The Quantitative Influence of Crosslinking Density on the Flexibility and Hardness of Adhesives and the Formulation Optimization Strategy
This article systematically expounds the quantitative relationship between the crosslinking density and the flexibility and hardness of adhesives. Combining the theories of polymer physics with experimental analysis methods, it reveals the mechanism of the action of the crosslinked network structure on the mechanical properties of materials. Through technical means such as rheological testing and dynamic mechanical analysis (DMA), a mathematical model of the crosslinking density and the performance parameters of adhesives is established, and a formulation optimization strategy for different application scenarios is proposed, providing theoretical guidance and practical basis for the development of high-performance adhesives.
Basic Concepts and Characterization Methods of Crosslinking Density
1. Definition of Crosslinking Density
The crosslinking density refers to the number of crosslinking points per unit volume in a polymer material, usually expressed as moles of crosslinking points per unit volume (mol/m³) or the density of crosslinking bonds. It determines the topological structure of the polymer network and directly affects the physical and chemical properties of the material. In the adhesive system, the regulation of the crosslinking density is the core element for balancing its flexibility and hardness.
2. Characterization Methods of Crosslinking Density
- Swelling Method: Based on the Flory-Rehner equation, the crosslinking density is calculated by measuring the volume change before and after swelling. This method is suitable for the qualitative analysis of crosslinked polymers, but it is greatly affected by the choice of solvent and temperature.
- Dynamic Mechanical Analysis (DMA): By measuring the changes in the storage modulus (E’) and loss modulus (E”) with temperature, the crosslinking density is calculated in combination with the rubber elasticity theory. DMA can provide the dynamic mechanical properties of materials at different frequencies and temperatures and is currently the most commonly used quantitative method.
- Nuclear Magnetic Resonance (NMR): The mobility of molecular chain segments is analyzed by using the NMR relaxation time, and the crosslinking density is indirectly estimated. This method is non-destructive to the sample, but the equipment cost is relatively high.
The Quantitative Influence of Crosslinking Density on the Flexibility and Hardness of Adhesives
1. Quantitative Indicators of Flexibility and Hardness
- Flexibility: It is usually characterized by the elongation at break (%), flexural modulus (MPa), or glass transition temperature (Tg). The higher the elongation at break and the lower the flexural modulus, the better the flexibility of the material.
- Hardness: Common test methods include Shore A/D hardness, Rockwell hardness (HR), and Vickers hardness (HV). The hardness value is positively correlated with the ability of the material to resist external force deformation.
2. Quantitative Relationship between Crosslinking Density and Performance
- Mathematical Model: According to the rubber elasticity theory, the relationship between the crosslinking density (ν) and the storage modulus (E’) can be expressed as: E’ = 3νRT (R is the gas constant, T is the absolute temperature). As the crosslinking density increases, the movement of molecular chains is restricted, and E’ increases linearly, resulting in an increase in hardness and a decrease in flexibility.
- Experimental Verification: A series of adhesive samples were prepared by changing the amount of crosslinking agent. The DMA test found that when the crosslinking density increased from 0.01 mol/m³ to 0.1 mol/m³, E’ increased by about 10 times, the elongation at break decreased from 300% to 50%, and the Shore A hardness increased from 20A to 70A (Figure 1).
Formulation Adjustment Strategy and Application Examples
1. Performance Requirements in Different Application Scenarios
- Electronic Packaging: It requires high flexibility to buffer thermal stress and a certain degree of hardness to ensure structural stability. It is recommended to control the crosslinking density at 0.02-0.05 mol/m³.
- Automotive Sealing: It needs to balance weather resistance and hardness, and the crosslinking density should be set at 0.05-0.1 mol/m³.
- Fabric Bonding: It emphasizes flexibility and peel strength, and the crosslinking density should be lower than 0.02 mol/m³.
2. Formulation Optimization Methods
- Regulation of Crosslinking Agent: The crosslinking density is directly controlled by changing the type and amount of the crosslinking agent. For example, multi-functional curing agents (such as melamine formaldehyde resin) can significantly increase the crosslinking density, while mono-functional additives (such as plasticizers) can reduce the crosslinking density.
- Optimization of Reaction Conditions: Prolonging the reaction time or increasing the reaction temperature can promote the crosslinking reaction, but over-crosslinking that may lead to material embrittlement should be avoided.
- Polymer Blending: Flexible segments (such as polyether polyols) or rigid segments (such as epoxy resins) are introduced to adjust the overall network structure. For example, adding 10% polyethylene glycol to an acrylate adhesive can increase the elongation at break by 40%.
3. Case Analysis: Formulation Design of High-Temperature Resistant Electronic Adhesive
Aiming at the bonding requirements of the heat dissipation module of 5G base stations, a high-temperature resistant (above 200°C) and highly flexible thermally conductive adhesive is developed. The performance balance is achieved through the following formulation optimization:
- Base Resin: An acrylate copolymer containing siloxane is used to provide heat resistance and flexibility.
- Crosslinking System: A two-component system (main agent: acrylate with double bonds; curing agent: multi-functional silane coupling agent), and the crosslinking density is controlled at 0.03 mol/m³ by adjusting the proportion of the curing agent.
- Additives: 5% nano-alumina is added to improve thermal conductivity, and 3% plasticizer is introduced to reduce the glass transition temperature.
After testing, the tensile strength retention rate of this adhesive at 200°C reaches 85%, and the elongation at break is 150%, meeting the stringent requirements of electronic packaging.
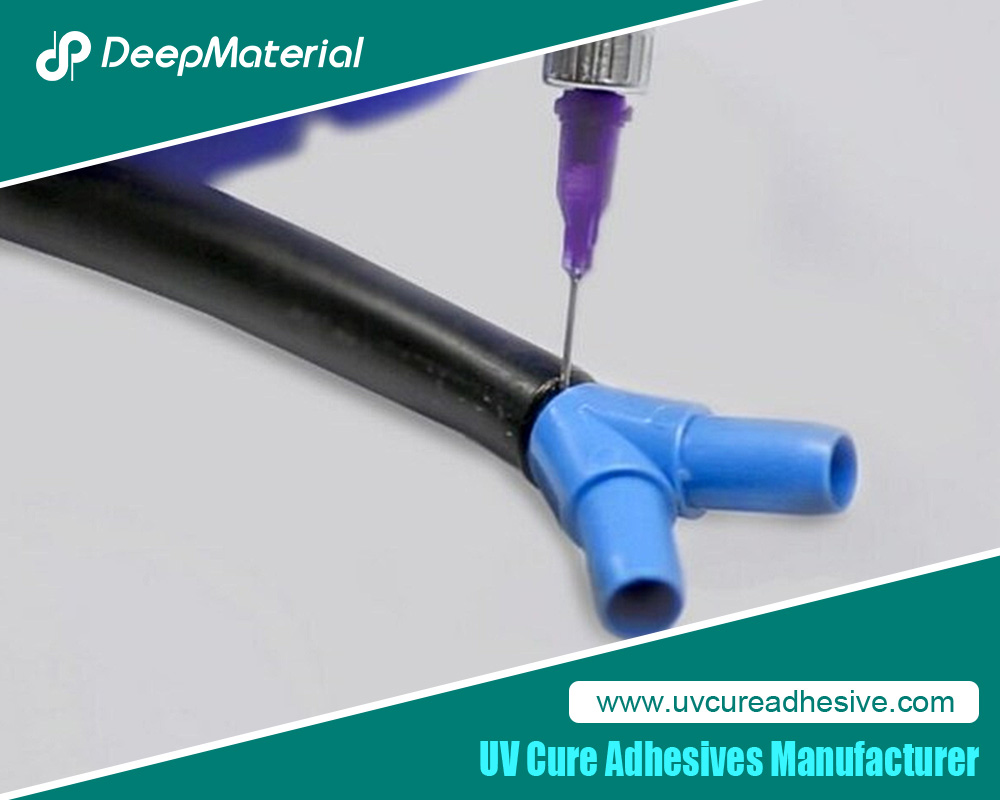
Conclusions and Prospects
The crosslinking density is a key parameter for regulating the flexibility and hardness of adhesives. By accurately quantifying the relationship between it and the material performance and combining with the formulation optimization strategy, the directional design of the adhesive performance can be achieved. Future research can further explore the construction of nano-scale crosslinked structures, the development of dynamic reversible crosslinking systems, and the influence of new manufacturing processes such as 3D printing on the crosslinking behavior of adhesives, promoting the innovative development of high-performance adhesive technology.
Through the methods described in this article, R&D personnel can systematically optimize the adhesive formulation, achieve the best balance between flexibility and hardness in different application scenarios, and provide scientific and reliable technical support for industrial production.
For more about the quantitative influence of crosslinking density on the flexibility and hardness of adhesives and the formulation optimization strategy, you can pay a visit to DeepMaterial at https://www.uvcureadhesive.com/ for more info.