How to Select Suitable UV Adhesives for Touch Screens
Touch screens have become a critical human-machine interface in modern electronic devices, widely used in smartphones, tablets, smartwatches, industrial control panels, and various other products. UV adhesives, or ultraviolet-curing adhesives, play a pivotal role in touch screen manufacturing due to their fast curing, high bonding strength, and high transparency. Choosing the right UV adhesives for touch screens is essential to ensure the performance, reliability, and production efficiency of touch screens.
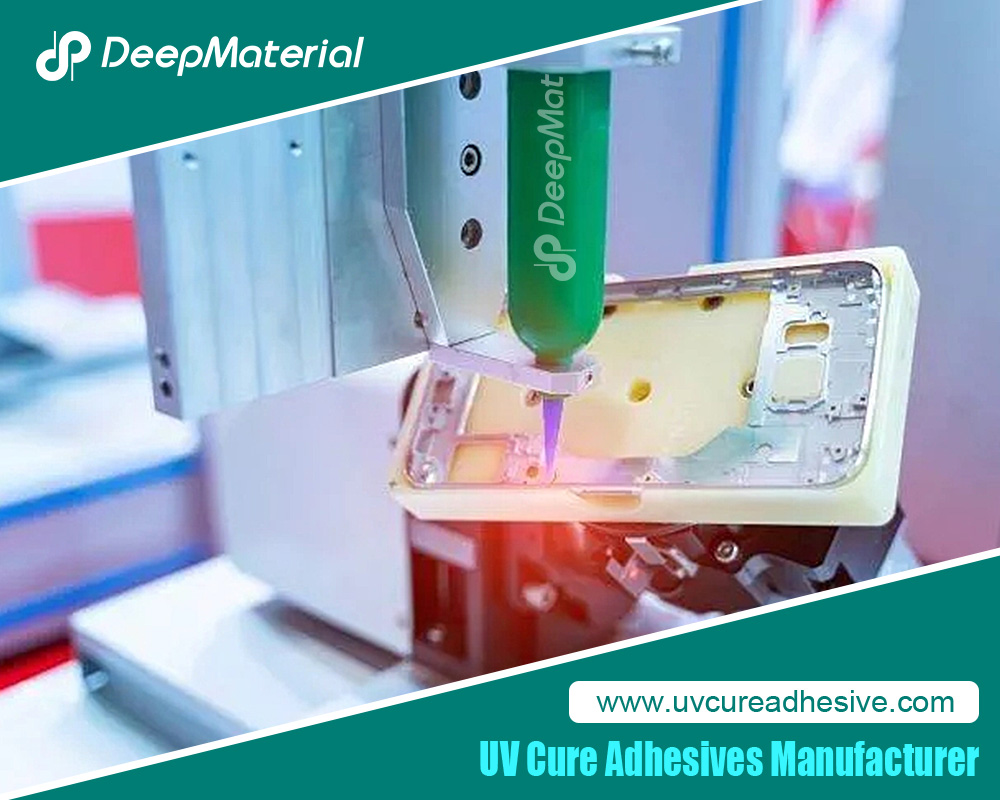
I. Understand the Application Scenarios and Requirements of Touch Screens
Performance requirements for touch screens vary significantly across different application scenarios, directly influencing the selection of UV adhesives.
(A) Consumer Electronics
Devices like mobile phones and tablets prioritize thinness, high sensitivity, and aesthetics. UV adhesives must have low viscosity for uniform coating in narrow spaces to achieve ultra-thin bonding; high transparency to ensure clear screen display without affecting color reproduction and visual effects; and fast curing properties to meet mass automated production needs and improve efficiency.
(B) Industrial Control
Industrial environments are complex, with common challenges like vibration, high temperatures, humidity, and chemical corrosion. UV adhesives for industrial touch screens must exhibit excellent weather resistance, maintaining stable performance after drastic temperature and humidity changes; high bonding strength to ensure components do not detach under vibration or impact; and good chemical stability to resist industrial chemical erosion.
(C) Medical Equipment
The medical field demands the highest standards of safety and reliability. UV adhesives for medical device touch screens must be non-toxic, odorless, and environmentally friendly, complying with medical-grade certification standards (e.g., ISO 10993 biocompatibility standards) to ensure no harmful substance release and no health risks to patients or medical staff. Additionally, they need excellent antibacterial properties to prevent bacterial growth and ensure a safe medical environment.
II. Consider Key Performance Indicators of UV Adhesives
(A) Curing Performance
- Curing Speed Fast curing speeds can shorten production cycles and improve efficiency, especially for large-scale automated production. However, excessively fast curing may prevent the adhesive from fully leveling or degassing, affecting bonding quality. UV adhesives should be selected based on production processes and equipment. For example, online UV curing equipment may require fast-curing adhesives, while manual operations or processes requiring good flow and filling may need adhesives with moderate curing speeds.
- Cure Depth Ensuring full curing of UV adhesives in all parts of the touch screen is critical. For thick or complex-structured touch screens, adhesives with good cure depth are needed to ensure even bottom-layer curing and avoid issues like pseudo-curing or whitening.
(B) Bonding Strength
- Adhesion Compatibility with Different Materials Touch screens typically consist of multiple materials, such as glass, ITO films, and plastic substrates. High-quality UV adhesives should achieve strong bonding with these materials to ensure overall structural stability. Before selection, test the adhesive’s bonding effect with each touch screen material to evaluate bonding strength and reliability.
- Long-Term Stability The bonding strength of UV adhesives must remain stable throughout the touch screen’s service life. Consider the adhesive’s aging performance under different environmental conditions (e.g., temperature, humidity, UV exposure), and choose products with good anti-aging properties to prevent strength degradation over time, which could lead to component detachment or separation.
(C) Optical Performance
- Transparency The transparency of UV adhesives directly affects screen display quality. High-transparency UV adhesives (with a light transmittance generally exceeding 98%) reduce light loss, enhance screen brightness and contrast, and ensure clear, vivid images. Low-transparency adhesives can cause blurry, yellowish displays and degrade the visual experience.
- Refractive Index Matching To minimize light reflection and refraction at material interfaces, the refractive index of UV adhesives should ideally match that of touch screen materials (e.g., glass, plastic). Poor refractive index matching can cause optical issues like Newton’s rings, interfering with display quality.
(D) Physical Properties
- Flexibility and Hardness Touch screens may experience external forces like bending or squeezing during use. Flexible UV adhesives can buffer stress and reduce cracking or debonding from external impacts, while certain support or protection applications may require adhesives with specific hardness. Balance flexibility and hardness based on the touch screen’s design and application scenario.
- Shrinkage Rate Shrinkage during curing can generate internal stress, potentially causing touch screen warping, deformation, or bonding cracks. Choosing UV adhesives with low shrinkage rates can effectively reduce internal stress and improve dimensional stability and reliability.
III. Evaluate the Reliability and Stability of UV Adhesives
(A) Weather Resistance Testing
Simulate real-world usage environments (e.g., high-temperature/high-humidity conditions like 85°C/85% RH, high-low temperature cycling like -40°C to 85°C, UV exposure) to assess performance changes in UV adhesives. After testing, check for issues like yellowing, cracking, debonding, or strength degradation to ensure long-term stability in complex environments.
(B) Reliability Certifications
Select UV adhesives that meet relevant industry standards, such as electronic product reliability certifications (e.g., AEC-Q100 for automotive touch screens). These certifications provide authoritative validation of the adhesive’s performance and quality for specific applications.
(C) Batch-to-Batch Consistency
Stable batch quality is crucial for mass production. Evaluate suppliers’ production process control capabilities and quality inspection systems to ensure consistent performance across different batches. Request multiple batches for testing to assess consistency.
IV. Consider Production Processes and Cost Factors
(A) Compatibility with Production Equipment
- Dispensing EquipmentThe viscosity of UV adhesives must match dispensing equipment. Low-viscosity adhesives are suitable for jet dispensing to achieve high-precision micro-dispensing, while high-viscosity adhesives may require piston or screw pump dispensing. Incompatibility can lead to issues like uneven dispensing, stringing, or needle clogging, affecting production efficiency and product quality.
- Curing EquipmentSelect UV adhesives that effectively complement curing equipment parameters (e.g., power, wavelength distribution). Different adhesives have specific requirements for UV wavelength and energy; mismatched curing equipment can result in incomplete or excessive curing, compromising adhesive performance and touch screen quality.
(B) Operational Convenience
- Storage ConditionsUnderstand the storage requirements of UV adhesives (e.g., temperature, humidity, light avoidance). Some adhesives require cold storage; if production sites lack such conditions, shelf life and performance may be affected. Choose adhesives with easily met storage conditions to reduce production management complexity and costs.
- Application Process DifficultySimple application processes can reduce production defects and labor costs. Single-component UV adhesives are easy to use without mixing, while two-component adhesives require precise mixing, which is more complex and demands higher operator skills and equipment accuracy.
(C) Cost-Benefit Analysis
- Material CostsWhile the price of UV adhesives is important, selection should not rely solely on cost. Consider performance and usage comprehensively: a high-cost but high-performance adhesive may reduce defect rates and lower overall production costs due to its reliability and strong bonding.
- Production Efficiency and Defect RateFast-curing and easy-to-use adhesives can improve production efficiency, reduce equipment downtime, and lower labor costs. Reliable, stable adhesives also minimize defect rates, avoiding rework and scrap costs from quality issues. Evaluate the comprehensive cost-benefit impact of UV adhesives on production efficiency and defect rates during selection.
Selecting suitable UV adhesives for touch screens is a systematic process requiring comprehensive consideration of application scenarios, performance indicators, reliability, production processes, and costs. By deeply understanding touch screen requirements, rigorously evaluating adhesive performance, and analyzing production realities, manufacturers can identify the optimal UV adhesive products, ensuring high-quality touch screen manufacturing and long-term stable performance.
For more about how to select suitable UV adhesives for touch screens, you can pay a visit to DeepMaterial at https://www.uvcureadhesive.com/ for more info.