- Home
- >
- UV Cure Adhesive
- >
- UV Curing Encapsulants
UV Curing Encapsulants
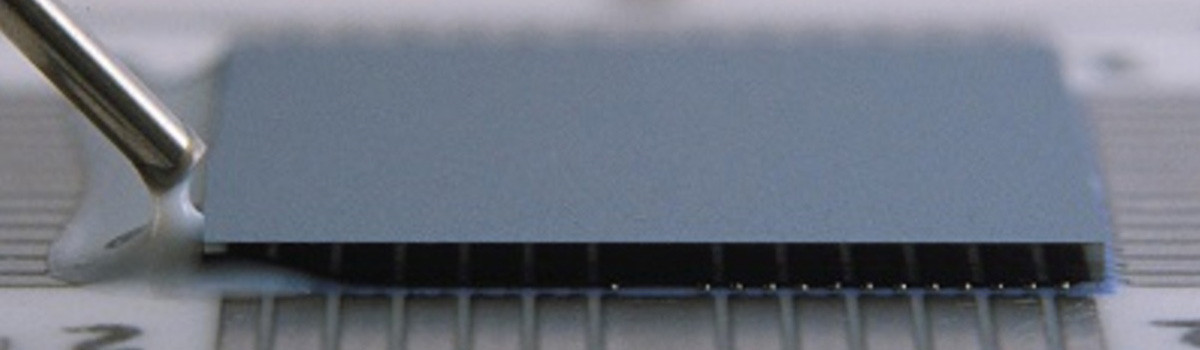
UV Curing Encapsulants are a crucial category in advanced materials and manufacturing processes. UV-curing encapsulants play a pivotal role in various industries, offering unique properties and applications that make them indispensable for multiple purposes. In this guide, we will explore the intricacies of UV curing encapsulants, their features, and applications, and answer essential questions to enhance your understanding of this cutting-edge technology.
Table of Contents
ToggleWhat are UV-curing encapsulants, and how do they work?
UV-curing encapsulants are materials used in various industries to encapsulate or coat electronic components, assemblies, or other sensitive devices. The encapsulation process involves applying a liquid or gel-like material to protect the enclosed components from environmental factors such as moisture, dust, chemicals, and mechanical stress. UV-curing encapsulants are unique because they cure or solidify quickly when exposed to ultraviolet (UV) light.
Here’s a general overview of how UV-curing encapsulants work:
- Liquid Formulation:UV-curing encapsulants typically come in liquid form. This liquid contains a mixture of monomers, oligomers, photoinitiators, and other additives.
- Application:The liquid encapsulant is applied to the components or devices that need protection. This can be done through dispensing, spraying, or other application methods, depending on the application’s specific requirements.
- UV Exposure:Once the liquid encapsulant is applied, it must be exposed to UV light to initiate curing. UV light activates the photoinitiators present in the formulation.
- Photopolymerization:The activated photoinitiators trigger a polymerization reaction within the encapsulant. This reaction causes the monomers and oligomers to cross-link and form a solid, three-dimensional network structure. The encapsulant hardens rapidly during this process.
- Cured Encapsulation:After exposure to UV light, the encapsulant becomes a solid, durable material that protects the enclosed components. The cured encapsulant forms a protective barrier against environmental elements, preventing damage and ensuring the long-term reliability of the devices.
The advantages of UV-curing encapsulants include:
- Rapid Cure Time:UV-curing encapsulants cure within seconds or minutes, allowing for high-speed production.
- Precise Control:The curing process is easily controllable, allowing manufacturers to optimize the encapsulation conditions.
- Low Heat Generation:UV curing generates minimal heat during the procedure, reducing the risk of thermal damage to sensitive components.
- Reduced Volatile Organic Compounds (VOCs):UV-curing formulations often contain fewer VOCs than traditional curing methods, making them more environmentally friendly.
UV-curing encapsulants find applications in electronics manufacturing, such as coating integrated circuits, sensors, LEDs, and other electronic devices where fast and efficient encapsulation is crucial.
What industries commonly utilize UV-curing encapsulants?
UV-curing encapsulants are commonly used in various industries where the encapsulation or protection of sensitive components is required. UV curing involves using ultraviolet (UV) light to cure or harden a liquid or gel-like material, creating a solid and protective encapsulation. Here are some industries where UV-curing encapsulants find typical applications:
Electronics Manufacturing:
- UV-curing encapsulants protect electronic components such as semiconductors, printed circuit boards (PCBs), and sensors from environmental factors, moisture, and physical damage.
Medical Devices:
- Medical electronics often use UV-cured encapsulants to protect sensitive components from bodily fluids and ecological conditions. These encapsulants may be biocompatible and protect sterilization processes.
Optoelectronics:
- UV-curable materials encapsulate optoelectronic devices, including LEDs (light-emitting diodes) and photovoltaic cells. The transparent nature of UV-cured materials is beneficial in maintaining optical clarity.
Automotive Electronics:
- UV-curing encapsulants are used in automotive applications to protect electronic components from vibration, heat, and other harsh environmental conditions.
Aerospace and Defense:
- In aerospace and defense applications, UV-cured encapsulants protect electronics in avionics, sensors, and communication devices. Their lightweight and durable properties make them suitable for these industries.
Renewable Energy:
- UV-cured encapsulants are used in the encapsulation of solar cells and modules. They protect against weathering, UV radiation, and moisture, ensuring the longevity and performance of solar panels.
Telecommunications:
- Fiber optic components and other telecommunications devices often use UV-cured materials for protection and insulation. The rapid curing process is advantageous in high-volume manufacturing.
Consumer Electronics:
- For protection and durability, various consumer electronic devices, such as smartphones, wearables, and smart gadgets, may incorporate UV-curing encapsulants.
Industrial Equipment:
- UV-cured encapsulants are used to encapsulate components in industrial equipment to protect against chemicals, moisture, and physical damage.
Automotive Lighting:
- UV-cured encapsulants are commonly used in the production of automotive lighting systems, providing a protective layer for bulbs and LEDs.
The use of UV-curing encapsulants continues to expand as technology advances, and the demand for high-performance, durable, and efficient encapsulation solutions grows across various industries.
What are the key characteristics that make UV-curing encapsulants unique?
UV-curing encapsulants are cured or hardened materials using ultraviolet (UV) light. These encapsulants have several key characteristics that make them unique for specific applications. Here are some of the key features:
Rapid Cure Time:
- UV-curing encapsulants cure quickly when exposed to UV light. This quick cure time can be advantageous in manufacturing processes where fast production is essential.
Selective Curing:
- UV curing is a process that only cures in areas exposed to UV light. This allows for precise control over the curing process and is particularly useful in applications requiring selective or patterned encapsulation.
Low Heat Generation:
- UV curing typically generates low heat compared to other curing methods like thermal curing. This can be beneficial when working with heat-sensitive components or materials.
Energy Efficiency:
- UV-curing systems are generally energy-efficient because the curing process occurs quickly, reducing overall energy consumption compared to processes that require prolonged heating.
Solvent-Free Formulations:
- Many UV-curing encapsulants are available in solvent-free formulations. This is advantageous for applications with undesirable solvents due to environmental or health considerations.
Excellent Adhesion:
- UV-cured encapsulants often provide strong adhesion to various substrates, including plastics, metals, and electronic components. This characteristic is crucial for ensuring the encapsulated material adheres well to the surfaces it is intended to protect.
Chemical Resistance:
- UV-cured encapsulants can offer good chemical resistance, making them suitable for applications where exposure to harsh chemicals is a concern.
Optical Clarity:
- Some UV-curing encapsulants are formulated to be optically transparent, allowing for applications where transparency or clarity is essential, such as in optical devices or displays.
Flexibility and Toughness:
- UV-cured encapsulants can be engineered to provide flexibility or toughness based on the application’s specific requirements. This versatility makes them suitable for various applications, from delicate electronics to more rugged environments.
Environmental Considerations:
- UV-curing processes are often considered environmentally friendly because they do not typically involve the release of volatile organic compounds (VOCs) and can be more energy-efficient compared to some traditional curing methods.
These characteristics make UV-curing encapsulants well-suited for applications in electronics, optics, medical devices, and other industries where precise and efficient encapsulation is required.
How does the curing process using UV light differ from other curing methods?
The curing process using UV (ultraviolet) light differs from other curing methods, primarily in the energy source used for the curing reaction. UV curing is a photochemical process that uses ultraviolet light to initiate a polymerization reaction in certain materials, typically inks, coatings, adhesives, and resins. Here are some critical differences between UV curing and other curing methods:
Energy Source:
- UV Curing:Utilizes ultraviolet light in the range of 200 to 400 nanometers to initiate the curing reaction. UV light activates photoinitiators, which in turn trigger polymerization.
- Other Curing Methods:Use heat, chemical reactions, or other forms of energy to initiate the curing process. For example, thermal curing involves the application of heat, while chemical curing may involve using catalysts or initiators.
Speed of Curing:
- UV Curing:Generally offers rapid curing times, often in seconds or milliseconds. The process is quick and does not require extended exposure times.
- Other Curing Methods:Cure times can vary widely, and some methods may require longer durations for the curing process to complete.
Selective Curing:
- UV Curing:Provides precise control over curing due to the focused nature of UV light. It allows for selective curing in specific areas, making it suitable for intricate patterns and designs.
- Other Curing Methods:These may offer a different level of precision, and selective curing can be more challenging.
Temperature Sensitivity:
- UV Curing:Typically operates at lower temperatures than thermal curing methods, making it suitable for heat-sensitive substrates.
- Other Curing Methods:Some methods, such as heat curing, may require elevated temperatures that could damage heat-sensitive materials.
Environmental Considerations:
- UV Curing:Often considered environmentally friendly as it does not involve the emission of volatile organic compounds (VOCs) or the generation of excessive heat.
- Other Curing Methods:Depending on the method, environmental concerns may be related to emissions or energy consumption.
Equipment Complexity:
- UV Curing:Requires specialized UV lamps, LED sources, and appropriate control systems. The equipment can be more compact compared to some other curing methods.
- Other Curing Methods:Equipment requirements vary, and some methods may involve more complex setups.
It’s important to note that the choice of curing method depends on the specific application, material properties, and desired outcomes. Depending on their unique requirements, different industries and processes may favor UV curing or other methods.
What types of polymers are commonly used in UV-curing encapsulants?
UV-curing encapsulants, used for encapsulating electronic components, LEDs, and other sensitive devices, often consist of polymers that can be cross-linked rapidly under ultraviolet (UV) light. These polymers provide the enclosed components protection, insulation, and mechanical support. Common types of polymers used in UV-curing encapsulants include:
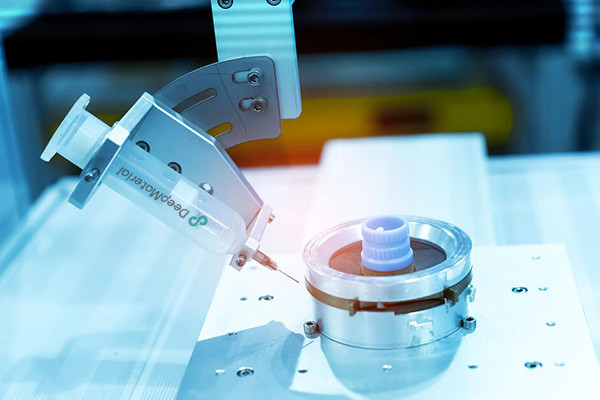
Epoxy Resins:
- Epoxy-based UV-curing encapsulants offer excellent adhesion, thermal stability, and mechanical strength. They are commonly used for encapsulating electronic components and protecting against environmental factors.
Acrylate Resins:
- UV-curable acrylate resins are widely used in encapsulation due to their fast curing times and versatility. They can be formulated to achieve various properties such as flexibility, toughness, and chemical resistance.
Silicone Resins:
- UV-curable silicone encapsulants are known for their excellent thermal stability and flexibility. They provide reasonable protection against moisture, chemicals, and extreme temperatures. Silicone encapsulants are often used in applications where flexibility and a wide operating temperature range are critical.
Polyurethane Resins:
- UV-curable polyurethane encapsulants balance mechanical properties, flexibility, and chemical resistance. They are suitable for applications where the encapsulated components may experience dynamic stresses.
Polyesters:
- UV-curable polyesters are used in encapsulation applications where rigidity and UV resistance are required. They can provide reasonable protection against UV radiation and environmental factors.
Hybrid Systems:
- Some UV-curing encapsulants may be formulated as hybrid systems, combining two or more types of polymers to achieve specific performance characteristics. For example, a mixed formulation may combine acrylates’ flexibility with silicone’s thermal stability.
The selection of the appropriate polymer for UV-curing encapsulation depends on the application’s specific requirements. Factors such as the operating environment, mechanical properties, thermal resistance, and desired cure speed are crucial in determining the most suitable encapsulant. Additionally, the formulation may include additives such as UV stabilizers, adhesion promoters, and fillers to enhance the overall performance of the encapsulation material.
What are the primary applications of UV-curing encapsulants in electronics manufacturing?
UV-curing encapsulants play a crucial role in various applications in electronics manufacturing. These encapsulants provide protection, insulation, and mechanical support to electronic components and devices. Some primary applications include:
Printed Circuit Board (PCB) Encapsulation:
- UV-curing encapsulants are applied to encapsulate and protect entire PCBs or specific components on the board. This protects the electronics from environmental factors such as moisture, dust, and chemicals, enhancing the reliability and lifespan of the electronic devices.
LED Encapsulation:
- LEDs are sensitive to environmental conditions, and UV-curing encapsulants are often used to protect them from moisture, heat, and mechanical stress. The encapsulants enhance the performance and reliability of LEDs in various applications, including lighting and display technologies.
Semiconductor Encapsulation:
- In semiconductor manufacturing, UV-curing encapsulants protect delicate semiconductor devices from external influences. This helps prevent contamination, provide management, and improve device performance.
Microelectronics and MEMS Devices:
- Microelectronic components and Micro-Electro-Mechanical Systems (MEMS) often require precise encapsulation for protection. UV-curing encapsulants can protect these miniature devices, ensuring their reliability and functionality.
Sensor Encapsulation:
- Sensors benefit from encapsulation with UV-curing materials, especially those used in harsh environments. These encapsulants provide a protective barrier against moisture, chemicals, and physical damage, ensuring sensors’ accurate and stable operation.
Smart Cards and RFID Devices:
- UV-curing encapsulants manufacture smart cards and Radio-Frequency Identification (RFID) devices. These materials protect the electronic components embedded in these cards, ensuring durability and resistance to environmental factors.
Automotive Electronics:
- Automotive electronic components, such as sensors, control modules, and displays, often require robust encapsulation to protect against temperature variations, vibrations, and chemical exposure. UV-curing encapsulants are employed to meet these requirements.
Medical Electronics:
- Electronic devices used in medical applications, such as sensors, diagnostic equipment, and monitoring devices, benefit from UV-curing encapsulation for protection against bodily fluids, chemicals, and environmental contaminants.
Consumer Electronics:
- Various consumer electronic devices, such as smartphones, wearables, and electronic modules, use UV-curing encapsulants to enhance durability, protect against external factors, and improve overall device reliability.
The versatility, rapid curing times, and ability to achieve precise encapsulation make UV-curing encapsulants well-suited for various applications in electronics manufacturing, contributing to the production of reliable and high-performance electronic devices.
How do UV-curing encapsulants contribute to the protection of electronic components?
UV-curing encapsulants contribute significantly to the protection of electronic components by providing a protective barrier against various environmental factors. Here are several ways in which UV-curing encapsulants contribute to the protection of electronic components:
Moisture and Chemical Resistance:
- UV-curing encapsulants form a barrier that protects electronic components from moisture and chemicals. This is particularly important in environments where exposure to humidity, water, corrosive substances, or chemicals could lead to the degradation or malfunction of electronic devices.
Mechanical Protection:
- The encapsulation process helps create a protective layer around electronic components, providing mechanical support and guarding against physical impacts, vibrations, and potential damage during handling, transportation, or operation.
Dust and Particle Protection:
- UV-curing encapsulants create a sealed environment around electronic components, preventing the ingress of dust, particles, and contaminants. This is crucial in maintaining the cleanliness of sensitive electronic elements and preventing performance issues.
Thermal Management:
- Some UV-curing encapsulants are formulated to have excellent thermal conductivity. Encapsulating electronic components with these materials can improve heat dissipation, helping regulate and manage the temperatures of sensitive devices.
UV Resistance:
- UV-curing encapsulants themselves are often designed to be resistant to UV radiation. This feature ensures the encapsulant remains stable and does not degrade when exposed to sunlight or other ultraviolet light sources.
Electrical Insulation:
- Encapsulation with UV-curing materials provides electrical insulation, protecting electronic components from electrical interference, short circuits, and potential damage from exposure to conductive materials.
Corrosion Protection:
- For electronic components in harsh environments or those exposed to corrosive substances, UV-curing encapsulants can provide a protective barrier against corrosion, extending the lifespan of the components.
Adhesion and Sealing:
- UV-curing encapsulants adhere well to various substrates, ensuring a secure and reliable seal around electronic components. This helps create a barrier against entering liquids, gases, and contaminants.
UV-Curable Formulations for Precision:
- UV-curing encapsulants offer rapid and controlled curing, allowing for precise encapsulation of intricate electronic components. This precision ensures that the encapsulant covers all critical areas and provides uniform protection.
Enhanced Durability:
- UV-curing encapsulants improve electronic components’ overall durability, enabling them to withstand challenging operating conditions and extend their operational lifespan.
Combining these protective features makes UV-curing encapsulants a valuable choice in electronics manufacturing, contributing to electronic devices’ reliability, longevity, and performance in a wide range of applications.
Are UV-curing encapsulants suitable for outdoor applications?
UV-curing encapsulants can be suitable for outdoor applications. Still, their performance depends on various factors, such as the specific formulation of the encapsulant, the environmental conditions, and the intended application. UV-curing encapsulants are known for their fast curing times and the ability to provide a protective layer, making them suitable for specific outdoor applications.
Here are some considerations:
- UV Resistance:UV-curing encapsulants should be formulated to resist degradation caused by sun exposure to ultraviolet (UV) radiation. UV stabilizers or additives may be incorporated into the encapsulant to enhance its resistance to UV light.
- Weather Resistance:Outdoor applications expose materials to various weather conditions, including temperature variations, moisture, and harsh weather elements. The encapsulant should be designed to withstand these conditions without degrading or losing its protective properties.
- Temperature Stability:Outdoor environments often experience temperature fluctuations. The encapsulant should have good temperature stability to prevent cracking, shrinking, or other forms of degradation under extreme temperatures.
- Chemical Resistance:Depending on the specific outdoor application, the encapsulant may be exposed to various chemicals. It’s essential to ensure that the encapsulant is resistant to the chemicals in the environment to maintain its integrity and protective function.
- Mechanical Properties:The encapsulant should maintain its mechanical properties, such as flexibility and adhesion, under outdoor conditions. This is important to prevent the material from becoming brittle or losing its bond over time.
- Application-specific Requirements:Different outdoor applications may have specific requirements. For example, if the encapsulant protects electronic components, it should provide electrical insulation and have good dielectric properties.
It’s crucial to consult with the manufacturer or supplier of the specific UV-curing encapsulant you are considering to understand its suitability for your intended outdoor application. Additionally, conducting thorough testing and evaluation under simulated or actual outdoor conditions can help ensure the encapsulant meets the performance requirements for your specific use case.
What role do UV stabilizers play in UV-curing encapsulants?
UV stabilizers play a crucial role in UV-curing encapsulants by helping to protect the material from the potentially harmful effects of ultraviolet (UV) radiation. UV-curing encapsulants are materials that solidify or cure when exposed to UV light. These encapsulants are often used in applications like adhesives, coatings, and potting compounds.
Here are the critical roles of UV stabilizers in UV-curing encapsulants:
- Preventing Degradation:UV stabilizers help prevent the degradation of the encapsulant material when exposed to UV radiation. UV light can initiate chemical reactions that may lead to the breakdown of the polymer matrix, resulting in reduced mechanical properties, discoloration, or other undesirable changes in the material.
- Extending Service Life:UV stabilizers contribute to the material’s longevity and performance over time by protecting the encapsulant from UV-induced degradation. This is particularly important in applications where the encapsulant is exposed to sunlight or other sources of UV radiation.
- Maintaining Optical Clarity:UV stabilizers help maintain the optical clarity of UV-curing encapsulants. Without stabilizers, exposure to UV light might cause the material to turn yellow or become hazy over time, which is undesirable in applications where transparency or clarity is essential.
- Enhancing Weatherability:UV stabilizers improve the wearability of UV-curing encapsulants, helping them withstand outdoor environmental conditions. This is especially important in applications like outdoor electronics or solar panels, where the encapsulant is exposed to sunlight and various weather elements.
- Preventing Cracking and Chalking:UV stabilizers can help prevent the encapsulant from developing cracks or chalking on the surface. These issues can arise due to UV-induced degradation and UV stabilizers work to mitigate these effects.
UV stabilizers are additives that play a protective role in UV-curing encapsulants, safeguarding the material against the potentially harmful effects of UV radiation. This helps ensure the encapsulated components’ long-term performance, durability, and appearance.
How do UV-curing encapsulants contribute to the overall reliability of electronic devices?
UV-curing encapsulants play a crucial role in enhancing the reliability of electronic devices by providing protection and stability to sensitive electronic components. Here are several ways in which UV-curing encapsulants contribute to the overall reliability of electronic devices:
Environmental Protection:
- UV-curing encapsulants create a protective barrier around electronic components, shielding them from environmental factors such as moisture, dust, chemicals, and contaminants. This protection is vital for preventing corrosion, short circuits, and other issues from exposure to harsh conditions.
Mechanical Stability:
- These encapsulants enhance the mechanical stability of electronic devices by forming a durable and rigid coating. This helps to secure delicate components in place and reduces the risk of damage due to mechanical stress, vibration, or shock during transportation, handling, or operation.
Thermal Management:
- UV-curing encapsulants often have excellent thermal conductivity properties. By efficiently dissipating heat generated by electronic components, they contribute to thermal management. This is crucial for preventing overheating, which can lead to performance degradation and even component failure.
Electrical Insulation:
- Encapsulants provide electrical insulation, containing the contact of conductive elements with external materials. This insulation helps to avoid short circuits and electrical failures, ensuring the proper functioning of electronic devices.
Chemical Resistance:
- UV-curing encapsulants are often resistant to chemicals and solvents. This resistance is essential for protecting electronic components from exposure to aggressive substances that could otherwise compromise their performance and longevity.
UV Resistance:
- Since these encapsulants cure using ultraviolet (UV) light, they inherently resist degradation caused by exposure to UV radiation. This property benefits electronic devices used outdoors or in environments with high UV exposure.
Improved Reliability in Harsh Environments:
- Electronic devices are often deployed in harsh environments, such as automotive, aerospace, or industrial settings. UV-curing encapsulants help improve the overall reliability of devices in these environments by providing robust protection against challenging conditions.
Streamlined Manufacturing Processes:
- UV-curing encapsulants offer fast curing times, enabling efficient and streamlined manufacturing processes. This can increase productivity and reduce production costs while maintaining high-quality encapsulation.
UV-curing encapsulants enhance the reliability of electronic devices by providing a protective, stable, and durable encapsulation that guards against environmental, mechanical, thermal, and electrical stresses. This contributes to electronic components’ longevity and proper functioning, especially in challenging operating conditions.
Can UV curing encapsulants be customized for specific applications?
Yes, UV (ultraviolet) curing encapsulants can often be customized for specific applications. UV-curing encapsulants are materials that harden or cure when exposed to ultraviolet light. They are commonly used for encapsulating and protecting electronic components, such as integrated circuits, LEDs, and sensors.
Customization of UV curing encapsulants can involve several factors:
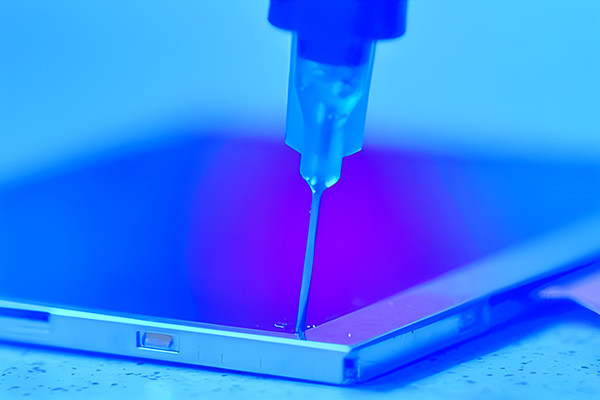
- Chemical Formulation:The chemical composition of the encapsulant can be tailored to meet specific performance requirements. This may include adjusting the viscosity, flexibility, hardness, and other material properties. Different monomers, oligomers, and additives can be combined to achieve the desired characteristics.
- Curing Properties:The curing process, including the curing rate and the cure depth, can be adjusted to match the specific production requirements. This is important for ensuring that the encapsulant cures thoroughly and consistently in the intended application.
- Optical Properties:The formulation can be optimized to meet these requirements for applications where visual clarity or specific light transmission properties are critical. This is particularly important for devices like LEDs and sensors where light transmission may be a key consideration.
- Thermal Conductivity:In some applications, such as in the encapsulation of high-power electronic components, thermal conductivity may be crucial. UV curing encapsulants can be formulated to have enhanced thermal conductivity to dissipate heat effectively.
- Adhesion:The encapsulant’s adhesion to various substrates, such as metals, ceramics, or plastics, can be customized. Ensuring proper adhesion is essential for the encapsulant to protect the enclosed components effectively.
- Chemical Resistance:Depending on the environment in which the encapsulated components will be used, the chemical resistance of the encapsulant may need to be customized to withstand exposure to specific chemicals or environmental conditions.
- Environmental Considerations:Formulations can also be adjusted to meet specific environmental standards or regulations, such as compliance with RoHS (Restriction of Hazardous Substances).
To customize UV curing encapsulants, it’s advisable to work closely with a manufacturer or supplier that specializes in these materials. They can guide in selecting or formulating a product that meets the exact requirements of the intended application. Testing and validation should also be conducted to ensure the customized encapsulant performs as expected in the specific application.
What considerations should be taken into account when selecting a UV-curing encapsulant?
Selecting a UV-curing encapsulant involves carefully considering various factors to ensure that the chosen material meets the specific requirements of the intended application. Here are some key considerations:
Application Requirements:
- Physical Properties:Consider the mechanical, thermal, and electrical properties required for the application. For example, if the encapsulant is exposed to high temperatures, it should have good thermal stability.
- Flexibility:Depending on the application, flexibility may be crucial to accommodate any movement or stress the encapsulated components may experience.
Chemical Compatibility:
- Substrate Compatibility:Ensure the encapsulant is compatible with the materials it will contact, including electronic components, PCBs, and other substrates.
- Chemical Resistance:Evaluate the resistance of the encapsulant to chemicals, solvents, and environmental factors to ensure long-term stability.
UV-Curing Performance:
- Curing Speed:Consider the required curing time and whether the UV-curing encapsulant meets the speed requirements of the manufacturing process.
- UV Light Source:Ensure that the UV light source used for curing matches the specifications recommended by the encapsulant manufacturer.
Optical Properties:
- Transparency:Depending on the application, the level of openness may be critical. Some applications may require clear encapsulants for visual or aesthetic reasons.
- Refractive Index:Match the refractive index of the encapsulant with other materials to minimize optical distortion.
Environmental Conditions:
- Temperature Range:Consider the operating temperature range of the encapsulant and ensure it aligns with the environmental conditions the device will face.
- Moisture Resistance:Evaluate the encapsulant’s resistance to moisture and humidity, especially for outdoor or harsh environments.
Electrical Insulation:
- Dielectric Strength:Ensure that the encapsulant provides sufficient electrical insulation to protect electronic components from potential electrical breakdown.
- Volume Resistivity:Check the volume resistivity to ensure effective electrical insulation over time.
Adhesion:
- Substrate Adhesion:Evaluate the encapsulant’s adhesion properties to ensure it bonds well with the substrate materials and prevents delamination.
- Coefficient of Thermal Expansion (CTE):Match the CTE of the encapsulant with the substrates to minimize the risk of cracking due to thermal cycling.
Regulatory Compliance:
- Compliance Standards:Ensure that the selected encapsulant meets relevant industry standards and regulatory requirements for the specific application.
Cost Considerations:
- Material Cost:Consider the encapsulant’s overall cost, including material and processing costs. Balance performance requirements with budget constraints.
Supplier Reliability:
- Supplier Reputation:Choose a reliable and reputable supplier with a history of delivering quality products and providing technical support.
By carefully considering these factors, you can select a UV-curing encapsulant that aligns with your application’s specific needs and performance criteria.
How does the environmental impact of UV-curing encapsulants compare to traditional methods?
The environmental impact of UV-curing encapsulants compared to traditional methods depends on various factors, including the specific materials used, the manufacturing processes, and the end-of-life considerations. Here are some general points to consider:
UV-Curing Encapsulants:
Energy Consumption:
- UV curing typically requires less energy than traditional methods like heat or solvent-based curing. The curing process is faster and can be more localized.
Volatile Organic Compounds (VOCs):
- UV-curing processes often result in lower VOC emissions compared to traditional methods. This is because UV curing doesn’t involve using solvents, which can release harmful VOCs into the atmosphere.
Chemical Usage:
- UV-curing encapsulants may use fewer chemicals and additives compared to traditional methods. The absence of solvents and the quicker curing process contribute to a potentially lower environmental impact.
Waste Generation:
- The efficiency of UV curing can lead to less material waste as it doesn’t require excess materials for cleanup or removal of solvents. The reduced waste generation can be an environmental benefit.
Temperature Control:
- UV curing often doesn’t require high-temperature processing, which can reduce the overall energy consumption associated with maintaining elevated temperatures.
Traditional Methods (Heat or Solvent-Based):
Energy Consumption:
- Traditional methods, such as heat curing, may require more energy, especially if high temperatures are needed. This can result in higher overall energy consumption.
VOC Emissions:
- Solvent-based encapsulants can release significant amounts of VOCs during curing. This can contribute to air pollution and have adverse effects on human health.
Chemical Usage:
- Some traditional encapsulants may require more chemicals, including solvents and additives. The use of these chemicals can contribute to environmental pollution.
Waste Generation:
- Traditional methods generate more waste, mainly if excess materials are used for cleanup or by-products need proper disposal.
Temperature Control:
- High-temperature processes may be necessary for conventional curing methods, leading to higher energy consumption and potentially contributing to greenhouse gas emissions.
Considerations:
- End-of-Life:
- The environmental impact should also consider the end-of-life stage. Are the materials recyclable or biodegradable, and what is the environmental impact of disposal?
- Specific Materials:
- The environmental impact can vary based on the specific UV-curing or traditional encapsulant materials. Different formulations may have different ecological footprints.
UV-curing encapsulants generally have the potential for a lower environmental impact due to reduced energy consumption, lower VOC emissions, and less waste generation. However, evaluating each case individually and considering the specific materials and processes involved is crucial. Additionally, technological advancements and sustainability practices can influence the environmental performance of both UV-curing and traditional methods.
Are there any safety considerations associated with the use of UV-curing encapsulants?
Yes, several safety considerations are associated with using UV-curing encapsulants. UV-curing encapsulants are materials that harden or cure when exposed to ultraviolet (UV) light. These encapsulants are commonly used in various industries, including electronics, optics, and medical devices. Here are some safety considerations:
UV Radiation Exposure:
- UV-curing encapsulants cure through exposure to UV light. Prolonged exposure to UV radiation can be harmful to the skin and eyes. Using appropriate personal protective equipment (PPE) such as gloves, safety glasses, and protective clothing is crucial to minimize skin contact and prevent eye injuries.
Ventilation:
- Ensure proper ventilation in the working area to avoid inhaling potentially harmful fumes released during the curing process. Use the encapsulants in well-ventilated spaces, or consider using fume extraction systems.
Material Handling:
- Follow proper procedures for handling and dispensing UV-curing encapsulants. Be aware of the material’s viscosity, curing time, and application requirements. Use the recommended tools and equipment to manage and administer the encapsulant safely.
Curing Process:
- Follow the manufacturer’s instructions regarding the curing process, including the recommended curing time and intensity of UV light. Improper curing may result in incomplete encapsulation and compromised performance.
Skin and Eye Contact:
- In case of skin contact, immediately wash the affected area with soap and water. If the encapsulant comes into contact with the eyes, rinse them thoroughly with water and seek medical attention if irritation persists.
Material Compatibility:
- Ensure that the UV-curing encapsulant is compatible with the materials it will contact, such as substrates and other components in the assembly. Some materials may react adversely to the encapsulant, affecting performance and safety.
Storage and Handling:
- Store UV-curing encapsulants according to the manufacturer’s guidelines, including temperature and humidity. Improper storage can affect the encapsulant’s properties and performance.
Waste Disposal:
- Dispose of waste materials, including uncured encapsulant and used containers, by local regulations. Some UV-curing materials may be classified as hazardous waste, and proper disposal practices should be followed.
Training and Awareness:
- Ensure that personnel working with UV-curing encapsulants are adequately trained on safety procedures and are aware of the potential risks associated with the materials.
Always refer to the specific product’s safety data sheet (SDS) provided by the manufacturer for detailed information on safety precautions, handling, and disposal instructions.
What advancements have been made in UV-curing encapsulant technology in recent years?
UV-curing encapsulants are commonly used in various industries, including electronics, solar, and medical devices, to protect and enhance the performance of components. Some key trends and advancements in this technology include:
Improved Formulations:
- Ongoing research has focused on developing encapsulant formulations with enhanced properties, such as improved flexibility, adhesion, and resistance to environmental factors like moisture, heat, and UV radiation.
High-Performance Materials:
- Advancements have been made in developing high-performance materials, such as silicone-based UV-curing encapsulants, which offer excellent thermal stability and electrical insulation properties.
Faster Curing Times:
- Efforts have been made to reduce curing times, enhancing the efficiency of manufacturing processes. This is especially important in industries where rapid production cycles are crucial.
Optical Clarity:
- UV-curing encapsulants for applications like LED lighting and solar panels have seen improvements in optical clarity to ensure that the encapsulant does not hinder the performance of the devices it protects.
Customization for Specific Applications:
- Researchers have been working on tailoring encapsulant formulations to meet the specific requirements of different applications. This involves adjusting properties such as hardness, flexibility, and thermal conductivity.
Enhanced Reliability:
- Reliability is a critical factor, especially in electronics and solar applications. Advances have been made to improve the long-term reliability of UV-cured encapsulants under various operating conditions.
Environmental Considerations:
- There is a growing emphasis on developing UV-curing encapsulants that are more environmentally friendly, with reduced levels of volatile organic compounds (VOCs) and other potentially harmful substances.
Process Optimization:
- Researchers and manufacturers have been optimizing the UV-curing process, ensuring uniform curing throughout the encapsulant and minimizing the risk of defects.
Compatibility with Advanced Technologies:
- As electronic devices become more advanced and miniaturized, UV-curing encapsulants are being developed to be compatible with the latest technologies and substrates.
It’s recommended to check the latest research articles, industry publications, and updates from manufacturers to get the most current information on advancements in UV-curing encapsulant technology.
Can UV-curing encapsulants be used in medical device manufacturing?
UV-curing encapsulants can be used in medical device manufacturing, but their suitability depends on various factors and the specific requirements of the medical device. UV-curing encapsulants are materials that solidify or cure when exposed to ultraviolet (UV) light. These materials are often used for encapsulating and protecting electronic components in devices.
Here are some considerations for using UV-curing encapsulants in medical device manufacturing:

Biocompatibility:
- Ensure the UV-curing encapsulant is biocompatible, meaning it won’t cause harmful reactions when in contact with living tissues. This is crucial for medical devices in direct or indirect contact with the human body.
Regulatory Compliance:
- Medical devices are subject to strict regulations, and any materials used in their manufacturing must comply with relevant standards and guidelines. Verify that the UV-curing encapsulant meets the regulatory requirements for medical devices in the intended market.
Chemical Compatibility:
- Consider the chemical compatibility of the encapsulant with other materials used in the medical device. Ensure it does not react adversely with components or substances it may contact during use.
Physical Properties:
- Evaluate the physical properties of the UV-curing encapsulant, such as its hardness, flexibility, and thermal resistance. These properties should align with the medical device’s specific needs and environmental conditions.
Curing Process:
- Assess whether the UV-curing process is suitable for the manufacturing process of the medical device. Consider factors such as the cure time, intensity of UV light required, and the ability to achieve consistent and reliable curing.
Adherence to Substrates:
- Verify that the encapsulant adheres well to the substrates used in the medical device. Poor adhesion can compromise the integrity of the encapsulation and the device’s overall performance.
Optical Clarity:
- For specific medical devices, especially those with visual components, the optical clarity of the encapsulant may be critical. Ensure that the encapsulant does not introduce visual distortions that could affect device functionality.
Before incorporating any material, including UV-curing encapsulants, into the manufacturing process of medical devices, it is advisable to consult with regulatory experts and perform thorough testing to ensure compliance and safety. Additionally, manufacturers should stay informed about updates in regulations and industry standards related to medical devices.
How does the cost of UV-curing encapsulants compare to alternative encapsulation methods?
Here are some general considerations regarding the cost of UV-curing encapsulants compared to alternative methods:
Material Cost:
- UV-curing encapsulants often have specific chemical formulations that can influence their material cost. The cost may vary depending on the required properties (such as flexibility, thermal conductivity, or resistance to environmental factors).
- Alternative encapsulation methods, such as thermosetting or thermoplastic materials, may also have varying material costs depending on their composition and performance characteristics.
Manufacturing Process:
- UV-curing encapsulants offer rapid curing times, which can contribute to increased efficiency in the manufacturing process. This might result in lower production costs, especially if the curing process allows faster throughput.
- Alternative methods involve different curing or manufacturing processes, and the associated equipment and labor costs can influence the overall cost.
Equipment and Energy Costs:
- UV-curing requires specific equipment, such as UV lamps, which may contribute to initial setup costs. However, the energy consumption during the curing process can be relatively low compared to alternative methods.
- Other encapsulation methods involve different equipment and energy requirements, impacting overall costs.
Application Considerations:
- The suitability of UV-curing encapsulants and alternative methods for specific applications can affect the overall cost. For example, if UV-curing provides better adhesion or performance in a particular application, it might justify the slightly higher material cost.
Market Demand and Supply:
- Market dynamics, including demand and supply, can influence the pricing of encapsulation materials. Economies of scale might lead to more competitive pricing if there’s a higher demand for UV-curing encapsulants.
Customization and Performance Requirements:
- Custom formulations or specific performance requirements can impact costs for UV-curing encapsulants and alternative methods. Customized solutions may come at a premium.
Conducting a detailed cost-benefit analysis based on your application needs, production volume, and other relevant factors is crucial to determining your particular use case’s most economical encapsulation method. Consulting with suppliers and industry experts will also provide you with the most current information on material costs and market trends.
What role do UV-curing encapsulants play in enhancing LED performance and longevity?
UV-curing encapsulants are crucial in enhancing LED (Light Emitting Diode) performance and longevity by providing protection and improving various aspects of LED devices. Here are some critical roles of UV-curing encapsulants in this context:
- Protection from Environmental Factors:UV-curing encapsulants create a protective barrier around the LED components, shielding them from environmental factors such as moisture, dust, and chemicals. This protection helps prevent corrosion, oxidation, and other forms of degradation that can compromise the performance and lifespan of LEDs.
- Thermal Management:Many UV-curing encapsulants are designed to have excellent thermal conductivity. This property helps to dissipate heat generated during LED operation, preventing overheating and maintaining optimal operating temperatures. Efficient thermal management is crucial for ensuring the stability and longevity of LED devices.
- Improved Light Output:Encapsulants can enhance the light output of LEDs by providing a medium with a high refractive index. This helps improve light extraction from the LED chip, reducing internal reflection and improving overall luminous efficiency.
- UV Resistance:Since LEDs emit UV light, the encapsulant must resist UV radiation. UV-curing encapsulants are formulated to withstand exposure to UV light without degrading or yellowing over time. This UV resistance is essential for maintaining the optical clarity of the encapsulant and preventing performance degradation.
- Enhanced Mechanical Strength:Encapsulants add mechanical strength to the LED package, protecting it from physical damage due to handling, vibration, or external forces. This mechanical reinforcement contributes to the overall robustness and durability of LED devices.
- Improved Reliability:By providing a protective and stable environment, UV-curing encapsulants contribute to the overall reliability of LED devices. This is particularly important in applications where reliability is critical, such as automotive lighting, aerospace, and outdoor lighting.
- Customization and Flexibility:UV-curing encapsulants offer flexibility in application and curing. They can be applied in a liquid state and then cured rapidly using UV light, allowing efficient and precise manufacturing processes. This enables the encapsulation of intricate LED designs and facilitates mass production.
UV-curing encapsulants play a multifaceted role in enhancing LED performance and longevity by providing protection, improving thermal management, enhancing light output, resisting UV radiation, adding mechanical strength, and contributing to overall reliability. These benefits collectively produce more efficient, durable, and reliable LED devices across various applications.
Are there any limitations or challenges associated with using UV-curing encapsulants?
UV-curing encapsulants are materials commonly used in electronics and other industries for protecting and insulating electronic components. While they offer several advantages, they also have some limitations and challenges. Here are some considerations:
Substrate Sensitivity:
- UV-curing encapsulants may not be suitable for all substrates. Some materials are sensitive to UV radiation and may degrade or undergo unwanted reactions during curing.
Depth of Cure:
- UV light penetration is limited, so the depth of cure is a consideration. Thicker sections or components with complex geometries may not cure completely, leading to potential performance issues.
Shadow Areas:
- Components with shadow areas not exposed to UV light may not cure adequately. Manufacturers must ensure that all areas requiring encapsulation receive sufficient UV exposure.
UV Light Source:
- The quality and intensity of the UV light source are critical. Curing may be complete if the light source is calibrated correctly or the power is sufficient, leading to reduced mechanical properties and inadequate protection.
Temperature Sensitivity:
- UV-curing encapsulants may be sensitive to temperature variations. Extreme temperatures can affect the curing process and the final properties of the encapsulant.
Moisture Sensitivity:
- Some UV-curing materials may be susceptible to moisture, and exposure to humidity during storage or application can affect their performance.
Chemical Compatibility:
- UV-curing encapsulants may not be compatible with certain chemicals or environmental conditions. Considering the application environment and potential exposure to chemicals that could compromise the encapsulant is essential.
Cost:
- UV-curing systems can be more expensive to set up initially. The cost of UV light sources and associated equipment may be higher than other encapsulation methods.
Health and Safety Considerations:
- UV light can pose health risks to human skin and eyes. Adequate safety measures, such as using appropriate personal protective equipment, must be taken during the handling and curing.
Post-Cure Shrinkage:
- Some UV-curing encapsulants may experience post-cure shrinkage, which can affect the long-term stability and performance of the encapsulated components.
Limited Working Time:
- Once the UV-curing process begins, it progresses rapidly. This limited working time can be a challenge for large-scale or intricate applications requiring precise placement or adjustments.
Considering these limitations and challenges, users must carefully assess their specific application requirements to determine whether UV-curing encapsulants are the most suitable choice for their needs. Additionally, ongoing advancements in materials and technology may address some of these limitations over time.
How can the proper handling and storage of UV-curing encapsulants be ensured for optimal performance?
Proper handling and storage of UV-curing encapsulants are crucial to ensure their optimal performance. UV-curing encapsulants are materials that harden or cure when exposed to ultraviolet (UV) light. Here are some guidelines to ensure their proper handling and storage:
Handling:
Clean Work Environment:
- Ensure the work area is clean and free from contaminants that could affect the encapsulant.
Use Clean Tools:
- Use clean and dry tools to handle the encapsulant to prevent any contamination.
Mixing:
- Follow the manufacturer’s instructions for mixing if the encapsulant requires it. Use the recommended ratios and procedures.
Avoid Air Entrapment:
- Minimize the introduction of air bubbles during application, as they can affect the encapsulant’s properties.
Proper Application:
- Apply the encapsulant evenly and at the recommended thickness to ensure adequate curing.
UV Exposure:
- Expose the encapsulant to the appropriate UV light source for the recommended duration and intensity. Follow the manufacturer’s guidelines for curing.
Safety Precautions:
- When handling UV-curing encapsulants, wear proper personal protective equipment (PPE), such as gloves and safety glasses.
Storage:
Temperature Control:
- Store encapsulants in a controlled environment with a stable temperature. Extreme temperatures can affect the encapsulant’s performance.
Avoid Sunlight Exposure:
- Store encapsulants away from direct sunlight, as UV exposure can prematurely cure or degrade the material.
Seal Properly:
- Ensure containers are tightly sealed to prevent exposure to air and moisture, which can affect the encapsulant’s properties.
Follow Shelf Life:
- Adhere to the manufacturer’s recommended shelf life. Do not use encapsulants that have exceeded their expiration date.
Storage Conditions:
- Follow specific storage recommendations provided by the manufacturer, such as storing in a dark, cool place.
Avoid Contamination:
- Prevent contamination by keeping storage containers and surrounding areas clean.
Monitor Conditions:
- Regularly check the storage conditions; if there are any deviations or concerns, consult the manufacturer or supplier for guidance.
Labeling:
- Clearly label containers with the product name, batch number, and expiration date for easy tracking and identification.
Always refer to the specific product documentation and guidelines provided by the encapsulant manufacturer for the most accurate and up-to-date information on handling and storage.
Conclusion:
In conclusion, UV curing encapsulants are a testament to the continuous innovation in materials science and manufacturing. Their versatile applications and unique properties make them an integral part of various industries. As technology evolves, so does the potential for advancements in UV-curing encapsulant technology. By exploring the questions in this guide, you have gained valuable insights into the world of UV-curing encapsulants, paving the way for informed decisions and applications in your field. If you have further inquiries or require particular guidance, feel free to reach out – we’re here to illuminate the path forward in UV curing encapsulation technology.
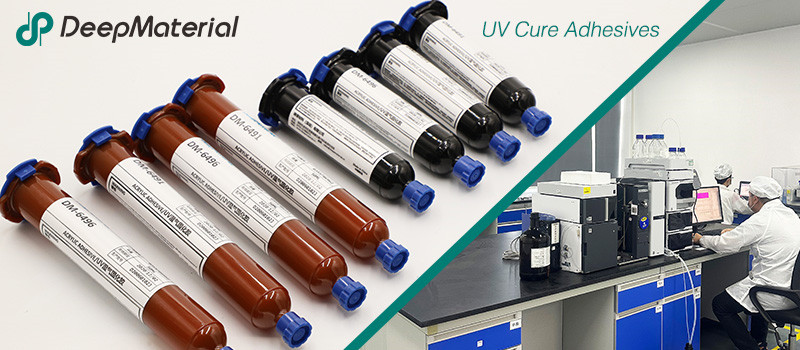
DeepMaterial
Based on the core technology of adhesives, DeepMaterial has developed adhesives for chip packaging and testing, circuit board level adhesives, and adhesives for electronic products. Based on adhesives, it has developed protective films, semiconductor fillers, and packaging materials for semiconductor wafer processing and chip packaging and testing. More…
UV Curing Adhesives
UV light cure have a number of benefits making them a popular choice among many product assembly and manufacturing applications. Many UV light cure adhesives can provide a nearly instantaneous bond to difficult substrates like glass and plastic. UV cure adhesives often require an accelerator or UV light for a bond to form.
Adhesive Blogs & News
The latest adhesive industry science and technology, Deepmaterial news, and market trends and forecasts.
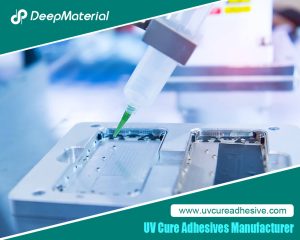
The Quantitative Influence of Crosslinking Density on the Flexibility and Hardness of Adhesives and the Formulation Optimization Strategy
The Quantitative Influence of Crosslinking Density on the Flexibility and Hardness of Adhesives and the Formulation Optimization Strategy This article systematically expounds the quantitative relationship between the crosslinking density and the flexibility and hardness of adhesives. Combining the theories of polymer physics with experimental analysis methods, it reveals the mechanism of the action of the
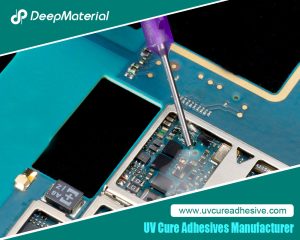
Technical Strategies for Balancing the Rapid Curing Property and Long Operating Time of UV Adhesives
Technical Strategies for Balancing the Rapid Curing Property and Long Operating Time of UV Adhesives UV adhesives have been widely used in many fields such as electronics, optics, and medicine due to their advantages of rapid curing, high bonding strength, and environmental protection. However, their rapid curing property also brings challenges in some application scenarios.
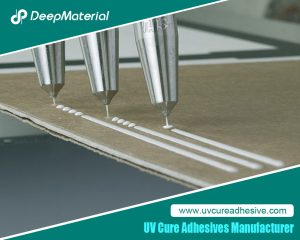
Biocompatibility of LED UV Glue Adhesive and Its Application Potential in Medical and Food Packaging Fields
Biocompatibility of LED UV Glue Adhesive and Its Application Potential in Medical and Food Packaging Fields LED UV glue adhesive has been widely applied in numerous fields due to its advantages such as rapid curing and easy operation. However, in fields with stringent safety requirements like medical and food packaging, its biocompatibility after curing
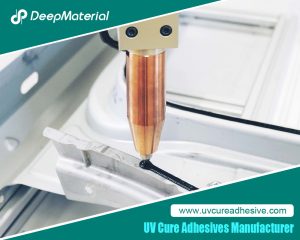
Exploring the Environmental Performance of UV Glue and Strategies for Optimizing Odor and VOC Content
Exploring the Environmental Performance of UV Glue and Strategies for Optimizing Odor and VOC Content UV glue, as an adhesive that achieves rapid curing through ultraviolet (UV) light irradiation, has been widely applied in numerous fields such as electronics, optics, healthcare, and automobiles, thanks to its advantages of fast curing speed, high bonding strength, and
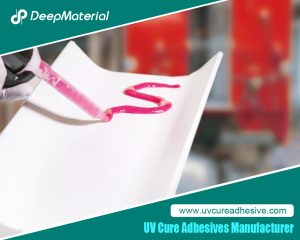
Compatibility Analysis and Countermeasures of LED UV Glue with Automated Production Equipment
Compatibility Analysis and Countermeasures of LED UV Glue with Automated Production Equipment LED UV glue has been widely used in modern manufacturing due to its advantages such as fast curing speed, high bonding strength, and environmental friendliness. However, in the automated production process, if there are problems with the adaptability between the glue and equipment
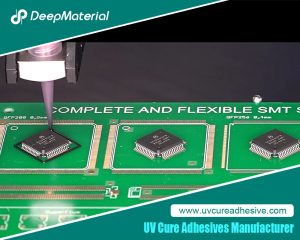
Influence of Viscosity and Thixotropy of Glue on the Quality of Glue Dots in the Dispensing Process and Solutions
Influence of Viscosity and Thixotropy of Glue on the Quality of Glue Dots in the Dispensing Process and Solutions The dispensing process is an important part of the application of LED UV glue adhesive, and the quality of this process directly affects the final performance of the product. The physical properties of the glue,