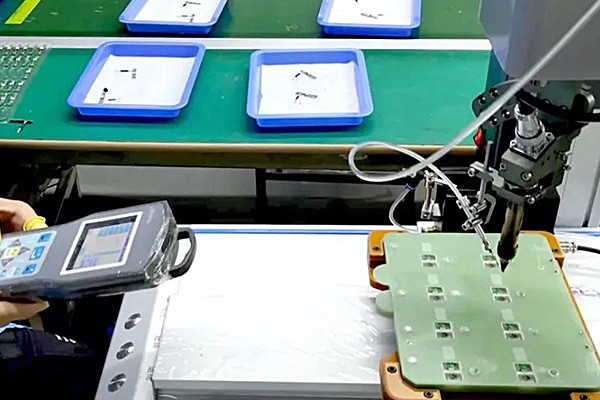
Factors that can influence the curing time of TWS adhesives include:
- Temperature:Generally, higher temperatures accelerate the curing process, while lower temperatures may slow it down. Some adhesives may have a minimum recommended application temperature.
- Humidity:Humidity levels can affect the curing of certain adhesives. Some products may cure more slowly in low-humidity environments.
- Thickness of the Bond Line:The thickness of the adhesive bond line can impact curing times. Thicker bond lines may take longer to cure completely.
- Substrate Material:The type of materials being bonded can influence the curing process. Different adhesives are designed for specific materials, and the compatibility of the adhesive with the substrate can affect curing times.
- Mixing Ratio:Following the recommended mixing ratio of the resin and hardener is crucial. Deviating from the specified ratio can affect the curing process and the final bond strength.
Always follow the manufacturer’s guidelines and recommendations for your specific TWS adhesive. Suppose you are working on a critical application. In that case, it’s advisable to perform tests to ensure that the adhesive has fully cured and developed the desired properties before subjecting the bonded materials to stress or load.
Are There Adhesives Suitable for TWS Headset DIY Customizations?
Yes, there are adhesives that you can use for do-it-yourself (DIY) customizations of True Wireless Stereo (TWS) headsets. The type of adhesive you choose depends on the materials you’re working with and the specific customization you’re planning. Here are some standard adhesive options:
- Cyanoacrylate (Super Glue):This fast-bonding adhesive works well on various materials like plastics and metals. It’s suitable for small, precise applications. However, be cautious as it can be brittle and may not be the best choice for flexible or moving parts.
- Epoxy Resin:Epoxy is a versatile adhesive that works on various materials. It’s known for its solid and durable bond. Epoxy comes in two parts that you mix before application. It takes longer to cure than superglue but often provides a more robust bond.
- Hot Glue:Hot glue guns are commonly used for DIY projects. They are easy to use, offer a quick bond, and can be removed more quickly than other adhesives. However, hot glue may not be the best choice for applications involving a lot of movement or joint stress.
- Double-Sided Tape:For less permanent customizations, consider double-sided tape. This is an excellent option to attach or secure something without needing a strong, permanent bond. Double-sided tapes have various strengths and can be a good choice for lightweight applications.
- Silicone Adhesive:Silicone adhesives are flexible and provide a strong bond. They are often used for sealing and bonding applications. Silicone can be a good choice if flexibility is essential for your customization.
Before applying any adhesive, cleaning and preparing the surfaces properly is essential. Ensure that the adhesive you choose is compatible with the materials you are working with, and follow the manufacturer’s instructions for application and curing times. Additionally, consider the impact of the adhesive on the overall aesthetics and functionality of your TWS headset.
Do Adhesives Affect TWS Headset Audio Quality?
In general, if adhesives are applied correctly and in moderation, they should not significantly affect the audio quality of a True Wireless Stereo (TWS) headset. However, there are a few considerations to keep in mind:
- Driver Housing and Acoustic Properties:If you are customizing the physical structure of the TWS headset, such as the driver housing or other components close to the speakers, changes in shape or material could influence the acoustic properties. In such cases, it’s essential to be mindful of the impact on the placement and function of the audio drivers.
- Blocking Ports or Microphones:Applying adhesive to block ports, microphones, or other openings on the TWS headset can affect audio quality. Make sure that any customization you perform doesn’t interfere with the original design and functionality of the headset.
- Material Compatibility:Some adhesives emit volatile organic compounds (VOCs) as they cure, and these could affect the materials or coatings used to construct the TWS headset. Ensure that the adhesive you choose is compatible with the materials of the headset and won’t cause damage over time.
- Balance and Weight Distribution:If your customization involves adding significant weight or altering the TWS headset’s balance, it could affect how the headset sits in your ears. This may indirectly impact the quality of the audio experience, especially if a poor fit leads to changes in how the audio drivers align with your ears.
To minimize the risk of affecting audio quality, follow these guidelines:
- Use adhesives sparingly and only where necessary.
- Avoid blocking any openings, ports, or microphones.
- Choose adhesives specifically designed for use with electronics and safe for the headset’s materials.
- Be mindful of the overall weight and balance of the headset.
Always test the modified headset after customization to ensure no noticeable changes in audio quality. If in doubt, consult the manufacturer’s guidelines or seek professional advice before significantly modifying your TWS headset.
Can Adhesives Enhance the Stability of TWS Earbud Components?
Yes, adhesives can play a crucial role in enhancing the stability of TWS (True Wireless Stereo) earbud components. TWS earbuds typically consist of various components, including the earbud housing, speakers, batteries, and electronic circuits. Adhesives can be used in several ways to improve the stability and overall performance of these components:
- Bonding Components:Adhesives are commonly used to bond different components, providing structural stability to the earbuds. This helps in preventing disassembly or damage during regular use.
- Vibration Damping:TWS earbuds are exposed to vibrations, mainly when used. Adhesives with vibration-damping properties can help reduce the impact of vibrations on internal components, preventing damage and enhancing the longevity of the earbuds.
- Sealing and Water Resistance:Adhesives can create a seal around the components, making the earbuds more resistant to water and moisture. This is particularly important for TWS earbuds that may be used in various environmental conditions, such as during workouts or in rainy weather.
- Wire Management:TWS earbuds often have small, intricate wiring for connectivity between the left and right earbuds. Adhesives can be used to secure and organize these wires, preventing tangling and improving the overall reliability of the earbuds.
- Heat Dissipation:Some adhesives are designed to have good thermal conductivity. Using such adhesives can help dissipate heat generated by electronic components, preventing overheating and ensuring the optimal performance of the earbuds.
- Weight Distribution:Adhesives can contribute to even weight distribution within the earbuds, making them more comfortable to wear for extended periods.
When selecting adhesives for TWS earbuds, it’s essential to consider factors such as the type of materials being bonded, the intended use of the earbuds, and any specific requirements for flexibility, temperature resistance, and water resistance. Manufacturers often conduct extensive testing to ensure that the chosen adhesives meet the durability and performance standards required for TWS earbuds.
What is the Lifespan of TWS Headset Adhesives?
The lifespan of adhesives used in True Wireless Stereo (TWS) headset construction can vary based on several factors, including the quality of the adhesive, environmental conditions, and how well the headset is maintained. Adhesives are commonly used to bond components, such as the casing, battery, circuitry, and speakers in TWS headsets.
High-quality adhesives designed for electronic devices are typically durable and can withstand normal wear and tear. However, environmental factors like temperature, humidity, and moisture exposure can affect the adhesive’s longevity. Additionally, the frequency of use and the physical stress the headset experiences during handling and usage can impact the adhesive’s lifespan.
Manufacturers often conduct tests and evaluations to ensure that the adhesives used in their products meet specific standards and can endure the expected lifespan of the device. However, it’s challenging to provide a specific timeframe for the lifespan of TWS headset adhesives, as it depends on the factors mentioned above.
Suppose you’re experiencing issues with the adhesives in your TWS headset, such as components coming apart or the device not functioning. In that case, it’s advisable to contact the manufacturer’s customer support for guidance or to explore warranty options if the device is still under warranty. Regular maintenance and avoiding exposure to extreme conditions can also help prolong the lifespan of the adhesives in electronic devices.
Are There Adhesives Specifically Designed for TWS Charging Cases?
There weren’t adhesives specifically marketed as designed exclusively for TWS (True Wireless Stereo) charging cases. However, the type of adhesive you might use for a TWS charging case would depend on the case’s materials and the manufacturer’s specific requirements.
TWS charging cases are often made from various plastics, metals, or a combination of materials. Standard adhesives used in electronic device assembly include cyanoacrylate (super glue), epoxy, or specialized electronic adhesives designed for bonding components in electronic devices.
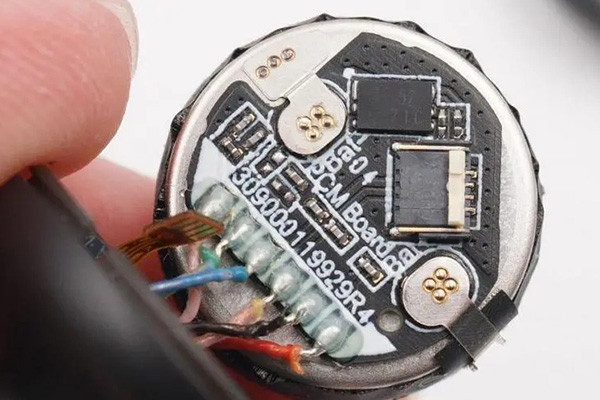
If you are dealing with a damaged or detached part of a TWS charging case and need to reattach it, you should consider the following:
- Material Compatibility:Ensure that the adhesive you choose is compatible with the materials used in the charging case. Some adhesives may not bond well with certain plastics or metals.
- Strength and Durability:Look for an adhesive with the appropriate strength for the intended use. Charging cases may experience stress, so a durable and flexible adhesive may be necessary.
- Water Resistance:TWS charging cases are often exposed to some level of moisture. If water resistance is essential, choose an adhesive that provides a good seal and is moisture-resistant.
- Quick Curing:Some adhesives offer short curing times, which can benefit assembly processes or users who want to use their TWS earbuds soon after repair.
- Temperature Resistance:Consider the temperature conditions to which the charging case may be exposed and choose an adhesive that can withstand those conditions.
Always follow the manufacturer’s recommendations for repair and use adhesives in a well-ventilated area, adhering to safety guidelines. Also, remember that technology and product specifications can change, so it’s a good idea to check for any updates or specific recommendations from the TWS charging case manufacturer or adhesive manufacturers.
For the latest information, it’s recommended to check with the manufacturer of the TWS charging case or consult with adhesive manufacturers for any new products designed for electronic device assembly.
Can TWS Adhesives Withstand Temperature Variations?
The ability of TWS (Two-Part Epoxy) adhesives to withstand temperature variations depends on the specific formulation of the adhesive and the intended application. Generally, TWS adhesives are known for their versatility and can exhibit good temperature resistance.
Two-part epoxy adhesives typically consist of a resin and a hardener that react chemically to form a strong bond. The temperature resistance of the cured epoxy depends on factors such as the chemical composition of the epoxy, the curing process, and any additional additives in the formulation.
In many cases, TWS adhesives can withstand a wide range of temperatures, including both high and low extremes. However, it’s essential to check the manufacturer’s specifications and recommendations for your specific epoxy product. Manufacturers usually provide information on the adhesive’s temperature resistance, including its service temperature range and limitations.
Keep in mind that prolonged exposure to extreme temperatures, especially temperatures beyond the specified range, may affect the performance of the adhesive. Additionally, rapid temperature changes or cycling between high and low temperatures can impact the durability of epoxy bonds.
Suppose you have a specific application or temperature range in mind. In that case, it’s advisable to consult with the adhesive manufacturer or supplier for guidance on selecting the most suitable TWS adhesive for your needs. They can provide information on the adhesive’s thermal properties and offer recommendations based on your specific requirements.
Do TWS Adhesives Leave Residue During Removal?
The residue left behind during the removal of TWS (Two-Part Epoxy) adhesives can vary depending on the specific formulation of the adhesive, the substrate it was applied to, and the removal method used. Properly cured and fully hardened epoxy adhesives are designed to form strong and durable bonds, and their removal can only be challenging with proper techniques.
If you need to remove a TWS epoxy adhesive and want to minimize residue, here are some considerations:
Softening the adhesive:
- Some TWS adhesives can be softened by heating. Applying heat to the adhesive can make it more pliable, allowing for easier removal. However, excessive heat may damage specific substrates or materials.
Chemical solvents:
- There are chemical solvents designed to break down or soften epoxy adhesives. These solvents are formulated to dissolve or weaken the bond. It’s crucial to use safe solvents for the substrate material and to follow proper safety precautions.
Mechanical methods:
- Mechanical methods, such as scraping or sanding, may be used to remove epoxy adhesive. However, this could damage the underlying surface and may not be suitable for all applications.
Adhesive removers:
- Some commercial adhesive removers are designed explicitly for removing various adhesives, including epoxies. These products are formulated to break down the adhesive without causing damage to the substrate.
Regardless of the method used, it’s essential to follow the manufacturer’s recommendations for removal and to test any removal method on a small, inconspicuous area first to ensure it doesn’t damage the substrate.
Remember that residue-free removal may not always be achievable, especially if the epoxy has fully cured and formed a strong bond. In some cases, a certain degree of residue or adhesive remnants may remain, and additional cleaning or surface preparation may be necessary if you plan to apply new materials or coatings to the substrate.
Are There Adhesives Compatible with TWS Headset Brands X, Y, and Z?
To find the most accurate and up-to-date information, I recommend checking the product specifications and guidelines provided by the TWS headset manufacturers. You can visit the official websites of brands X, Y, and Z or contact their customer support for information on recommended adhesives or compatibility considerations.
Suppose you are looking for adhesives to repair or modify TWS headsets. In that case, it’s essential to choose adhesives that are safe for the materials used in the headset and provide a secure bond without causing damage. Consider looking for adhesives specifically designed for electronics or minor device repairs.
Always follow the manufacturer’s guidelines and recommendations to ensure that any modifications or repairs you make do not void the warranty or cause other issues with the TWS headset.
How Can I Choose the Right TWS Adhesive for My Specific Needs?
Choosing the suitable adhesive for your TWS (True Wireless Stereo) headset involves considering several factors to ensure proper bonding without causing damage. Here are some guidelines to help you choose the suitable TWS adhesive for your specific needs:
Check Manufacturer Guidelines:
- Review the TWS headset manufacturer’s guidelines or user manual for any specific recommendations regarding repairs or adhesives. Using adhesives not recommended by the manufacturer may void the warranty.
Material Compatibility:
- Identify the materials used in your TWS headset. Common materials include plastic, metal, and rubber. Choose an adhesive compatible with these materials to ensure a solid and lasting bond.
Type of Bond Needed:
- Consider the type of bond required for your application. Some adhesives are designed for flexible bonds, while others offer rigid bonds. Choose an adhesive that suits the structural requirements of your TWS headset.
Application Method:
- Determine the application method that best suits your needs. Some adhesives come in liquid form, while others are available as gels or tapes. The application method should align with the specific repair or modification you are performing.
Curing Time:
- Take into account the curing time of the adhesive. Depending on the type of adhesive, curing times can vary from a few minutes to several hours. Ensure you have enough time for the adhesive to fully cure before using the TWS headset.
Temperature and Environmental Considerations:
- Consider the environmental conditions the TWS headset will be exposed to. Some adhesives may be more suitable for extreme temperatures or moisture resistance. Choose an adhesive that can withstand your TWS headset’s environmental conditions.
Removability:
- If you need to disassemble or repair the TWS headset in the future, consider using an adhesive that allows for easy removal without causing damage.
Reviews and Recommendations:
- Look for reviews and recommendations from other users who have undertaken similar repairs or modifications. This can provide insights into the effectiveness and reliability of specific adhesives.
Brand-Specific Adhesives:
- Some electronics manufacturers offer branded adhesives explicitly designed for their products. Check if the TWS headset manufacturer provides or recommends a specific adhesive.
Always follow the safety instructions the adhesive manufacturer provides, and make sure to use adhesives in a well-ventilated area. If you need clarification on the suitable adhesive for your specific needs, consult the manufacturer or seek advice from professionals with experience in electronic repairs.
Conclusion:
In conclusion, understanding TWS headset adhesives is crucial for maintaining and optimizing the performance of these wireless audio devices. From repairs to customizations, the suitable adhesive can significantly affect the durability, functionality, and overall user experience of TWS headsets. We hope this guide has provided valuable insights into the world of TWS headset adhesives, helping you make informed decisions for the care and enhancement of your audio devices. If you have further questions or need assistance, please explore our other resources or contact our experts.
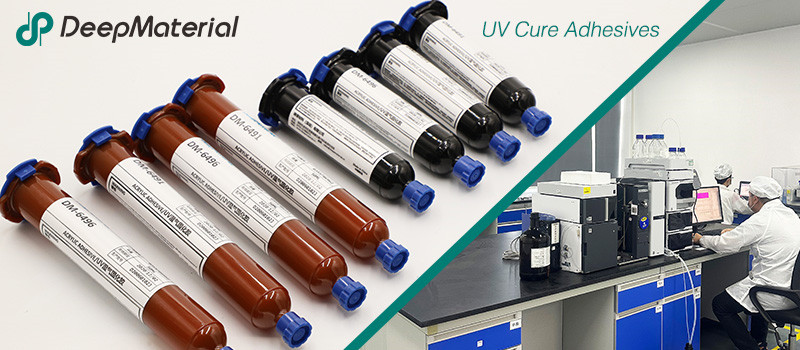
DeepMaterial
Based on the core technology of adhesives, DeepMaterial has developed adhesives for chip packaging and testing, circuit board level adhesives, and adhesives for electronic products. Based on adhesives, it has developed protective films, semiconductor fillers, and packaging materials for semiconductor wafer processing and chip packaging and testing. More…
UV Curing Adhesives
UV light cure have a number of benefits making them a popular choice among many product assembly and manufacturing applications. Many UV light cure adhesives can provide a nearly instantaneous bond to difficult substrates like glass and plastic. UV cure adhesives often require an accelerator or UV light for a bond to form.
Adhesive Blogs & News
The latest adhesive industry science and technology, Deepmaterial news, and market trends and forecasts.
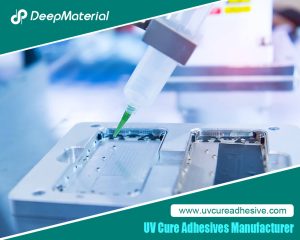
The Quantitative Influence of Crosslinking Density on the Flexibility and Hardness of Adhesives and the Formulation Optimization Strategy
The Quantitative Influence of Crosslinking Density on the Flexibility and Hardness of Adhesives and the Formulation Optimization Strategy This article systematically expounds the quantitative relationship between the crosslinking density and the flexibility and hardness of adhesives. Combining the theories of polymer physics with experimental analysis methods, it reveals the mechanism of the action of the
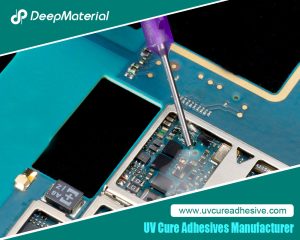
Technical Strategies for Balancing the Rapid Curing Property and Long Operating Time of UV Adhesives
Technical Strategies for Balancing the Rapid Curing Property and Long Operating Time of UV Adhesives UV adhesives have been widely used in many fields such as electronics, optics, and medicine due to their advantages of rapid curing, high bonding strength, and environmental protection. However, their rapid curing property also brings challenges in some application scenarios.
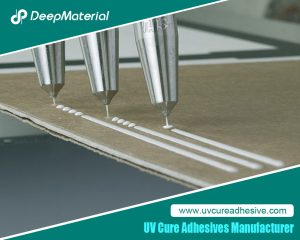
Biocompatibility of LED UV Glue Adhesive and Its Application Potential in Medical and Food Packaging Fields
Biocompatibility of LED UV Glue Adhesive and Its Application Potential in Medical and Food Packaging Fields LED UV glue adhesive has been widely applied in numerous fields due to its advantages such as rapid curing and easy operation. However, in fields with stringent safety requirements like medical and food packaging, its biocompatibility after curing
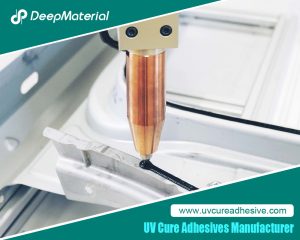
Exploring the Environmental Performance of UV Glue and Strategies for Optimizing Odor and VOC Content
Exploring the Environmental Performance of UV Glue and Strategies for Optimizing Odor and VOC Content UV glue, as an adhesive that achieves rapid curing through ultraviolet (UV) light irradiation, has been widely applied in numerous fields such as electronics, optics, healthcare, and automobiles, thanks to its advantages of fast curing speed, high bonding strength, and
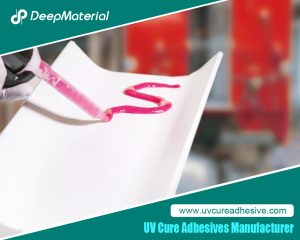
Compatibility Analysis and Countermeasures of LED UV Glue with Automated Production Equipment
Compatibility Analysis and Countermeasures of LED UV Glue with Automated Production Equipment LED UV glue has been widely used in modern manufacturing due to its advantages such as fast curing speed, high bonding strength, and environmental friendliness. However, in the automated production process, if there are problems with the adaptability between the glue and equipment
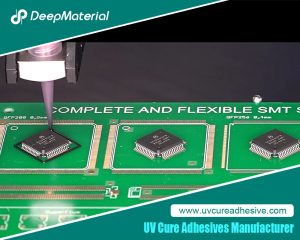
Influence of Viscosity and Thixotropy of Glue on the Quality of Glue Dots in the Dispensing Process and Solutions
Influence of Viscosity and Thixotropy of Glue on the Quality of Glue Dots in the Dispensing Process and Solutions The dispensing process is an important part of the application of LED UV glue adhesive, and the quality of this process directly affects the final performance of the product. The physical properties of the glue,