- Home
- >
- Material Bonding
- >
- UV Cure Adhesive For Glass
UV Cure Adhesive For Glass
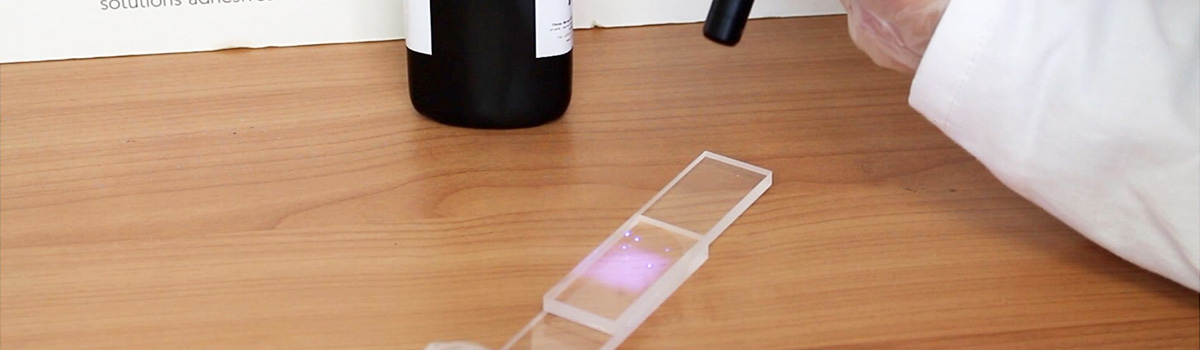
UV cure adhesives for glass have emerged as a game-changer in adhesive solutions, offering a fast and efficient bonding method. This category page delves into the intricacies of UV cure adhesive, exploring its applications and advantages and answering key questions surrounding its use.
Table of Contents
ToggleHow does UV-cure adhesive work on glass surfaces?
UV-curable adhesives cure or harden when exposed to ultraviolet (UV) light. These adhesives are widely used in various industries for bonding applications due to their fast curing, high bond strength, and ability to bond a wide range of substrates, including glass. Here’s a general overview of how UV-cure adhesives work on glass surfaces:
Composition:
- UV-cure adhesives typically consist of monomers, oligomers, photoinitiators, and other additives.
- Monomers and oligomers are the primary components that form the adhesive matrix.
- Photoinitiators are chemicals that absorb UV light and initiate the polymerization reaction, causing the adhesive to cure.
Application:
- The liquid adhesive is applied to the desired bond line thickness of the glass surface.
Exposure to UV Light:
- Once the adhesive is applied, it is exposed to UV light with a specific wavelength, typically 320 to 400 nanometers.
- The photoinitiators in the adhesive absorb the UV light and become energized.
Initiation of Polymerization:
- The energized photoinitiators start a photochemical reaction, breaking into free radicals.
- These free radicals initiate the polymerization of the monomers and oligomers in the adhesive.
Polymerization and Curing:
- The polymerization process involves the monomers and oligomers linking to form a three-dimensional network, creating a solid and durable bond.
- This curing process occurs rapidly, usually within seconds to minutes, depending on the adhesive formulation and the intensity of the UV light.
Bond Formation:
- As the polymerization progresses, the adhesive hardens, creating a solid bond between the glass surfaces.
Post-Curing (Optional):
- Some UV-cure adhesives may undergo a post-curing process to ensure complete curing and optimal bond strength.
Final Bond:
- Once the UV-cure adhesive has fully cured, the glass components are bonded together securely.
UV-cure adhesives are advantageous because they offer precise control over the curing process, allowing for fast and efficient bonding. Additionally, they can be used in applications where heat-sensitive substrates, like certain plastics, may be damaged by traditional heat-curing adhesives.
What makes UV cure adhesive a preferred choice for glass bonding?
UV-curable adhesives are often a preferred choice for glass bonding due to several advantages:
- Rapid Cure Time:UV-curable adhesives cure quickly when exposed to ultraviolet (UV) light. This fast curing process allows for high production throughput, making it ideal for applications where efficiency and speed are crucial.
- Precise Control of Cure:The curing process of UV adhesives is initiated and controlled by exposure to UV light. This enables precise control over the curing time, allowing for accurate alignment of components before bonding and ensuring a consistent and reliable bond.
- Low Heat Generation:UV curing is a low-temperature process compared to other bonding methods, such as heat curing. This is particularly important for bonding glass, as excessive heat can cause thermal stress and potentially damage the glass.
- High Strength and Durability:UV-curable adhesives can provide high bond strength and durability, contributing to the overall performance of the bonded glass components. This is essential for applications where the related parts are subject to mechanical stress or environmental factors.
- Clean and Environmentally Friendly:UV-curable adhesives typically contain fewer volatile organic compounds (VOCs) than solvent-based adhesives. The clean and environmentally friendly nature of UV curing makes it a preferred choice for applications where emissions and environmental impact are concerns.
- Versatility:UV-curable adhesives can bond with various substrates, including glass, plastics, metals, and ceramics. This versatility makes them suitable for multiple electronics, medical devices, optics, and automotive applications.
- Minimal Shrinkage:UV-curable adhesives often exhibit minimal shrinkage during the curing process. This characteristic is essential for maintaining dimensional stability and ensuring a precise fit between bonded components.
- Optical Clarity:UV-curable adhesives can offer excellent optical clarity, making them suitable for applications where transparency is essential, such as in optical devices or displays.
While UV-curable adhesives offer many advantages, it’s essential to consider the application’s specific requirements and the materials being bonded. Factors such as the thickness of the adhesive layer, the type of glass, and environmental conditions can influence the choice of adhesive and the UV curing process.
Are UV cure adhesives suitable for both transparent and colored glass?
UV cure adhesives can be suitable for bonding both transparent and colored glass, but it depends on the adhesive’s specific properties and the application’s requirements. UV cure adhesives are versatile and widely used in various industries due to their rapid curing process and strong bond formation when exposed to ultraviolet (UV) light.
Here are some factors to consider:
Transparency:
- UV cure adhesives are generally transparent, making them suitable for bonding fine materials like clear glass. This is important for applications where aesthetics or visibility are critical.
Colored Glass:
- UV cure adhesives can also be used with colored glass, but the adhesive’s transparency may affect the overall appearance. Suppose the color of the adhesive is a concern. In that case, it’s essential to choose a UV adhesive specifically designed to be colorless or have minimal impact on the appearance of the colored glass.
Adhesive Compatibility:
- Some UV-cure adhesives may have specific formulations that make them more suitable for certain materials. It’s essential to choose an adhesive compatible with the glass substrate and any coatings or colors on the glass surface.
Curing Time:
- UV cure adhesives typically have fast curing times, which can be an advantage in applications requiring quick bonding. However, the curing time can vary among different adhesives, so selecting one that meets the application’s specific needs is essential.
UV Light Exposure:
- Ensure that the adhesive receives sufficient UV light exposure during the curing process. If the glass has areas shielded from UV light, the adhesive may not cure properly in those areas.
Before selecting a UV cure adhesive for bonding glass, it’s advisable to consult the manufacturer’s guidelines and test the adhesive in a small, inconspicuous area to ensure compatibility and satisfactory performance. Additionally, consider factors such as temperature resistance, flexibility, and the application’s specific requirements to choose the most appropriate adhesive for your needs.
Can UV-cure adhesives withstand extreme temperatures?
The ability of UV-cure adhesives to withstand extreme temperatures depends on the specific formulation of the adhesive and the intended application. UV-cure adhesives are generally known for their excellent bonding properties, rapid curing times, and versatility. However, their performance under extreme temperatures can vary.
Some UV-cure adhesives are designed to withstand a wide range of temperatures, including both high and low extremes. Manufacturers often provide temperature resistance specifications for their products, indicating the upper and lower temperature limits at which the adhesive can maintain its structural integrity and bonding strength.
It’s essential to check the product datasheet or consult the adhesive manufacturer to ensure that a particular UV-cure adhesive meets the temperature requirements for your specific application. Factors such as the substrate materials being bonded, the expected temperature range in the application environment, and the intended use (e.g., aerospace, automotive, electronics) can all influence the choice of adhesive.
In some cases, UV-cure adhesives may have limitations at extremely high temperatures, and alternative adhesive technologies may be more suitable for applications with extreme heat exposure. For example, specific epoxy or silicone-based adhesives are known for their high-temperature resistance.
Always follow the manufacturer’s recommendations and guidelines for proper application and curing processes to ensure optimal performance of the UV-cure adhesive in challenging temperature conditions.
What are the critical applications of UV cure adhesive in the glass industry?
UV-cure adhesives play a crucial role in various applications within the glass industry due to their unique properties and advantages. Some critical applications include:
Bonding and Sealing:
- Glass Bonding:UV-cure adhesives are used for bonding glass to glass or glass to other materials. This is common in manufacturing glass assemblies, such as display screens, optical devices, and glass furniture.
- Structural Bonding:UV adhesives provide high-strength bonds suitable for structural applications, contributing to the stability and durability of glass structures.
Optical Devices:
- Lens Assembly:UV-cure adhesives are widely employed to assemble optical components, such as lenses and prisms. The fast curing time and optical clarity of these adhesives are essential for maintaining the visual quality of the devices.
Touchscreen Manufacturing:
- Display and Touch Panel Assembly:UV adhesives bond layers to produce touchscreen displays. The clarity of the adhesive ensures that the display remains visually apparent, and the rapid curing process aids in efficient manufacturing.
Automotive Glass Applications:
- Windshield Bonding:UV-cure adhesives are utilized in bonding windshields to the vehicle frame. The quick curing time is particularly advantageous in automotive manufacturing processes.
Furniture and Decor:
- Glass Furniture Assembly:UV adhesives are employed in assembling glass furniture, providing structural integrity and aesthetic appeal. This can include tables, shelves, and other decorative glass elements.
Electronic Devices:
- Electronic Display Assembly:UV-cure adhesives assemble electronic displays, ensuring a secure bond between glass layers in devices like smartphones, tablets, and monitors.
Medical Devices:
- Medical Instrument Assembly:UV adhesives find applications in assembling medical devices, especially those involving glass components. Their ability to bond quickly and securely is valuable in medical equipment manufacturing.
Aerospace Industry:
- Aircraft Windows:UV adhesives are used in the aerospace industry for bonding and sealing aircraft windows. Their lightweight nature and high strength make them suitable for this critical application.
Energy Sector:
- Solar Panel Manufacturing:UV-cure adhesives are used to assemble solar panels, helping bond glass components together. The transparency and efficiency of these adhesives are essential for maintaining the performance of solar panels.
Is UV-cure adhesive environmentally friendly?
UV-cure adhesives can be considered more environmentally friendly than traditional adhesives due to specific characteristics, but their overall environmental impact depends on various factors.
Advantages of UV-cure adhesives that contribute to their environmental friendliness include:
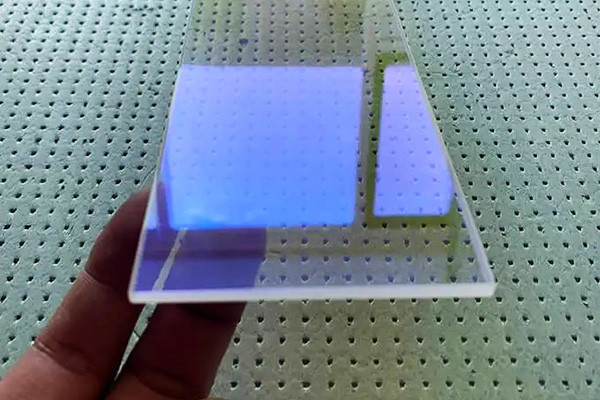
- Low VOC Emissions:UV-cure adhesives often have low or zero volatile organic compound (VOC) emissions compared to solvent-based adhesives. This is beneficial for air quality and reduces the release of harmful chemicals into the atmosphere.
- Energy Efficiency:The curing process of UV adhesives is relatively quick and typically requires less energy than other curing methods. This can result in lower energy consumption and reduced greenhouse gas emissions.
- Reduced Hazardous Materials:UV-cure adhesives usually do not contain harmful solvents or other hazardous materials, making them safer for workers and the environment.
However, it’s essential to consider some potential drawbacks:
- Raw Material Extraction:The production of raw materials for UV-cure adhesives may involve extracting resources, which can have environmental impacts. Additionally, the manufacturing process itself may require energy and produce some waste.
- End-of-Life Considerations:The ecological impact also depends on what happens at the end of the product’s life cycle. If UV-cure adhesive products are disposed of improperly, they may contribute to environmental pollution. However, the adhesives themselves are often inert once cured.
- UV Radiation Concerns:The UV curing process involves using ultraviolet (UV) radiation, which can pose safety and environmental concerns. Adequate measures should be taken to ensure the curing process is controlled and does not have adverse effects.
UV-cure adhesives can be more environmentally friendly than some alternatives. Still, their impact depends on raw material extraction, energy consumption, and end-of-life considerations. It’s essential to consider the specific formulation and application of the adhesive, as well as adherence to proper safety and disposal practices.
How does the curing time of UV adhesive compare to traditional adhesives?
UV (Ultraviolet) curing time and traditional adhesives can vary significantly based on the specific formulation and intended application. Here are some general comparisons between UV adhesives and conventional adhesives:
UV Adhesives:
- Speed of Curing:UV adhesives typically cure quickly when exposed to ultraviolet light. The UV light initiates the curing process, and it can take only a few seconds to a few minutes to achieve a complete cure, depending on factors such as the adhesive type, thickness, and intensity of the UV light.
- Controlled Curing:UV adhesives offer better control over the curing process. The curing only occurs when exposed to UV light, allowing for precise application and positioning before final curing.
- Clean and Efficient:UV adhesives are often considered cleaner than traditional adhesives because they do not require solvents or water for curing. The curing process is dry, and there are minimal by-products.
Traditional Adhesives:
- Varied Curing Times:Traditional adhesives encompass various formulations, including solvent-based, water-based, and reactive adhesives. Curing times can vary significantly, ranging from minutes to hours or even days, depending on the type of adhesive and environmental conditions.
- Chemical Reaction:Many traditional adhesives rely on chemical reactions for curing, and this process can be influenced by factors such as temperature, humidity, and the materials being bonded. Some traditional adhesives may require pressure or clamping during the curing process.
- Versatility:Traditional adhesives may be preferred when assembly or adjustment before the adhesive cures require a longer open time. They can be more versatile in working with a broader range of materials and substrates.
UV adhesives generally offer a faster curing time compared to many traditional adhesives. However, the choice between UV and conventional adhesives depends on the application’s specific requirements, the bonded materials, and the desired characteristics of the adhesive joint.
Are there different types of UV cure adhesives for specific glass applications?
UV-cure adhesives are used in bonding and sealing applications where a fast, clean, and efficient curing process is desired. The selection of a specific UV-cure adhesive depends on the requirements of the glass application. Here are some common types:
- Visible Light Cure Adhesives:These adhesives cure under visible light, which is more convenient than UV light. They are often used for bonding glass in applications where UV light may not penetrate effectively.
- Low Outgassing UV Adhesives:Some applications, such as in the electronics and aerospace industries, require adhesives that emit deficient levels of volatile substances. Low-out-gassing UV adhesives are designed to meet these specific requirements.
- Flexible UV Adhesives:Flexible UV adhesives are used for applications where the bonded materials may experience movement or flexing. They maintain their bond strength even under dynamic conditions.
- High-Temperature UV Adhesives:High-temperature UV adhesives ensure stability and performance in specific applications where elevated temperatures are expected, such as in the automotive or industrial sectors.
- Optically Clear UV Adhesives:When bonding glass that requires optical clarity, such as in the assembly of displays or optical devices, optically clear UV adhesives are used to minimize interference with light transmission.
- Structural UV Adhesives:Structural UV adhesives are employed for applications requiring high bond strength and durability. These adhesives provide a solid and long-lasting bond, making them suitable for load-bearing applications.
- Medical Grade UV Adhesives:In the medical industry, UV adhesives may be used for bonding glass components in medical devices. Medical-grade adhesives adhere to stringent biocompatibility and sterilization requirements.
- UV-Curable Gaskets and Sealants:UV-curable gaskets and sealants seal glass components to prevent moisture, dust, or other environmental factors from entering.
When selecting a UV-cure adhesive for a specific glass application, it’s essential to consider factors such as the type of glass, environmental conditions, cure time, bond strength, and any specific performance requirements. Additionally, compatibility with the curing equipment and process parameters should be considered to ensure optimal results.
Can UV-cure adhesive be used for bonding glass to other materials?
UV-cure adhesives are often chosen for their fast curing times and ability to create strong bonds without needing heat or solvents. These adhesives typically consist of a liquid monomer and a photoinitiator. When exposed to ultraviolet (UV) light, the photoinitiator initiates a chemical reaction that transforms the liquid into a solid, creating the bond.
When bonding glass to other materials, it’s essential to consider the compatibility of the adhesive with the specific types of materials involved. UV-cure adhesives are versatile and can be formulated to work with various substrates, including glass, metals, plastics, and ceramics. However, the success of the bond may depend on factors such as the surface preparation, the adhesive’s formulation, and the application’s specific requirements.
Here are some general tips for using UV-cure adhesives for bonding glass to other materials:
- Surface Preparation:Ensure that the surfaces to be bonded are clean and free of contaminants. Proper surface preparation, such as cleaning and sometimes roughening the surfaces, can enhance the adhesion.
- Adhesive Selection:Choose a UV-cure adhesive compatible with the glass and the other material. Some adhesives are specifically formulated for bonding glass, while others are designed for multi-substrate applications.
- Curing Conditions:Follow the manufacturer’s recommendations for curing conditions. This typically involves exposing the adhesive to UV light of the specified wavelength and intensity for a specific time. Adequate exposure is crucial for achieving a solid bond.
- Gap Filling:Consider the gap size between the glass and the other material. Some UV-cure adhesives are designed for thin bond lines, while others may be suitable for applications with more significant gaps.
Always refer to the specific product’s technical data sheet and instructions provided by the manufacturer for detailed guidance on application, curing, and other relevant information.
What safety precautions should be taken when working with UV-cure adhesives?
Working with UV-cure adhesives requires careful attention to safety precautions to protect yourself and others. UV-cure adhesives typically contain chemicals that can be harmful if mishandled. Here are some general safety precautions to follow:
Personal Protective Equipment (PPE):
- Wear appropriate PPE, including safety glasses or goggles with UV protection to shield your eyes from UV radiation.
- Use gloves to protect your skin from contact with the adhesive.
Ventilation:
- Work in a well-ventilated area to minimize exposure to fumes and vapors.
UV Exposure:
- Avoid direct skin exposure to UV light. Prolonged exposure to UV radiation can cause skin damage.
- Do not look directly into the UV light source.
Read and Follow the Instructions:
- Read and understand the manufacturer’s instructions and safety data sheets (SDS) for the specific UV-cure adhesive you are using.
Storage:
- Store UV-cure adhesives in a cool, dry place, away from direct sunlight.
Avoid Contamination:
- Prevent contamination of the adhesive by using clean tools and surfaces.
- Keep containers closed when not in use.
Emergency Procedures:
- Familiarize yourself with emergency procedures, including the location of safety equipment such as eyewash stations and emergency showers.
Training:
- Ensure that individuals working with UV-cure adhesives are trained on the proper handling, application, and safety precautions.
Skin Contact:
- In case of skin contact, immediately wash the affected area with soap and water.
- Seek medical attention if irritation persists.
Eye Contact:
- Flush your eyes with water for at least 15 minutes in eye contact. Seek medical attention if irritation persists.
Inhalation:
- If fumes are inhaled, move to an area with fresh air. Seek medical attention if symptoms persist.
Dispose of Waste Properly:
- Dispose of used materials and waste by local regulations.
Fire Safety:
- UV-cure adhesives may be flammable. Take precautions to avoid ignition sources and have appropriate fire extinguishing equipment available.
Protective Barriers:
- Use protective barriers, such as UV-blocking curtains or shields, to prevent accidental exposure to UV light.
Always check the specific safety guidelines provided by the manufacturer of the UV-cure adhesive you are using, as different formulations may have unique safety considerations.
Are there limitations to the thickness of glass that UV-cure adhesive can bond?
The thickness of glass that UV-cure adhesives can effectively bond depends on several factors, including the type of adhesive used, the intensity and wavelength of the UV light source, and the specific requirements of the bonding application. UV-cure adhesives are commonly used for bonding glass in various industries, such as electronics, optics, and medical devices. However, there are some limitations to consider:
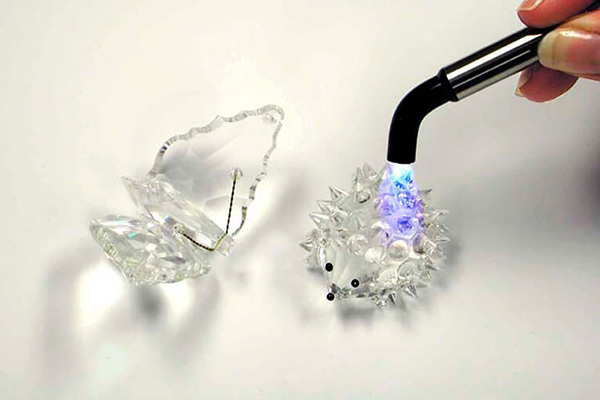
UV Penetration Depth:
- UV light has a limited penetration depth in materials. Thicker glass may pose a challenge as the UV light may not penetrate deep enough to cure the adhesive throughout the entire thickness. This can result in incomplete curing and weaker bonds.
Adhesive Composition:
- The formulation of the UV-cure adhesive plays a crucial role. Some adhesives are designed explicitly for bonding thicker substrates. It’s essential to choose an adhesive that matches the glass’s thickness and meets the application’s specific requirements.
UV Light Source:
- The intensity and wavelength of the UV light source are critical. Some UV-cure adhesives are formulated to cure with specific UV wavelengths, and the light source must match these requirements. In some cases, additional UV lamps or more powerful sources may be needed for thicker materials.
Surface Preparation:
- Proper surface preparation is crucial for successful bonding. The glass surfaces must be clean and free of contaminants that could interfere with the curing process.
Curing Time:
- Thicker glass may require longer curing times to ensure complete curing throughout the entire thickness. Manufacturers often provide guidelines on curing times based on the adhesive and glass thickness.
Temperature Sensitivity:
- Some UV-cure adhesives may be sensitive to temperature. It’s essential to consider the environmental conditions during and after the curing process, as temperature variations can affect the bonding performance.
Application Technique:
- The application technique, including the amount of adhesive applied and the uniformity of the application, can impact the bonding performance.
Before using a UV-cure adhesive for bonding thicker glass, it is advisable to consult the product datasheet provided by the adhesive manufacturer. The datasheet typically includes guidelines on the recommended thickness range, curing conditions, and other important considerations for optimal performance. Additionally, conducting tests or consulting with technical support from the adhesive manufacturer can help ensure success in specific applications.
What factors affect the bond strength of UV cure adhesive on glass?
Several factors influence the bond strength of UV-cured adhesives on glass. Here are some key factors that can affect the bond strength:
Adhesive Formulation:
- Composition:The chemical formulation of the UV-curable adhesive plays a crucial role. The type and concentration of monomers, oligomers, photoinitiators, and additives can impact the adhesive’s compatibility with glass and its bonding strength.
Substrate Preparation:
- Surface Cleanliness:The cleanliness of the glass surface is essential. Any contaminants, such as oils, dust, or residues, can hinder the adhesive’s ability to bond with the glass. Proper cleaning methods, such as using solvents, can enhance bond strength.
- Surface Activation:Some adhesives may benefit from surface activation techniques, like plasma treatment or priming, to improve adhesion to glass.
UV Exposure:
- Light Intensity and Wavelength:The UV light source’s intensity and wavelength should match the adhesive’s curing requirements. Inadequate exposure or using the wrong type of UV light may result in incomplete curing and reduced bond strength.
- Curing Time:The duration of UV exposure influences the adhesive’s curing and bond strength. A sufficient curing time can lead to complete polymerization and a stronger bond.
Glass Type:
- Surface Energy:The surface energy of the glass can affect adhesion. Higher surface energy generally leads to better wetting and adhesion. Low-energy surfaces require surface treatment for improved bonding.
Temperature and Humidity:
- Curing Environment:The ambient temperature and humidity during and after curing can affect the adhesive’s performance. Adhesive manufacturers often provide recommended curing conditions for optimal bond strength.
Thermal Expansion Coefficient:
- Compatibility:The thermal expansion coefficient of the adhesive should be compatible with that of glass to prevent stress and potential bond failure due to thermal cycling.
Joint Design:
- Gap Thickness:The adhesive layer’s thickness and the bonded area’s size can impact bond strength. Follow the manufacturer’s recommendations for the appropriate bond line thickness.
Quality of Glass Surface:
- Scratches and Defects:Surface imperfections, scratches, or defects on the glass can weaken the bond. Careful handling and inspection of the glass surface are essential.
Can UV-cure adhesive be used in outdoor applications for glass bonding?
Following the adhesive manufacturer’s guidelines and conducting thorough testing is crucial to ensure the desired bond strength for specific applications. The curing equipment and process parameters should also be carefully controlled to achieve consistent and reliable results.
UV-cure adhesives are generally not recommended for outdoor applications due to their UV (ultraviolet) light sensitivity. While UV-cure adhesives are excellent for bonding applications in controlled environments where exposure to UV light can be easily managed during the curing process, outdoor conditions present challenges.
In outdoor environments, UV radiation from sunlight is omnipresent and can affect the performance of UV-cure adhesives. Prolonged exposure to UV light can lead to premature degradation of the adhesive, resulting in reduced bond strength and overall performance. Exposure to varying weather conditions, temperature extremes, and moisture can further compromise the adhesive bond.
It is generally recommended to use adhesives specifically designed for outdoor use and capable of withstanding environmental challenges for outdoor glass bonding applications. Weather-resistant and UV-resistant adhesives, such as certain structural silicones or modified acrylics, are better suited for outdoor applications where exposure to sunlight and weather conditions is unavoidable. These adhesives are formulated to provide long-term durability and maintain their performance under outdoor exposure.
Always refer to the manufacturer’s guidelines and specifications to ensure the chosen adhesive is suitable for your outdoor application on glass or other materials. Testing and evaluating the adhesive in simulated or outdoor conditions may also be advisable to ensure the desired performance over time.
How long does the bond created by UV cure adhesive last on glass?
The longevity of a bond created by UV cure adhesive on glass can depend on several factors, including the specific type of UV cure adhesive used, the application conditions, and the environmental factors to which the bond is exposed.
UV cure adhesives typically provide strong and durable bonds, especially on glass surfaces. These adhesives cure quickly when exposed to ultraviolet (UV) light, creating a bond often resistant to heat, chemicals, and environmental conditions. However, the exact duration of the bond can vary.
It’s essential to consider the following factors that can influence the longevity of the bond:
- Adhesive Type:Different UV cure adhesives have varying formulations and properties. Some are designed for specific applications and environments, so it’s crucial to choose an adhesive that meets the requirements of your particular application.
- Surface Preparation:Proper surface preparation is essential for achieving a solid bond. Ensure the glass surface is clean, dry, and free from contaminants that could hinder adhesion.
- Curing Conditions:Adhering to the recommended conditions specified by the adhesive manufacturer is critical. This includes using the correct intensity and duration of UV light exposure during curing.
- Environmental Factors:The longevity of the bond can be influenced by environmental conditions such as temperature, humidity, and exposure to chemicals. UV cure adhesives resist many environmental factors, but extreme conditions may affect performance.
- Mechanical Stress:The bond’s durability can be influenced by mechanical stresses such as tension, compression, or shear forces. Consider the specific requirements of your application and whether the bond will be subjected to any significant mechanical stress.
In general, UV cure adhesives are known for creating robust bonds on glass and are widely used in various industries. To determine the expected lifespan of the bond in your specific application, it is recommended to consult the technical data provided by the adhesive manufacturer and consider the unique conditions of your use case.
Are there any special considerations when bonding curved or uneven glass surfaces?
Bonding curved or uneven glass surfaces can present unique challenges compared to bonding flat surfaces. Here are some considerations to keep in mind:
Surface Preparation:
- Ensure that the surfaces to be bonded are clean and free from any contaminants, such as dust, oil, or fingerprints. Use a suitable glass cleaner and ensure the surfaces are dry before bonding.
- If the glass has a coating or treatment, ensure the adhesive you choose is compatible.
Adhesive Selection:
- Choose a flexible adhesive that can accommodate the curvature or unevenness of the glass surfaces. Flexible adhesives can withstand the stresses caused by bending or uneven contours without losing their bonding strength.
- Consider using a UV-curing adhesive for quicker curing times and more precise control over the bonding process.
Adhesive Application:
- Apply the adhesive evenly across the entire bonding surface. If the glass is curved, apply the adhesive to ensure uniform coverage on both the concave and convex sides.
- Use the appropriate adhesive thickness. Too much adhesive may create excess stress during curing, while too little may result in weak bonding.
Fixture and Support:
- Implement a suitable fixture or support system to hold the glass in place during bonding. This is especially important if the glass has a significant curvature.
- Ensure the fixture does not introduce additional stress or deformation to the glass during the curing period.
Curing Conditions:
- Follow the manufacturer’s recommended curing conditions, including temperature and humidity requirements. Adhesives may have specific curing parameters that must be met for optimal bonding strength.
- Consider using heat or UV lamps to promote faster and more consistent curing.
Testing and Quality Control:
- Perform thorough testing to ensure the strength and durability of the bond, especially considering the curved or uneven nature of the surfaces.
- Conduct quality control checks to verify that the bonding process has been executed correctly.
Expansion and Contraction:
- Consider the potential expansion and contraction of the materials due to temperature variations. Some adhesives are better suited to handle these changes without compromising the bond.
Always refer to the specific guidelines the adhesive manufacturer provides, as different adhesives may have unique requirements and considerations. Additionally, if the glass is part of a larger structure or assembly, consider how the bonding process may affect the system’s overall integrity.
What role does the intensity of UV light play in the curing process?
The intensity of UV (ultraviolet) light plays a crucial role in the curing process in various applications, particularly in the field of UV curing, which is commonly used in industries such as printing, coatings, adhesives, and electronics. UV curing involves using ultraviolet light to initiate a chemical reaction that transforms liquid monomers and oligomers into solid polymers. This process is known as photopolymerization.
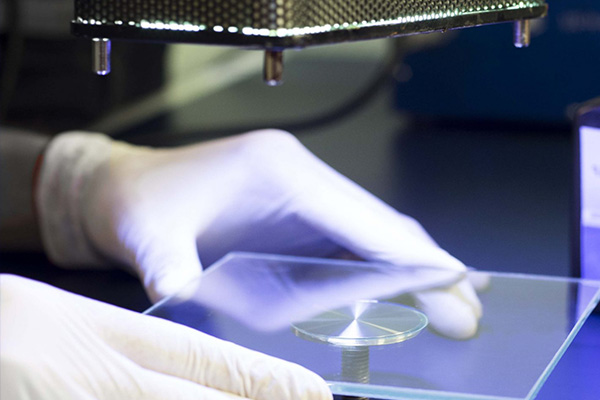
Here’s how the intensity of UV light influences the curing process:
- Initiation of Photopolymerization:UV light is the energy source that initiates the photopolymerization reaction. The higher the intensity of the UV light, the more energy is available to activate the photoinitiators, which are substances added to the formulation to absorb UV light and start the curing process.
- Reaction Rate:The intensity of UV light directly affects the curing reaction rate. Higher light intensity generally leads to faster curing times. This is crucial in industrial processes where rapid curing is desirable for increased efficiency and productivity.
- Depth of Cure:The penetration depth of UV light into the material is influenced by its intensity. Higher intensity can result in greater penetration, allowing for the curing of thicker layers of material. This is important in applications where thicker coatings or layers must be cured effectively.
- Uniformity of Cure:The uniformity of the UV light distribution across the curing area is essential for achieving consistent and even curing. Variations in intensity can lead to uneven curing, affecting the quality and performance of the cured material.
- Energy Efficiency:Optimizing the UV light intensity helps to achieve efficient curing without unnecessary energy consumption. It allows for using the minimum required energy to achieve the desired cure, contributing to cost-effectiveness in industrial processes.
It’s worth noting that different materials and formulations may have specific requirements regarding the optimal UV light intensity for curing. Manufacturers often provide guidelines and specifications for the curing process based on the characteristics of their products. UV curing systems are designed to deliver the appropriate intensity for a given application, and control systems may be employed to monitor and adjust the intensity as needed during the curing process.
Can UV-cure adhesive be used for connecting glass in medical applications?
UV-cure adhesives are commonly used for bonding glass in various applications, including medical devices. These adhesives offer several advantages: rapid curing, high bond strength, and bonding transparent materials like glass without discoloration. However, when considering the use of UV-cure adhesives in medical applications, it’s crucial to evaluate factors such as biocompatibility, sterilization methods, and the specific requirements of the medical device.
Here are some considerations:
- Biocompatibility:Ensure that the UV-cure adhesive is biocompatible and suitable for use in medical devices. Biocompatibility testing may be required to verify that the adhesive does not cause adverse reactions when in contact with the human body.
- Sterilization:Understand the sterilization methods applied to the medical device. UV-cure adhesives are often sensitive to specific sterilization techniques, such as gamma radiation or ethylene oxide. Choosing an adhesive that can withstand the selected sterilization process without compromising its performance is essential.
- Chemical Resistance:Assess the chemical resistance of the UV-cure adhesive, mainly if the medical device will come into contact with fluids or chemicals during its use. The adhesive should not degrade or release harmful substances under such conditions.
- Mechanical Properties:Evaluate the mechanical properties of the cured adhesive to ensure it meets the specific requirements of the medical application. Consider factors such as bond strength, flexibility, and resistance to temperature variations.
- Transparency:UV-cure adhesives are advantageous for bonding glass because they can create transparent bonds. Confirm that the cured adhesive maintains optical clarity and does not introduce distortions or cloudiness to the glass.
- Regulatory Compliance:Ensure that the chosen UV-cure adhesive complies with relevant regulatory standards for medical devices. Different regions may have specific requirements, so checking the applicable regulations is essential.
Before using any adhesive in a medical application, it is advisable to consult with manufacturers and conduct thorough testing to validate the chosen adhesive’s suitability for the medical device’s specific requirements. Additionally, involving regulatory experts in the process can help ensure compliance with relevant standards and regulations for medical devices.
Are there specific cleaning requirements for glass surfaces before applying UV-cure adhesive?
Proper cleaning of glass surfaces is crucial before applying UV-cure adhesive to ensure strong adhesion and optimal performance. Here are some general guidelines for cleaning glass surfaces before using UV-cure adhesives:
- Remove Dust and Debris:Before cleaning, remove any loose dust or debris from the glass surface using a soft brush or compressed air. This helps prevent scratching during the cleaning process.
- Use a Mild Detergent:Wash the glass surface with a mild detergent or cleaner. Ensure the cleaner does not leave any residue or film on the glass. Avoid using cleaners that contain oils, waxes, or silicones, as these can interfere with the adhesion of the UV-cure adhesive.
- Rinse Thoroughly:After cleaning, rinse the glass surface thoroughly with clean water to remove any detergent residue.
- Dry Completely:Allow the glass to dry completely before applying the UV-cure adhesive. Use a lint-free cloth or compressed air to speed up the drying process. Any moisture left on the surface can affect the adhesive bond.
- Isopropyl Alcohol (IPA) Wipe:For a final cleaning, use isopropyl alcohol (IPA) and a lint-free cloth to wipe the glass surface. IPA helps remove any remaining contaminants and ensures a clean, dry surface for optimal adhesion.
- Avoid Touching the Surface:Once cleaned, avoid touching the glass surface with bare hands, as oils and residues from skin contact can affect the adhesion.
- UV Light Inspection:After cleansing, inspect the glass under UV light to identify any remaining contaminants. Repeat the cleaning process if you see any residues until the surface is contaminant-free.
Always refer to the specific instructions provided by the UV-cure adhesive manufacturer, as they may have additional recommendations or particular products they recommend for cleaning. Additionally, the cleanliness of the substrate is crucial for the success of UV-curing adhesives, so take the time to ensure a thorough and proper cleaning process.
What are the common challenges faced when using UV-cure adhesive on glass?
UV-cure adhesives are commonly used for bonding glass due to their fast curing times and strong bonding capabilities. However, there are some challenges associated with using UV-cure adhesives on glass. Here are some common issues:
Substrate Transparency:
- UV adhesives cure when exposed to UV light. If the glass substrate is not transparent to the UV light, the adhesive may not cure properly in areas that are shaded or blocked from the UV light source.
Thickness of Adhesive:
- UV light has limited penetration ability. If the adhesive layer is too thick, the UV light may not penetrate through the entire thickness, resulting in incomplete curing. Ensuring that the adhesive coating is within the recommended thickness range is essential.
Surface Contamination:
- Contaminants on the glass surface, such as fingerprints, oils, or dust, can block UV light and interfere with curing. Proper cleaning and surface preparation are crucial to achieving a solid bond.
UV Light Intensity and Exposure Time:
- The intensity of the UV light source and the exposure time are critical for proper curing. Sufficient light intensity or adequate exposure time can lead to complete curing and a stronger bond.
Temperature and Humidity:
- Some UV-cure adhesives may be sensitive to temperature and humidity. Adhesive manufacturers often provide recommended curing conditions, and deviations from these conditions can affect the performance of the adhesive.
UV Absorption by Colored Glass:
- Colored or tinted glass may absorb UV light, reducing its ability to reach and cure the adhesive. It’s essential to consider the type of glass being used and whether it may impact the curing process.
UV Light Shielding:
- Surrounding materials or structures that block or reflect UV light can affect the curing of the adhesive. Ensuring UV light can reach all areas where the adhesive is applied is crucial.
Adhesive Compatibility:
- Not all UV-cure adhesives are suitable for bonding all types of glass. Choosing an adhesive compatible with the specific type of glass and the intended application is essential.
Safety Concerns:
- UV light can be harmful to the eyes and skin. Adequate safety precautions, such as using protective equipment and ensuring proper ventilation, are necessary when working with UV-cure adhesives.
To overcome these challenges, following the manufacturer’s guidelines, conducting thorough testing, and maintaining proper curing conditions during the bonding process is essential.
Are there any emerging trends or innovations in the UV cure adhesive for glass?
However, please note that the information might need to be updated, and it’s essential to check for the latest developments in the field.
Improved Formulations:
- Ongoing research aims to develop UV cure adhesive formulations with enhanced properties, such as higher strength, improved flexibility, and better resistance to environmental factors like UV radiation and temperature variations.
Faster Curing Times:
- Efforts are being made to reduce UV cure adhesives’ curing times, enhancing manufacturing processes’ efficiency and productivity.
Low-temperature Curing:
- Innovations are focused on formulating UV cure adhesives that can cure at lower temperatures, expanding their applicability to temperature-sensitive substrates like certain types of plastics.
Enhanced Transparency:
- Improved transparency is a key focus, especially in applications where aesthetics and clarity are crucial, such as in glass bonding for display panels and optical devices.
Adhesion to Diverse Substrates:
- Researchers are developing UV cure adhesives with broad substrate compatibility, enabling bonding to a wide range of materials beyond glass.
Functional Additives:
- Incorporating additives for specific functionalities, such as increased thermal or improved chemical resistance, is an area of ongoing research.
Environmentally Friendly Formulations:
- Increasing attention is given to developing UV cure adhesives with reduced environmental impact, such as formulations with lower levels of volatile organic compounds (VOCs) or using more sustainable raw materials.
Customized Solutions:
- With the growth of various industries, there is a trend towards developing UV cure adhesives tailored to specific applications, meeting the unique requirements of industries such as electronics, automotive, and medical devices.
To stay updated on the latest trends and innovations in UV cure adhesives for glass, it’s recommended to check recent publications, industry conferences, and information from leading manufacturers and research institutions.
Conclusion:
As we conclude our exploration into the world of UV cure adhesive for glass, it becomes evident that this innovative bonding solution holds tremendous promise across various industries. Its quick curing time, versatility, and reliability make it a standout choice for applications demanding precision and durability. With ongoing advancements, the future of glass bonding appears bright under the UV cure adhesive spotlight.
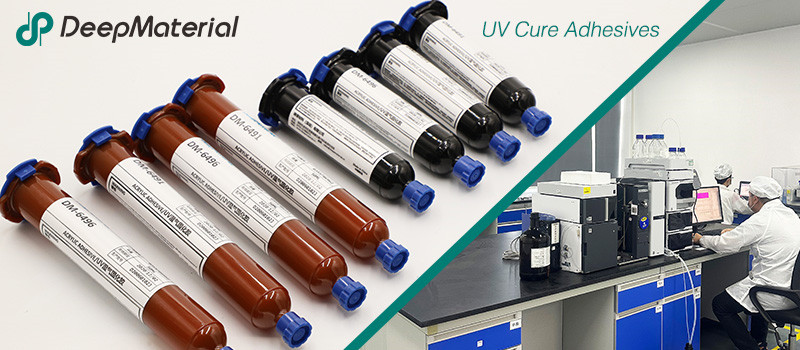
DeepMaterial
Based on the core technology of adhesives, DeepMaterial has developed adhesives for chip packaging and testing, circuit board level adhesives, and adhesives for electronic products. Based on adhesives, it has developed protective films, semiconductor fillers, and packaging materials for semiconductor wafer processing and chip packaging and testing. More…
UV Curing Adhesives
UV light cure have a number of benefits making them a popular choice among many product assembly and manufacturing applications. Many UV light cure adhesives can provide a nearly instantaneous bond to difficult substrates like glass and plastic. UV cure adhesives often require an accelerator or UV light for a bond to form.
Adhesive Blogs & News
The latest adhesive industry science and technology, Deepmaterial news, and market trends and forecasts.
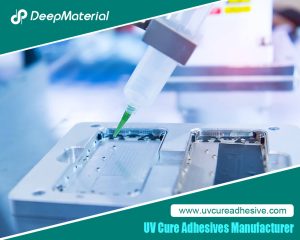
The Quantitative Influence of Crosslinking Density on the Flexibility and Hardness of Adhesives and the Formulation Optimization Strategy
The Quantitative Influence of Crosslinking Density on the Flexibility and Hardness of Adhesives and the Formulation Optimization Strategy This article systematically expounds the quantitative relationship between the crosslinking density and the flexibility and hardness of adhesives. Combining the theories of polymer physics with experimental analysis methods, it reveals the mechanism of the action of the
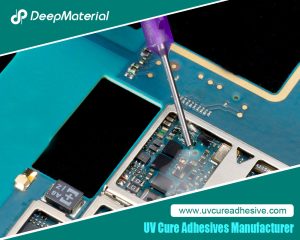
Technical Strategies for Balancing the Rapid Curing Property and Long Operating Time of UV Adhesives
Technical Strategies for Balancing the Rapid Curing Property and Long Operating Time of UV Adhesives UV adhesives have been widely used in many fields such as electronics, optics, and medicine due to their advantages of rapid curing, high bonding strength, and environmental protection. However, their rapid curing property also brings challenges in some application scenarios.
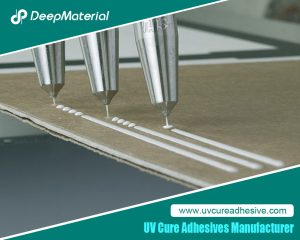
Biocompatibility of LED UV Glue Adhesive and Its Application Potential in Medical and Food Packaging Fields
Biocompatibility of LED UV Glue Adhesive and Its Application Potential in Medical and Food Packaging Fields LED UV glue adhesive has been widely applied in numerous fields due to its advantages such as rapid curing and easy operation. However, in fields with stringent safety requirements like medical and food packaging, its biocompatibility after curing
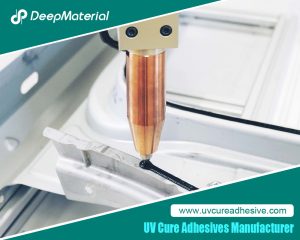
Exploring the Environmental Performance of UV Glue and Strategies for Optimizing Odor and VOC Content
Exploring the Environmental Performance of UV Glue and Strategies for Optimizing Odor and VOC Content UV glue, as an adhesive that achieves rapid curing through ultraviolet (UV) light irradiation, has been widely applied in numerous fields such as electronics, optics, healthcare, and automobiles, thanks to its advantages of fast curing speed, high bonding strength, and
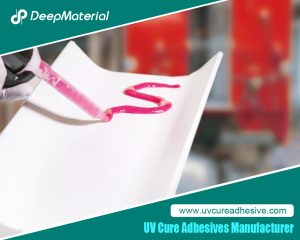
Compatibility Analysis and Countermeasures of LED UV Glue with Automated Production Equipment
Compatibility Analysis and Countermeasures of LED UV Glue with Automated Production Equipment LED UV glue has been widely used in modern manufacturing due to its advantages such as fast curing speed, high bonding strength, and environmental friendliness. However, in the automated production process, if there are problems with the adaptability between the glue and equipment
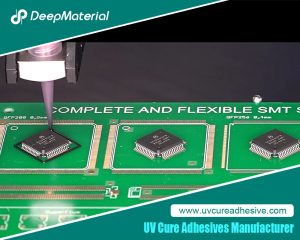
Influence of Viscosity and Thixotropy of Glue on the Quality of Glue Dots in the Dispensing Process and Solutions
Influence of Viscosity and Thixotropy of Glue on the Quality of Glue Dots in the Dispensing Process and Solutions The dispensing process is an important part of the application of LED UV glue adhesive, and the quality of this process directly affects the final performance of the product. The physical properties of the glue,