- Home
- >
- UV Cure Adhesive
- >
- UV Curable Conformal Coating
UV Curable Conformal Coating
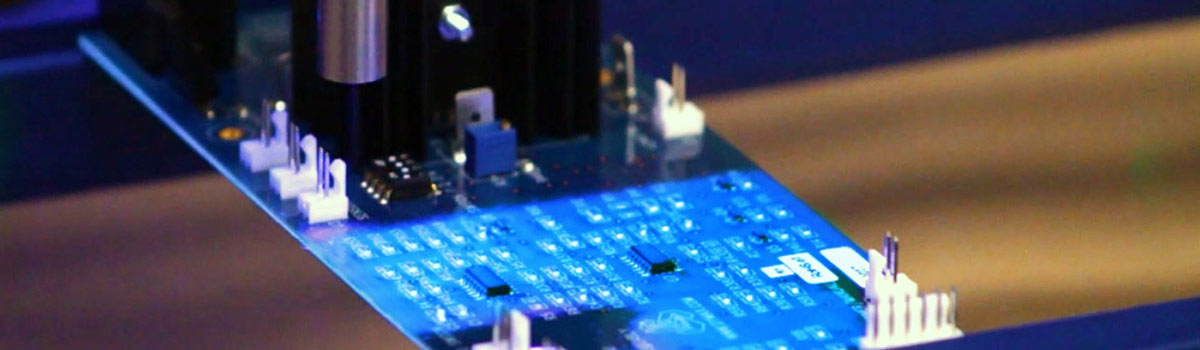
As technological demands rise, the significance of conformal coatings, particularly those curable by UV light, becomes increasingly apparent. UV-cured formulations offer rapid curing times combined with robust protective properties. This guide explores various facets of UV Curable Conformal Coating, covering its applications and advantages and addressing common queries to aid you in making informed decisions.
Table of Contents
ToggleWhat defines UV-curable conformal Coating?
UV-curable conformal coatings are protective Coatings used in electronics manufacturing to protect printed circuit boards (PCBs) and other electronic components from environmental factors such as moisture, dust, chemicals, and temperature extremes. These coatings are applied in a liquid form and then cured using ultraviolet (UV) light. The UV curing allows for rapid and efficient coating application, making it suitable for high-volume production.
Here are some key characteristics that define UV-curable conformal coatings:
- UV-Curing Process:The primary defining characteristic is using ultraviolet light for curing. The coating material contains photoinitiators that initiate a chemical reaction when exposed to UV light, transforming the liquid Coating into a solid film. This quick curing process, often taking only a few seconds, contributes to faster production cycles.
- Rapid Curing Time:UV-curable conformal coatings offer faster curing times than other conformal coatings, such as those cured through heat or air drying. This rapid curing is advantageous in high-throughput manufacturing environments.
- Low Thermal Impact:The UV curing process generates minimal heat, which is beneficial for temperature-sensitive components on the PCB. This characteristic helps prevent damage to electronic components during the coating application.
- High Chemical Resistance:UV-curable conformal coatings typically resist chemicals, including solvents and other harsh substances. This chemical resistance helps protect the PCB and electronic components from potential damage caused by exposure to corrosive environments.
- Good Adhesion:UV-curable coatings often exhibit strong adhesion to various substrates, including PCBs and mounted components. This adhesion is essential for ensuring that the Coating forms a durable protective layer.
- Excellent Electrical Insulation Properties:Conformal coatings, including UV-curable ones, are designed to provide electrical insulation. This is crucial for preventing current leakage and short circuits on the PCB.
- Optical Clarity:Some UV-curable conformal coatings are formulated to be optically transparent, allowing for visual inspection of components after coating application. This transparency is essential when inspecting LEDs, displays, or other optical components.
- UV Absorption and Blockage:UV-curable coatings are designed to absorb and block UV light after curing. This ensures that the Coating is fully cured and prevents post-cure exposure from affecting the Coating’s properties.
UV-curable conformal coatings are commonly used in industries where rapid production, precise application, and protection against environmental factors are critical considerations, such as electronics, aerospace, and automotive manufacturing.
How does UV curing distinguish itself from alternative curing methods?
UV curing is a unique method that distinguishes itself from alternative curing methods by using ultraviolet (UV) light to initiate a chemical reaction that results in the hardening or curing of materials. Here are some key aspects that set UV curing apart from alternative methods:
Speed of Cure:
- UV curing is known for its rapid curing time. The process typically takes seconds to a few minutes, making it significantly faster than many alternative curing methods.
- Traditional curing methods, such as heat or air drying, may take longer to achieve the same level of curing.
Energy Efficiency:
- UV curing is energy-efficient because the curing process is initiated by UV light, and the curing reaction occurs at ambient temperatures. This can be contrasted with heat-curing processes, often requiring elevated temperatures and consuming more energy.
Precision and Control:
- UV curing offers precise control over the curing process. The intensity and duration of UV light exposure can be carefully regulated to achieve the desired level of curing.
- This level of control is sometimes challenging to accomplish with other curing methods, especially those involving heat, where maintaining precise temperature control can be more difficult.
Low Volatile Organic Compounds (VOCs):
- UV curing typically results in lower emissions of volatile organic compounds compared to alternative curing methods, such as solvent-based curing. This makes UV curing more environmentally friendly.
Reduced Physical Distortion:
- UV curing is a “cold” process that doesn’t involve high temperatures. This is advantageous for heat-sensitive substrates or materials that deform or distort under elevated temperatures.
Versatility:
- UV curing can be applied to various materials, including inks, adhesives, coatings, and dental materials. Its versatility makes it suitable for multiple industries, such as printing, electronics, automotive, and medical.
Instantaneous Curing:
- UV curing provides nearly fast curing once the UV light is applied. This contrasts with some curing methods requiring longer waiting or drying periods.
It’s important to note that the choice of curing method depends on the specific requirements of the application and the properties of the materials being used. While UV curing offers several advantages, alternative methods may still be preferred in certain situations based on factors such as cost, equipment availability, or the nature of the materials involved.
What are the primary applications of UV-curable conformal coatings?
UV-curable conformal coatings find applications in various industries where the protection of electronic components and assemblies is essential. Conformal coatings are thin layers of material applied to the surfaces of printed circuit boards (PCBs) and electronic assemblies to protect them from environmental factors such as moisture, dust, chemicals, and temperature extremes. UV-curable conformal coatings offer unique advantages in specific applications, including:
Electronics and PCB Assembly:
- UV-curable conformal coatings are commonly used in electronics to protect PCBs from environmental stressors. The fast curing time allows for high-speed production processes, and the coatings provide excellent protection against moisture, corrosion, and other contaminants.
Medical Devices:
- Medical electronics often require protection against body fluids, chemicals, and sterilization processes. UV-curable conformal coatings can be applied to medical device assemblies to ensure the longevity and reliability of electronic components in these critical applications.
LEDs and Lighting Systems:
- UV-curable coatings are suitable for protecting LEDs and lighting systems, offering a quick and efficient curing process compatible with these devices’ production speed. The coatings help enhance the lifespan and performance of LED components.
Automotive Electronics:
- Conformal coatings are used in automotive electronics to protect sensitive electronic components from harsh environmental conditions, including temperature fluctuations, humidity, and chemical exposure. UV-curable coatings are chosen for their fast curing times and reliability.
Aerospace and Defense:
- In aerospace and defense applications, electronic components may be exposed to extreme conditions such as high altitudes, temperature variations, and vibrations. UV-curable conformal coatings provide a protective barrier against these environmental stressors.
Consumer Electronics:
- UV-curable conformal coatings are used in consumer electronic devices to protect circuits from moisture, dust, and other contaminants. The rapid curing process aligns well with the high-volume production requirements of consumer electronics.
Telecommunications:
- Electronic components in telecommunications equipment, such as routers and switches, can benefit from UV-curable conformal coatings. These coatings provide a protective layer that helps ensure the reliability and performance of the electronics.
Solar Panels and Renewable Energy Systems:
- UV-curable coatings protect electronic components in solar panels and other renewable energy systems. The coatings offer resistance to UV radiation and environmental factors, helping maintain the equipment’s efficiency and longevity.
UV-curable conformal coatings are versatile and well-suited for applications where fast curing, precise control, and reliable protection of electronic components are essential. Their use is prevalent in industries that demand high-performance and durable protection for sensitive electronic assemblies.
In what industries are UV-curable conformal coatings most beneficial?
UV-curable conformal coatings offer unique advantages in various industries due to their fast curing times, environmental benefits, and improved performance characteristics. Some of the sectors where UV-curable conformal coatings are most beneficial include:
Electronics and Electrical Components:
- UV-curable conformal coatings are widely used in electronics to protect printed circuit boards (PCBs), components, and other electronic devices. Their rapid curing time is especially advantageous in high-volume manufacturing processes.
Automotive:
- The automotive industry utilizes UV-curable conformal coatings for electronic components, sensors, and other critical parts. The coatings protect environmental factors, moisture, and chemicals while offering a quick production turnaround.
Medical Devices:
- UV-curable coatings are suitable for medical devices and equipment due to their biocompatibility and fast-curing properties. They are often used to protect electronic components in medical devices and ensure their reliability in various healthcare applications.
Aerospace:
- In aerospace, UV-curable conformal coatings protect electronic systems, sensors, and communication devices. The coatings’ ability to cure rapidly is advantageous in aerospace manufacturing processes where efficiency is critical.
LEDs and Lighting:
- UV-curable coatings protect LEDs and lighting components from environmental factors such as moisture, dust, and temperature fluctuations. The quick curing time allows for faster production cycles in the lighting industry.
Telecommunications:
- UV-curable conformal coatings find applications in the telecommunications industry to protect the electronic components of devices such as routers, switches, and communication systems. The coatings offer reliable protection while allowing for efficient manufacturing processes.
Military and Defense:
- The military and defense sectors use UV-curable conformal coatings to protect electronic components in various equipment, including communication devices, sensors, and control systems. The coatings’ quick curing time is beneficial for meeting stringent production timelines.
Consumer Electronics:
- UV-curable coatings produce consumer electronic devices, including smartphones, tablets, and wearables. The coatings protectprotect against scratches, moisture, and other environmental factors without slowing the manufacturing process.
Renewable Energy:
- UV-curable conformal coatings protect electronic components in solar panels, wind turbines, and other renewable energy systems in the renewable energy sector. The coatings enhance the durability and reliability of these components in harsh environmental conditions.
UV-curable conformal coatings balance performance, efficiency, and environmental considerations, making them versatile across various industries where the protection of electronic components is crucial.
What unique advantages characterize the use of UV-cured coatings in electronics manufacturing?
UV-cured coatings offer several unique advantages in electronics manufacturing, making them popular for various applications. Here are some of the key benefits:
Rapid Cure Time:
- UV-cured coatings cure almost instantly when exposed to ultraviolet light. This fast cure time accelerates the manufacturing process and allows for increased production speed.
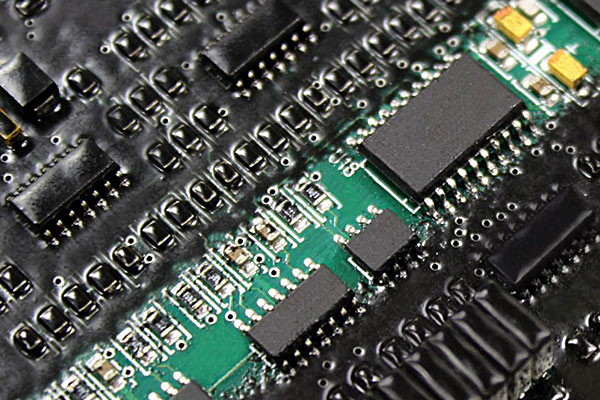
Energy Efficiency:
- UV curing does not require high temperatures, reducing energy consumption compared to traditional curing methods. This energy efficiency is beneficial both economically and environmentally.
Low Volatile Organic Compounds (VOCs):
- UV-cured coatings typically contain fewer VOCs compared to solvent-based coatings. This is crucial in electronics manufacturing, where strict environmental regulations may limit the use of certain chemicals.
Precise Application:
- UV coatings can be applied precisely, ensuring uniform coverage and consistent thickness. This is especially important in electronics manufacturing, where the coating must protect delicate components without interfering with their functionality.
Reduced Floor Space Requirements:
- UV curing systems are often compact and require less floor space than traditional ones. This is advantageous in crowded manufacturing environments where space optimization is critical.
Instantaneous Quality Control:
- The rapid cure time of UV coatings allows for immediate inspection and quality control. Manufacturers can quickly assess the coating’s integrity and adjust as needed, reducing the likelihood of defects in the final product.
No Solvent Evaporation:
- Unlike solvent-based coatings, UV-cured coatings do not rely on solvent evaporation for curing. This eliminates the risk of solvent entrapment, which can lead to defects or performance issues in electronic devices.
Improved Scratch and Abrasion Resistance:
- UV-cured coatings often exhibit enhanced durability, including better resistance to scratches and abrasion. This is crucial in electronic applications where devices may be subjected to wear and tear during use.
Compatibility with Heat-Sensitive Substrates:
- UV curing is a low-temperature process, making it suitable for heat-sensitive substrates commonly found in electronics manufacturing. This allows for applying coatings without risking damage to the electronic components.
Customization and Special Effects:
- UV coatings can be formulated to achieve various finishes, textures, and effects, allowing manufacturers to create visually appealing and functional electronic products.
While UV-cured coatings offer numerous advantages, it’s important to note that their effectiveness depends on factors such as substrate material, coating formulation, and the specific requirements of the electronic components being coated. Manufacturers should consider these factors when choosing a coating method for their applications.
Can UV-curable conformal coatings be applied across diverse substrates?
UV-curable conformal coatings can be applied across diverse substrates to a certain extent, but the compatibility depends on several factors. Here are some considerations:
Substrate Material:
- UV-curable conformal coatings are generally compatible with various substrates, including plastics, glass, ceramics, and metals. However, the specific formulation of the coating may need to be adjusted based on the characteristics of the substrate.
Surface Energy:
- The surface energy of the substrate can impact the adhesion of the UV-curable conformal coating. Some substrates may require pre-treatment or adhesion promoters to enhance the coating’s adhesion.
Coefficient of Thermal Expansion (CTE):
- Matching the coefficient of thermal expansion between the conformal coating and the substrate is essential to prevent cracking or delamination, especially in environments with temperature variations.
Flexibility:
- Different substrates have varying levels of flexibility. UV-curable conformal coatings should be selected or formulated to accommodate the flexibility of the substrate without cracking or losing adhesion over time.
Chemical Compatibility:
- Consider the chemical resistance of the conformal coating to the substances the electronic device may encounter. Some substrates may be sensitive to certain chemicals in the coating, and compatibility testing is essential.
UV Penetration:
- The ability of UV light to penetrate the substrate is a crucial factor. Some substrates may be opaque or absorb UV light, making it challenging for the coating to cure effectively. In such cases, modifications to the coating formulation or curing process may be necessary.
Adhesion Promoters and Primers:
- When adhesion between the UV-curable conformal coating and the substrate is insufficient, adhesion promoters or primers specific to the substrate may enhance bonding.
Application Method:
- Applying the UV-curable conformal coating can also affect its compatibility with diverse substrates. Spraying, dipping, or selective coating methods may be chosen based on the substrate and the requirements of the electronic components.
Environmental Conditions:
- Consider the environmental conditions to which the coated electronic devices will be exposed. UV-curable conformal coatings should protect against moisture, chemicals, and other ecological factors relevant to the application.
Before applying UV-curable conformal coatings across diverse substrates, it is advisable to conduct thorough compatibility testing. This involves using the coating to sample substrates, curing them, and evaluating factors such as adhesion, flexibility, and chemical resistance. This testing helps ensure that the conformal coating meets the specific requirements of the electronics being protected and extends the longevity of the components.
What factors influence the curing time of UV conformal coatings, and how can they be optimized?
The curing time of UV (Ultraviolet) conformal coatings, which are often used in electronic and other industries to protect and insulate components, can be influenced by various factors. Optimizing the curing process is crucial to ensure proper coating performance. Here are some factors that can influence UV conformal coating curing time and ways to optimize them:
UV Light Intensity:
- Factor:The intensity of the UV light source is a critical factor. Higher-intensity UV light typically results in faster curing.
- Optimization:Ensure the UV light source is calibrated and operating at the recommended intensity. Regularly check and maintain the UV lamps to ensure consistent performance.
Wavelength of UV Light:
- Factor:The wavelength of UV light affects the curing process. Different formulations of conformal coatings may require specific UV wavelengths for optimal curing.
- Optimization:Use UV lamps with the appropriate wavelength recommended by the conformal coating manufacturer.
Coating Thickness:
- Factor:Thicker coatings may require more time to cure completely.
- Optimization:Apply coatings within the recommended thickness range specified by the manufacturer. Consider multiple thinner layers if necessary, allowing each layer to cure before applying the next.
Type of Substrate:
- Factor:Different substrates may absorb or reflect UV light differently, impacting curing.
- Optimization:Choose conformal coatings that are suitable for the specific substrate. Test and adjust curing parameters based on the substrate material.
Ambient Temperature:
- Factor:Curing time can be influenced by the ambient temperature. Higher temperatures generally accelerate the curing process.
- Optimization:Control the ambient temperature within the recommended range during curing. Avoid extreme temperatures that may affect the coating quality.
Chemical Formulation of the Coating:
- Factor:The chemical composition of the conformal coating influences its curing characteristics.
- Optimization:Follow the manufacturer’s guidelines for the specific conformal coating. Ensure the coating is mixed correctly and stored according to recommendations.
Presence of Oxygen:
- Factor:The presence of oxygen can inhibit the curing of certain UV coatings.
- Optimization:Consider using formulations less sensitive to oxygen inhibition or implement inert gas environments if applicable.
Post-Cure Processes:
- Factor:Some coatings may benefit from post-cure processes, such as additional exposure to heat.
- Optimization:Follow any post-cure recommendations the coating manufacturer provides to ensure complete and thorough curing.
Optimizing the curing time of UV conformal coatings involves a combination of proper equipment calibration, adherence to recommended application parameters, and understanding the specific characteristics of the coating material being used. Always refer to the manufacturer’s guidelines and conduct thorough testing to ensure the desired performance of the conformal coating.
Are there notable environmental considerations tied to UV-curable coatings?
UV-curable coatings have gained popularity in various industries due to their fast curing times, low VOC (volatile organic compounds) emissions, and other advantages. However, like any technology, UV-curable coatings also have environmental considerations. Here are some notable points:
- Energy Consumption:UV-curable coatings require UV light for curing. The energy consumption associated with UV curing systems can be a concern, especially if the energy source is not renewable. Considering the overall environmental impact of the energy used in the curing process is essential.
- Raw Materials and Chemicals:The materials used in UV-curable coatings, including monomers and oligomers, may have environmental implications. Some of these materials may be derived from petrochemicals or have other ecological considerations. Manufacturers are increasingly exploring bio-based and renewable sources for these raw materials to reduce environmental impact.
- Waste Disposal:UV-cured coatings typically generate less waste than traditional solvent-based coatings. However, the disposal of waste containing cured materials, such as scrap pieces or rejected products, should be managed carefully to minimize environmental impact. Additionally, the disposal of UV lamps and other equipment at the end of their life cycle requires proper consideration to prevent environmental contamination.
- Toxic Emissions:UV-curable coatings generally have lower VOC emissions than solvent-based coatings, but they may still release certain volatile compounds during curing. Understanding and managing potential emissions is crucial to ensure compliance with environmental regulations and minimize the impact on air quality.
- Health and Safety:Using UV light in the curing process raises health and safety considerations for workers. Exposure to UV light can have adverse effects on the skin and eyes. Adequate safety measures, such as proper protective equipment and controlled exposure, should be implemented to protect workers.
- Regulatory Compliance:Environmental regulations and standards regarding using certain chemicals, emissions, and waste disposal vary by region. It’s essential for manufacturers using UV-curable coatings to stay informed about and comply with relevant environmental regulations.
- Life Cycle Analysis:A comprehensive life cycle analysis (LCA) can provide insights into the overall environmental impact of UV-curable coatings, taking into account raw material extraction, manufacturing processes, product use, and disposal. LCAs help identify areas for improvement in terms of environmental performance.
As technology advances, the industry continues to explore ways to mitigate environmental concerns associated with UV-curable coatings. This may involve the development of more sustainable raw materials, energy-efficient curing processes, and improved waste management practices.
How does UV curing impact the overall durability and reliability of conformal coatings?
UV (ultraviolet) curing is commonly used in applying conformal coatings in electronics manufacturing. Conformal coatings are protective layers applied to printed circuit boards (PCBs) and electronic components to safeguard them from environmental factors such as moisture, chemicals, dust, and temperature extremes. UV curing is a specific method of drying or curing these coatings, and it can impact the overall durability and reliability of conformal coatings in several ways:
- Faster Curing Time:UV curing is known for its rapid curing time. Compared to traditional methods like thermal curing, UV can significantly reduce the time required to cure the conformal coating. The faster curing time can enhance manufacturing efficiency and throughput.
- Uniform Coating Thickness:UV curing provides better control over the curing process, resulting in a more uniform coating thickness. This uniformity ensures the conformal coating provides consistent protection across the entire PCB or electronic assembly.
- Improved Adhesion:UV-cured conformal coatings often exhibit better adhesion to the substrate. Improved adhesion contributes to a more robust protective barrier against environmental stressors and mechanical damage.
- Reduced Thermal Stress:UV curing typically involves lower temperatures than thermal curing. This reduced thermal stress on the electronic components and substrates is particularly beneficial for sensitive components and materials that may be adversely affected by high temperatures.
- Enhanced Chemical Resistance:UV-cured conformal coatings can improve resistance to certain chemicals and solvents. This property is vital for protecting electronic assemblies in environments where exposure to corrosive substances is a concern.
- Lower Energy Consumption:UV curing requires less energy than thermal curing methods, contributing to overall energy efficiency in manufacturing.
- Optical Clarity:UV-cured coatings can maintain optical clarity, which is crucial when visual inspection of components is necessary. This feature is essential for applications where transparency or clarity is required.
- Consistency in Performance:The controlled nature of UV curing helps achieve consistent coating properties from batch to batch, ensuring that conformal coatings exhibit reliable performance characteristics.
While UV curing offers several advantages, it’s important to note that selecting the suitable conformal coating and curing method depends on the application’s specific requirements. Factors such as the type of electronic components, operating environment, and manufacturing processes should be considered when determining the most suitable conformal coating and curing method to achieve optimal durability and reliability.
What challenges or limitations might one encounter with UV-curable conformal coatings?
UV-curable conformal coatings offer several advantages, such as rapid curing, reduced processing time, and excellent chemical resistance. However, they also come with their set of challenges and limitations. Here are some factors to consider:
Substrate Compatibility:
- UV-curable conformal coatings may not be compatible with all substrates. Some materials may not allow proper adhesion or undergo undesired reactions with the coating, leading to poor performance or adhesion failure.
Shadowing Effects:
- UV light must reach the entire surface to ensure complete curing. Components with complex geometries or shadowed areas may need more UV exposure, resulting in incomplete curing and reduced coating performance.
Thickness Control:
- Achieving uniform coating thickness can be challenging, especially on complex or three-dimensional surfaces. Inconsistent coating thickness may impact the coating’s protective properties.
Curing Depth:
- The depth to which the UV light can penetrate and cure the coating is limited. Ensuring complete curing throughout the entire thickness can be challenging for thicker coatings or densely populated electronic assemblies.
Moisture Sensitivity:
- UV-curable coatings can be sensitive to moisture. If moisture is present on the substrate or in the environment during the application or curing process, it can affect the coating’s performance and adhesion.
Temperature Sensitivity:
- The curing process of UV coatings may be affected by temperature variations. Extreme temperatures can either slow down or speed up the curing process, impacting the coating’s final properties.
UV Light Absorption:
- Some materials or pigments may absorb UV light, reducing its effectiveness in curing the coating. This can result in uneven curing and compromised performance.
Cost of Equipment:
- The equipment required for UV curing can be expensive. UV lamps and curing systems must be appropriately designed and maintained to ensure consistent and effective curing.
Health and Safety Concerns:
- UV-curable coatings involve UV light, which can pose health risks to operators. Proper safety measures, including protective equipment, are essential to mitigate these risks.
Limited Pot Life:
- Once mixed or exposed to UV light, the pot life of UV-curable coatings can be limited. This means that once the coating is prepared, it must be applied and cured within a specific timeframe to ensure optimal performance.
Despite these challenges, UV-curable conformal coatings are widely used in many industries for their numerous benefits. Addressing these limitations often involves careful selection of materials, process optimization, and adherence to best practices in application and curing.
Do different formulations exist for UV-curable conformal coatings, and how do they vary?
Yes, various formulations of UV-curable conformal coatings exist, and they can vary based on several factors, including the specific application requirements and the desired properties of the coating. Some critical variations in formulations include:
Chemical Composition:
- UV-curable conformal coatings can be based on chemical compositions, such as acrylates, epoxies, urethanes, or silicones. The choice of base material influences properties such as flexibility, hardness, and chemical resistance.
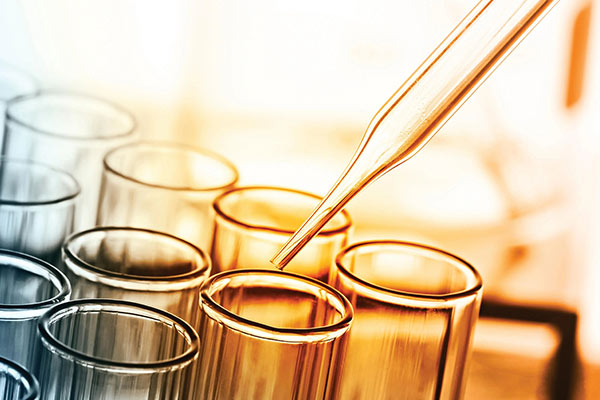
Monomer Type:
- For example, different monomers, such as monofunctional, difunctional, or multifunctional acrylates, may be used within acrylate-based coatings. The type of monomer affects the crosslinking density and, consequently, the coating’s mechanical and chemical properties.
Oligomers:
- UV-curable coatings often include oligomers and prepolymers with a relatively low molecular weight. The selection of oligomers can impact the coating’s flexibility, adhesion, and overall performance.
Photoinitiators:
- Photoinitiators are crucial components that initiate the curing process when exposed to UV light. Different formulations may use various photoinitiators, and their selection can influence curing speed, depth, and overall efficiency.
Fillers and Additives:
- Formulations may include fillers and additives to enhance specific properties. For example, adding nanoparticles or other fillers can improve mechanical strength, thermal conductivity, or barrier properties.
Reactivity:
- UV-curable coatings can be formulated to have different reactivity levels. Some coatings cure rapidly under low-intensity UV light, while others may require higher-intensity light sources or longer exposure times.
Curing Conditions:
- Formulations can be tailored for specific conditions, such as ambient or low-temperature curing. This flexibility allows for customization based on the requirements of the application process and the materials being coated.
Optical Clarity:
- Some applications, particularly those involving optical devices or displays, may require coatings with high optical clarity. Formulations can be adjusted to minimize the impact on light transmission and maintain visual clarity.
Adhesion Promoters:
- Formulations may include adhesion promoters or coupling agents that enhance the bonding between the coating and the substrate to ensure strong adhesion to various substrates.
Specialized Properties:
- Formulations can be developed for specific applications, such as coatings for flexible electronics, high-temperature environments, or chemical-resistant coatings. These formulations are designed to meet the unique challenges posed by these applications.
It’s important to note that the choice of formulation depends on the application’s specific needs, and coatings are often customized to achieve the desired balance of properties. Manufacturers may offer a range of formulations to accommodate diverse industries and applications. Additionally, ongoing research and development in the field continue to introduce new formulations with improved performance characteristics.
How does the viscosity of UV-curable coatings affect the application process?
The viscosity of UV-curable coatings plays a crucial role in the application process, influencing various aspects such as coating uniformity, flow characteristics, and overall performance. Viscosity refers to a liquid’s resistance to flow, typically measured in units such as centipoise (cP). Here’s how viscosity affects the application of UV-curable coatings:
Flow and Leveling:
- Low-viscosity coatings tend to flow more efficiently, resulting in a smoother and more level surface. This is beneficial for achieving an even coating thickness, reducing the likelihood of streaks or uneven coverage.
- Higher viscosity coatings may have reduced flow, leading to a thicker application in certain areas and potentially causing uneven surfaces.
Spraying and Atomization:
- Low-viscosity UV coatings are often preferred for spray applications. They can be atomized more efficiently, allowing finer droplets and a more even distribution on the substrate.
- Higher-viscosity coatings may require more pressure and be challenging to atomize correctly, leading to overspray or uneven coating distribution.
Substrate Wetting:
- The viscosity of the coating affects its ability to wet the substrate. Low-viscosity coatings tend to wet surfaces more readily, ensuring good adhesion and coverage.
- High-viscosity coatings may have reduced wetting properties, which can result in poor adhesion and inadequate coverage.
Curing Depth and Penetration:
- Viscosity influences the penetration of UV light into the coating. Lower viscosity coatings may allow for better light penetration, leading to more effective curing throughout the thickness of the coating.
- Higher viscosity coatings may limit the depth of cure as they may block UV light from reaching the underlying layers, potentially leading to incomplete curing.
Application Methods:
- Different application methods, such as dipping, brushing, or roller coating, may be influenced by the viscosity of the UV-curable coating. The coating’s viscosity should be compatible with the chosen application method to ensure proper coating performance.
Controlled Thickness:
- Viscosity affects the ability to control coating thickness. Controlling viscosity is crucial to achieving the desired film thickness, especially in applications with a critical coating thickness.
It’s important to note that the optimal viscosity depends on various factors, including the application method, substrate, curing equipment, and specific coating process requirements. Manufacturers of UV-curable coatings often provide guidelines and recommendations for viscosity levels to achieve optimal performance during application and curing. Adjusting viscosity as needed can help ensure the successful application of UV-curable coatings for different substrates and application methods.
Is reworking or removing UV-curable coatings feasible, and what does it entail?
Reworking or removing UV-curable coatings is feasible, but the process can be more challenging than traditional coatings due to the unique properties of UV-curable materials. UV-curable coatings cure or harden when exposed to ultraviolet (UV) light, making them durable and chemical-resistant. Here are some general considerations and methods for reworking or removing UV-curable coatings:
Considerations:
Type of UV-Curable Coating:
- Different UV-curable coatings may have different formulations, so the method of rework/removal may vary depending on the coating used.
Substrate Compatibility:
- Ensure that the substrate (the material the coating is applied to) can withstand the removal process without damage.
Safety Precautions:
- UV-curable coatings may contain chemicals that require proper handling and disposal. Follow safety guidelines and use appropriate personal protective equipment.
Methods for Reworking/Removing UV-Curable Coatings:
Mechanical Methods:
- Abrasion:Abrasive methods such as sanding or blasting can remove the coating mechanically. This method is effective for thicker coatings.
- Scraping:Using tools to scrape off the cured coating from the substrate.
Chemical Methods:
- Chemical Strippers:Specialized chemical strippers designed for UV-curable coatings can be applied to soften or break down the coating, making it easier to remove. However, compatibility with the substrate must be considered.
- Solvent-Based Removers:Some solvents may help soften the cured coating, making removing it easier. Test the solvent on a small, inconspicuous area first to ensure compatibility.
Thermal Methods:
- Heat:Applying heat can soften the coating, making it easier to peel or scrape off. However, excessive heat may damage the substrate, so control is crucial.
UV Exposure:
- Re-exposure to UV Light:In some cases, reapplying UV light to the cured coating may partially reverse the curing process, allowing for easier removal.
Combination Methods:
- Combining Methods:Depending on the specific coating and substrate, mechanical, chemical, and thermal methods may be effective.
Important Notes:
- Test in a Small Area:Before attempting large-scale rework or removal, test the chosen method in a small, inconspicuous area to ensure it doesn’t damage the substrate.
- Professional Assistance:In complex or critical situations, it may be advisable to seek assistance from professionals or the manufacturer of the UV-curable coating for guidance.
Refer to the product datasheet or consult the coating manufacturer for specific recommendations on reworking or removing their UV-curable coatings.
Are there specific guidelines for the proper application of UV-curable conformal coatings?
Yes, the application of UV-curable conformal coatings requires careful consideration and adherence to specific guidelines to ensure optimal performance and reliability. While the exact procedures can vary based on the specific coating product and manufacturer recommendations, here are some general guidelines for the proper application of UV-curable conformal coatings:
- Surface Preparation:
- Ensure that the substrate is clean, dry, and free of contaminants, such as dust, oils, and residues.
- Consider using a cleaning agent compatible with the coating material to achieve proper adhesion.
- Application Equipment:
- Use equipment designed for UV-curable coatings, including dispensing systems and curing equipment.
- Ensure that all application equipment is properly calibrated and maintained.
- Coating Thickness:
- Follow the manufacturer’s recommendations regarding the recommended coating thickness for optimal performance.
- Uniformly apply the coating to achieve consistent thickness across the substrate.
- Curing Conditions:
- Utilize the appropriate UV light source for curing, considering factors such as wavelength and intensity specified by the coating manufacturer.
- Ensure that the UV curing equipment is in good working condition and properly calibrated.
- Curing Time:
- Adhere to the recommended curing time provided by the coating manufacturer.
- Monitor the curing process to ensure that the coating is adequately cured throughout its thickness.
- Handling and Storage:
- Follow guidelines for proper handling and storage of UV-curable conformal coatings to maintain their stability and performance.
- Store coatings in a cool, dry place away from direct sunlight.
- Safety Precautions:
- Wear appropriate personal protective equipment (PPE), including gloves and safety glasses, when handling UV-curable coatings.
- Follow safety guidelines provided by the coating manufacturer.
- Testing and Quality Control:
- Conduct adhesion tests and other relevant quality control measures to ensure the coating’s performance meets the required standards.
- Monitor and document the application process for consistency and traceability.
- Environmental Considerations:
- Consider the environmental conditions during application, such as temperature and humidity, as they can affect the coating process.
Always refer to the specific technical data sheets and application guidelines provided by the manufacturer of the UV-curable conformal coating you are using. These guidelines will provide detailed instructions tailored to the particular characteristics of the coating product.
In terms of cost, how do UV-curable conformal coatings compare to traditional alternatives?
However, consider that costs vary based on specific product formulations, suppliers, and regional market conditions. Here are some aspects to consider:
*Material Cost:UV-curable coatings often involve specialized materials, including photoinitiators and monomers that react to UV light. These materials can be more expensive than those used in traditional coatings.
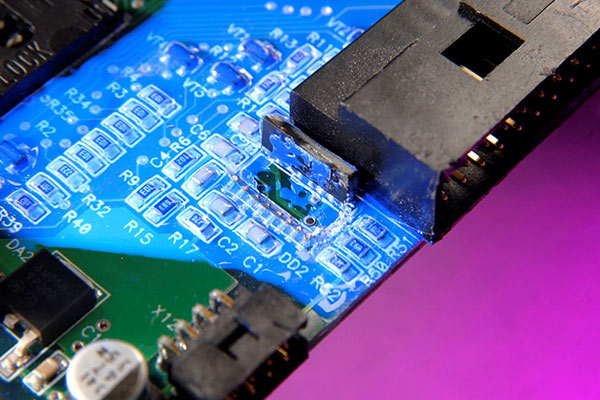
*Equipment Costs:UV-curable coatings require UV curing equipment, which can be a significant upfront investment. Conventional coatings may not require such specialized curing processes.
*Energy Consumption:UV-curable coatings generally require less energy for curing than heat-cured or air-dried coatings, which can result in lower operational costs. However, the initial investment in UV curing equipment needs to be considered.
*Application Efficiency:UV-curable coatings can offer faster curing times, potentially leading to increased production efficiency and reduced labor costs. However, this advantage may vary depending on the application and curing requirements.
*Environmental and Health Considerations:Traditional coatings may involve solvents and other chemicals with potential health and environmental concerns. UV-curable coatings are often considered more environmentally friendly due to lower solvent content.
*Customization and Specialization:Depending on your specific requirements, UV-curable coatings might offer unique properties that can justify their higher cost. For instance, they may provide better adhesion, chemical resistance, or thermal stability for specific applications.
It’s essential to consult with suppliers, consider your specific application needs, and evaluate the total cost of ownership over time.
What considerations should be taken into account when selecting a UV curing system?
Selecting a UV curing system involves several considerations to ensure that it meets your application’s specific needs and requirements. Here are vital factors to take into account:
Type of UV Curing System:
- Mercury Vapor Lamps:Traditional UV curing systems often use mercury vapor lamps. Consider if this type is suitable for your application.
- LED UV Systems:LED UV curing is gaining popularity due to its energy efficiency, longer lifespan, and targeted wavelength options. Assess whether LED technology is compatible with your curing requirements.
Wavelength:
- Choose the appropriate UV wavelength for your specific curing needs. Different materials and UV-sensitive substances respond to different wavelengths, so ensure compatibility with your application.
Intensity and Power Output:
- Consider the intensity and power output of the UV system, as they directly impact the curing speed and effectiveness. The intensity should match the requirements of your application.
Substrate Compatibility:
- Verify that the UV curing system is compatible with the materials and substrates used in your application. Some materials may require specific wavelengths or curing profiles.
Curing Area Size:
- Determine the size of the curing area needed for your application. Ensure the UV system can cover the entire area uniformly for consistent curing results.
Cooling System:
- UV curing systems generate heat, and proper cooling is essential for maintaining system efficiency and preventing overheating. Evaluate the cooling mechanism of the system.
Control and Monitoring Features:
- Look for UV systems with advanced control and monitoring features. This may include adjustable intensity, real-time monitoring, and programmable curing profiles for different materials.
Safety Features:
- Ensure the UV curing system has adequate safety features, such as interlocks, shielding, and alarms, to protect operators from UV exposure and prevent accidents.
Energy Efficiency:
- Consider the energy efficiency of the UV curing system, mainly if it will be used continuously. LED UV systems are generally more energy-efficient than traditional mercury vapor lamps.
Ease of Maintenance:
- Assess the ease of maintenance and availability of replacement parts. A system with easy access for lamp replacement and routine maintenance can minimize downtime.
Cost Considerations:
- Compare the initial, operating, and long-term costs of different UV curing systems. Factor in energy consumption, lamp life, and maintenance expenses.
Environmental Considerations:
- Consider environmental factors such as ozone emissions (standard mercury vapor lamps) and the overall environmental impact of the system.
Application-Specific Requirements:
- Identify any specific requirements unique to your application, such as curing speed, temperature sensitivity, or special conditions, and ensure the selected UV system can meet these needs.
By carefully considering these factors, you can choose a UV curing system that aligns with your application’s requirements and ensures efficient and reliable curing processes.
What safety precautions should one follow when working with UV curing processes?
Working with UV (ultraviolet) curing processes involves exposure to ultraviolet light, posing potential health and safety risks. Here are some safety precautions to follow when working with UV curing processes:
Protective Clothing and Equipment:
- Wear appropriate personal protective equipment (PPE) such as UV-blocking safety glasses, face shields, and gloves.
- Use UV-resistant clothing to cover exposed skin.
Ventilation:
- Ensure good ventilation in the working area to minimize the buildup of fumes and prevent overexposure.
Eye Protection:
- UV light can be harmful to the eyes. Always wear UV-blocking safety glasses that provide sufficient protection for the specific wavelengths used in the curing process.
Skin Protection:
- UV exposure can cause skin damage. Wear protective clothing that covers as much skin as possible, including long sleeves and pants.
Training:
- Ensure all personnel working with UV curing processes are adequately trained on the potential hazards, safe handling procedures, and emergency protocols.
Emergency Procedures:
- Establish and communicate emergency procedures in case of accidental exposure or other incidents. This may include eye-flushing stations and emergency exits.
UV Light Monitoring:
- Regularly monitor UV light intensity using appropriate equipment to ensure exposure levels are within safe limits.
Workspace Design:
- Design the workspace to minimize direct exposure to UV light. Consider using barriers or enclosures to contain the UV light within the curing area.
Hazard Assessment:
- Conduct a thorough hazard assessment to identify and mitigate potential risks associated with UV curing processes.
Timer Systems:
- Implement timer systems or other controls to limit the duration of UV exposure. This helps prevent overexposure during extended working periods.
Regular Maintenance:
- Ensure UV curing equipment is regularly inspected and properly maintained to avoid malfunctions that could lead to increased risk.
UV Curing Chamber:
- If using a UV curing chamber, ensure it is properly enclosed and access is restricted during operation.
Chemical Exposure:
- Be aware of any chemicals used with the UV curing process, and follow safety guidelines for those chemicals.
Pregnancy Considerations:
- Pregnant individuals should exercise extra caution and consult with a healthcare professional, as there may be potential risks to the developing fetus.
Always consult the manufacturer’s guidelines and safety data sheets for specific materials and equipment used in your UV curing process. Following these precautions helps to minimize the risks associated with UV exposure and ensures a safer working environment.
Have there been recent advancements or innovations in UV-curable conformal coating technology?
In general, the field of conformal coatings is dynamic, with ongoing research and development aimed at improving performance, efficiency, and environmental impact. Innovations involve enhancements in formulation, curing processes, application methods, and developing coatings with new or improved properties.
To stay informed about recent advancements, consider looking into industry journals, attending conferences or trade shows related to electronics manufacturing or materials science, and contacting suppliers or manufacturers specializing in conformal coatings. Additionally, industry associations and online forums can be valuable resources for staying updated on the latest UV-curable conformal coating technology developments.
Can UV-curable coatings contribute to the aesthetic appeal of electronic assemblies?
Yes, UV-curable coatings can contribute to the aesthetic appeal of electronic assemblies. UV-curable coatings offer several benefits that can enhance the visual appearance of electronic components and devices. Some ways in which UV-curable coatings contribute to aesthetics include:
- Clarity and Transparency:UV-curable coatings can be formulated as clear and transparent. This is particularly beneficial when applied to surfaces with intricate designs, labels, or graphics, as the underlying features can remain visible. This is important for products where aesthetics are a vital consideration.
- High Gloss and Matte Finishes:UV-curable coatings can be designed to produce various finishes, including high gloss or matte. This flexibility allows manufacturers to choose coatings that match the desired aesthetic for their products. High gloss finishes, for example, can give a sleek and polished appearance, while matte finishes may provide a more subdued and sophisticated look.
- Color Matching:UV-curable coatings can be formulated in various colors, allowing for precise color matching to meet design requirements. This is especially important for electronic devices where color coordination is critical to aesthetic design.
- Consistency and Uniformity:UV curing is a rapid process, allowing for the application of coatings in a controlled and consistent manner. This helps achieve uniform coverage, crucial for maintaining a professional and aesthetically pleasing appearance.
- Durability and Resistance:UV-curable coatings can provide durable protection against environmental factors, ensuring that the appearance of electronic assemblies remains intact over time. This resistance to wear, chemicals, and other stressors contributes to the long-term aesthetic appeal of the coated surfaces.
- Customization:UV-curable coatings offer a high degree of customization in formulation and application methods. Manufacturers can work with coating suppliers to tailor coatings to meet specific aesthetic and functional requirements.
UV-curable coatings provide functional benefits in terms of protection and contribute significantly to the aesthetic qualities of electronic assemblies. Manufacturers often leverage these coatings to achieve visual appeal and robust product protection.
What is the future outlook for UV-curable conformal coatings within the electronics industry?
UV-curable conformal coatings have been gaining popularity in the electronics industry due to their numerous advantages, such as rapid curing, reduced energy consumption, and enhanced performance. However, specific details about the current market and future outlook may have evolved since then. Here are some general trends and considerations that were relevant up to my last update:
- Growing Demand for Electronics:The increasing demand for electronic devices in various industries, including consumer electronics, automotive, and healthcare, contributes to the demand for advanced protection measures like conformal coatings.
- Performance Advantages:UV-curable conformal coatings offer quick curing times, improved chemical resistance, and better overall performance than traditional coatings. As the electronics industry advances, the need for higher-performance materials will likely persist.
- Miniaturization and Increased Complexity:With the trend toward smaller and more complex electronic components, there is a need for conformal coatings that can provide reliable protection without adding bulk. UV-curable coatings can be applied in thin layers, making them suitable for protecting delicate and intricate electronic assemblies.
- Environmental Regulations:There is a growing emphasis on environmentally friendly and low-VOC (volatile organic compound) solutions. UV-curable coatings are often considered more environmentally friendly than some solvent-based alternatives, which can contribute to their continued adoption.
- Innovation in Formulations:Ongoing research and development efforts in material science may lead to the formulation of new UV-curable coatings with enhanced properties, addressing specific challenges in the electronics industry, such as thermal management and flexibility.
- Adoption Challenges:While UV-curable coatings offer numerous benefits, there may be challenges related to equipment costs, process optimization, and the need for specialized expertise. Overcoming these challenges and streamlining the adoption process could influence the future outlook.
- Global Economic Factors:Economic conditions and global market trends can also impact the adoption of new technologies. Changes in manufacturing trends, trade policies, and other economic factors may influence the growth of UV-curable conformal coatings in the electronics industry.
To get the most accurate and up-to-date information on the future outlook for UV-curable conformal coatings in the electronics industry, it is advisable to consult recent market reports, industry publications, and experts in the field.
Conclusion:
In summary, UV Curable Conformal Coatings stand at the forefront of electronics manufacturing, offering swift curing times and formidable protective capabilities. This guide aims to illuminate the intricate details of UV-cured formulations, equipping you with knowledge to navigate the evolving landscape of conformal coatings. Should you have further inquiries or require assistance, don’t hesitate to contact our experts.
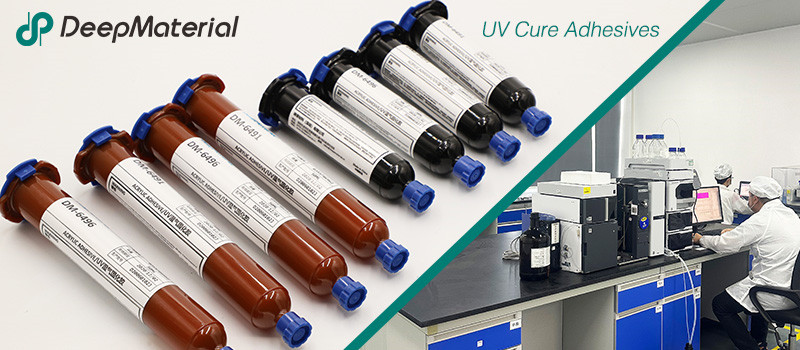
DeepMaterial
Based on the core technology of adhesives, DeepMaterial has developed adhesives for chip packaging and testing, circuit board level adhesives, and adhesives for electronic products. Based on adhesives, it has developed protective films, semiconductor fillers, and packaging materials for semiconductor wafer processing and chip packaging and testing. More…
UV Curing Adhesives
UV light cure have a number of benefits making them a popular choice among many product assembly and manufacturing applications. Many UV light cure adhesives can provide a nearly instantaneous bond to difficult substrates like glass and plastic. UV cure adhesives often require an accelerator or UV light for a bond to form.
Adhesive Blogs & News
The latest adhesive industry science and technology, Deepmaterial news, and market trends and forecasts.
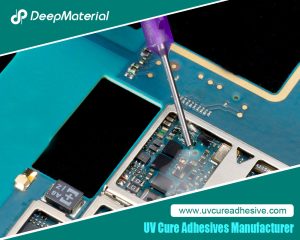
Technical Strategies for Balancing the Rapid Curing Property and Long Operating Time of UV Adhesives
Technical Strategies for Balancing the Rapid Curing Property and Long Operating Time of UV Adhesives UV adhesives have been widely used in many fields such as electronics, optics, and medicine due to their advantages of rapid curing, high bonding strength, and environmental protection. However, their rapid curing property also brings challenges in some application scenarios.
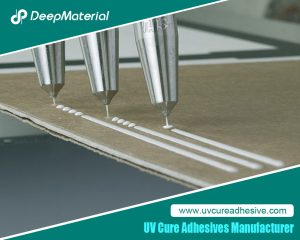
Biocompatibility of LED UV Glue Adhesive and Its Application Potential in Medical and Food Packaging Fields
Biocompatibility of LED UV Glue Adhesive and Its Application Potential in Medical and Food Packaging Fields LED UV glue adhesive has been widely applied in numerous fields due to its advantages such as rapid curing and easy operation. However, in fields with stringent safety requirements like medical and food packaging, its biocompatibility after curing
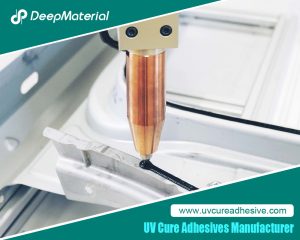
Exploring the Environmental Performance of UV Glue and Strategies for Optimizing Odor and VOC Content
Exploring the Environmental Performance of UV Glue and Strategies for Optimizing Odor and VOC Content UV glue, as an adhesive that achieves rapid curing through ultraviolet (UV) light irradiation, has been widely applied in numerous fields such as electronics, optics, healthcare, and automobiles, thanks to its advantages of fast curing speed, high bonding strength, and
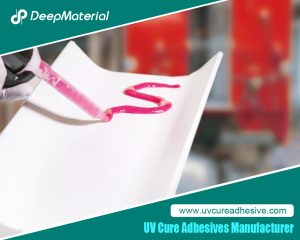
Compatibility Analysis and Countermeasures of LED UV Glue with Automated Production Equipment
Compatibility Analysis and Countermeasures of LED UV Glue with Automated Production Equipment LED UV glue has been widely used in modern manufacturing due to its advantages such as fast curing speed, high bonding strength, and environmental friendliness. However, in the automated production process, if there are problems with the adaptability between the glue and equipment
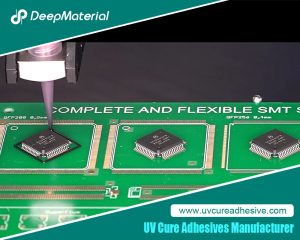
Influence of Viscosity and Thixotropy of Glue on the Quality of Glue Dots in the Dispensing Process and Solutions
Influence of Viscosity and Thixotropy of Glue on the Quality of Glue Dots in the Dispensing Process and Solutions The dispensing process is an important part of the application of LED UV glue adhesive, and the quality of this process directly affects the final performance of the product. The physical properties of the glue,
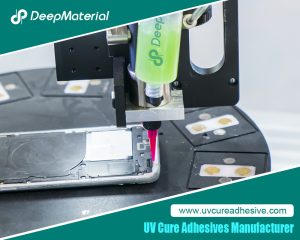
Aging Mechanism and Modification Strategies of LED UV Glue under Long-term Ultraviolet Irradiation
Aging Mechanism and Modification Strategies of LED UV Glue under Long-term Ultraviolet Irradiation LED UV glue, with its advantages of fast curing speed, high bonding strength, and environmental friendliness, has been widely used in fields such as optical device packaging, electronic assembly, and medical devices. However, in scenarios where it is exposed to ultraviolet environments